航空機の燃料消費低減のために軽量化は重要課題であり、機体やエンジン部品(ファン、ファンケース)への軽量合金や炭素繊維強化プラスチックス(CFRP:Carbon Fiber Reinforced Plastics)の適用のための開発が、継続的に進められている。
ジェットエンジンでは、圧縮機の高圧力比化・高温化やタービン入口温度の高温化に向け、耐熱材料開発、冷却技術開発、空力設計技術の開発が行われてきた。最近では、燃焼器やタービンなど高温部へのセラミックス基複合材料(CMC:Ceramics Matrix Composite)の適用が進められている。
機体構造材料の軽量化
航空機における燃費の向上や航続距離の延伸のために、機体構造材料の軽量化は必須であり継続的に開発が進められてきた。図1には、各種構造材料について比強度(強度σf/密度ρ)と比弾性(弾性率E/密度ρ)の関係を示す。比強度と比弾性が大きい材料ほど、機体の軽量化には有効である。
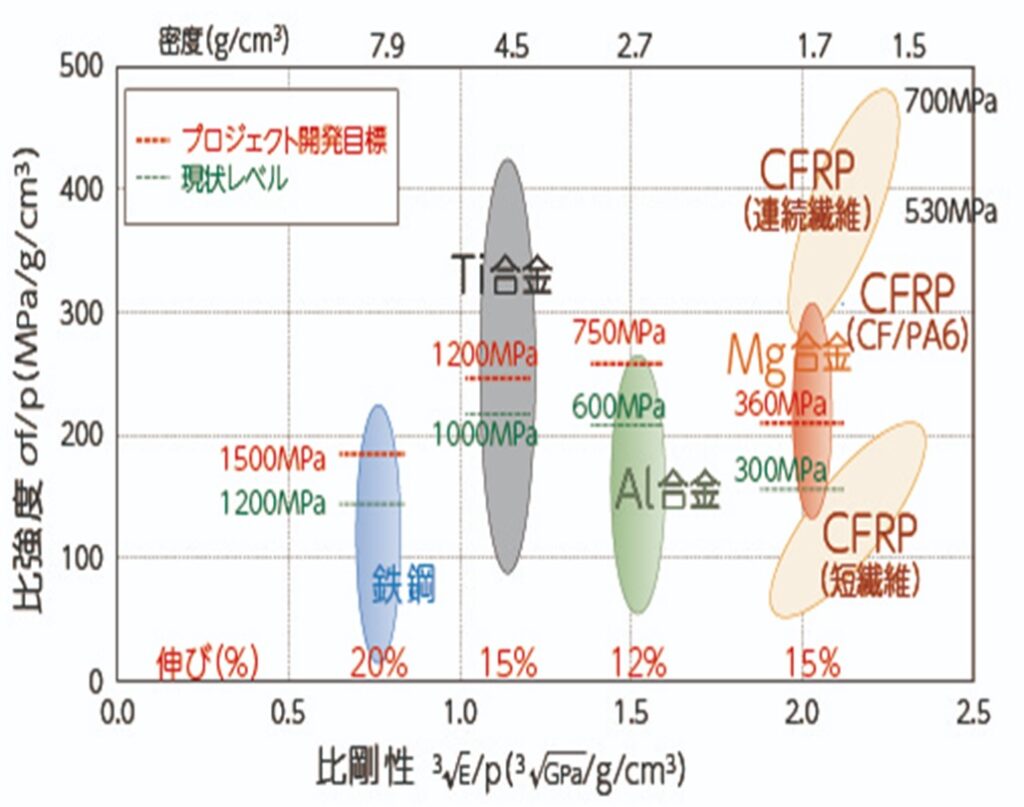
出典:新構造材料技術研究組合(ISMA)
機体構造材料の変遷
軽量化に向けて、航空機の機体構造材料は以下のような変遷をたどっている。
●1930年代、布・木・鋼に替えて、アルミニウム合金が航空機の機体材料として使用され始めた。その後、アルミニウム合金の高強度化が進められ、機体材料の主流となり適用範囲が拡大される。
●1940年代、比弾性に優れたマグネシウム合金の開発が始まり、2010年代に座席など内装品への適用が認可された。しかし、現時点でアルミニウム合金の代替には至っていない。
●1940年代後半、高強度アルミニウム合金(ジュラルミンなど)の代用としてフラップ、舵構造材などの2次構造材にガラス繊維強化プラスチック(GFRP:Glass Fiber Reinforced Plastics)が採用された。しかし、GFRPはアルミニウム合金と比べて比強度は高いが比弾性は劣るため、1次構造材への採用には至っていない。
●1950年代、チタン合金(主にTi-6Al-4V合金)の使用検討が開始された。
●1960 年代後半、アルミニウム合金よりも圧倒的に比強度と比弾性が高い各種の先進複合材料(Advanced Composites)の開発が進み、炭素繊維強化プラスチック(CFRP:Carbon Fiber Reinforced Plastics)の航空機構造材料への採用検討が開始された。
●1980年代に入ると、CFRPは航空機の2次構造材である主翼と尾翼のラダー(方向舵)や客室桁材などに採用された。
●1980年代後半、大型の1次構造材である垂直・水平尾翼安定板や胴体へのCFRPの採用が進められた。CFRPー金属材料継手では、腐食電位差により金属材料側にガルバニック腐食が生じるため、CFRPを多用する機体ではガルバニック腐食を生じにくいチタン合金が多用されている。
ただし、高価なチタン合金は大負荷が作用する主脚、エンジンを支えるパイロン、垂直尾翼、補助動力装置(APU:Auxiliary Power Unit)取付部、尾翼を支える下部構造などに限定される。
材料メーカーの動向
2022年3月、国際航空運送協会(IATA)は2024年の世界の航空旅客数が40億人とコロナ前の2019年を3%上回ると予測している。
新型コロナの感染拡大で、2021年の国内線・国際線を合計した旅客数は2019年比で47%に留まったが、2022年には83%に、2023年には94%にまで回復し、2024年には103%に、2025年には111%に増加すると予測している。
今後も航空業界では難局が続くと考えられているが、2022年6月に入り、新型コロナ禍で低迷した航空機部材メーカーの生産回復が進められている。ウクライナ危機による燃料高騰や環境規制の強化により、航空機軽量部材の需要は強まっている。
東レは、新型コロナ感染拡大の影響で2020年夏に停止した米国サウスカロライナ州の炭素繊維の主力工場で、2022年内に航空機向けの出荷を再開する方針を示した。原糸製造からCFRP加工まで一貫生産を担う中核拠点で、ボーイングの中型機B787の主翼や胴体などに使われる予定である。
帝人は、航空機向けの炭素繊維とCFRP部材の生産について、日本とドイツの工場で稼働率を高め、2022年3月期比で2023年3月期には2割の増産、2024年3月期には4割の増産計画を表明している。
東邦亜鉛は、航空機の降着装置(ランディングギア)やエンジン部品の耐久性を高める電解鉄(世界シェア7割)の増産を表明している。2023年3月期には生産を前期比2割増と新型コロナ感染拡大前の水準に戻す。2024年3月期には自動車向けの出荷も増して同7割増にする。
国際民間航空機関(ICAO)は2021年、航空各社がCO2排出を2019年より増やさないとのルールを導入した。現在は各国の自主的な対応となっているが、2027年には義務化する方針である。環境規制が強まれば、金属の代わりに軽量高強度のCFRP需要が増える。
航空機の機体材料
米国ボーイングの中型ワイドボディ機B787では機体材料に占めるアルミニウム合金の重量比が20%に減少し、複合材料(CFRP、GFRPなど)の重量比が50%に高まった。欧州エアバスの中型ワイドボディ機A350XWB機ではアルミニウム合金の重量比が21%に減少し、CFRPの重量比53%に高まった。
ボーイング787
米国ボーイングの747、767、777では機体材料の70~80%を占めていたアルミニウム合金の使用比率が、最新のB787(Boeing 787 Dreamliner)では20%に減少し、複合材料(CFRP、GFRPなど)の使用比率が50%にまで高まった。
炭素繊維は同じ強度で比較すると重量は鋼の1/4程度で済み、ボーイング787はCFRPを多く使うことで、従来機より燃費性能が2割向上した。
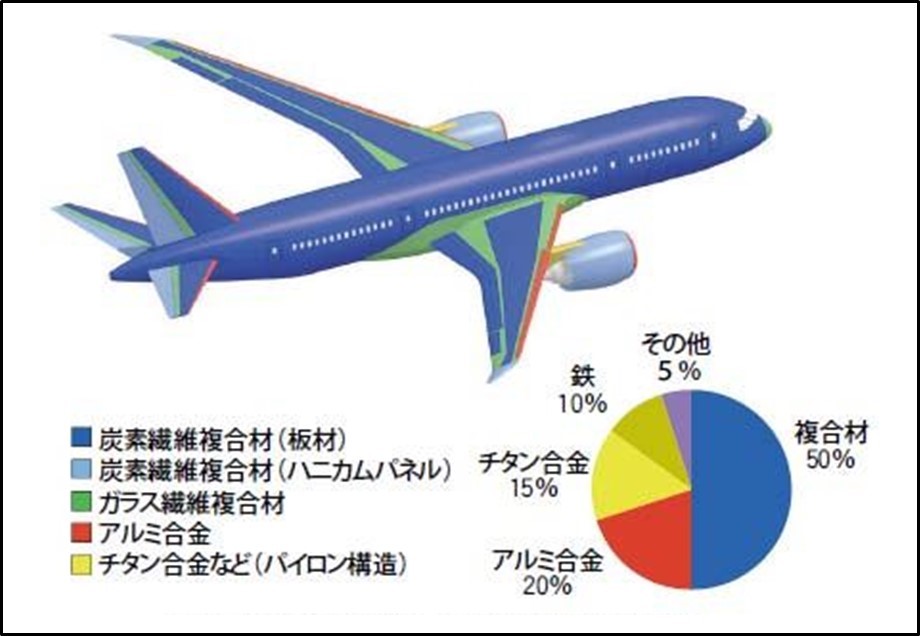
出典:炭素繊維協会
2011年から就航した長距離用中型のワイドボディ機B787(全幅:60m、全長:57m、全高:17m)には、Trent1000もしくはGEnxエンジンが搭載されており、図2のように機体へのCFRP適用が重量比で50%に達している。
機体材料の重量比20%を占めるアルミニウム合金は、新たにアルミニウム・リチウム合金(Al-Li合金、2098-T8)の板材が適用されている。機体材料の15%を占めるチタン合金については、主要部品である主脚(ランディングギア)にTi-5Al-5Mo-5V-3Cr 合金が用いられている
2023年に就航予定の大型旅客機であるボーイング777X(全長:69.79m(777-8機)、76.72m(777-9機))には、GE9X エンジンが搭載されており、CFRP製の主翼が採用されている。
この主翼は折りたたみ式のウィングチップが採用され、駐機時は折りたたみ(翼幅:64.82m)、飛行時には7m長くなるよう展開(71.75m)し、大きな揚力を発生させ燃費効率を最大化している。
また、アルミニウム合金には、銀(Ag)が添加された2029-T8 クラッド材やAl-Li 合金(2098-T84) 板材および2055-T84 押出材などが適用されている。
エアバス380
欧州エアバスでも複合材料(CFRP、GFRPなど)の使用比率は増加する傾向にあり、エアバス320で15%、A380では 22%と増加し、最新のワイドボディ機A350XWB(Airbus A350 eXtra Wide Body))では、図3に示すように53%に達している。
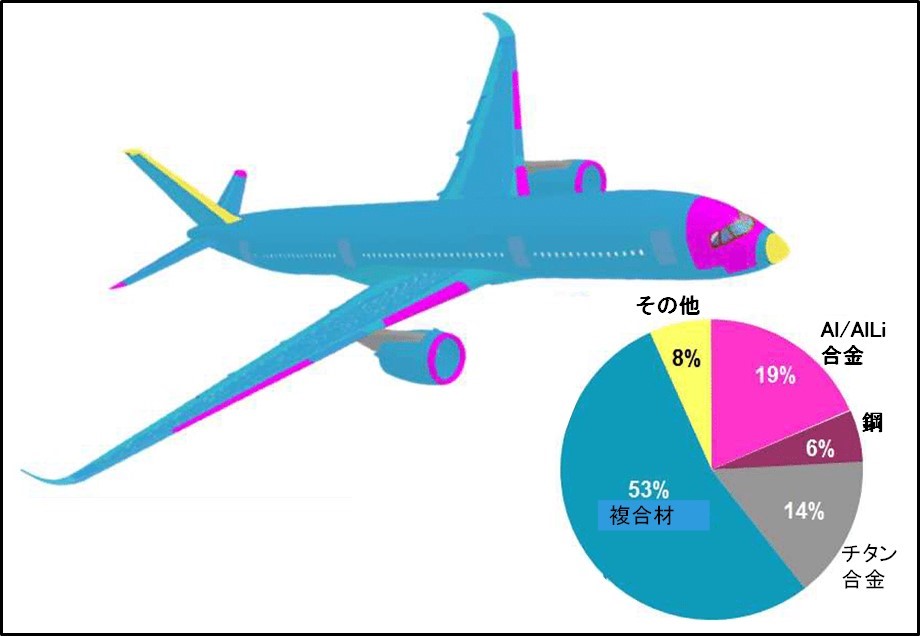
出典: Science China Technological Sciences
60-9,(2017)、1301-1317.
2007年就航の超大型ワイドボディ機のエアバス380(全長:72.7 m、全幅:79.8 m、全高:24.1 m)には、エンジン・アライアンス GP7200もしくはロールス・ロイス Trent900エンジンが搭載され、中央翼、水平・垂直尾翼など1次構造部材へのCFRP適用が30トンを超え、重量比で22%に達した。
重量比で61%のアルミニウム合金は、主翼桁材に7040-T7651合金、リブ材に7449-T7651合金、主翼下面ストリンガにZr添加2027-T3511合金、主翼上面外板材に7056-T7951合金が使用された。
また、Al-Li合金はメインデッキ、クロスビーム、床、ストリンガに2099-T83、2196-T8511押出材、主翼の桁やリブなどの内部構造に、2050-T84 厚板が採用された。しかし、2019年2月、販売不振によりA380機は、2021年以降の生産打ち切りが発表された。
2015年に就航した中型ワイドボディ機のA350XWB(全長:66.8m(350XWB-900)、73.79m(350XWB-1000)、全幅:64.75m、全高:17.5(350XWB-900)、17.8m(350XWB-1000))には、ロールス・ロイス製Trent XWBエンジンが搭載された。
重量比で53%にCFRPは主翼、中央翼とキールビーム、テールコーン、スキンパネル、フレーム、ストリンガー、ダブラーなどに採用されている。重量比で21%を占めるアルミニウム合金は、バードストライク対策のため衝撃に弱いCFRP に代わり、コックピット周辺や主翼の前縁などに用いられている。
また、Al-Li 合金は、2198-T851 板材の成形品、主翼ボックスのリブなどに2050-T84 厚板、中央ビームに2050-T852 鍛造材が使用されている。重量比で14%を占めるチタン合金は、高荷重フレーム、ドア周辺、ランディングギア、パイロに用いられている。
航空機ジェットエンジンと環境問題
2020年10月、日本は脱炭素社会の実現に向け「2050年カーボンニュートラル」を宣言した。これを実現するために、2021年4月、2030年度の温室効果ガス排出量を2013年度比で46%削減、さらに50%削減をめざして挑戦を続けることを表明した。
また、2025年2月には、「地球温暖化対策計画」で2035年度、2040年度の温室効果ガス排出量を2013年度比で、それぞれ60%、73%削減をめざすとした。
一方、2021年10月に国際航空運送協会(IATA)、2022年10月に国際民間航空機関(ICAO)で、「2050年カーボンニュートラル達成」の国際的な目標が合意された。日本も国際航空分野において2050年までにカーボンニュートラルを達成することを公式に宣言しており、航空分野におけるCO2削減の動きが活発化している。
そのため、航空機運航全般に係るCO2排出量削減の取組みを、これまで以上に加速する目的で、2021年3月に国土交通省航空局は「航空機運航分野におけるCO2削減に関する検討会」を立ち上げた。
グリーンリカバリー(環境に配慮した危機からの回復)の観点から、航空関連事業者の国際競争力強化も視野に入れ、日本の運航分野の取組みについて検討が行われた。その結果、航空分野におけるCO2排出量削減のアプローチのうち、特に運航に関わる次の3分野について具体策が検討されている。
(1)電動航空機と水素ジェットエンジンの開発、
ならびに機体やエンジンの軽量化・高効率化に資する複合材関連技術
(2)飛行経路短縮など消費燃料削減に資する管制の高度化による運航方式の改善
(3)バイオジェット燃料などの持続可能な航空燃料(SAF:Sustainable Aviation Fuel)の導入促進
この中でも、機体の軽量化・高効率化に資する複合材関連技術についての開発の歴史は長い。
1960 年代後半には、アルミニウム合金やチタン合金よりも比強度、比弾性率が高い炭素繊維強化プラスチック(CFRP:Carbon Fiber Reinforced Plastics)の航空機構造材への採用が開始された。
1995 年には高靱化エポキシ樹脂を用いたCFRPが開発され、ボーイング777機用の超大型エンジン「GE90」にCFRP ファンブレードが採用された。
2016年には航空機ジェットエンジンの軽量化・高効率化に資するセラミックス基複合材料(CMC:Ceramics Matrix Composites)の採用が、欧米の航空機エンジンメーカーにより始まった。
一方で、2023年6月、ボーイングとエアバスのCEOが新型機開発の見通しを公表している。
●ボーイングは、新型機開発について現行機と比べ20~30%効率改善した航空機が必要と考えているが、タイムラインは不明。2050年までのネットゼロに向けてはSAFが唯一のチャンスであり、水素については25年以内に意味のある変化をもたらすのであれば検討するが、長い道のりである。
⚫エアバス社は2050年までには技術的だけではなく、商業的(経済的)にも100%SAFの利用が必要である。A320neo・ A321neoと比較して燃費を20~25%改善した航空機を2035年に運用開始とし、水素についても開発を継続し、2035年に水素航空機を市場に送り出す計画を継続する。
ボーイングとエアバスは、中期的には現行機と比べて燃費を20~30%改善した航空機の開発を進め、「2050年カーボンニュートラル」の実現には持続可能な航空燃料(SAF)の利用が必須としている。また、長期的視野に立ち、水素航空機の開発は重要と考えている。
ターボファン・エンジンの開発
ターボファン・エンジンとは
現在、商用機の航空機エンジンの主流はターボファン・エンジンと呼ばれ、圧縮機の前にファンを設置してエンジン外側を迂回させて流す空気と、エンジン内側で燃焼させてから排出する空気に使い分けている。
ファンのみを通過する空気流入量とエンジンで使用する空気流入量の比率はバイパス比と呼ばれ、ボーイング787機のエンジンではバイパス比が9程度と高く、燃費効率に優れている。
民間航空機用エンジンでは、1950年代に初めてターボファン・エンジンが搭載されて以降、燃費効率の向上と低騒音化が進められ、低バイパス比から高バイパス比ターボファン・エンジンへと急速に進化してきた。高バイパス比エンジンとはバイパス比が約4以上で、比較的低速の飛行に適している。
エンジンの基本構造は、前方から吸い込んだ空気を圧縮機で高圧化し、それに燃料を混ぜて着火することにより直接燃焼し、急激に膨張する燃焼ガスを後方に噴射して推力を得ており、一部の燃焼ガスでタービンを回転させて圧縮機を駆動する。
一般に航空機ジェットエンジンでは、ドーナツ状のライナーで構成されたアニュラ型燃焼器が採用されており、タービン入口温度(TIT:Turbine Inlet Temperature)は1500~1700℃に達している。
航空機ジェットエンジンでは離着陸時に最高出力で1~数分間稼働し、フライト中は負荷を下げて運転されるため20000~24000回程度の熱サイクル疲労を受ける。ケースに多数設置された検査孔から定期的(航空会社ごとに運転時間、離陸回数で規定)にエンジン内部の検査を行い、メーカー許容値を判定基準として適切な時期にオーバーホール整備を実施するオンコンディション整備が行われている。
2016年1月に初飛行したフランス・エアバスの「A320neo」(neo:new engine option)はA320ファミリー機の最新版で、新型エンジンを搭載した単通路の近中距離向け旅客機である。「A320」と比べて燃費面で15%の低減、騒音面で50%の低減が公表されている。
2010年12月、米国Pratt & Whitneyの「PW1100G-JM」 とCFM International(フランスSnecmaと米国GEの合弁会社)の「LEAP-1A」 は、フランス・エアバスからA320neoファミリー機のエンジンに選定された。次に、両エンジンの特徴を示す。
Pratt & Whitneyの「PW1100G-JM」エンジン
エアバスの開発した「A320neo」は、既存のA320ファミリー機のエンジン(V2500およびCFM56)を最新型のエンジンに換えて、経済性と環境適合性を大幅に改善した。
「A320neo」に搭載された「PW1100G-JM」エンジンは、米国Pratt&Whitney(P&W、出資比率:59%)、ドイツMTU Aero Engines(MTU、18%)、日本航空機エンジン協会(JAEC、23%)による共同事業体であるInternational Aero Engines LLC (IAE LLC)により開発された。
2011年度に開発は始まり、設計、開発エンジンの試作および各種開発試験を経て、2014年にエンジン型式承認を取得し、「A320neo」に搭載されて2016年1月から運航している。
ファンの回転速度を下げるため、圧縮機との間に減速ギアを配置したギアードターボファンエンジン(GTF、Geared Turbo Fan Engine)が最大の特徴で、直径:2.06mの大口径ファンによりバイパス比を約12まで上げ、推力:11~15トン級を実現した。
JAEC(IHI、川崎重工業、三菱重工業)がファン、低圧圧縮機、低圧シャフト、燃焼器の一部を担当し、MTUは低圧タービンと高圧圧縮機の一部、P&Wはそれら以外の部位を担当した。
ファン部の軽量化のために、P&Wによるアルミニウム合金製の中空ファン動翼、IHIによる炭素繊維強化プラスチック(CFRP)製のファンケースと構造案内翼(SGV:Structural Guide Vane)の採用が特徴である。
加えて、回転数が高い低圧圧縮機は、可変入口案内翼をもつ3 段で構成され、高い遠心力に耐えるため各段落とも動翼とディスクを一体化したIBR(Integrated Bladed Rotor)ローター が採用された。
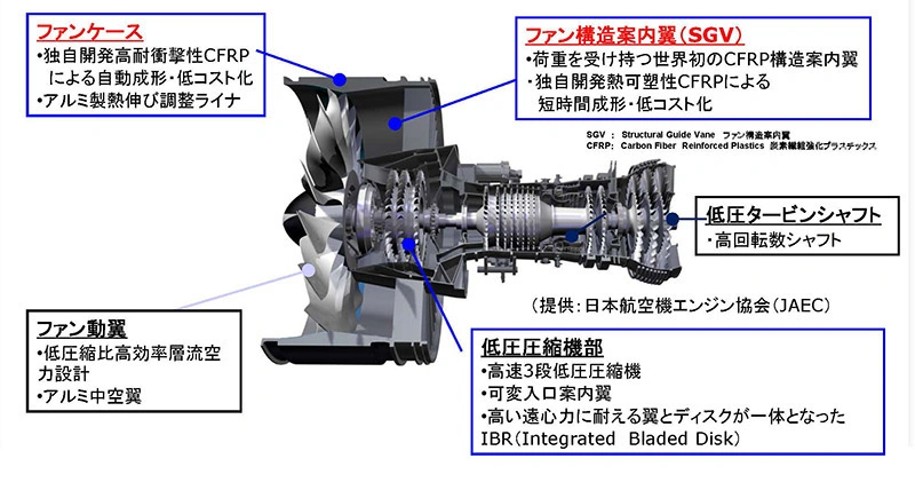
2023年7月、2015~2021年にかけてP&Wが製造した「PW1100G-JM」エンジンの粉末冶金部品で、部品寿命に影響する異物混入が認められた。同エンジンは国際共同開発で進められたため、本事案で発生する顧客への補償や整備費用など総額約70億米ドル(約1兆円)は、出資比率に応じて日本企業にも影響が出た。
CFMインターナショナルの「LEAP」エンジン
「LEAP-X」エンジンは、米国GE(出資比率:50%)とフランスのスネクマ(50%)の合弁会社であるCFMインターナショナルが開発した高バイパス比ターボファンエンジンである。
2008年7月に開発が始められ、2015年5月、エアバス「A320-251neo」に「LEAP-1A」エンジンが搭載され初飛行が行われた。2016年5月にはエンジン型式承認を取得した。
現在、近中距離路線を飛ぶLCCが運航する航空機は、単通路のナローボディー機が主流であり、最新型であるエアバス「A320neo」に「LEAP-1A」エンジンが搭載された。直径1.98mの大口径ファンによりバイパス比を約11まで上げ、推力:11~15トン級を実現して2016年に就航した。
また、ボーイング「B737MAX」には「LEAP-1B」エンジンが搭載され、直径1.76mの大口径ファンでバイパス比を約9とし、推力:10~13トン級を実現して2017年に就航した。中国商用飛機「COMAC C919」には「LEAP-1C」エンジンが搭載され、直径1.98mの大口径ファンでバイパス比を約11とし、推力:13~14トン級を実現して2018年に就航した。
現在、「LEAP」エンジンの製造は、高温部品は米国インディアナ州のラファイエットとノースカロライナ州のダーラムにあるGEエアロスペースの工場で、ファンや低圧タービンなどはフランス・ヴィラロッシュにあるサフランの工場で行われている。
構造材料で最大の特徴は、セラミックス基複合材料(CMC)が民間航空機エンジンの高温部品に初適用された点があげられる。高圧タービンの高温静止部品であるタービン・シュラウドに適用されており、従来のNi基超合金に比べて1/3と軽量で、2倍の高温強度を有し、耐熱性にも優れている。
その他、低圧タービンブレードにはNi基超合金の1/2と軽量なTiAl金属間化合物、ファンブレードやファンケースにはチタン合金の1/2と軽量な三次元織炭素繊維強化プラスチック(CFRP)が採用されている。また、燃料ノズルは3Dプリンティング技術により製造された点も注目されている。
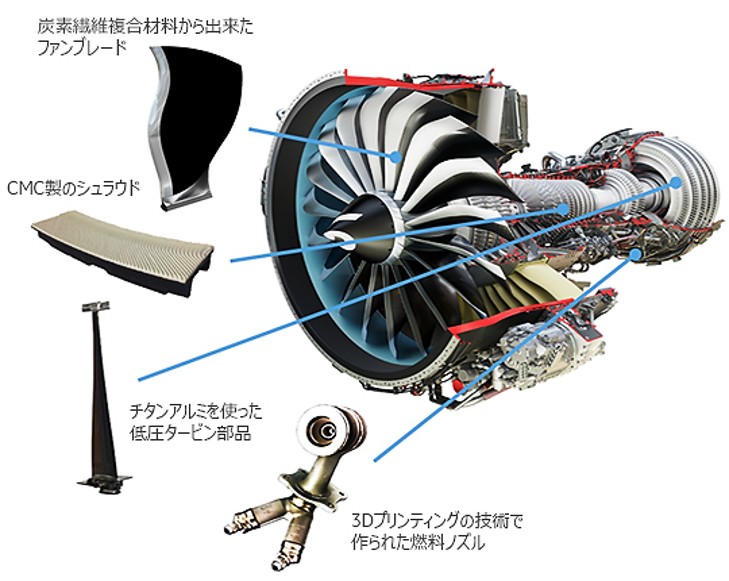
低バイパス比ターボファンエンジン
軍用航空機エンジンでは超高速飛行に優れたターボジェットエンジンが主流であったが、1960年代初めにターボファンエンジンが開発されて、現在では低バイパス比ターボファンエンジンが主流となっている。
例えば、米国ロッキードマーチン「F-35」戦闘機に搭載されたP&Wの「F135」エンジンは、アフターバーナ (A/B :Afterburner) 付低バイパス比ターボファンエンジンである。
バイパス比:0.57でファンからの空気排出量が少なく、ターボジェットエンジンに近い特性である、推力:12.7トン、タービン入口温度:1980℃である。また、酸素を含む高温排気に再度燃料を吹きつけて燃焼させるアフターバーナー (A/B :Afterburner) が付帯され、A/B使用で推力は19.5トンに増強される。
国内では、2020年11月に開催された「防衛装備庁技術シンポジウム2020」で、次世代ハイパワーエンジン「XF9」の開発状況が報告されている。
戦闘機用エンジン「XF9」は、アフターバーナー付低バイパス比ターボファンエンジンである。バイパス比:0.4で、推力:11トン、タービン入口温度:1800℃で、A/B使用で推力は15トンに増強される。
「XF9-1」エンジンの主要な高温部品には、最新材料が適用されている。タービン動静翼は物質・材料研究機構(NIMS)が開発した第5世代のニッケル基単結晶超合金「TMS-162」に、電子ビーム物理蒸着法(EB-PVD)によるセラミック遮熱コーティング(TBC)が施工されている。
また、タービンディスクにはNIMSが開発した溶製鍛造製のニッケル・コバルト基超合金「TMW-24」が採用され、タービン・シュラウドにはセラミックス基複合材料(CMC)に耐環境性コーティング(EBC)が施され、冷却空気の低減が図られている。

出典:防衛装備庁
高分子マトリックス複合材料(PMC)の開発
民間航空機エンジンでは、大型化するファン構造の軽量化が高分子マトリックス複合材料(PMC:Polymer Matrix Composite)の適用により進められた。安価なガラス繊維強化プラスチック(GFRP)や高強度の炭素繊維強化プラスチック(GFRP)など、用いる強化繊維により様々な特性が発現される。
中でも、CFRPは軽量(比重:約2.0)、高強度、高剛性であり、航空機の機体に始まり、ターボファンエンジンのファン部品への適用が進められた。
PMCの製造技術
強化繊維とマトリックス樹脂を成形してPMCを製造するプロセスは、部品形状に合わせて様々な方法が開発されている。これらの成形プロセスの中から、採用する強化繊維やマトリックス樹脂の種類、部品形状、コスト、数量、品質などから、最適なものを選定してPMCが製造されている。
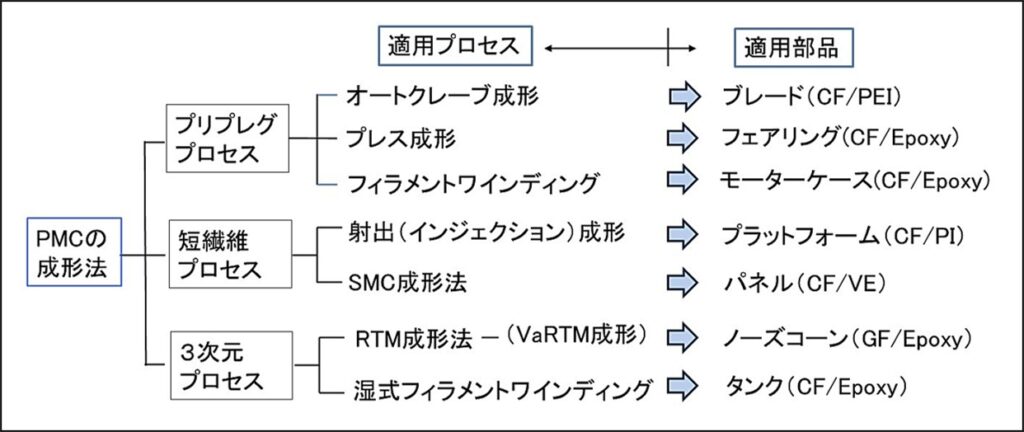
プリプレグプロセス
樹脂があらかじめ予備含侵された繊維シートは「プリプレグ」と呼ばれる。用途に合わせて、繊維が一方向に配列されたUDシートや、横糸と縦糸とが織物になっているClothシートなどがある。また、マトリクス樹脂も、用途に合わせて熱硬化性樹脂や熱可塑性樹脂など幅広く商品化されている。
「オートクレーブ成形」では、所定の形状に裁断したプリプレグを必要な枚数積層し、層間に空気が残留しないようフィルムバックで覆い、真空引きしながら、オートクレーブ(高温高圧釜)内で加熱・加圧しながら樹脂を硬化させる。ボイドが少ない高品質の製品を得ることが可能である。
一般的な航空機用CFRP部品の製造方法として採用されている。プリプレグ積層工程は1970年代から自動化が進められ、ボーイング787型機やエアバスA350型機の胴体、主翼など多くの部位に適用されている。
「プレス成形」では、所定の形状に裁断したプリプレグなどの中間材を、あらかじめ加熱した金型で挟み、プレス機によって加圧しながら硬化させる。金型を使用するため寸法精度の高い成形品が得られ、成形時に昇温・降温を行わないため生産性に優れる。
「フィラメントワインディング」では、マンドレル(芯金)にプリプレグ、その上から熱収縮テープを巻き付けて、オーブンに入れて加熱硬化させ、マンドレルを取り外す成形法である。パイプ形状部品の生産に優れている。
短繊維プロセス
「射出(インジェクション)成形」では、熱可塑性のマトリックス樹脂と短く細断した炭素繊維を混錬してペレット化する。一定量のペレットを加熱融解し、金型内に射出して成形して金型内で冷却され硬化した後に、成形品を取り出す。金型を使用するため寸法精度の高い成形品が得られ、小型部品の生産性に優れる。
「SMC(Sheet Molding Compound)成形」では、強化繊維を長さ10~50mm程度に切断し、マトリックス樹脂中に硬化剤、内部離型剤などを加えた混合物を含浸させ、さらに加熱して増粘させて厚さ1~5mmのシート状、板状に加工した中間材がSMCシートである。
このSMCシートを所定の形状に切断して積層し、あらかじめ加熱して金型で挟み、プレス機によって加圧しながら硬化させる。金型により寸法精度の高い成型品の大量生産が可能である。
最近では、短繊維プロセスの一種の「3D造形装置」が開発されている。炭素繊維を強化材料としたCFRPがレーザー焼結法(SLS:Selective Laser Sintering)や熱溶解積層法(FDM:Fused Deposition Modeling)により製造されているが、現時点で航空機部品への適用例はない。
3次元プロセス
「RTM(Resin Transfer Molding)成形」では、所定の形状に裁断した炭素繊維の織物を製品形状に予備賦形した中間材(プリフォーム)を作製して加熱金型内へ配置し、樹脂と硬化剤を加圧注入して硬化させる。金型を使用するため高品質で、比較的単純な形状の中規模量産品に適している。
「バータム成形(VaRTM、Vacuum assisted Resin Transfer Molding)」は、下型だけを使用して上面はフィルムバックで覆い、真空吸引の力を利用して樹脂を含浸する成形法である。樹脂製や木工製の型が使用でき、低コスト化と共に大型化が容易である。
「湿式フィラメントワインディング」では、強化繊維束(フィラメント)を樹脂槽の中を通過させて樹脂を含浸させた後、マンドレル(芯金)に巻き付け、オーブンに入れて加熱硬化させ、マンドレルを取り外す。繊維巻き付け後に樹脂を含浸する成形法も実用化されている。円筒状製品の成形には適している。
最近では、連続繊維を使ったCFRPの「3D造形装置」が開発されている。米国Markforgedの「Mark Two」「Industrial シリーズ X7」はFDM法、米国AREVOの「AQUA」はSLS法による造形装置が知られている。
高バイパス比ファンへのCFRP適用
近年、燃料費の高騰と温室効果ガス(CO2)削減の要請を受け、民間航空機エンジンに対する低燃費化の要求が厳しい。そのため民間航空機に用いられるターボファンエンジンについては、燃費改善の主な手段として高バイパス比化による推進効率向上と圧縮機での高圧力比化による熱効率向上が進められてきた。
実際に、1980年代初期のバイパス比は5程度であったが、最近の「LEAP」エンジンではバイパス比11まで上昇している。このようにバイパス比が高くなるほど、亜音速での推進効率が高くなり、低速航行時の燃料消費率が下がり、排気騒音も低くなる。
この高バイパス比用の大口径ファンを実現するためには、大型化するファン部品の軽量化が必須となり、従来のアルミ合金やチタン合金製から、より軽量なCFRPの採用による重量削減が進められてきた。
対象とされたのが、ファンブレード、ファンケース、構造案内翼(SGV:Structural Guide Vane)であり、いずれも最高使用温度が100℃程度でCFRP適用が可能な温度域である。
米国GE Aerospace(GEエアロスペース)
1990年代に入り、ボーイング「777」に搭載されたGEエアロスペース製の超大型エンジン「GE90」では、大口径ファンの”ファンブレード”にCFRP素材が世界で初めて適用された。高靱化エポキシ樹脂によりCFRPの靱性を向上することで、鳥衝撃(Bird Strike)による破損対策が功を奏した。
加えて、金属に比べて衝撃時の破壊リスク低減のため、CFRPファンブレード前縁部に耐衝撃性に優れるチタン合金板が接着された。
しかし、1000枚以上のCFRP 素材シート(プリプレグ)を手作業で積み重ね、オートクレーブ成形で数時間かけて加熱硬化させる製造プロセスは、極めて高コストであった。CFRPファン部品の適用を広めるには、低コスト化が次なる課題であった。

2010年代には、ボーイング787機に搭載された大型エンジン「GEnx」向けに、CFRPファンブレードに加えて、”CFRPファンケース”の実用化に成功し、20年近く量産が続けられている。
ファンケースはエンジンで最も重い部品の一つであり、CFRP適用による軽量化の効果が大きい。ファン空気流路を形成するダクトとしての機能に加えて、ファンブレードの飛散(FBO、Fan Blade Off)を止める耐衝撃性(コンテインメント特性)が必要とされる。
ファンケースの製造では、炭素繊維織物を金型上に自動で巻き付け、エポキシ樹脂を含浸して硬化させるRTM成形法が採用された。耐衝撃性と低コスト化を両立させる第2世代のCFRPファン部品を実用化した。
エアバス「A320neo」機に搭載されたCFMインターナショナルの中型エンジン「LEAP-1A」には、3次元構造織物とRTM成形法を組み合わせた”ファンブレード”と”ファンケース”が採用されている。

2020年代には、民間機用に”オープンローター”が採用された次世代エンジンの実証試験が加速されている。従来のターボファンエンジンとは異なり、ファンブレードを覆うファンケースがない構造であり、推進効率を大幅に向上できることが理論的に明らかにされている。
GEとSafran Aircraft Enginesが発表した「CFM RISEプログラム」では、ローターブレードに三次元編みCFRPを採用する計画で、直径約3.9mの大径化で超高バイパス比70の実現をめざしている。
英国Rolls-Royce(RR、ロールスロイス)
CFRP製ファンブレードの開発では、1970 年代に英国Rolls Royce(RR)が、ロッキードトライスター「L1011」に搭載する大型エンジン「RB211 シリーズ」への採用を試みたが、バードストライク(鳥衝撃)に耐えられず失敗に終わったのが最初である。
炭素繊維製造の黎明期で、炭素繊維及びその周辺技術が未成熟な状態での早すぎた挑戦が失敗の原因と考えられている。その後、耐衝撃性(靱性)の改善に向け、CFRP素材メーカーにより靱性向上に向けた種々改善が試みられている。
そのため2010年代、ボーイング787機に搭載された大型エンジン「トレント1000」には、チタン合金製のファンブレードが搭載された。2枚のチタン合金板の間に不活性ガスを封入して圧着することで軽量化を実現した。

出典: Rolls-Royce HP.
2007年から英国政府の支援を受け、次世代大型エンジン「UltraFan」向けにCFRPファンブレードとCFRPファンケースの開発が進められた。航空機部品メーカーのGKNと共同で、エポキシ樹脂のプリプレグを自動積層し、オートクレーブ成形による製造プロセスが採用された。
ブレード前縁には薄いチタン合金板を取り付け、バードストライクなどへの耐性を大幅に向上させた
2013年1月、”新CFRPファンブレード”量産化に向けた新工場が開設され、少量生産が始められた。その後、RR所有のボーイング747飛行試験機に、「改修トレント1000」エンジンを取付け、フライトテストが実施された。
2020年2月、次世代の低燃費・低騒音エンジン技術「UltraFan」の実証機エンジン用に世界最大のCFRPファンブレードの製造を開始した。直径は140インチ(約3.6m)で、ブリストルのテクノロジーハブで製造する。2021年に地上試験を開始し、2020年代終わりに運用可能となる。
「UltraFan」は、初期のトレントエンジンと比べ、燃費が25%向上し、温室効果ガス排出量も25%減少する。
米国Pratt & Whitney(P&W、プラット・アンド・ホイットニー)
2011年、International Aero Engines LLC (IAE LLC)により「PW1100G-JM」エンジンの開発が始まり、設計、開発エンジンの試作および各種開発試験を経て、2014年にエンジン型式承認を取得し、エアバス「A320neo」に搭載されて2016年1月より運航した。
IAE LLCは、Pratt & Whitney(P&W)、日本航空機エンジン協会 (JAEC)、ドイツのMTU Aero Engines (MTU)の共同事業体である。
「PW1100G-JM」エンジンには、変性エポキシ樹脂のCFRP素材(プリプレグ)を使用した自動シートワインディング成形法で製造した”ファンケース”、及び熱可塑性樹脂のプリプレグを使用した自動積層・プレス成形法で製造した”構造案内翼(SGV)” が採用された。いずれも、JAECの一員として参画したIHIが開発した。
ファンケースには、①3次元織物とRTM成形の組合せ、②高靱化エポキシ樹脂プリプレグのオートクレーブ成形、③変性エポキシ樹脂プリプレグとフィラメントワインディング自動積層が候補材に選ばれ、飛翔体(鋼製円柱)をエアガンで撃ち込む高速衝撃試験が行われ、③フィラメントワインディング材が採用された。
構造案内翼(SGV)は、飛行荷重および安全を考慮したFBO荷重に耐え、エンジン全体から要求される剛性を得るため、CFRP翼の両端(内外径)部を金属製のサポートで挟み込む構造が採用された。
①高靱性エポキシ樹脂プリプレグ、②市販の熱可塑性樹脂のプリプレグ、③繊維/樹脂界面を改善した改良型熱可塑性樹脂プリプレグを候補材として高速衝撃試験が行われた。その結果、SGVには高靱性で硬化時間の短い③改良型熱可塑性樹脂プリプレグでロボットによる自動積層と高速プレス成形が採用された。
IHIでは、次世代エンジンに向け、「PW1100G-JM」では採用されていない「CFRPファンブレード」や「耐熱CFRPフレーム」の採用をめざして、新しいPMCの開発を進めている。

航空機ジェットエンジン向け耐熱材料の開発
航空機ジェットエンジンの高性能化を実現するには、高バイパス比化と並び高圧力比化・高温化による熱効率向上が鍵となる。すなわち、燃焼器やタービンなど高温部品の耐熱性の向上である。
下図には、航空機ジェットエンジン用の耐熱材料の開発状況と、それに伴うタービン入口温度(TIT:Turbine Inlet Temperature)の上昇を示す。
従来から、ニッケル(Ni)基やコバルト(Co)基の耐熱合金開発が進められてきた。近年では、使用条件の厳しいタービン動翼材である普通鋳造Ni基超合金(CC:Conventionally Cast)について結晶制御技術による耐熱性向上が進められた。
一方向凝固化(DS:Directionally Solidified)で約20℃、単結晶化(SC: Single Crystal)でさらに約30℃の耐熱性向上が実現され、耐熱温度は1100℃(強度設計上では1000℃)程度に達している。
現在は、酸化物セラミックスを用いた遮熱コーティング(TBC:Thermal Barrier Coating)が翼外面に施され、翼内に形成された複雑な冷却孔を通じて圧縮空気により内面の対流冷却、外面のフィルム冷却が行われことで、タービン入口温度(TIT)の上昇に対応している。
静翼材には、溶接などによる補修性を考慮してCo基合金が使われており、翼外面にはTBCが施され、翼内に形成された複雑な冷却孔を通じて圧縮空気により内面の対流冷却、外面のフィルム冷却が行われている。
燃焼器には、加工性に優れた薄板のNi基合金やCo基合金が使われており、内面にはTBCが施され、外面は対流冷却が行われている。
一方、次世代耐熱材料として期待されているセラミックス基複合材料(CMC)は、2016年に就航したエアバス「A320neo」に搭載された「LEAP-1A」エンジンの一部品に採用され、酸化物セラミックスの耐環境コーティング(EBC)が施され、今後のタービン入口温度(TIT)の上昇が期待されている。

耐熱超合金の開発
1960年代、ガスタービン動翼材料としてγ‘(ガンマプライム)相Ni3(Al,Ti)析出強化型で等軸晶の普通鋳造Ni基超合金(CC : Conventional Casting)が開発された。現在も、使用温度の低い後段動翼で使われている。
近年、結晶制御技術の高度化により、動翼の長手方向に対して直角な結晶粒界をなくした一方向凝固(DS:Directional Solidification)合金、高温での弱化要因である結晶粒界を完全に排除した単結晶(SC:Single Crystal)合金化により耐熱温度の向上が実現された。
単結晶合金には結晶粒界が存在しないため、粒界強化元素の添加を控えられるため合金の融点低下を抑制でき、γ‘相を完全固溶させる溶体化熱処理が可能となる。そのため、一方向凝固合金以上に高温クリープ寿命と疲労寿命の向上を実現した。
1970年代後半には、一方向凝固合金よりも耐熱温度が約50℃高い単結晶合金が開発され、「PWA1480」、「ReneN4」、「CMSX-2」などの第1世代超合金と呼ばれた。その後、耐食性と高温クリープ寿命の改善に有効なレニウム(Re)を添加した「CMSX-4」など第2世代超合金が開発され、耐熱温度は1000℃に達した。
第3世代超合金では、Re添加量が約3→約6mass%まで増加され、第4世代超合金は、ルテニウム(Ru)添加量が2~3mass%で高温組織安定性が高められた。さらに第4世代超合金のRe添加量を増加させた第5世代超合金が、国内の物質材料機構により開発されて「TMS-162」は耐用温度が約1100℃に達した。
一方、Ni基超合金製のガスタービン動翼材料の寿命は、使用温度が1000℃以上の場合には、高温酸化と高温クリープ寿命が支配し、使用温度が1000℃以下の場合には、燃料由来の高温ホットコロージョン(硫化腐食)とガスタービンの起動・停止に伴う熱疲労が主要な支配的要因である。
そのため、Ni基超合金製のガスタービン動翼表面には、各種の高温耐食・耐酸化コーティングが不可欠である。特に、使用温度が1000℃以下のガスタービン動翼に生じる高温腐食現象は、高温環境により腐食機構が異なるため、燃料のクリーン化を含む様々な対策が施されてきた。
実際に、800~900℃の温度域の「高温硫化腐食」は、燃料に含まれるNaとSが燃焼器中で溶融硫酸塩Na2SO4を生成して動翼のNiと共晶反応を生じる。また、650~750℃の「高温硫化腐食」は、吸入空気中のNaCl(海塩粒子)と燃料中のSが燃焼器中で反応し、動翼のNiやCoと共晶反応を生じる問題が発生した。
低温腐食現象では、500~700℃の「バナジウムアッタック」は、燃料中のV化合物に起因する加速酸化腐食が発生し、S化合物が水蒸気と結合して200℃以下の低温部に凝着して生じる「硫酸露点腐食」などが知られており対策が施されている。
高温耐食・耐酸化コーティング
ガスタービンの高温耐食・耐酸化コーティング技術の開発の歴史は古く、1950年代までさかのぼる。当初は、Cr、Al、Siなどの保護性酸化皮膜の形成元素を主成分とした「拡散浸透法」が、第一世代の高温耐食・耐酸化コーティングとして採用された。
経済性に優れ、その優れた耐酸化性から、現在でもガスタービン高温部品の冷却孔内面のコーティングに適用されている。しかし、コーティング材料が限定されるプロセスであり、基材表面への金属間化合物の形成ため表面層の脆化に加え、補修が困難などの問題を有している。
第二世代の高温耐食・耐酸化コーティングは、主に電気めっき法などで形成した貴金属(Pt、Rhなど)皮膜にAl拡散浸透処理を施す複合コーティングである。貴金属を使うため高コストであるが、耐酸化性と共に高温腐食にも優れた耐性を示し、現在でも「Pt/Al複合コーティング」は航空機エンジンで使われている。
現在の主流は、第三世代の高温耐食・耐酸化コーティングである。MCrAlY合金(MはNi、Co、あるいは両方)皮膜が、電子ビーム物理蒸着法(EB-PVD:Electron Beam-Physical Vapor Deposition)、量産性に優れた大気プラズマ溶射(APS:Atmospheric Plasma Spraying)→減圧プラズマ溶射法(LPS:Low Pressure Plasma Spraying)で形成されている。
また、酸素と液体燃料の燃焼フレームを細径ノズルで絞り溶射粉末を投入する高速フレーム溶射法(HVOF: High Velocity Oxygen Fuel)でも緻密で密着性に優れ、経済性も良好なためLPS代替として使われている。
耐酸化性に優れたNiCrAlY、耐食性(硫化腐食)に優れたCoCrAlY、両者の欠点を取り除いたNiCoCrAlY、延性に優れたCoNoCrAlYなど多種のMCrAlY合金が開発された。MCrAlY合金皮膜は高温域での延性に優れ、基材のNi基超合金のクリープ寿命、高温疲労寿命には影響を及ぼさない。

以上のコーティング技術は、次に示すセラミック遮熱コーティングの下地層(ボンドコート)としても適用されており、高温耐食・耐酸化機能の維持はもちろんのこと、セラミック遮熱層(トップコート)の密着性向上にも大きな影響を及ぼしている。
セラミック遮熱コーティング
セラミック遮熱コーティング(TBC:Thermal Barrier Coating)は、裏面が強制冷却されている耐熱合金基材の表面に、低熱伝導率の酸化物セラミックスをコーティングすることで、表面温度を低下させる技術である。
TBC無しの場合には、耐熱合金基材裏面が強制冷却されていても、基材表面は燃焼ガスで高温に曝される。一方、TBC有りの場合には、基材に比べて低熱伝導率のセラミックス層内で温度降下が生じ、耐熱合金表面の温度を低く抑えることができ、耐熱合金の長寿命化や冷却空気量の低減にも有効である。
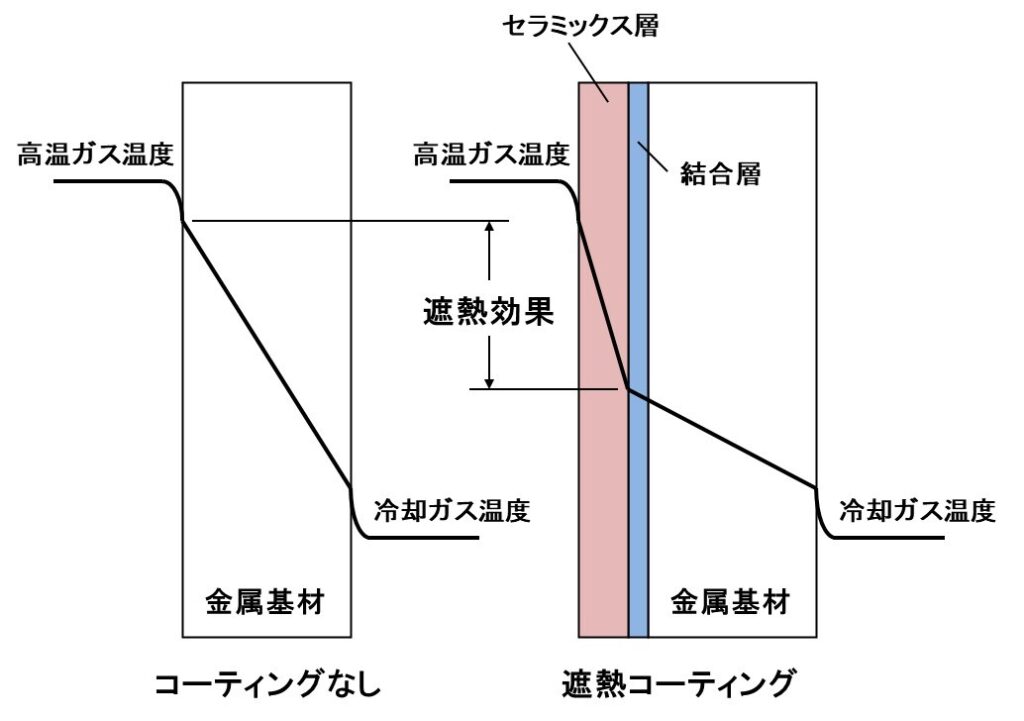
第一世代の遮熱コーティング(TBC)は、生産性に優れた多孔質な大気プラズマ溶射(APS)が採用され、高温の燃焼ガスに曝される燃焼器内面に施工された。
TBCの耐久性向上をめざし、ボンドコートはNiAl→CoCrAlY→NiCrAlY→NiCoCrAlY、トップコートはCaO、MgO安定化ZrO2(CSZ、MSZ)→Y2O3部分安定化ZrO2(YSZ)、中間層に熱応力緩和効果を持たせるなどの変遷を経て、現在の主流であるMCrAlY/7~8mass%YSZの2層遮熱コーティングに至った。
TBCトップコートにYSZが採用されたのは、遮熱特性と共に、耐熱サイクル特性、耐熱衝撃特性にも優れているためである。APSにより形成されたYSZ皮膜は気孔率10~25体積%で、積層方向に多数の微小割れが生じるため熱伝導率が低く、応力誘起マルテンサイト変態による強靭化機構が働くと考えられている。
しかし、破損した場合のリスクが高いため、ガスタービン動翼へのTBC適用は慎重に進められた。
第二世代の遮熱コーティングは、Pt/Al複合コーティング後に軽く表面研磨し、EB-PVDによりセグメンテーションされたYSZトップコートを積層したものが主流で、タービン動静翼の表面に施工されている。
EB-PVDは真空容器中でYSZに高出力電子ビームを偏向照射して溶融蒸発させ、高温(900~1000℃)に予熱した基材表面に成膜させるプロセスで、面外に<100>配向した柱状組織が形成できて、縦割れが容易に導入される。耐エロージョン性、耐熱衝撃性、耐熱サイクル性に優れたTBCとして使われている。
第三世代の遮熱コーティングは、量産化に優れたLPSによるMCrAlY合金ボンドコート上に、APSあるいはEB-PVDによるYSZトップコートを施工したもので、TBCの耐久性が著しく改善された。
LPSーMCrAlYボンドコートの表面粗さはRa>6µmで優れたアンカー効果を発揮し、APSーYSZトップコートの密着性保持には有効である。耐熱サイクル特性に優れたEB-PVDによるYSZトップコートの施工には、グリッドブラスト、グラインダー、ショットピーニングなどでボンドコート表面をRa≦2 µmに平滑化する必要がある。
EB-PVDとAPSで形成された7YSZ皮膜の高温熱伝導率は異なる:
■緻密な7YSZ焼結体の高温熱伝導率は2.2W/mKであるが、EB-PVDで形成された7YSZは1.5W/mK、APSで形成された7YSZは0.8W/mK程度で異なる。APS皮膜は多数の気孔や微小き裂が熱抵抗として働くが、EB-PVD皮膜は柱状晶中心部の欠陥が少ない部位を熱が伝わるため熱抵抗は少ない。
■EB-PVDで形成された7YSZ皮膜は、基材表面近傍ではYSZが等軸粒子(粒径:0.5~1㎛)の多結晶組織で内部欠陥が多く含まれるが、成長した柱状晶組織(直径:2~10㎛)では欠陥密度が減少する。
■EB-PVDで形成された7YSZ皮膜の高温熱伝導率は膜厚によって変化する。100㎛以下では1.0W/mKであるが、100㎛以上では1.5~1.8W/mKまで増加するため、厚膜化には注意を要する。
■APSで形成された7YSZ皮膜の高温熱伝導率は膜厚によって変化しない。
現時点で、耐熱合金は表裏面の高度冷却機構により表面温度を400~600℃程度下げることが可能であり、加えてTBCを施すことで耐熱合金の表面温度を50~150℃程度下げることが可能である。

現在、YSZのセグメント構造TBCを超える次世代の遮熱コーティングに関して、YSZよりも低熱伝導率で相安定性に優れた希土類ジルコン酸塩、屈折率が高い希土類チタン酸塩などを候補材とした基礎研究が進められているが、いずれも破壊靭性が低いため熱サイクル寿命の改善が鍵となっている。
また、プロセス開発では、化学蒸着法(CVD:Chemical Vapor Deposition)、前駆体プラズマ溶射(SPPS:Solution Precursor Plasma Spray)、プラズマ溶射・物理蒸着法(PS-PVD:Plasma Spray-Physical Vapor Deposition)、サスペンションプラズマ溶射(SPS:Suspension Plasma Spray) での柱状組織形成、レーザーの表面溶融による縦割れ導入など様々な試みが進められている。
一方、1990年頃から飛行中の航空機エンジンに取り込まれた砂や火山灰などが、TBC表面に付着して溶融損傷を生じる問題が報告されている。付着物の主成分がCaO、MgO、Al2O3、SiO2であることから、頭文字をとって「CMAS損傷」と呼ばれ様々な対策が検討されている。
セラミック基複合材料(CMC)の開発
高バイパス比化と並ぶ燃費低減方法は、タービンの高圧力比化と高温化による熱効率向上である。しかし、従来のNi基超合金を使用する限り冷却は不可欠で、冷却空気量の増加で燃費低減効果が失われる。
そこで、2016年に就航したエアバス「A320neo」に搭載された「LEAP-1A」エンジンには、セラミックス基複合材料(CMC:Ceramic Matrix Composites)が、民間航空機エンジンの高温静止部品に初適用された。
タービン・シュラウドに採用されたSiC/SiC複合材料(SiC密度:3.1g/cm3)は、従来のNi基超合金(Ni密度:8.9g/cm3)に比べて軽量で、耐熱温度は1300℃(米国では2400℉と記載)とされ、単結晶Ni基超合金(SC)と比べて約200℃高い。
また、機械的性質では2倍の高温強度を有し、引張強度:250~325MPa、曲げ強度:400~550MPa、圧縮強度:1000~1300MPa、破断ひずみ:0.2~0.7%と公表されている。
CMCの製造技術
セラミック基複合材料(CMC)は、炭化ケイ素長繊維強化炭化ケイ素基複合材料(SiC/SiC composite、以下ではSiC/SiC複合材料)が主流となり、2000年初期に基礎開発が終了した。
製造プロセスは、セラミックス繊維による織物構造(プリフォーム)を作る「製織工程」と、その後に織り上げたセラミックス繊維間にマトリックスを形成する「複合化工程」とで構成される。SiC/SiC複合材料の基本的な材料特性は、この複合化工程により大きな影響を受ける。
代表的な複合化工程として、前駆体含浸・焼成法(PIP:Precursor Impregnation and Pyrolysis)、化学気相浸透法(CVI:Chemical Vapor Infiltration)、反応焼結法(RS:Reactive Sintering)とプリプレグ/溶浸法(MI: Melt Infiltration)、熱間加圧焼結法(HP:Hot Pressing)などが開発されている。
ただし、ファインセラミックスで主流の常圧焼結法は採用されていない。一般にSiCの常圧焼結法では焼成温度が2000℃を超えるため、現有のSiC繊維は損傷を受けてためである。

CMCの製造プロセスは、未だ開発途上にあるといえる。今後、経済性も含めて部品形状に合わせた様々な方法が開発されるであろう。現在、第一世代のSiC/SiC複合材料として航空機ジェットエンジン用に実用化されているのは「プリプレグ/溶浸法(MI)」のみである。
前駆体含浸・焼成法(PIP)
初期に開発されたPIP法はプリカーサー含浸・焼成法とも呼ばれ、前駆体ポリマーを加熱溶融あるいは溶剤に溶解して液相とし、含浸と焼結を複数回繰返すことでSiC繊維プリフォーム中にSiCマトリックスを形成する。原理的に緻密なマトリックスを得ることは困難で、気孔率が20~30%程度は残留する。
日本カーボンがニカロン繊維へCVD法により炭素をコーティングし、PIP法で製造した「ニカロセラム」などを商品化した。現在は、アート科学が製造を引き継ぎ、湿式法による安価なSiNBC系界面コートやβ-SiCナノ粒子などを利用した先進PIP法を開発し、SiC/SiC複合材料の供給を行っている。
化学気相浸透法(CVI)
加熱したSiC繊維プリフォーム中に原料ガスの送給・吸引を繰り返し、繊維表面に化学気相反応によりBN界面コーティング、その後にSiCマトリックスを析出させる。マトリックスを効率よく析出させるためチャンバー内の原料ガス温度、ガス濃度、処理時間などの最適化が重要である。気孔率は10~15%程度は残留する。
複雑形状部品への対応が可能で高品質のSiCマトリックスが形成できるため、IHIは航空機ジェットエンジン用のCMCタービン部品製造にCVI法を採用している。CVI後に残留した連続空孔を埋めるため、固相含浸(SPI:Solid Phase Infiltration)法や低融点(1325℃)のSi-10at%Y合金の高温真空含浸法などを検討している。
反応焼結法(RS)とプリプレグ/溶浸法(MI)
SiC繊維プリフォーム中にSiCとCの粉末を含むスラリーを含浸し、その後にSi(融点:1414℃)を溶融含浸し、C+Si→SiCの反応により短時間でSiCマトリックスを形成する。焼結収縮率が±1%以内と小さいため大型・複雑形状対応が容易で、PIP法やCVI法に比べて短時間で緻密なマトリックスが得られる。
東芝は、発電用ガスタービン高温部品へのCMC適用に向け「反応焼結法(RS)」を開発した。CVD法によりBN/SiCの2層界面コートを施工し、部品形状に繊維プリフォームを編み上げ、SiC+C粉末のスラリーを加圧含浸し、真空炉中1450℃でSi(Bを微量添加)を溶融含浸する。気孔率は2%以下を実現した。
米国GEは、「LEAP」エンジン向けに「プリプレグ/溶浸法(MI)」を開発した。SiC繊維表面にCVD法で界面コートを施し、バインダー+SiC and/or Cからなるスラリー中を通して湿式ドラムで巻き取り、一方向繊維テープを製造する。その後、所定の形状に切断・積層し、500℃以下で脱脂処理して繊維プリフォームを作製する。この繊維プリフォームを真空炉中で1400~1450℃に加熱してSiを溶融含浸し、C+Si→SiCの反応により短時間で緻密質マトリックスを形成する。
いずれのプロセスでも未反応のSiが残留するため、CMCの使用上限温度がSiの融点(1414℃)で規定される。実際に、第一世代のSiC/SiC複合材料の耐熱温度は、安全性を考慮して1300℃とされている。
熱間加圧焼結法(HP)
SiC繊維とSiCマトリックスの原料粉末を一緒に加圧焼結(HP)する方法である。マトリックス原料として単一粉末原料を使用する場合や、複数原料を使用して反応焼結あるいは液相焼結により複合化を行う場合もある。緻密なマトリックスのCMCが製造できるが、大型・複雑形状部品の製造は困難である。
平均粒径:15~30nmのSiC粉末に焼結助剤(Y2O3, Al2O3, SiO2)を添加したスラリーから、テープキャスティングで作製したグリーンシートと、炭素界面コートを施したSiC繊維周辺にSiCスラリーを塗布したプリプレグシートを積層し、ホットプレスで成形する。2020年9月に京都大学発ベンチャーのNITEが商品化した。
また、宇部興産はチラノ繊維の製造過程品をHP法で成形して、2種類の繊維集合体セラミックスを開発している。SAチラノヘックス(繊維体積率:約 95%、気孔率:約 1%、密度:約 3.1g/cm3)と、チラノヘックス(繊維体積率:約 87%、気孔率:約 1%、密度:約 2.4g/cm3)で、2014年11月から超高温センターが製造・販売している。
化学液体蒸着法(CLVD)
化学液体蒸着法(CLVD:Chemical Liquid Vapor Deposition)は膜沸騰化学気相浸透法(FBCVI:Film Boiling Chemical Vapor Infiltration)とも呼ばれており、1990年代からフランス・サクレー原子力庁センターの研究所で、緻密なSiCを合成する手法として開発が進められてきた。
最近になりC/C複合材料、C/SiC複合材料、SiC/SiC複合材料を対象とし、CVI法に比べて短時間で緻密な界面コートとマトリックスを形成できるプロセスとして注目されている。繊維プリフォームを液体前駆体の溶液中に浸漬して加熱処理を行うプロセスである。
IHIエアロスペースは、炭素繊維プリフォームを液体ポリシラン(LPS)に浸漬して1150~1200℃で6h、または6h×3回の処理を行うことでマトリックス形成し、その後にセラミックス化のためArガス雰囲気で1500℃、または1650℃の熱処理を施してC/SiC複合材料を作製している。SiC/SiC複合材料の開発にも着手している。
耐環境コーティング技術
SiC/SiC複合材料は、高温大気中で優れた耐酸化性を示す。”SiC+3/2O2(g)→SiO2+CO(g)”の反応式から、SiC表面には密着性に優れた緻密な保護性酸化皮膜(SiO2)が形成される。
しかし、ガスタービンのような水蒸気(H2O(g))を多く含む燃焼ガス雰囲気では、”SiC+3H2O(g)→SiO2+3H2(g)+CO(g)” ⇒ ”SiO2+2H2O(g)→Si(OH)4(g)”の反応式により、SiO2のガス化で揮散が進み顕著な減肉が生じることが報告されている。
SiC/SiC複合材料を航空機ジェットエンジンの高温部品に適用するためには、耐環境コーティング(EBC:Environmental Barrier Coating)が不可欠とされ様々な研究開発が行われた。
プリプレグ/溶浸法(MI法)で製造されたSiC/SiC複合材料の熱膨張係数は4.0~5.0X10-6/℃である。この上に形成される耐環境コーティングの割れや剥離を回避するためには、金属基材上に形成されたセラミック遮熱コーティング以上に熱膨張係数のマッチングが重要となる。
1990年、米国航空宇宙局(NASA)のHSCT/EPM (High Speed Civilian Transport/Enabling Propulsion Materials)プログラムで、NASA、GE、UTRCにより「BSAS/Mullite+BSAS/Si」のEBCが開発され、第一世代の耐環境コーティングである。
使用上限温度は、BSASとTGO層に形成されるSiO2との共晶点(1310℃)により規定されるため、1300℃級EBCと位置付けられている。民間航空機エンジン「LEAP」のタービン高温部品であるシュラウド(表面温度:1200℃)に採用されている。
トップコートの高温水蒸気腐食に優れたBSAS(1-xBaO・xSrO・Al2O3・2SiO2、0≦x≦1)と熱応力緩和を目的としたムライト(3Al2O3・2SiO2)とBSASの混合組織は大気プラズマ溶射、酸素拡散防止層と密着性向上層としてSiボンドコートが減圧プラズマ溶射による成膜された。

一方、近年では火山灰や砂塵による航空機ジェットエンジンの損傷で注目を集めている「カルシウム・マグネシウム・アルミノシリケート(CMAS:Calcium Magnesium Alumino-Silicate)損傷」が、EBCを施したSiC/SiC複合材料部品においても解決すべき課題として重要視されている。
1300℃級EBCの場合、約1200℃以上で溶融したCMASとBSAS界面ではBa、Sr元素が拡散反応し、エンジン停止による冷却過程でEBCが損傷を受けて減肉する。
航空機ジェットエンジン・メーカーの動向
限界が見えてきた耐熱超合金に替えて、セラミックス基複合材料(CMC)の適用が航空機エンジンメーカーを中心に進められ、耐環境コーティングと共に、今後の重要な開発課題と位置付けられている。
航空機ジェットエンジンへのCMC適用で、世界の先頭を走るのは米国GE(現GEエアロスペース)である。一方で、米国のP&W、英国のRRは共にCMCメーカーを買収するなどして、キャッチアップを加速している。
米国GE Aerospace(GEエアロスペース)の開発動向
米国GEエアロスペースは、航空機ジェットエンジンへのCMC適用で世界の先頭を走る。
1974年、米国GEとフランスSNECMA(サフラングループ)は合弁会社CFMインターナショナルを設立し、小型機用航空機ジェットエンジン「LEAP」の共同開発を開始した。表面温度が1200℃に曝される高圧タービン・シュラウドに、「MI-SiC/SiC複合材料」を搭載して軽量化を進めるのが狙いである。
2012年4月、日本カーボン、GE、サフランの合弁会社NGSアドバンストファイバーが、富山県でCMC原料であるSiC繊維の製造を開始した。2019年4月から日本カーボンが製造ライセンスを供与し、GEがアラバマ州ハンツビルでSiC繊維工場を稼働させた。
2014年、CMCジェットエンジン部品の本格的製造工場をノースカロライナ州アッシュビルに建設した。同年11月には、GEとイタリアTurbocoatingは、耐環境コーティング(EBC)を施工するための合弁会社「Advanced Ceramic Coatings」をサウスカロライナ州ダンカンに設立した。
2014年初め、「LEAPエンジン」向けのCMC製高圧タービン2段目の非冷却シュラウドの生産を、SNECMA(LEAP1Aエンジン)とGE(LEAP1Bエンジン)で開始し、2016年にはエアバス「A320neo」、2017年にはボーイング「B737 MAX」、中国商用飛機有限責任公司(COMAC)「C919」に搭載された。
LEAP エンジンには 18個/台に分割されたリング状のCMCシュラウドが装着されており、2021年8月にはアッシュビルで10万台目のCMCシュラウドの出荷を公表している。

GEは最新型航空機エンジン「GE9X」の5種類の高温部品(高圧タービン第一段シュラウドと静翼、高圧タービン第二段静翼、燃焼器の内・外面ライナー)へのCMC採用を公表。GE9Xは現行モデルのGE90に比べて燃費が10%高く、2020年にFAA認証を取得し、次世代旅客機のボーイング「B777X」に搭載される。
さらに、米国空軍の「アダプティブ(適応型)エンジン移行プログラム(AETP:Adaptive Engine Transition Program)」の下で「XA100」エンジン開発にも取り組み、低圧タービンブレードへのCMC採用を検討している。

2022年7月、GEは3分社計画を発表した。ヘルスケア事業のGE HealthCare Technologies(ヘルスケア・テクノロジーズ)は、2023年1月に分社化を完了。2024年4月に航空宇宙事業にフォーカスするGE Aerospace(GEエアロスペース)は、エネルギー事業のGE Vernova(GEベルノバ)の分社化を完了した。
プラットアンドホイットニー(P&W)の開発動向
2019年11月に、米国ユナイテッドテクノロジー(UTC:United Technologies)の航空機エンジン部門であるプラットアンドホイットニー(P&W:Pratt & Whitney)は、カリフォルニア州カールスバッドにCMCのエンジニアリング&研究開発施設を開設すると発表した。
2020年4月、UTCの航空宇宙事業はレイセオンと経営統合し、レイセオン・テクノロジーズに社名変更された。エアバス「A320neo」向けの2機種のエンジンには、CFMインターナショナル「LEAP1A」とP&W「PW1100G-JM」が採用されたが、CMC製高温部品の適用は補修の難しさと経済性から断念した。
「PW1100G-JM」には、30年かけて開発してきたギヤードターボファンエンジン(GTF)が採用され、遊星ギアによりタービンとファンが最も効率よく作動できる機構を備え、高い燃費効率と環境性を実現している。
一方、CMCとEBCの開発は親会社UTCがNASAプロジェクトで進め、世界最大の航空宇宙•防衛製品サプライヤーであるUTCエアロスペースシステムズ(UTCAS:UTC aerospace systems)を傘下に置いている。
UTCASは、2012年にUTC子会社の航空宇宙システム設計・製造のハミルトンサンドストランド(Hamilton Sundstrand)と、新たに買収した「MI-SiC/SiC複合材料」の製造で実績のある米国グッドリッチ(Goodrich Corporation)が合併して設立された。
2021年7月に、次世代のPurePower®Geared TurboFan(GTF)エンジンへのCMC適用を公表した。同年10月、NASAの「Hybrid Thermally Efficient Core(HyTEC)プロジェクト」で、次世代の単通路航空機の燃料消費と排出ガスを削減する高度な高圧タービン技術の開発を推進する。
「HyTEC」がめざす技術には、現在のCMCよりも高い温度で動作できる次世代CMC材料、耐環境コーティング、新しいコンポーネント設計と効率を可能にする高度な冷却および空力アプローチが含まれる。
2024年4月、東京工科大学セラミックス複合材料研究センター(TUT)は、プラット・アンド・ホイットニー(P&W)と、SiC/SiC複合材料の共同研究を開始した。P&Wが資金を提供し、SiC/SiC複合材料の各温度での基本特性を調べ、得られた特性について理論的な研究が行われる。
ロールスロイス(RR)の開発動向
2012年、RRは1300℃級のSiC/SiC複合材料製の高圧タービン動翼の設計・製造・試験を終了し、2013年には英国の環境適合性エンジン(EFE:Environmental Friendly Engine) プログラムの一環で、繰返し耐久性検証試験を実施し、2016年末から地上試験を開始している。
最終版の「アドバンス3」では、「トレントXWB」のファンと「トレント1000」の6段の低圧タービンを使い、新設計の高圧(HP)コンプレッサー・タービンを組み込み、希薄燃焼(Lean-burn)の燃焼室と1段高圧タービンのアウターシールにSiC/SiC複合材料を採用し、健全性を確認した。
並行して、2013年5月、ロールスロイス(RR:Rolls-Royce Limited)は、「CVI-SiC/SiC複合材料」を製造する米国ハイパーサーム(Hyper-Therm High Temperature Composites)を買収して「Rolls-Royce HT」とした。
2016年11月、CMC研究開発に特化した「Rolls-Royce HT」の新工場を、カリフォルニア州サイプレスに開設した。元々は極太のSCS-Ultra繊維(繊維径:142μm、引張強度:5900MPa、弾性率:415MPa)でCVI-SiC/SiC複合材料を製造していたが、現在は繊維径:10~15μmのSiC繊維を使う開発に移行した。
2021年から飛行試験を予定している希薄燃焼/低エミッション燃焼の「ウルトラファン」エンジンには、「アドバンス3」の高圧(HP)系コアが使われている。
すなわち、1段高圧タービン・アウターシールと静翼には耐CMAS性に優れたEBCが施されたSiC/SiC複合材料が採用された。動翼や燃焼器への適用は、CMC技術の成熟に伴い採用を検討するとしている。
一方、米国ボーイングはCLEEN(Continuous Lower Energy, Emissions and Noise)開発計画を進めており、ボーイング技術研究所が開発した酸化物系CMCの排気ノズル部品を、RRのTrent1000エンジンに搭載し、NASAステニス宇宙センター内のRR屋外試験設備で73hの燃焼試験を終了した。
その後、酸化物系CMCの排気ノズル部品はボーイング787-8ドリームライナーに取付けられ、2014年後半からの飛行試験で耐久性55000hを達成している。

航空機ジェットエンジン材料の未来予測
2025年3月、経済産業省は国内航空機産業の強化のため、2025年度から5年間で1200億円規模の支援を行う方針を表明した。次期航空機の機体部品の生産に向けた技術的実証や供給網の強化、低燃費エンジンの開発を支援する。ドローンなど無人機の量産体制確立を図るための枠組みも設ける。
日本が強みを持つ炭素繊維や複合材などの主要部品の技術を磨き、脱炭素に対応した次期航空機などの開発・生産能力の獲得をめざし、海外に依存している整備や修理でのノウハウ取得も促す。また、国産旅客機の事業化に向け、2035年までに機体の量産や次世代航空機の開発目標を掲げている。
2025年4月、経済産業省は航空機産業の供給網強化に向けた官民検討会「サプライチェーン現代化検討会」を新設する。日本航空宇宙工業会、三菱重工業、川崎重工業、IHIの他、胴体・主翼などの機体構造体、ブレード・ディスクなどのエンジン関係、内装品・アクチュエーターなど装備品の関連企業も参加する。
欧州エアバス、米国ボーイングは次期航空機の開発構想で、部素材の高機能化や生産機数を増やす高レート化などを視野に入れており、サプライヤーの能力向上や国内産業の規模拡大が必要である。
既に、経済産業省は航空機部品を経済安全保障上の「特定重要物資」に指定し、744億円の予算で大型鍛造品や複合材料などの増産・研究開発を支援している。また、「GX移行債」を活用して航空機の高レート生産などの設備投資や、工程認証取得に向けた生産実証を支援する方針を掲げている。
現時点で、商業用航空機ジェットエンジンの基本的な開発方向は、「高バイパス比」と共に「高圧力比・高温化」による燃費低減である。今後、鍵となる技術は、セラミックス複合材料(CMC)と耐環境コーティングの高温化対応であることは間違いない。
米国が先行する次世代CMC開発
既述のように、第一世代のSiC/SiC複合材料の耐熱温度は1300℃(米国では2400℉と記載)で、単結晶Ni基超合金(SC)と比べて約200℃高く、飛躍的な耐熱性の向上を実現した。2016年からCFMインターナショナルより、航空機エンジンの静止部品へのCMC適用が開始されている。
SiC/SiC複合材料は約1100℃以上の水蒸気を含む燃焼ガス雰囲気に曝されると、顕著な高温水蒸気腐食が生じるため、CMC表面には第一世代の耐環境コーティング(EBC)が施工されている。
1999年からNASA「Ultra-Efficient Engine Technology」プログラムでは、より耐熱性に優れた第二世代の耐環境コーティングの開発が進められている。開発目標は、EBC表面温度が1482℃(2700℉)、EBC/CMC界面温度が1316℃(2400℉)である。
すなわち、第一世代のMI-SiC/SiC複合材料(耐熱温度:1300℃級)を対象にして、遮熱特性に優れた表面温度1500℃級のTEBC(TEBC:Thermal-Environmental Barrier Coatings)の開発が進められている。
各種EBC候補材料について1500℃、1気圧における水蒸気腐食試験が行われた結果、希土類シリケートであるモノシリケート(RE2SiO5)とダイシリケート(RE2Si2O7)(REとは、Yb、Y、Lu Scなど)が、耐高温水蒸気腐食特性に優れていることが明らかにされている。
中でも、Y2SiO5、Er2SiO5、Yb2SiO5は熱膨張係数がSiCと良く一致しており、実際にMI-SiC/SiC複合材料の表面にプラズマ溶射法でSi/ムライト/Yb2SiO5がコーティングされ、高圧バーナー加熱試験により健全性が確認されている。
また、次世代EBC材料として注目されているイットリウムケイ酸塩(Y2SiO5、Yb2Si2O7)も、CMASと反応することが示されている。EBCと反応して固着したCMASはEBCの割れやはく離を引き起こすため、航空機ジェットエンジン向けのEBCにはCMAS対策を施す必要がある。現在は、TBCのCMAS対策で効果を上げたGd2Zr2O7層を最外表面に形成したEBCなどが検討されている。
また、NASAのグレン研究センターではスラリーコーティングによるYb2Si2O7ベースのボンドコート、すなわち酸化物セラミックス系ボンドコートの開発が進められ、バーナー加熱試験が実施されている。
EBCボンドコートについては、SiC/SiC複合材料との高い密着性の確保に加えて、TGO層の成長抑制によるEBCの長寿命化が課題である。
現在、欧米では第二世代のSiC/SiC複合材料の開発が耐熱温度1500℃を目標に進められている。商品化されているSiC繊維の耐熱温度は長時間加熱では1400℃程度にとどまっており、NASAを中心に新たなSiC繊維の開発が進められている。また、中国や韓国でも、SiC繊維の開発が進められている。
その場合の遮熱特性に優れた第三世代の耐環境コーティング(TEBC:Thermal-Environmental Barrier Coatings)の開発目標は、EBC表面温度が1650℃(3000℉)、EBC/CMC界面温度が1482℃(2700℉)である。新たなTEBCの開発が不可欠である。
日本におけるCMCの開発動向(主にIHI)
1990 年代~2000 年頃まで、国家プロジェクトとして、「超音速輸送機用推進システム研究開発(HYPER)」(1993~2003年度)、「先進材料利用ガスジェネレータ技術開発(AMG)」(1993~2003年度)、「環境適合型次世代超音速機用 推進システムの研究開発(ESPR)」(1999~2004年度)、「シナジーセラミックス」(1994~2003年度)が実施され、航空機用ジェットエンジン部品などの要素技術の一部でCMC開発が行われた。
その後、CMC開発への国からの支援が細り、多くの企業も事業化の見通しが得られずに撤退するなかで、IHI、日本カーボンなどにより国家プロジェクト「軽量耐熱複合材CMC技術開発」(2008~2010年度)、「タービン動翼に適用可能な軽量耐熱複合材料の研究開発」(2010~2012年度)が進められた。
2010年代に入り、米国GEによるSiC/SiC複合材料の航空機エンジン部品の開発状況が伝わる。
これを受け、NEDO「戦略的省エネルギー技術革新プログラム」(2013~2015年度)、内閣府主導の戦略的イノベーション創造プログラム(SIP)では「革新的構造材料」と「耐環境性セラミックコーティングの開発」(2014~2018年度)、NEDO/METI「次世代構造部材創製・加工技術開発」では「軽量耐熱複合材CMC技術開発(基盤技術開発)(2011~2015年度)と「軽量耐熱複合材CMC技術開発(高性能材料開発)(2015~2019年度))など多くのプロジェクトが進められた。
SIPの「1400℃級耐環境コーティングの開発」では、Si溶浸で緻密化したCVI-SiC/SiC複合材料に、EB-PVDで遮熱性を有するセグメント構造のYb2SiO5層、その下に水蒸気遮蔽性の緻密なYb2SiO5→Yb2Si2O7傾斜組成層、酸素遮蔽性のムライト、ムライトの分解を防ぐSiAlONボンドコートの多層EBCが開発された。
2021年6~7月、IHIは、防衛装備庁のP-1固定翼哨戒機用の高バイパス比ターボファンエンジン「F7-10」に1400℃級CMCシュラウド(多層EBCを施工)を組み込み、実証試験を行った。
また、NEDO「次世代複合材創生・成型技術開発」(2020~2024年度)の中で、IHIは耐水蒸気性に優れた希土類ケイ酸化物粉末を織物内に含浸後、共晶組成の酸化物を織物に溶融含浸させた1400℃級CMC材料の実用化を進め、耐CMAS性に優れたYb2O3-Al2O3-HfO2系EBCを開発した。

現在、NEDO「航空機エンジン向け先進材料技術の開発・実証」(2023~2027年度)が、IHI、JAXA、UBEにより進められている。1400 ℃級CMC材料の製造・量産技術開発では、IHI横浜事業所のCMC製造専用棟にCMC製造設備を集約して、量産条件での製造技術実証を進めて課題の抽出・解決をめざしている。
国内でのCMCとEBCの開発は航空機エンジンメーカーのIHIが先頭を走っており、SiC/SiC複合材料によるタービン高温部品の開発が進められている。しかし、2025年3月時点で、飛行試験には至っていない。

その他の国内企業のCMC開発
2023年10月、「JAXA革新的将来宇宙輸送プログラム」に選定された湘南先端材料研究所のSiC繊維強化Al2O3(CMC)が、JAXAのアーク加熱風洞試験(750kW)で850℃の耐熱性を実証した。
Al2O3マトリックスにホウケイ酸ガラスをベースとした特殊な添加剤を配合したプリプレグを積層し低温焼結するプロセスで、SiC繊維の表面コーティングを施さず、SiC繊維も低価格品を使用する。850℃の曲げ強度も十分高く、比重は3以下と軽量で、面積1m2×板厚2mmの量産コストは100万円以下をめざしている。
2024年2月、三菱ケミカルグループは、高耐熱CMC材料(C/SiC)を発表。ピッチ系炭素繊維を用い、表面に酸素透過バリア層を設けることで、空気中で1500℃×1h保持しても強度が低下しない。
「JAXA革新的将来宇宙輸送システム研究開発プログラム」で参考値として示されている1,600℃で800秒間の条件にも耐えうる材料である。今後は、2030年代前半の実現をめざす宇宙輸送システムの往還機熱シールドや、宇宙利用・回収プラットフォーム部材への採用を視野に耐熱性向上をめざす。
2024年8月、東ソーは高耐熱酸化物系CMCを発表した。アルミナ繊維系「TCA-01」とムライト繊維系「TCM-01」をベースに酸化物系マトリックスを組み合わせた。大気中1200℃、1000hの熱暴露後でも強度が低下しない。高温での繊維の粒成長を抑制する元素を、均質にドープする新規組織制御技術(UDM)を開発した。
酸化物系CMCは、高温酸化雰囲気での耐久性に優れているが、高温域での繊維の結晶粒成長や繊維中の空孔形成が進むことで、800~1000℃以上での強度低下が問題であった。これが改善でき、SiC系CMCと比べて低コストであるため、適用部品の拡大が期待できる。
■2000年代に入るまで、セラミックス基複合材料(CMC)の開発は日本が世界をリードしてきた。なぜなら、SiC繊維の開発・供給メーカーは日本カーボンとUBE(元宇部興産)の2社のみであったから。
■2000年代に入り、政府からの開発支援が先細る中で、IHIと日本カーボンを除く多く国内企業がCMC開発から撤退した。しかし、米国ではGEが粛々とCMC開発を継続していた。
■2010年代に入り、状況が一変したのはGE、サフラン、日本カーボンが合弁会社を作り、SiC繊維の生産を開始した時である。慌てて、政府支援を復活させたものの後の祭りであった。
技術は継続して”なんぼ”。IHIが、何とかCMC開発を継続してきたのが救いである。今後の鍵を握るのはUBEによるSiC繊維の耐熱性向上で、東レの炭素繊維のように頑張れるか、期待したい。
新しい接合技術の適用
航空機構造では、溶接が比較的難しいアルミニウム合金やチタン合金、溶接が不可能なCFRPなどが多用されているため、胴体外板同士の締結や外板と補強部材の締結などにはリベットやボルトによる機械継手が多く採用されているのが現状である。
これら航空機構造の機械継手部や溶接継手部では安全率を高く設定する必要があり、機体の軽量化の障害となっている。そのため摩擦撹拌接合(FSW)や線形摩擦接合(LFW)などの高い信頼性を保持できる新しい接合技術の適用が望まれている。
摩擦撹拌接合(FSW)
摩擦撹拌接合(FSW:Friction Stir Welding)は、1991年に英国TWI(The Welding Institute)によって開発された新しい接合プロセスである。高速回転ツールを接合部に押し当て、摩擦熱を生じさせて軟化した部分を攪拌し、塑性流動を生じさせて固相接合する。
材料を局部的に溶かして接合する従来の溶接技術に比べて、溶接変形や強度劣化などを抑制でき、アルミニウム合金のような難溶接材料でも大気中での接合が可能であるため、鉄道車両への適用に始まり、自動車や航空宇宙機器への適用が急速に広がっている。
欧州ではWAFS(Welding of Airframes using Friction Stir)やTANGO(Technology Application to the Near Term Business Goals and Objectives of the Aerospace Industry)などの国家横断的プロジェクトなどで、航空機構造へのFSW適用が積極的に進められた。
欧州エアバスではリベット接合の代替として、中央翼、主翼、胴体などの 1 次構造部への適用検討が積極的に進められた。A350XWB機の胴体外板の長手方向の接合にFSW適用が検討されたが、設計変更により胴体構造がアルミニウム合金からCFRPに変更され、FSW 適用も立ち消えている。
米国ボーイングでは、宇宙機器であるデルタロケットやスペースシャトルのアルミニウム合金製あるいはアルミニウム-リチウム合金製の燃料タンク製造にFSWを適用している。
航空機の1 次構造部への適用検討は遅れているが、輸送機のアルミニウム合金製床構造部などへの適用が始まっており、B747やB777 Freighterのカーゴバリヤービーム組立にFSWが使用されている。
米国Eclipse Aviationでは、小型ジェット機「Eclipse 500」へのFSW適用を公表している。外板と骨材の重ね接合のリベットを廃してFSWを採用し、大幅なコスト低減を実現した。また、翼部材にもFSWを採用しており、富士重工業が施工している。
三菱重工業は、2005年にH-ⅡB ロケットのアルミニウム合金製の推進薬タンク製造にFSWの適用を公表している。ボビンツールと呼ばれる接合工具を実用化して裏当て金なしの状態でFSWを行い、タンク軸方向接合に加えて円周方向接合を実現している。
川崎重工業は、2012年にリベット結合や抵抗スポット溶接の代替となる摩擦攪拌点接合(FSJ:Friction Spot Joining)技術を開発し、自動車メーカーの生産ラインに導入された。接合部に工具の圧入痕が残るため、航空機の機体接合用に平滑な外観が得られる穴無しFSJ接合ツールを開発している。
現在、アルミニウム合金以外にも、FSWによる金属材料の接合技術開発は難燃性マグネシウム合金、チタン合金、各種鋼材などについても実施されている。
今後、航空機機体へのCFRP適用が増加すると、耐食性の観点からチタン合金の適用増が見込まれている。チタン合金とアルミニウム合金、チタン合金とCFRPなどの異種材料接合について、信頼性の高い接合・接着技術の開発と、継手設計や非破壊検査を含めた総合的な接合技術の開発が重要である。
線形摩擦接合(LFW)
航空機ジェットエンジンでは、動翼(Blade)とディスク(Disk)を一体化したブリスク(Blisk)を、ファンや圧縮機のロータに積極的に採用する事例が、民間機用の航空機エンジン(2008年:GEnx-1B、2014年:PW1100G-JM、2015年:LEAP-1A)で増加している。
このブリスクは、鍛造素材から動翼部を削り出す製造方法が一般的である。しかし、ファン、圧縮機のディスク、動翼には高価なチタン合金が使われることが多いため、コスト低減のために線形摩擦接合(LFW:Linear Friction Welding)が戦闘機用エンジンなどで採用されている。今後、民間機用の航空機エンジンへの適用拡大が想定されている。
このLFWは、接合する材料同士を押し付け、一方を接合面に平行に線形運動で擦りあわせ、接合界面に発生する摩擦熱を利用して、加圧により塑性変形を与えて接合する固相接合法である。
溶融溶接に比べて接合部の組織粗大化や気孔などの欠陥を生じないが、接合界面に融合不良を生じる場合もあることから、非破壊検査による確認は必須である。特に、異種材料間の接合については、接合界面に金属間化合物が形成される場合も想定され、継手強度評価が重要である。
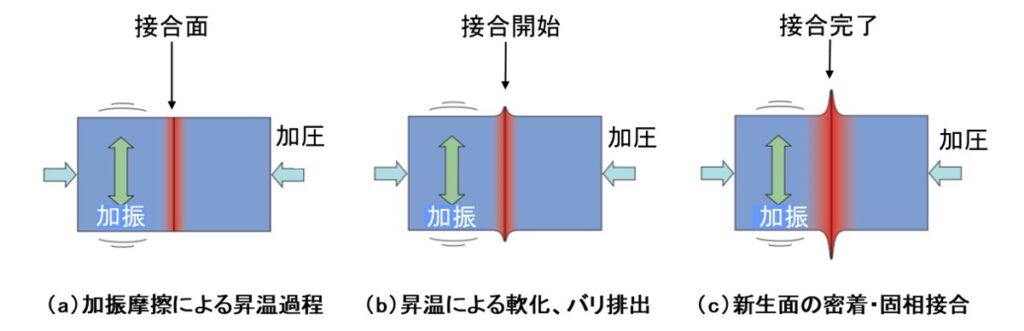
出典: IHI技報
積層造形技術(AM)
最近では、積層造形技術(AM:Additive Manufacturing)の航空機への適用が積極的に進められている。米国ボーイングはB787機にはエアダクト、内装品の小部品、後部ギャレーフィッティングなど25000点のAM部品が採用されている。
また、CFMインターナショナルのLEAPエンジンの燃焼器ノズルにもGEが開発したAM部品が採用されており、高低圧タービン翼やベアリングハウジングなどの試作が行われている。
材料表面へのサメ肌加工
サメ肌を模した微細なリブレット加工が、流体による摩擦抵抗の低減に有効なことは良く知られている。航空機の機体表面へのリブレット加工の実証試験が、航空各社(ルフトハンザ、ANA、JAL)で進められている。1~2%程度の燃費削減が可能な技術で、CO2削減にも有効とされている。
今後のリブレット加工の適用拡大には費用対効果が鍵となる。記録を争う高速水着では、それなりの意味はあったが、経済的に成り立たなければ大面積の航空機の機体での採用は難しい。
バイオミミクリーとは?
バイオミミクリー(生物模模倣)とは、ギリシャ語で「生命」を意味するbiosと「模倣」を意味するmimesisを組み合わせた造語で、生命・自然界における形状・プロセス・生態系から学び、注意深く模倣することで、より持続可能なデザインイノベーションを生み出すことである。
持続可能な社会に向けて、長い年月で進化してきた自然界の叡智に敬意を払い、学ぶことがバイオミミクリーの本質である。
バイオミミクリーが注目を集めた一つに、北京オリンピックに向けて2007年に登場した英国speedoが開発した水着のLZR Racer(レーザー・レーサー)が良く知られている。
サメ肌には、水の抵抗を減らし推進力を高める効果があることが知られており、これを模して高速水着の表面には微細なリブレット加工が施されていた。多くの水泳選手が着用し、次々と世界新記録を出したことは記憶に新しい。2010年4月、高速水着は規制され、実質的な禁止措置が取られたが、、、
サメ肌に関する最近の研究
2018年3月、ハーバード大学とサウスカロライナ大学は共同でサメの皮膚に関する研究を行い、皮膚の微細構造が推進力を高めるメカニズムを解明した。サメの皮膚を電子顕微鏡で見ると、数千もの小さな鱗(うろこ)または小歯状突起で覆われている。
研究チームは小歯状突起をマイクロCTスキャンを使って3次元モデル化し、それを湾曲した翼体の表面に3Dプリントして風洞実験を行った。その結果、小歯状突起形状は薄型の微細な渦発生装置として作用し、翼体の揚力を大きく増加させることを発見した。
一般に、翼体の表面に凹凸を付けると流体による摩擦抵抗は増える。しかし、小歯状突起形状の場合は微細な渦が多数発生して翼体の揚力を大きく増加させることで、摩擦抵抗の増大よりも圧力抵抗の低減の効果が顕著となるのである。最近の新しい知見である。
なるほど、本わさびを擦りおろす時にサメ肌を使うと、きめ細かくクリーミーに仕上がる理由が分かる。空気を多く含ませることで、本わさびの香りとツンとくる刺激が強化されるようだ。
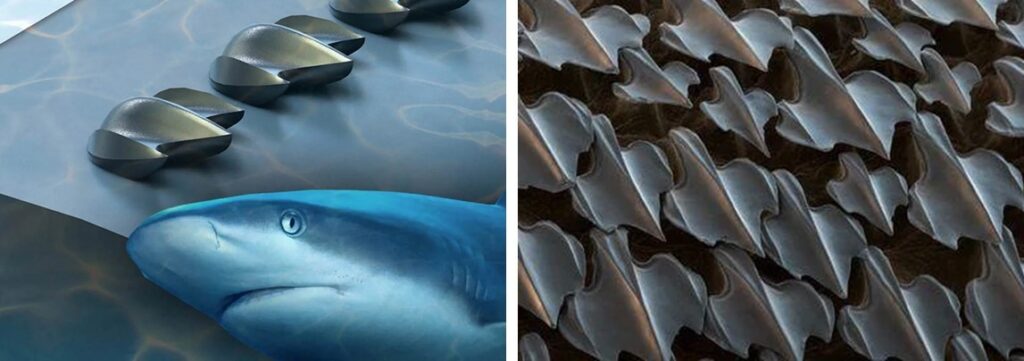
しかし、現時点ではこのサメ肌を直接に翼体の表面に再現するのは経済的に難しい。そのため、高速水着のように微細なリブレット加工(縦溝)を施すことで、様々な機械部品表面の摩擦抵抗の低減が検討されている。
リブレットは摩擦抵抗の低減に有効である。乱流と呼ばれる領域では壁面境界層に強いヘアピン渦が発生し、それに伴う壁面近傍の連続的な縦渦の発生により摩擦抵抗が生じる。リブレット加工を施すと、渦と壁面との間に距離が生じ、接触面積が少なくなることで接触摩擦抵抗を低減する。
リブレット効果を最大化するには、対象部位毎の流体状況(流速・密度・粘性・流れの向き等)に応じて計算流体力学による縦溝構造の設計が重要である。2021年5月、ニコンは、オーストリアのバイオニック・サーフェス・テクノロジーズと、リブレット加工技術の戦略的共同開発契約を締結した。
また、ニコンは、リブレットのレーザー加工の受託サービスを行っており、従来の樹脂フィルムに加えて、樹脂、金属、コーティング・塗膜などにもリブレットを直接付与することが可能である。実際に、ガスタービン圧縮機や超小型ジェットエンジン部品などへの適用検討を進めている。

また、オーウエルは、既存の塗膜上に水溶性の型(モールド)を使ってリブレット(縦溝)を形成する「Paint-to-Paint Method」を開発している。
所定のリブレット形状を写した水溶性モールドに、航空機と同じ塗料を塗工してフィルム化し、航空機の既存の塗膜の上に同フィルムを圧着する。塗膜が硬化した後、水洗いすることで水溶性モールドを除去する手法で、高さ50μmのリブレットを寸法誤差±5%以下で形成できる。
2024年9月、ニコンは、風力発電機の羽根に「リブレット加工」で発電効率を高める実証実験を始めた。摩擦抵抗を抑える効果があり、ユーラスエナジーホールディングスが北海道稚内市に持つ風車の羽根にフィルムを、発電量を1年間かけて比べる。小型風車を使った試験では、発電効率が約3%改善した。
航空機体へのリブレット加工の適用
ルフトハンザ
2021年5月、ルフトハンザグループの子会社Lufthansa Technikとドイツの総合化学メーカーBASFは、サメ肌を模した新フィルム「AeroSHARK」を開発し、ルフトハンザカーゴが2022年より全機に適用すると発表した。機体への新フィルム貼付により、1%程度の燃料削減を見積もっている。
「AeroSHARK」には、リブレットという高さ50μmの微小突起物が何百万個もあり、このフィルムを機体に貼ることで空気抵抗を減らす。ルフトハンザカーゴのボーイング777Fの場合、保有する全10機で約3700トン/年の燃料削減と、1.17万トン/年のCO2排出量の削減が可能である。
2022年3月には、ルフトハンザグループ傘下のスイス航空で機体への「AeroSHARK」の適用を公表している。ボーイング777型機の胴体とエンジン部分の表面に合計950m2のフィルムを貼ることで、約1.1%の燃料削減できるとしている。
スイス航空は2022年半ば以降、順次ボーイング777型機にフィルムを導入する。運航する全てのボーイング777型機で適用が進むと約4800トン/年の燃料削減と、最大1.52万トン/年のCO2排出量の削減が可能である。

全日本空輸(ANA)
2022年10月、ANAはB787型機の特別塗装機「ANAグリーンジェット」を公開した。胴体の一部に燃費改善効果があるニコンの「リブレットフィルム」を国内航空会社として初適用し、2機を使って耐久性を検証する。1機目は羽田―サンフランシスコの定期便、2機目は11月に国内線で運行する。
仮にANA全機の機体表面の約8割にリブレットフィルを装着すれば、約30万トン/年のCO2排出量の削減が見込めると試算している。
2024年8月、ボーイング777型機の貨物専用機(フレイター)と旅客機に、ルフトハンザ テクニックとBASFが共同開発した「AeroSHARK」フィルムを導入する。2024年9月の貨物定期便より、ボーイング777型フレイター(JA771F)が初めて就航し、来春から2号機目の旅客機(JA796A)を国際線にて運航する。
「AeroSHARK」フィルムは、1枚当たり幅約1m×高さ約0.5mで、50㎛程度の微細加工が施されており、機体胴体の大部分にこのフィルムを貼付することで、一機当たり年間約250トンの燃料消費量と約800トンのCO2排出量を削減することができる。2機の運航を通じて、その効果を検証した上で、同型機材への拡大を進める。
2025年4月、特殊フィルム「エアロシャーク」を装着した旅客機「B777」を国際線に就航させた。機体胴体の約7割にフィルムを張り付け飛行中の空気抵抗を減らす。燃料消費量とCO2排出量をそれぞれ1%減らす。
日本航空(JAL)
2023年2月、JALは、JAXA、ニコン、オーウエルと共同で、B737-800型機の2機で胴体外板の塗膜上にリブレット加工を施し、2022年7月から国内線で飛行試験(1機は750時間、もう1機は1500時間)を実施した結果、燃費改善効果と実用化に十分な耐久性を確認したと発表した。
1機にはニコンによる塗膜上に直接レーザーでリブレット加工、もう1機にはオーエンによるPaint-to-Paint Methodのリブレット加工を、胴体下部のサービスパネル(機体内部を点検・整備するために開閉できる蓋)上の2箇所(約7.5cm2)に施した。
ピッチに対して高さを半分にすると摩擦低減効果が高くなるため、リブレット加工は高さ50μm、ピッチ100μmとした。JAXAの試算では、リブレット加工を航空機全面に施工すると、約2%の燃費改善が見込める。
今後、737-800型機に対してより大面積のリブレット加工を施した実証機で飛行試験を継続し、その後、国内線の大型機、国際線機材へと順次展開していく計画としている。
しかし、航空機の機体表面80%以上への適用で1~2%程度の燃費削減が可能な技術では、費用対効果が課題となるであろう。より一層の低コストプロセスの開発が急務である。
2025年1月、機体表面に「サメ肌」状の塗装を施した1機を国際線で1月中旬から導入する。機体と空気の摩擦抵抗を従来より0.24%減らし燃費改善をめざす。羽田空港内で凸凹のリブレット形状を施したボーイング中型機「787」を公開し、ロサンゼルス便やフランクフルト便などの中長距離路線に充てる。
宇宙航空研究開発機構(JAXA)や塗料などを扱うオーウエルと共に、翼を含めた機体全体の約20%、機体胴体の約30%にリブレット形状の塗装を施した。約119トン/年の燃料改善、CO2排出量も約381トン減少する。
機体の塗装を除去し、新たにリブレット塗装を施すため、ルフトハンザ航空やANAなどのフィルム貼付法に比べて機体が重くならず、フィルムのはく離も生じない。塗装の耐用年数は8〜10年としている。