リチウムイオン電池の技術開発では世界に先行した日本であるが、市場は中国・韓国勢の後塵を拝している。この現状を打破するために蓄電池の産業戦略は重要である。以前に、半導体や太陽光パネルがたどった経緯と良く似ている。何故、日本は技術開発で先行しても、先行者利益が得られないのか?
国内蓄電池メーカーの投資意欲が高まるのは確実な国内市場の拡大が基本であり、蓄電池ユーザーの購買意欲が高まるのは高性能・低コスト化である。未だに、この機軸が見えてこない。
蓄電池と自動車メーカーの提携
現在、多くの自動車メーカーは電池技術の蓄積はなく、電気自動車(BEV)を商品化するにあたり蓄電池メーカーに大きく依存している。そのため蓄電池を安定的に大量調達するため、電池メーカーへの出資や、合弁会社を立ち上げるなどの様々な提携を進めている。
BEVに搭載される蓄電池容量は50~100kWhと、HEVの1kWh、PHEVの10kWhに比べて格段に多く、そのため蓄電池メーカーからの供給が必須となっている。図1には、2022年現在の蓄電池メーカーと自動車メーカーの提携関係を示す。
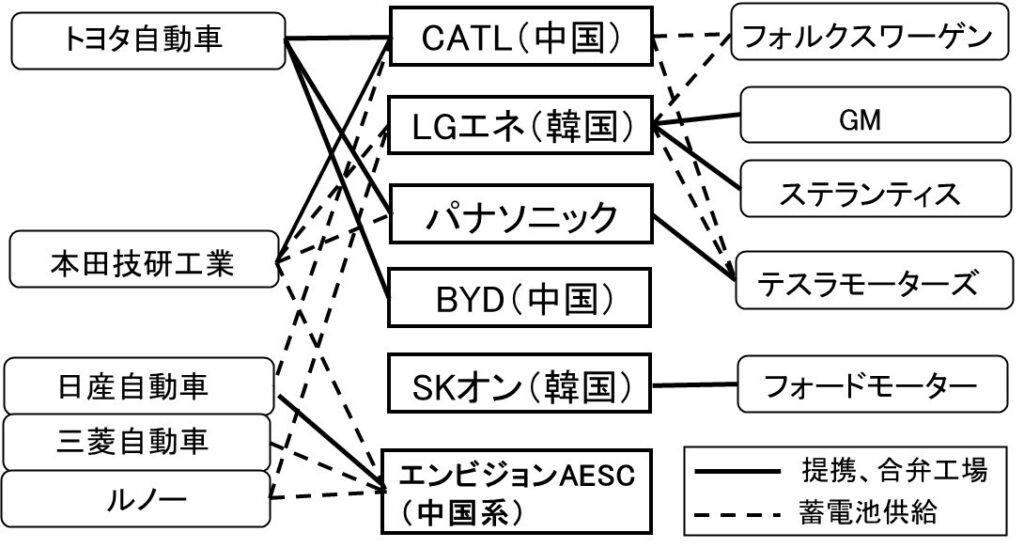
エネルギー専門市場調査機関の韓国SNEリサーチによれば、図2で示すように、2021年度における世界の車載用蓄電池のメーカーシェアは、中国の寧徳時代新能源科技(CATL)が32.6%と1位で、韓国のLG Energy Solution(20.2%)が2位、日本のパナソニック(12.2%)が3位である。
特徴的なのは、中国勢がシェア40%超で独走して、韓国勢が30%超と追随している点があげられる。日本勢はパナソニックが3位に入っているのみで、全体的に地盤沈下がみられる。
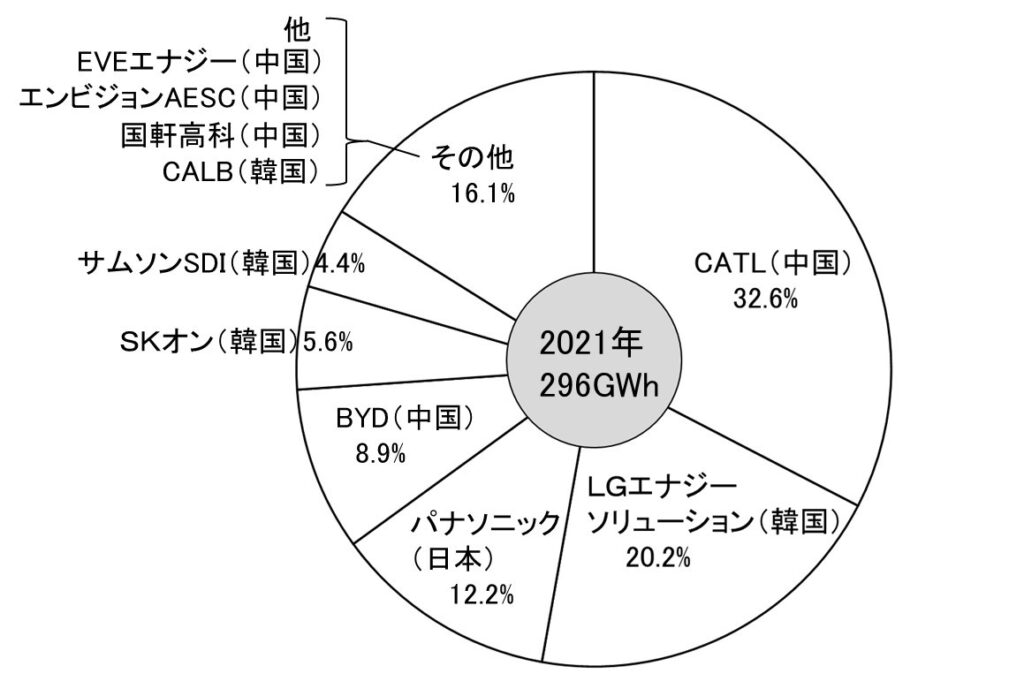
出典:韓国SNEリサーチ
以上の状況から、2022年4月、経済産業省は国内企業の蓄電池製造を支援するため、2030年に蓄電池生産能力:600GWh/年(国内:150GWh/年、海外:450GWh/年)の目標設定を公表した。2020年の約20倍の目標で、民間企業の投資を促すため補助金を拡充し、世界シェアを維持するのが狙いとした。
車載用蓄電池の製造ラインを国内に作る場合、生産能力150GWh/年について約2.5兆円の投資が必要とされる。当面はリチウムイオン電池(LIB)が主体であるが、2030年頃には安全性に優れる全固体電池の実用化を目指すことも戦略には書き込まれる。(日本の『蓄電池産業戦略』については後述。)
2023年8月、AESCグループは主要取引先の日産自動車以外に、2024年以降は本田技研工業、マツダ、メルセデス・ベンツGr、BMWなどに蓄電池を供給する。米英中など6カ国に新工場を設置、2026年までに生産能力を400GWh/年と20倍に高め、2027年までに全固体電池も量産できる体制を整える。
パナソニックHDは主要取引先のテスラ以外に、マツダ、SUBARUにEV向け電池を供給する検討を始めた。中国の寧徳時代新能源科技(CATL)も地場メーカー以外に、トヨタ自動車、フォルクスワーゲン(VW)、本田技研工業などに供給を広げ、電池メーカーが1社依存からの脱却を開始している。
米国自動車メーカーの動向
テスラモーターズとパナソニック
EV最大手の米国テスラモーターズは、2007年にパナソニックと技術提携し、2009年に蓄電池供給が始まる。2014年、ネバタ州で共同運営する電池工場「ギガファクトリー1」(生産能力:35GWh/年)の建設に合意し、2017年には米国内で量産車向けの蓄電池の共同生産を始めた。
2019年、テスラの中国工場が稼働した。蓄電池は中国のCATLや韓国のLG Energy Solutionが供給しており、パナソニックからの独占供給体制は崩れた。同年、テスラは米国マクスウェル・テクノロジーズを買収し、電極素材や製造工程を抜本的に見直して蓄電池の自社生産を始めている。
2021年、テスラはニューカレドニアのニッケル製造企業と提携し、オーストラリアのBHPとニッケル調達契約を締結、2022年1月、タロン・メタルズとミネソタ州の鉱山からのニッケル調達契約を締結した。2022年3月、ドイツ・ベルリン郊外の電池工場「ギガファクトリー」の生産を開始した。
一方、2021年6月、パナソニックが社名をパナソニックホールディングスに変更した翌日、テスラモーターズの全保有株式を約4000億円で売却し、蓄電池メーカーとして全方位経営を公表した。
2022年1月、パナソニックはEV15万台分のテスラ向け新型バッテリー「4680」(直径4.6×長さ8.0cm、容量:約5倍)を、2023年から和歌山工場で生産すると公表した。テスラ「モデルS」では、航続距離が650kmから750kmと延びる。
2022年7月、パナソニックは単独で2024年に米国カンザス州デソトに蓄電池の新工場を建設すると発表した。投資額は40億ドルで最大約4000人を雇用する大型工場で、テスラに新型蓄電池「4680」を供給する。「ギガファクトリー1」に続き米国で2カ所目の工場である。
2022年12月、パナソニックエナジーが国内生産する円筒型LIB「2170」(直径2.1×長さ7cm)を、新興EVメーカーの米国ルシード・グループへ供給すると発表。2024年にはカンザス州の新工場から供給する計画である。ルシードは2023~2031年にかけて合計約50億ドルの電池を調達するとしている。
2028年度までに、生産能力を現在の50GWh/年から3~4倍に増やす計画を表明している。
2023年1月、テスラは米西部ネバダ州の巨大電池工場に36億ドルの追加投資を発表した。大型で容量が約5倍の新型電池「4680」の生産能力100GWh/年を追加する。(現在、約40GWh/年)
また、同社初の商用車である電動トラック「セミ」の量産工場も新設する。2017年に試作車を公表し、これまでネバダ州内で試験的に生産し、2022年末に米飲料大手ペプシコへの納車を始めていた。
2023年5月、パナソニックHDは、電池生産能力を2030年度までに200GWhに引き上げると発表。2024年度に稼働するカンザス州の電池工場では、EV向け円筒型電池「2170」の生産拡大。和歌山県では新型電池「4680」の安定生産を進める。2030年までに北米新拠点での展開を予定。
2024年8月、EV向け電池の生産目標を引き下げた。2030年度に北米と日本で計200GWhとする従来計画を見直し、約3割減の150GWh程度になる見通しを示した。テスラなどへの供給が減っており、北米で3カ所目の電池工場の建設計画も年内は見送る。
電池事業会社パナソニックエナジー北米法人は、テスラに電池供給するネバダ州の工場のほか、カンザス州でも電池工場を建設している。
2025年1月、パナソニックエナジーは、米国EV新興ルーシッド・グループの新車種にEV用蓄電池が搭載された。2023年から別のEV向けに供給しているが、新型多目的スポーツ車(SUV)2車種に採用され、住之江工場で製造した円筒型電池「2170」(直径:21mm×長さ:70mm)を2024年8月から供給を始めた。
2025年3月末までに稼働予定の米国カンザス工場でも「2170」を製造する計画で、2026年には両工場から出荷を始める。
ジェネラル・モータース(GM)とLG Energy Solution
2021年4月、GMは韓国LG Energy Solutionと合弁会社Ultium Cells(アルティウムセルズ)を設立し、2022年にオハイオ州第1蓄電池工場(生産能力:35GWh/年以上)、2023年にテネシー州第2蓄電池工場(35GWh/年以上)の操業開始、2022年1月、ミシガン州第3蓄電池工場の建設を発表した。
2021年6月、2025年までにBEVと自動運転技術に350億ドルを投資し、世界で30車種以上のBEV発売計画を公表した。LG Energy Solutionと共同開発したリチウムイオン電池、モーターなどの動力装置で構成されるEVプラットホーム「アルティウム(Ultium)」を幅広い車種に共通使用する。
アルティウムは、大型EV「ハマーEV」から導入を始めており、2023年には大型ピックアップトラック「シルバラードEV」(蓄電池容量:200kWh)にも導入される。また、GMは自動運転機能「ウルトラ・クルーズ」を米半導体大手のクアルコムと共同開発を進めている。
2022年11月、LG化学は30億ドルを投じて米国テネシー州に電池材料工場を建設する。子会社のLG Energy Solutionが北米6カ所で電池工場を稼働しており、NCMA系正極材料の需要増に対応する。2025年中の生産開始、2027年までにEV120万台分に相当する12万トン/年に生産量を増やす。
2023年3月、LG Energy Solutionは、米国アリゾナ州での工場建設計画を発表した。米政府のインフレ抑制法でEV関連の補助金を受け、車載用円筒型電池(EV35万台分、27GWh)とエネルギー貯蔵装置(ESS、16GWh)向けパウチ型電池の2工場棟を建設する。2023年着工、2025年中の稼働を目指す。
LG Energy Solutionは、現在稼働中のミシガン州の自社工場に加えて、米国GMとの合弁で3工場、ホンダとオハイオ州に1工場、欧州ステランティスとカナダのオンタリオ州に1工場を稼働し、新たに自前の電池工場を建設して米国テスラなどへの供給能力を確保する計画である。
2024年12月、米国ミシガン州で韓国LGエネルギーソリューションと運営する予定の電池合弁工場の持ち分を同社に売却すると発表。EVの低価格化と市場変調を受け、電池の調達戦略を見直す。取引は2025年1〜3月に完了し、GMは約10億ドル(約1500億円)の投資を回収する。LGエネと開発する電池事業は継続する。
オハイオ州とテネシー州の2つの電池工場は引き続き活用してEV需要に対応する。
フォード・モーターとSKオン/LG Energy Solution
2022年12月、フォードは韓国のSKオンと合弁会社BlueOval SKを設立しケンタッキー州で蓄電池工場の起工式を行った。2025年から「Ford」および「Lincoln」ブランドのEV向け蓄電池を生産し、2026年末までに世界で年間200万台のEVを生産する計画である。
一方、2022年の電動ピックアップトラック「F-150ライトニング」の北米向け15万台/年、「マスタング」を北米、欧州、中国向けに27万台/年など、2023年末までに生産を予定するEVの60万台/年(蓄電池容量:60GWh)は寧徳時代新能源科技(CATL)や韓国・SKグループなどから調達する。
2023年1月、韓国電池大手SKオンがトルコで米国フォード・モーターと進めてきた車載電池の合弁生産計画が白紙撤回される見通しとなった。フォードは提携先をLG Energy Solutionに切り替える方針である。
現代自動車グループとSKオン/LG Energy Solution/サムスンSDI
2023年4月、現代自動車グループは韓国SK On(SKオン)と合弁で電池セル生産会社を米国に設立する計画を発表した。ジョージア州バートウ郡に35GWh/年の電池セル工場を建設し、2025年後半に電池セルの生産を開始する。両社は50%ずつ出資し、総投資額は50億ドルとなる。
新工場で生産した電池セルは、現代Mobis(現代モビス)が電池パックに組み立て、Hyundai、Kia、Genesis各ブランドの米国生産拠点に供給する。2022年8月に米国で成立した「Inflation Reduction Act(IRA、インフレ抑制法)」対応で、車両最終組立と電池生産を現地化する動きの一環である。
2023年5月、現代自動車グループとLG Energy Solutionは、米国ジョージア州ブライアン郡に電池セルの合弁会社を設立する。電池工場「メタプラントアメリカ」近郊で、生産した電池セルはHyundai Mobisが電池パック化し、米国内で製造するHyundai、Kia、GenesisブランドのEVに搭載する。
投資額は5兆7000億ウォン(約6042億円)で、両社とも50%ずつの株式を保有する。生産能力は30GWh/年で、2023年後半に工場の建設を始め、早ければ2025年末から生産を開始する予定。
LGエナジーは、本田技研工業や米国GMなどとも電池セルを供給する契約を結んでおり、2023年時点で米国内に7つの電池セル工場が稼働中もしくは建設中である。
2023年10月、サムスンSDIはハンガリー工場から現代自動車のチェコ完成車工場に、開発中の角形バッテリーを2026年から7年間でBEV50万台分を供給すると発表。ニッケル比率を高めた正極材と、独自素材の負極材でエネルギー密度を高めてBEVの航続距離を伸ばせる。
サムスンSDIは米国で、欧州ステランティスや米国GMと車載電池の合弁工場を建設している。欧州メーカーの中では特に独BMWとの関係を深めているが、新規顧客の獲得を急いでいる。
欧州自動車メーカーの動向
フォルクスワーゲン(VW)
ドイツのVWは、2026年までに6.7兆円をEV関連に投資し、2030年までに欧州に6カ所の蓄電池工場を設置することを表明している。
2022年3月、スウェーデンのNorthvolt(ノースボルト)に14億ユーロ超を出資し、折半出資で3カ所目となる蓄電池工場をドイツ北部シュレスウィヒ・ホルシュタイン州ハイデに建設する。2025年後半に生産を始め、生産能力:60GWh/年とし、約100万台のEVに供給できる。
その他、本社近くの独ザルツギッター、スペイン・バレンシアも含め、欧州3カ所で「ギガファクトリー」と呼ばれる巨大車載電池工場の建設を明らかにし、デンマークや北海の風力発電を使い製造過程でCO2排出量が少ない電池生産を目指し、レアメタルを再利用するリサイクル工場も敷地内に設置する。
その他、中国の国軒高科にも11億ユーロ出資して欧州に電池工場を建設するほか、LG化学や中国のCATLなど電池メーカーと幅広く提携し、2029年までに約75車種のBEVを投入する方針。
また、2024にも全固体電池の量産を計画する米国スタートアップのクアンタムスケープにも出資しており、自動運転機能に関しては米国インテルと提携を行っている。
2022年11月、VWはSUVタイプの新型BEV「ID.4」を国内で発売。「Lite Launch Edition」と「Pro Launch Edition」の2モデルで、Liteは蓄電池容量:52kWh、最高出力:125kWの電動機を搭載し、航続距離:388kmで価格:499.9万円(税込)。Proは77kWh、150kW、561km、636.5万円。
ID.4導入に合わせ、2022年度中に全国158の販売拠点に急速充電器の設置を進める。
2023年3月、米国インフレ抑制法(IRA)補助金を活用し、サウスカロライナ州にEVの多目的スポーツ車(SUV)「スカウト」の製造工場を新設すると発表した。2020年代後半にもメキシコのエンジン車工場で新たにEV製造を検討する。2030年までに25車種以上のEVを米国で発売する予定である。
2023年3月、カナダ東部オンタリオ州でEV向け車載電池工場を新設すると発表した。IRA補助金を活用し、90億〜100億ドルの支援を受け、2027年に工場を稼働する。
ダイムラー(メルセデス・ベンツ)と輝能科技
ドイツ・ダイムラーの高級車部門であるメルセデス・ベンツ(Mercedes-Benz)は、2025年以降に発表する次世代車をすべてBEV専用とし、2030年から販売する全モデルをBEV100%にすることを表明している。
2021年、メルセデス・ベンツは全固体電池の開発で、米国スタートアップのファクトリアルエナジーに出資を発表した。
また、2022年1月には、2006年設立の全固体電池ベンチャーである台湾の輝能科技(ProLogium Technology、プロロジウムテクノロジー)と、メルセデス・ベンツは次世代全固体電池の共同開発のため提携・出資を発表しており、2025年に全固体電池搭載のBEV販売を目指している。
輝能科技は世界で初めてセラミック型全固体電池を量産し、既に約8000個のサンプルを自動車各社に提供している。2022年内には、台北近郊に量産工場を設置する計画である。
ボルボ・カーとノースボルト
スウェーデンの新興電池メーカーであるNorthvolt(ノースボルト)は、2021年末にスウェーデン北部シェレフテオに初の蓄電池工場を稼働させ、2022年2月にはスウェーデン南部ヨーテボリに、スウェーデンのVolvo Cars(ボルボ・カー)と共同出資で2番目となる蓄電池工場の建設を公表した。
新工場は2023年に建設を始め、2025年に稼働する予定で、生産能力:最大60GWh/年、EV約60万台/年に供給する。生産した蓄電池はボルボの次世代高級EVである「Polestar(ポールスター)」に搭載される。2030年までに欧州に少なくともあと2カ所の工場を建設する。
ノースボルトは米国テスラの元幹部が創業し、ドイツのVW、BMW、米国ゴールドマン・サックスが出資している。さらに、スウェーデンやカナダの年金ファンドなどが新規参加しており、VWは6億2千万ドルを出資し約20%の出資比率を保持している。
2024年11月、EV向け蓄電池の量産を進めるスウェーデンのNorthvolt(ノースボルト)は米連邦破産法第11条(チャプター11)を申請した。同社は米国に子会社や資産を持っているため、チャプター11の申請要件を満たした。16GWh/年を想定して2021年末に稼働したスェーデン工場が、現状は1GWh/年前後にとどまる。
ステランティスとCATL
中国・寧徳時代新能源科技(CATL)が大口顧客向けに大胆な値引きを実施しており、事業再建を目指すが、欧州域内に電池産業を育てる構想は頓挫しかけている。
2024年12月、欧州Stellantis(ステランティス)はCATLと共同でスペインにEV向け電池工場を新設する。41億ユーロ(約6600億円)を投じ、最大で50GWh/年の生産工場を稼働させる。
2025年4月、中国の車載電池最大手の寧徳時代新能源科技(CATL)は、5分間の充電で520kmを走行できる新たなEV用電池を開発したと発表した。リン酸鉄リチウムイオン(LFP)電池で、満充電時の航続距離は800kmである。負極材料を改良したほか、電池内のイオンの流れを効率化した。
2025年12月にはエネルギー容量を175Wh/kgまで高めた新型ナトリウムイオン電池の量産開始も発表した。航続距離は、EVへの搭載で500km以上、PHVではEVモードで200km以上としている。
中国自動車メーカーの動向
広州汽車集団
2022年8月、広東省広州市にEV用車載電池(リン酸鉄リチウムイオン電池(LFP))工場(生産能力:26.8GWh)の新設を発表した。109億元を投資して2025年完成を目指す。生産した蓄電池は、自社EV用と外部供給も狙う。傘下の広州巨湾技研も広州市で急速充電対応の蓄電池工場を運営している。
電池が祖業の比亜迪(BYD)を除き、中国自動車メーカーの多くは寧徳時代新能源科技(CATL)などから電池を調達していたが、電池コストが車全体の40~60%を占めるため自前生産を始めている。
BYD
2025年2月、2027年頃から「全固体電池」を試験的に車両に搭載する。BYD子会社の深圳市比亜迪鋰電池が開発しており、量産での搭載となるのは2030年以降となる。今後、エネルギー密度を400Wh/Kg以上に高めるのが目標という。量産による全固体電池の価格は三元系リチウムイオン電池と理論上は同価格になる。
トヨタ自動車は2027年度にも全固体電池の量産を始める計画だ。ホンダは2020年代後半、日産自動車は2028年度の量産を目指すほか、韓国勢も開発を手がけている。
日本自動車メーカーの動向
日本メーカーは、BEVの基幹部品である蓄電池を安価な海外から調達してきた。世界的なEVシフトでこの蓄電池の調達がボトルネックとなり、海外メーカーでは自前生産の取り組みを急速に進めている。国内メーカーも自前生産の方針を探っているが、蓄電池工場の規模や稼働時期に遅れが見られる。
2024年5月、自動車・蓄電池トレーサビリティ推進センターは、車載電池のCO2排出量のデータなどを会員企業間で共有できるサービスを開始した。会員募集も始めており、既にトヨタ自動車や日産自動車など自動車大手14社が参画した。欧州では蓄電池のCO2排出量の開示が必要で、データ共有で規制対応を進める。
電池・部品メーカーなどが生産~廃棄までに出すCO2(カーボンフットプリント)を、それぞれデータの共有システムに入力し、合算して車載電池全体のCO2排出量を把握できるようにする。ブロックチェーン(分散型台帳)技術を使い、競合他社から自社データを閲覧できないよう担保する。
政府が進める「ウラノス・エコシステム」と呼ぶ独自の産業データ基盤開発の初の事例となる。将来的に欧州の別のデータ基盤と連携することも目指す。
日産自動車・ルノー・三菱自動車
2022年1月、日産自動車・フランスのルノー・三菱自動車は、2030年までのロードマップ「アライアンス2030」を発表した。世界の主要拠点で電池工場を拡充し、2030年度までに車載用蓄電池の生産能力を現在の20倍である220GWh/年、EV240万台分に引き上げると発表した。
すなわち、2026年度までにBEVなど電動車の開発に3社合わせて230億ユーロを投じ、2030年度までに35車種のBEVを投入し、9割の車種を共通の5つの車台で生産する。さらに、EV原価の30%を占める蓄電池コストを、2026年に現在比で50%、2028年には65%削減するとした。
また、航続距離が大幅に伸びる全固体電池を搭載したBEVに関しては、日産自動車は2024年から試験生産を開始し、2028年度までに発売する。日産自動車が開発した全固体電池は3社のBEVに搭載し、量産効果でBEV価格をガソリン車並みに引き下げる計画である。
現在、日産自動車の蓄電池生産能力は7.5GWh/年で、出資する中国系のエンビジョンAESCグループなどと組み、日本・英国・中国で工場を新増設し、2030年に130GWh/年まで増やす計画である。
2022年2月、日産自動車は日欧中向けガソリンエンジンの新規開発を中止する方針を固めた。2025年にも欧州で新しい排ガス規制が始まるため、欧州向けの新型エンジン開発を中止し、中国や日本向けも段階的に中止して、BEVやHEV向けの駆動装置の開発にシフトする。
ただし、ガソリン車自体は当面残るため、日欧中向けは新型ではなく、既存エンジンの改良で対応する。米国向けは、ピックアップトラックを中心としたガソリン車に一定の需要が見込めることから、新規開発を継続するとしている。
2022年2月、日産自動車は、米国南部ミシシッピー州キャントン工場の一部をBEVとHEV用に改修すると発表した。2025年までに5億ドルを投じて組立ロボットなど最新設備を導入し、高級車「インフィニティ」など、普及車2車種のBEV生産ラインを稼働させる。蓄電池は電池メーカーから調達する。
2022年4月、日産自動車も出資するエンビジョンAESCグループは、米国テネシー州に次いで2か所目のケンタッキー州でも電池工場の建設を公表した。投資額は20億ドルで、2025年の量産開始(生産能力:30GWh/年)を目指す。高エネルギー密度の次世代LIBをメルセデス・ベンツなどへ供給する。
中国系エンビジョンAESCグループは日米英中で車載用蓄電池工場を持ち、フランスや英国などでも新工場を建てる計画であり、世界での生産能力を、2026年時点で現状比20倍である300GWh/年をめざす。
2022年9月、日産自動車はBEV蓄電池の安定供給を目指し、車載用蓄電池メーカーのビークルエナジージャパンを官民ファンドの(株)INCJから買収して子会社とすることを発表した。
2023年5月、中国系エンビジョンAESCが、生産能力を2026年に現在の約20倍の400GWh/年まで高めることを公表した。世界6か国に電池工場を新設予定で、米国の新設2工場では、メルセデス・ベンツやBMWへの供給が決まった。中国・英国・フランス・スペインでも新工場をつくる。
国内では、500億円を投じて茨城県内に新工場を建設中で、2024年春の量産開始を見込み、日産のほか、ホンダやマツダへの供給を予定する。従来に比べて航続距離を伸ばせる新型電池を生産する。
2024年1月、日産自動車は割安なリン酸鉄リチウムイオン電池(LFP)を自前生産すると発表。2026年以降に新興国向けEVへの搭載を目指す。航続距離は落ちるが、電池コストを2〜3割減らせるため、EVの低価格化につながる。
国際エネルギー機関(IEA)によると、2022年の新車EVに搭載された電池の27%がLFPで、2019年(3%)から大幅に上昇した。EV向けLFPの生産量の95%は中国で生産する車に搭載されている。
2025年1月、福岡県内に計画するEV向けの電池工場が北九州市内に建設される。リン酸鉄リチウムイオン(LFP)電池の生産を始め、2028年度中にも軽EVへの搭載をめざす。新工場の生産能力は年5GWh/年を予定しており、投資額は1533億円を見込んでいる。2025年5月、経営難から本電池工場の建設は中止された。
2025年1月、米国市場で販売するEVの車載電池を韓国電池大手SKオンから調達。電池容量:20GWhの調達で、2028年をメドにEVへの搭載を始める。同3月には、2028〜33年の6年間で計99.4GWh分で、中型のEV100万台分に相当する。SKの米ジョージア州工場から米ミシシッピ州の完成車工場に電池を供給する。
パウチ型でニッケル成分の多く走行距離の長さが特徴で、北米で販売するSUVとセダンのEV4車種に搭載する。2026年度までに世界で30種類の新型車の開発を公表し、うち16車種は電動車と説明している。
本田技研工業
2020年9月、北米で米国GMとBEV事業で包括提携し、他社との連携を軸にBEVシフトを加速している。蓄電池の日米中3市場での調達計画を発表しており、日本市場はエンビジョンAESC(中国)、北米市場はLG Energy Solution(韓国)、中国市場はCATL(中国)としている。
2022年12月、韓国LGエネルギーソリューションとの合弁会社を米国オハイオ州に設立したと発表した。資本金は2.1億ドルで段階的に増やして最終的に35億ドルとし、2025年の量産開始(生産能力:約40GWh/年)を目指す。生産された蓄電池全量がEVシフトの急速に進む北米のホンダ車向けである。
一方、次世代蓄電池の全固体電池は、2020年代後半の実用化を目指して自社開発を進めている。
2024年4月、カナダのオンタリオ州の完成車工場に隣接し、EV新工場と蓄電池工場の新設を発表。総投資額は150億カナダドル(約1兆7千億円)で、カナダ政府などの資金支援を受けて2028年にも稼働、24万台/年、36GWh/年の生産規模。米国オハイオ州でも2025年後半からEV生産を計画し、北米で2か所目となる。
北米で一貫した調達網を構築する狙いで、韓国ポスコと正極材、旭化成とセパレーターの合弁会社をカナダで立ち上げる。カナダ政府は、2035年までにガソリン車など、エンジン車の販売を禁止する方針で、米国政府も北米で車両や電池が生産されたEVに対し、最大7500ドル(約100万円)の税制優遇を行っている。
2025年6月、ジーエス・ユアサコーポレーション(GSユアサ)が本田技研工業・ブルーエナジーと計画する滋賀県守山市のEV向けリチウムイオン電池工場の着工を延期する。笠松町の建設地の埋蔵文化財調査に時間を要しているほか、EV市況の低迷も考慮した。2028年頃の完成を最大3年間遅らせる。
横江町の工場は建設中で、予定通り2027年4月に稼働させる。GSユアサはEV電池の生産能力を2035年までに20GWh/年超に引き上げる計画で、この目標に現時点での変更はない。
トヨタ自動車
2021年12月、2030年のEV世界販売目標を350万台に引き上げる方針を掲げ、2030年までに生産設備のみで2兆円を投資し、蓄電池の生産能力:280GWh/年を確保する。比亜迪(BYD)や寧徳時代新能源科技(CATL)とも協業するが、蓄電池の生産能力増強は国内外の自社グループを中心に進める。
既に、2020年4月にはパナソニックと合弁会社プライム プラネット エナジー&ソリューションズ(PPES)を設立し、HEV用角形リチウムイオン電池の生産を徳島県で開始した。また、電池調達で中国CATL やBYDと提携するが、自社向け生産ラインの設備投資はトヨタ自動車が行う方針である。
2021年12月、12.9億ドルを投資して豊田通商と米国ノースカロライナ州に蓄電池工場を設立すると発表した。豊田通商はアルゼンチンでリチウムの権益を取得しており、プラント増強工事を進めている。生産能力はHEV向け蓄電池で年間80万台分とした。
2022年8月、米国ノースカロライナ州の蓄電池生産拠点であるToyota Battery Manufacturing North Carolina(TBMNC)に25億ドルの追加投資を発表した。この投資によりEV用蓄電池の生産能力を増強し、2025年の稼働を目指す。
また、国内でも自社工場と合弁会社PPESの姫路工場に4000億円を投資し、リチウムイオン電池生産ラインの2024年の稼働を目指す。トヨタ自動車の蓄電池生産能力は、2021年5月で6GWh/年であったが、一連の日米投資により最大40GWh/年に増強される。
また、2020年代前半に全固体電池を搭載したHEVを発売し、2022年にも国内で全固体電池を搭載したBEVを発売する計画を示している。自動運転は、ソフトバンクグループと提携している。
2023年6月、BEVの性能向上に向けて「全固体電池」を2027~28年に実用化する方針を明らかにした。搭載されるのは、5月に新設した専任組織「BEVファクトリー」が手がける次世代BEVで、10分以下でフル充電でき、航続距離:1200km程度を目指している。
また、豊田自動織機と協力してバイポーラ型リン酸鉄リチウムイオン(LFP)電池の開発・量産を進めることを明らかにした。現行のBEV「bZ4X」に搭載するLIBに比べ、航続距離を2割延ばせ、コストは4割安くなる。比較的廉価なBEVへの搭載を見込み、2026〜27年の実用化を目指す。
2023年10月、韓国のLGエネルギーソリューション(LGES)とEV用リチウムイオン電池の供給契約を締結。LGESが約30億ドルを投じ、米国ミシガン州の同社工場にトヨタ専用の電池生産ライン(20GW/年)を新設する。2025年に稼働を始める。
2023年10月、出光興産と硫化物系の全固体電池の量産に向けた協業で開発スピードを速める発表。開発を進めているのは、充電時間が10分以下、航続距離約1200kmで、現行のEV「bZ4X」向けリチウムイオン電池の充電時間約30分、航続距離約600kmを大きく上回る。
2023年10月、米国ノースカロライナ州で建設中の電池工場に約80億ドルを追加投資を発表した。同工場の累計投資額は約139億ドルで、新たに8ラインを立ち上げ2030年までに計10ラインとする。生産能力は30GWh/年以上で、3列シートを備えた多目的スポーツ車(SUV)のEVなどに搭載する。
新工場の法人には豊田通商も10%を出資し、2025年に稼働する予定で、EV換算では40万台程度を確保できる。EVの世界販売台数を2026年に150万台、2030年に350万台まで引き上げる計画を掲げており、2022年の販売実績は2万4000台で、今後4年で60倍以上に増やす。
2023年11月、米国ノースカロライナ州で建設中の車載電池工場で、リサイクル材料を使用すると発表した。電池部材スタートアップのレッドウッド・マテリアルズとの提携を拡大し、電池の正極材や負極材に使われる金属を調達する。電池資源の海外依存が課題となる中、北米で資源を循環させる体制を整える。
レッドウッドは使用済み電池からリチウム、コバルト、ニッケルなどのレアメタルを取り出し、正極・負極材に再利用する事業を手掛けている。フォード・モーターやパナソニックエナジーなどとも提携している。2022年6月にレッドウッドとの提携を発表していた。
2024年7月、福岡県にEV向けのリチウムイオン電池工場の新設を公表。2025年頃に着工し、2028年以降に稼働する。新工場はトヨタ自動車九州苅田工場に近い新松山臨海工業団地に設置し、電池子会社のプライムアースEVエナジーが運営する。投資額は数千億円規模で、経済産業省も建設資金を助成する。
トヨタ自動車九州はレクサスのSUVやセダンなどの生産を行い約9割を輸出している。2035年までにレクサス車の新車販売の全てをEV化する方針で、新型車投入に合わせて新工場で生産を始める計画であったが、2025年3月、EV市場減速の影響を受けての開発見直しで、搭載電池の製造開始も遅らせると発表。
2025年2月、 米国で韓国のLGエネルギーソリューション(LGES)から車載用電池を調達すると公表。2024年12月にGMが出資引き揚げを決めたミシガン州に建設中のLGESの工場から調達する。既に、ノースカロライナ州で北米初となるEVやHV向けの電池工場を建設しており、LGESからの調達分が新たに加算される。
マツダ
2022年11月、2030年までにBEVなどの電動化対応に車載電池の調達費を含めて1.5兆円規模を投じると発表した。今後、ガソリン車やディーゼル車への新規投資を大幅縮小し、2020年代後半にBEVの投入を本格化、これまで2030年に25%としていた世界生産に占めるEV比率を30~40%程度まで高める。
2023年6月、パナソニックエナジーとマツダは、EV向け電池の供給について協議を始めた。マツダは2020年代後半に発売するEVにパナHDの電池を搭載する方針で、実現すればパナHDが国内車大手に直接供給する初のケースになる。
パナHDが2024年にもEV向けに供給を始めるLIBの新製品「4680」をマツダが採用する可能性がある。「4680」は現行の「2170」と比べ容量が約5倍で、EVの航続距離の延長に寄与する。 パナHDは約50GWhの電池の生産能力を2030年度に約4倍の200GWhにする計画を掲げる。
2024年8月、パナソニックHDが、SUBARU、マツダと連携し、国内にEV用電池の生産拠点を整備する最終調整に入った。スバルとマツダは、2020年代後半に本格的にEV量産に乗り出す方針である。討している。
スバル向けは同社の生産拠点が集積する群馬県内に、セル製造~パッケージ化までの生産ラインを新設する。マツダ向けには同社工場がある広島県や山口県にパッケージ化のラインを整備し、セルは大阪市にあるパナソニックグループの電池工場から運ぶ。
トヨタ系のプライムプラネットエナジー&ソリューションズ(PPES)に加えて、エンビジョンAESCから新たに蓄電池を調達し、広島の本社工場でBEVの増産を進める。駆動装置に使うインバーター部品向けの半導体などでロームと協業し、BEV専用の車台や駆動装置「イーアクスル」の開発を強化する。
スズキ自動車
2022年3月、インドのグラチャート州でBEV向け蓄電池工場などに総額1500億円を投資を公表した。BEV生産能力の増強にはSuzuki Motor Gujarat Private Limited(SMG)に約487億円を投じ、2025年の稼働、SMGに近接して蓄電池工場を建設するのに約114億円を投じ、2026年の稼働を目指す。
また、Maruti Suzuki Toyotsu India Private Limited(MSTI)が、BEVのリサイクル工場を建設するのに約707億円を投資する。このリサイクル工場は2025年の稼働を目指す。
2023年1月、インドの自動車展示会で、BEV試作車「eVX」を2025年までにインドと欧州で発売すると発表した。SUV車で全長4.3m、幅1.8m、全高1.6m、航続距離は550kmである。
リチウムイオン電池の現状
リチウムイオン電池材料
現行のリチウムイオン電池(LIB)の基本構成は、コバルト酸リチウム(LiCoO2)などの正極材料と炭素(黒鉛)などの負極材料の間に、ポリオレフィンの微多孔フィルムなど絶縁性に優れたセパレーターを挟み、六フッ化リン酸リチウム(LiPF6)などの電解液で満たされたものである。

このLIBを構成する正極材料、負極材料、セパレーター、電解液の主要4部材について、2010年代前半まで世界シェアの上位を日本企業が占めていた。しかし、図2で示すように、2020年には中国勢の追い上げがコスト面、品質面でも顕著となっている。
2020~2021年には、韓国LG化学製LIBの発火による米国GMのBEV大規模リコール事件が発生したこともあり、品質面で優位な日本製の電池材料への需要も再び高まっているが、原料の調達や生産性向上などによる価格競争力の強化は不可欠である。
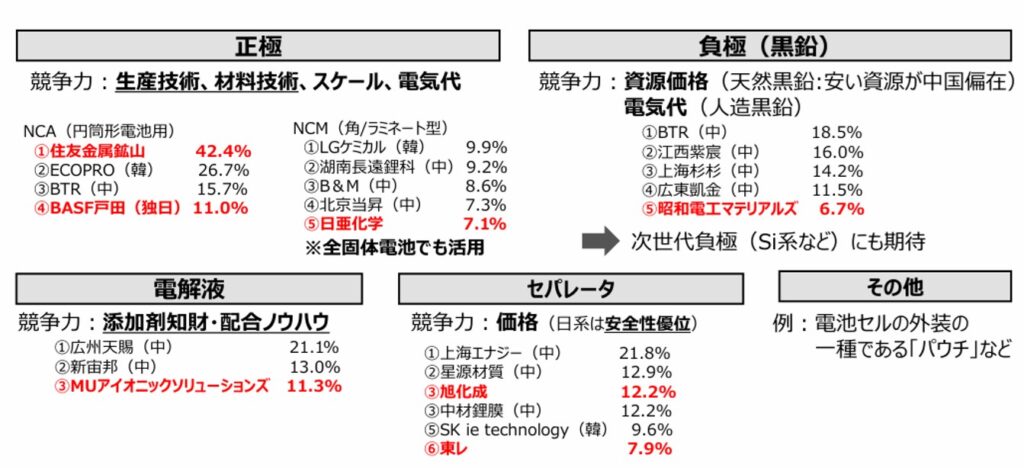
原料調達の優位性から、中国勢が主要4材料でシェアを伸ばしているが、その背景には車載用蓄電池メーカーの上位を中国企業が占めたことが大きな要因である。加えて、中国政府主導による巨大なBEV市場を背景に、自動車メーカーがBEV増産に傾注していることが影響している。
一方、2021年6月、スウェーデンの電池スタートアップNorthvolt(ノースボルト)は、27.5億ドルの増資によりスウェーデン北部シェレフテオ工場の生産能力を5割引き上げ60GWh/年にすると発表。
ノースボルトは、VWとの合弁でドイツに大型電池工場の建設を進めている。今回の拡張で合計生産能力は100GWh/年となるが、2030年までに欧州に少なくともあと2工場を建設し、欧州だけで生産能力150GWh/年とする計画で、アジア依存の蓄電池リスクの分散が期待されている。
2023年5月、中国系エンビジョンAESCが、生産能力を2026年に現在の約20倍の400GWh/年まで高めることを公表した。世界6か国に電池工場を新設予定で、米国の新設2工場では、メルセデス・ベンツやBMWへの供給が決まった。中国・英国・フランス・スペインでも新工場をつくる。
国内では、500億円を投じて茨城県内に新工場を建設中で、2024年春の量産開始を見込み、日産のほか、ホンダやマツダへの供給を予定する。従来に比べて航続距離を伸ばせる新型電池を生産する。
正極材料
車載用LIBの原材料の中で、正極材料は最も高価である。ベースとなるリチウムは①オーストラリア、②チリ、③中国、④アルゼンチンの4カ国に集中し、国際情勢や各国の政治動向などで供給が不安定化するリスクを抱える。米国アルベマール、チリ・SQM社、中国の天斉リチウム業などが生産している。
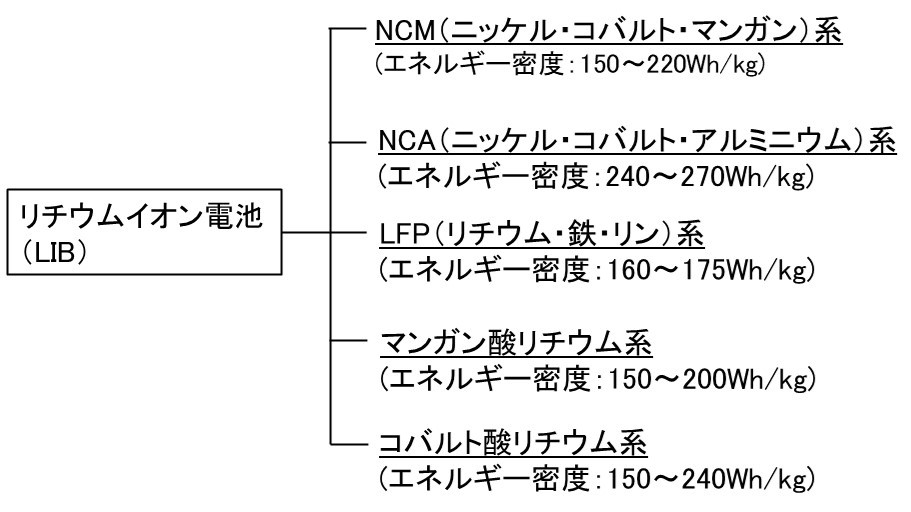
米国テスラ・モーターズは、パナソニックが製造するNCA(ニッケル・コバルト・アルミニウム)系正極材料の円筒型蓄電池をBEVに搭載。NCA系正極材料では住友金属鉱山が世界シェア首位の49%で、2位は韓国のEcoProBM(エコプロBM)、3位はBASF戸田バッテリーマテリアルズ合同会社である。
他の多くの自動車メーカーでは、NCM(ニッケル・コバルト・マンガン)系正極材料の角型/ラミネート型蓄電池をBEVに搭載している。このNCM系正極材料では日産化学が世界シェア首位の11%で、2位はベルギーのUmicore S.A.(ユミコア)、3位は韓国のLGケミカルである。
ニッケルの主要な生産国の順位は、①インドネシア、②フィリピン、③ロシア、④ニューカレドニア、⑤カナダである。また、コバルトの主要な生産国の順位は、①コンゴ、②オーストラリア、③ロシア、④キューバ、⑤カナダである。これらの高価な原材料を、日本は100%輸入に頼らざるを得ない。
中でも、コバルトは世界的なEV化の流れで需要は伸びているが、銅やニッケルの副産物のため急な増産が難しく、紛争リスクなどの懸念のあるコンゴが産出量の7割を占めており、調達先の多様化が不可欠と考えられている。国内非鉄大手では住友金属鉱山がコバルト生産を手掛けている。
2022年7月、車載電池最大手の中国・寧徳時代新能源科技(CATL)はリン酸鉄系(LFP)リチウムイオン電池を2023年に発売した。パック容量を増やすため、モジュールを省きセルを直接パックに詰め込む「セル・ツー・パック」を開発し、電池冷却部材を構造材と一体化して省スペースを実現した。
この高価なニッケルやコバルトを使わないリン酸鉄リチウム(LFP:LiFePO4)系正極材料を用いたリチウムイオン電池は、エネルギー密度は低いが安価なため自動車メーカーの注目を集めている。
米国テスラはCATLから供給を受け、上海で製造する「model 3」に搭載する。また、上汽通用五菱汽車が生産する超低価格の「宏光MINI EV」にも採用されており、ドイツVWも採用を決定している。LFP系正極材料のリチウムイオン電池は中国メーカーがほぼ独占している。
2023年8月、中国CATLは超急速充電が可能なLFP電池「神行(Shenxing)」を発表。常温では10分で電池残量(SoC)80%まで充電でき、10分で400km走行可能。-10℃の低温下でも30分で0%から80%まで充電可能で、2023年末までに量産を始め、2024年第1四半期に搭載EVが販売される。
一方、2023年4月、住友金属鉱山は2028年にもリチウム生産(2〜3万トン/年)を始めると発表。同社はニッケルやコバルトの海外生産は手掛けるが、リチウムは海外企業による生産に依存していた。
アルゼンチンやチリなどの塩湖からリチウムを高効率で抽出する吸着剤の技術開発を進め、従来1年程度の抽出期間を1週間程度に短縮し、必要な薬剤コストも約1/10に抑え、従来は収益性が低かった地域でも採算が取れる。今後、海外の資源開発大手との合弁や共同出資を通じた権益確保などを進める。
2023年5月、三菱マテリアルは低コバルト含有率の鉱石からも高効率で抽出できる新技術を開発し、2023年度からチリ・マントベルデ銅鉱山で実証試験を開始すると発表。2027年度に200トン/年規模の商業生産を目指す。
鉱石を硫酸に浸して銅を抽出した後、残渣液からコバルトを抽出する手法が一般的で、従来は採算性からコバルト含有率が0.1〜0.4%の鉱石が使われてきた。新技術では硫酸抽出法を工夫し、コバルト含有率が従来比1/30程度でも採算が取れる。オーストラリアなどの他の鉱山からの生産も検討する。
2023年5月、中国の電池メーカー国軒高科(Gotion High-Tech科)は、リン酸鉄リチウム(LFP)系リチウムイオン電池をベースにエネルギー密度を高めたリン酸マンガン(LMFP)系リチウムイオン電池[Astroinno」を開発したと発表。
EV向け電池パックの重量エネルギー密度は190Wh/kg。これはLFP系を上回り、NCM)系と同等ともいえる。量産が軌道に乗れば、LMFPは従来のNCM系LIBに比べてはるかに低コストにできる可能性が高く、2024年に量産を始めるとしている。
2023年11月、米国エクソンモービルはアーカンソー州で2027年からEV用蓄電池用のリチウムの生産を発表した。北米以外での生産も視野に入れ、2030年までに100万台/年分のリチウム供給を目指す。リチウムはオーストラリア、チリ、中国の3カ国に生産が偏り、供給網のリスク低減に有効となる。
石油・天然ガスの掘削技術を活用して地下約3000mからリチウム含有の塩水をくみあげ、従来より環境負荷の低い新技術でリチウムを分離し、現場のプラントで蓄電池用の素材に加工する。2030年まで約10万トン/年(炭酸リチウム換算)を生産する。
負極材料
車載用LIBの負極材料には、黒鉛やチタン酸リチウムが使用されている。主な使用原料である黒鉛には、天然黒鉛と人造黒鉛の2種類がある。天然黒鉛に関しては安価な資源が中国に偏在している。また、電力消費量の多い人造黒鉛に関しても、電気代の安い中国が優位である。
図2(b)に示すように、負極材料では貝特瑞新能源材料(BTR New Material)が世界シェア首位の18%で、2位は江西紫宸、3位は上海杉杉、4位は広東凱金と中国勢が上位を占め、5位に人造黒鉛系の昭和電工マテリアルズが入る。
2023年5月、クボタは負極材料事業に参入すると発表。10億円超を投じ、阪神工場尼崎事業所で2024年末からチタンニオブ複合酸化物の量産を始める。当初の生産能力は50トン/月で、2030までに5倍以上にする計画。一般的な負極材料の黒鉛と比べ、長寿命化や急速充電対応が期待できる。
2023年5月、米国の電池スタートアップの日本法人Enpower Japan(エンパワージャパン)がリチウム金属電池の工場を横浜市で2023年秋に稼働させる。リチウム金属電池は、LIBの負極を黒鉛からリチウム金属に置き換えることで、エネルギー密度をLIBの2倍程度に増加できる。
ただし、寿命がLIBの1/10と短く、コストも高いという問題を有するが、軽量化や航続距離を重視するドローン向けの需要があるとみて生産を進める計画である。
電解液
LIBの電解液である六フッ化リン酸リチウム(LiPF6)は、原材料である蛍石(フッ素)鉱石について世界全体の約6割が中国で産する。
そのため図2(c)に示すように、広州天腸高新材料が世界シェア首位の18%で、2位は新宇宙、3位は張家港国泰華栄と中国勢が上位を占め、4位に三菱ケミカルとUBE(旧宇部興産)の共同出資会社であるMUアイオニックソリューションズが入る。
2018年には、セントラル硝子は広州天腸高新材料の子会社である九江天賜高新材料と江西省九江市に合弁会社江西天賜中硝新材料有限公司(Jiangxi Tinci Central advanced materials )の設立を発表した。原材料の安定調達とコスト削減を目指している。
セントラル硝子は、六フッ化リン酸リチウム(LiPF6)の需要に対応するため、日本国内に次ぎ、韓国及び中国に電解液生産拠点を設立し、2017年には欧州において電解液製造販売会社を設立している。
セパレーター
セパレーターは図2(d)に示すように、中国の上海エナジーが首位の18%であるが、2位は旭化成、3位は韓国のSK ie technology、4位に東レが入っている。
2021年9月、旭化成は首位の上海エナジーと合弁会社江西恩博新材料有限公司(Jiangxi Enpo New Materials)を設立し、2022年上期に中国江西省高安市に工場を建設して乾式ポリプロピレン(PP)製セパレーターの生産を開始すると発表した。
電気自動車向けリチウムイオン電池(LIB)に使用される高品質・高性能な乾式セパレーターをに加えてエネルギー貯蔵システム(ESS)向けの現地需要を取り込むことを公表している。生産能力2022年上期に1億m2/年から立上げ2028年頃に10億m2/年とする計画である。
LIBの製造プロセス
進む低コスト化
過去を振り返ってみよう。2000年代に入りハイブリッド車が本格化すると、それまで主力であったニッケル水素電池からリチウムイオン電池への置き換わりが始まった。この動きは2018年頃からのEVシフトが本格化すると決定的なものとなる。
ニッケル水素電池(エネルギー密度:40~90Wh/kg)は負極に水素吸蔵合金、正極にオキシ水酸化ニッケル、電解液に水酸化カリウムなどのアルカリ水溶液を用いた二次電池である。 鉛蓄電池(20~40Wh/kg)に比べて高性能で、過充電・過放電に強く急速充放電が可能なため多用されてきた。
一方、リチウムイオン電池(LIB)はエネルギー密度が150~270Wh/kgと高くメモリー効果が小さいことから急速に普及した。しかし、過充電や過放電に弱いためコントローラーが不可欠であり、正極のリチウム含有金属酸化物が高価なため、低コスト化に向けた開発が継続的に進められてきた。
世界的な脱炭素化の流れの中で、EVメーカーは市場への投入機種を拡大し、低価格帯の車両を目指している。そのため車両価格の3割を占める車載電池のさらなる低コスト化が不可欠である。
英国調査会社IHSマークイットによると、車載用リチウムイオン電池の平均価格は2012年から20年にかけて82%下がり、2023年には97ドル/kWhと予想している。
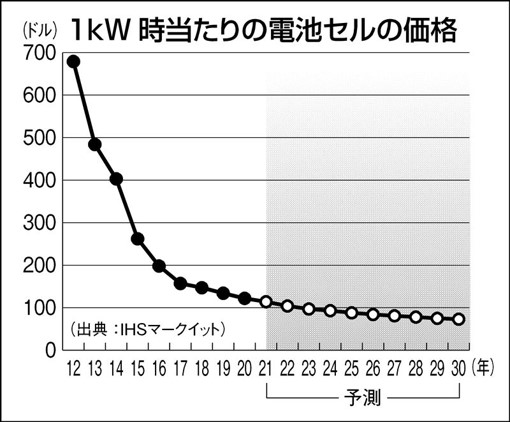
このような低コスト化には、EV需要の増加に伴うLIBの量産効果が大きく影響するが、他方で原材料の調達からLIB製造に至るまでの製造プロセスの革新が不可欠である。
従来のLIB製造工程の問題点
一般的なLIBの製造工程では、正極材料や負極材料に液状のバインダーを混合してスラリー状にする。得られたスラリーをアルミニウム箔(集電箔)に塗布した後、乾燥させて溶剤回収し、圧延して均一厚さのシート状とし、所定の寸法に裁断して正極と負極を製造する。
その後、正極、セパレーター、負極を交互に積層し、組立てた後にタブを溶接して容器に封入し、容器内に電解液を注液して完成である。充放電検査により、特性を確認する。
この製造プロセスのうち、乾燥炉は長さ50~100mと超大な装置となり、設備投資額が莫大となる。また、この乾燥工程が多くのCO2排出の原因となっている。
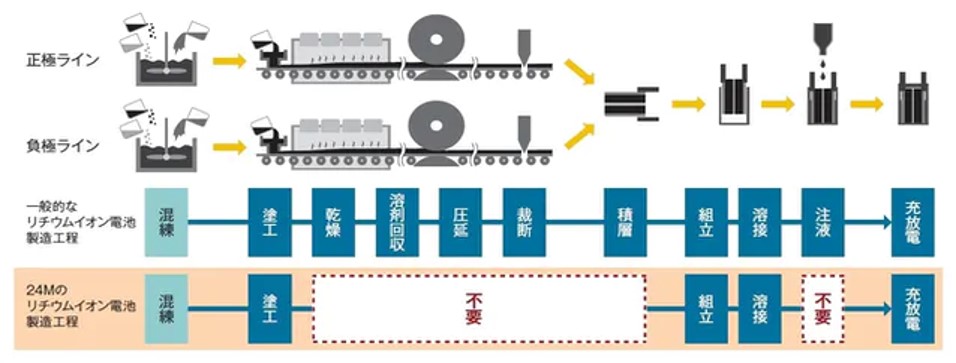
出典:日経クロステック
乾式電極(ドライ電極)技術によるプロセス合理化
2010年に設立された米国新興電池メーカーの24M Technologies(24Mテクノロジーズ)が、車載用蓄電池の製造設備への投資軽減と製造コスト削減を目指して、乾式電極技術によるLIB製造プロセスの合理化を進めていると報じられた。
伊藤忠商事、フォルクスワーゲン(VW)、富士フイルムが出資する24Mテクノロジーズの乾式電極技術は、バインダーの代わりに電解液を正極材料や負極材料と混合してスラリー状にし、アルミニウム箔に塗布して液体成分を蒸発させることなく電極にすることで、乾燥工程を省略できる。
可燃性の電解液の代わりにゲル・粘土・樹脂など半固体状の物質を使うことで、液漏れや発火の可能性は低減され、既存のリチウムイオン電池の生産ラインを活用できる利点が大きい。この半固体電解質に関しては、様々な提案が行われており、一部では固体電池と称するなど定義が定まっていない。
24Mテクノロジーズは流動性のあるスラリーを用いるため、これを「半固体電池」と称している。これにより電池製造工程を1/3に短縮し、設備投資を60%以上削減できるとしている。ライセンス先の企業を合計した生産量は2022年度で0.2GWhで、2026年度には80.5GWhに増加する。
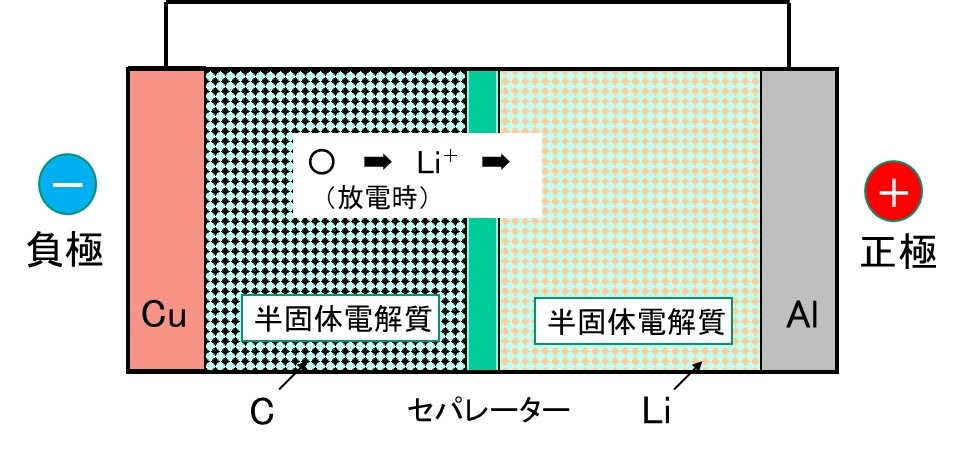
一方、2023年4月、ドイツFraunhofer-Gesellschaft(フラウンホーファー研究機構)のレーザー技術研究所(ILT)は、負極材の乾燥工程でダイオードレーザー(波長980nm、出力6kW)照射により、黒鉛粒子が発熱して液体が蒸発し、従来よりも高い蒸発速度が得られることを発表した。
半固体リチウムイオン電池の開発状況
2020年7月、日本ガイシは、セラミックス素材に電解液を染み込ませた半固体電池である超小型電池「EnerCera(エナセラ)」をIoT機器用に開発した。LIBの3倍となる9千回の充放電が可能で、山梨県富士吉田市でコイン型電池の量産を始めた。
2021年2月、京セラは24Mテクノロジーズ技術を使い半固体電池の量産化を開始した。住宅用蓄電システム2万台/年(容量:200MWh/年)の生産能力を有するが、車載用蓄電池への拡販も始めている。
電極に独自開発の電解液を練り込んで粘土状にする技術を確立し、クレイ型リチウムイオン蓄電池の開発に成功し、従来型の約1.5倍の長寿命を実現した。電極にはリン酸鉄リチウムを使い、セパレータと外装フィルムで正極と負極を完全に分離するユニットセル構造を採用している。
2021年1月、中国EVメーカー上海蔚来汽車(NIO)は、2022年に独自開発した固体電池を搭載した新型車を投入すると発表。中大型セダン「ET7」(44.8万元~)と中型セダン「ET5」(32.8万元~)で、いずれも航続距離:1000kmを超える。蓄電池ををレンタルで使う仕組みも準備している。
エネルギー密度は360Wh/kg、負極にはシリコン・カーボン複合負極材を採用し、正極にはニッケル正極材とナノレベルのコーティング技術を採用した。
2021年12月、フォルクスワーゲン(VW)グループは、EV向けバッテリー事業強化のために3社(ユミコア、24Mテクノロジーズ、バルカン・エナジー・リソーシズ)との戦略的提携を発表した。
ベルギーのユミコアとは、欧州にあるVWの蓄電池工場に正極材料を供給する合弁会社を設立する。2025年の生産開始、生産能力は20GWh/年から始め、2029年までに160GWh/年を目指している。
米国の24Mテクノロジーズとは、新たなバッテリー製造技術の実用化に向けて工場の生産技術の開発に取り組む。低生産コストの車載用蓄電池の開発を進め、2025~2030年の量産化を計画している。
オーストラリアのバルカン・エナジー・リソーシズとは、2026~2031年における水酸化リチウムの調達に係る長期契約を締結した。
VWグループの半固体リチウムイオン電池戦略:
2021年12月、VWグループは、蓄電池事業に特化した法人を新設し、同社が電池生産に係る開発から工場の生産管理までを行い、将来的には原材料のリサイクル事業も担う。
2019年6月、ドイツ北部のニーダーザクセン州ザルツギッターに蓄電池工場を設立し、2025年の操業開始を予定している。同工場が蓄電池事業のハブ拠点として拡張され、電池の量産開始までに総額約20億ユーロを投資し、2030年までに、欧州で6つの蓄電池工場を稼働させる予定。
2021年12月、山形大学発バッテリー・イノベーション・ハブ(BIH)と大阪ソーダは、充放電を繰り返しても分解しにくいゲル状の電解質を採用し、寿命がLIBの2倍の半固体電池を開発した。CO2や排出量や調達コストを5割削減した。2027年にもEVやドローン向けに用途を広げる狙いだ。
2022年9月、エンビジョンAESCは、2024年の量産開始に向け茨城県茨城町で新工場を建設している。マザー拠点と位置づける同工場への導入に向け、乾式電極技術の開発を加速している。また欧米で建設中の新工場でも同技術を活用した生産設備の導入を見込み、世界で競争力の向上につなげる。
2022 年 12月、日本電産は、24M Technologiesよりライセンスされる半固体リチウムイオン電池セルを製造する FREYR Battery(フレイル・バッテリー)と、合弁会社Nidec Energy AS(ニデック エナジー AS)を設立した。ノルウェーのモー・イ・ラーナ市に生産拠点を置く。
テスラ・モーターズ゙は2022年稼働のベルリン電池工場で乾式電極技術を採用し、設備面積とエネルギー消費を1/10に低減できるとしている。テスラの乾式電極技術は、2019年に買収した米国マクスウェル・テクノロジーズの技術に基づいているようで、24M Technologiesの技術とは異なる。
2023年3月、テスラでもドライ電極の製造が軌道に乗っていることが明らかとなった。
2023年4月、中国CATL(寧徳時代新能源科技)は「上海国際自動車ショー 2023」で、「凝聚態電池(Condensed Battery)」発表した。エネルギー密度:最大500Wh/kgと高い点が特徴である。電池の詳細は明らかにされていないが、半固体蓄電池の一種と考えられている。
2023年5月、ノルウェーのモー・イ・ラーナに小規模ラインを開設して半固体リチウムイオン電池の製造を開始したFREYR Batteryは、数十億ドルを投資して2025年までにノルウェーの「Giga Arctic」とジョージア州アトランタの「Giga America」の工場を建設する計画では公表した。
生産能力は合計で50GWh/年になる予定で、製造工程の簡素化によりコスト25%削減を実現した。
2023年12月、伊藤忠商事、富士フィルム、フォルクスワーゲンなどが出資する米国スタートアップ24Mテクノロジーズは、2025年にもリチウムイオン電池に比べて製造コストを最大4割減らした発火リスクの低い「半固体電池」を供給すると発表した。
電池パックのスペースを効率よく使える技術を開発し、部材や構造部品も減らし、通常のリチウムイオン電池に比べてエネルギー効率を5割程度高めることができる。
2024年2月、京セラは住宅向け蓄電システムの新製品「Enerezza Plus(エネレッツァプラス)」を製品化し、今春より販売する。半固体クレイ型リチウムイオン蓄電池で、従来は12000回の充放電で容量が60%に減少したが、20000回に長寿命化し、-20℃~40℃までの屋内外への設置に対応する。
1ユニットの外形寸法:W485×H562×D280mm、重量:64kg、容量:5.5kWh、税込み価格:341万円で、これを複数台組み合わせた11.0kWh(561万円)、16.5kWh(781万円)をラインアップ。太陽光発電と蓄電池の両方に対応できるマルチ入力型パワーコンディショナーとセット販売し、EVや発電機の電力を自宅内で使用できる。
全樹脂リチウムイオン電池の開発状況
「全樹脂電池(APB:All Polymer Battery」は慶應義塾大学の堀江英明特任教授が考案し、低コストの大量生産技術を確立するために2018年10月にAPBを設立した。2021年にはAPB福井センター武生工場を建設し、集電体に樹脂を使う「全樹脂電池」の開発・製造を進めている。
全樹脂電池の仕組み
従来の金属集電材料に替えて導電樹脂を採用し、活物質(LiやPt)を特殊な樹脂(ゲルポリマー)でコーティングすることで電解液を不要とし液漏れの心配がない。この特殊な樹脂は電子やイオンが移動できる材料で、電解液の役割りを果たしている。半固体電池を全固体電池に一歩近づけたイメージである。

すなわち、ゲルポリマーでコーティングされた正極と負極の活物質に粒子状の導電助剤や導電性繊維を混ぜた後、導電樹脂上に塗工してプレス・切断成形する。得られた正極シートと負極シートを、セパレーターを挟んで積層してシーリングを行いセルとするため乾燥工程が不要である。
次ぎに、得られたセルを用途に応じて積層してモジュール化する。一般的なLIBでは、金属集電体の横からタブを出して溶接により接合して電極とするが、全樹脂電池ではセルの表面が導電樹脂(電極)であるため、従来の溶接工程が不要で、大幅な低コスト化が可能である。
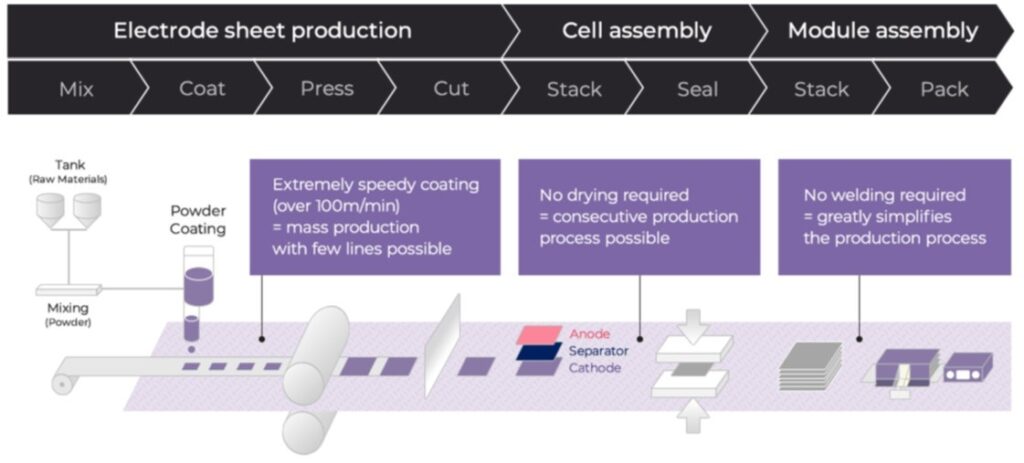
出典:APBホームページ
従来型のLIBでは、短絡を起こした場合に金属部材を通じて大電流が流れ、急激な内部発熱により発火する可能性があった。しかし、金属部材を使わない全樹脂電池は、短絡が生じた場合でも樹脂の電気抵抗が大きいため大電流が流れず発火には至らず、安全性に優れている。
当初、APBは、2021年から全樹脂電池の生産を開始し、現状のリチウムイオン電池の価格の1/2、2024年までに30GWh/年程度の量産工場の新設を目指すと宣言していた。しかし、2023年3月に当初の計画を撤回、2025年に高速量産の実現、2026年度からの大規模量産化すると再宣言している。
APBは全樹脂電池のエネルギー密度を公表していないが、LIBのエネルギー密度と同等としており、2024年までに150~250Wh/kgが達成可能と考えられる。また、同社が注目している用途は、再生可能エネルギー電力を蓄える「定置用電池」とし、使用環境の厳しいBEV向けは想定していない。
商品化動向
トリプルワン、三洋化成工業、JFEケミカル、JXTGイノベーションパートナーズ、大林組、慶應イノベーション・イニシアティブ1号投資事業、帝人、長瀬産業、横河電機などの出資企業は、全樹脂電池の開発・市場形成のパートナーとして、量産や市場展開に必要な支援を行っている。
JFEケミカルは、APBに負極材料のハードカーボンを提供する。帝人のカーボンナノファイバーは、APBの電極添加剤として活用されている。グンゼは樹脂電極、三洋化成工業はコーティング活物質の材料開発に取り組み、高性能な全樹脂電池の実現に協力している。
2020年7月、APBは全樹脂電池を川崎重工業の石油パイプラインなど海中設備の点検などに使う自律型無人潜水機(AUV:Autonomous Underwater Vehicle)に搭載し実証実験を始めた。全樹脂電池は水深3000mでも耐えられることが確認されている。
2023年4月、APBは、サウジアラビア国営石油会社サウジアラムコと、同電池の共同開発に向けて連携することで基本合意した。国内に留まっていた全樹脂電池の技術開発を、海外企業との連携により加速するのが狙いである。現在は、大規模量産化に向けた高速製造ラインの開発に取り組んでいる。
高速製造にめどを立て、8GWh/年の量産工場を福井県内に建設し、2026年度から稼働させる計画。
ポスト・リチウムイオン電池に向けて
製造プロセス合理化
以上のように、従来のリチウムイオン電池(LIP)の低コスト化に向けた製造プロセス合理化の観点から、半固体電池や全樹脂電池の開発が進められてきた。
2023年4月、中国の寧徳時代新能源科技(CATL:Contemporary Amperex Technology Co. Ltd))は「凝聚態電池(Condensed Battery)」発表した。エネルギー密度:最大500Wh/kgと高い点が特徴である。電池の詳細は明らかにされていないが、半固体蓄電池の一種と考えられている。
また、スタートアップのAPBは全樹脂電池のエネルギー密度を公表していないが、LIBのエネルギー密度と同等としており、2024年までに150~250Wh/kgが達成可能と考えられる。ただし、APSが注目している用途は、再生可能エネルギー電力を蓄える「定置用電池」としてである。
主要原料の変更
一方、2022年4月、リチウム(Li)の市場価格高騰で蓄電池を取り巻く状況が変化していると報じられた。2022年3月初頭時点で、炭酸リチウム(Li2CO3)価格は2020年末の16倍を超えた。また、児童労働問題やロシアのウクライナ侵攻などでニッケル、コバルト、アルミニウムなども値上がりしている。
リチウムイオン電池(LIB)の主要原料の高騰は、LIB価格の高騰を招くとともに、今後の蓄電池原料の安定供給への不安が広がった。
2021年7月、中国の寧徳時代新能源科技(CATL:Contemporary Amperex Technology Co. Ltd)は、ナトリウムイオン電池(NIB:Natrium Ion Battery)を2023年までに市場投入すると公表した。LIBの主要原料ある炭酸リチウム(Li2CO3)の市場価格が暴騰した結果である。
将来にわたり供給不安がない炭酸ナトリウム(Na2CO3)が脚光を浴びたのである。NIBはエネルギー密度ではLIBより若干低目であるが、量産が進めばかなり価格が安くなる。しかも、安全性や信頼性がLIBより高く、超急速充電や低温(ー30℃)での出力特性に優れている。
2022年7月、車載電池最大手の中国CATLは鉄(LFP)系リチウムイオン電池を、2023年に発売した。LFP系LIB(以下、LFP)は上汽通用五菱汽車が生産する超低価格の「宏光MINI EV」に採用され、米国テスラはCATLから供給を受けて上海で製造する「model 3」にも搭載される。
高価なニッケルやコバルトを使わないLFPは、エネルギー密度がLIBに比べて低目であるも関わらずBEVに採用された。このことからBEVの訴求ポイントは航続距離だけではなく、機種に応じた低コスト化も重要であることが明らかになった。
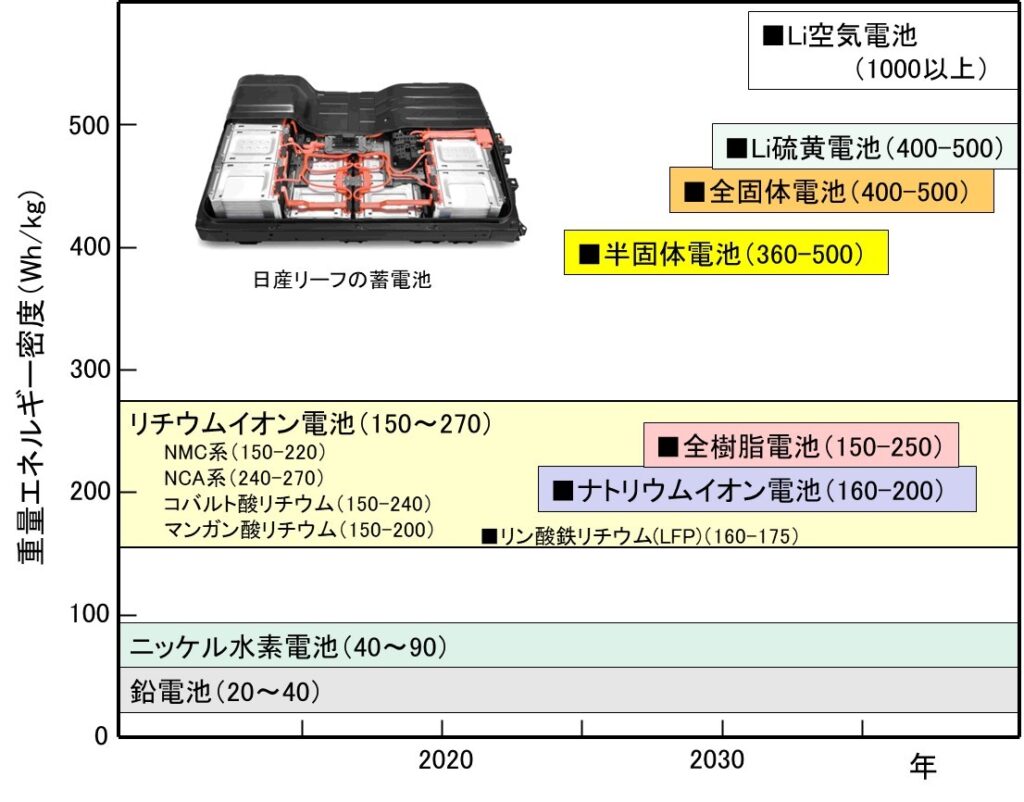
車載電池最大手の中国CATLの動きが早い。中国のリチウムの産出量割合は2016年時点で世界全体の約6%、埋蔵量でも約22%と低く、2021年末時点でLi2CO3の中国国内需要の7割を輸入に頼っているのが現状である。また、ニッケルやコバルトに関しても主要産出国ではない。
ポスト・リチウムイオン電池
ナトリウムイオン電池の開発動向
ナトリウムイオン電池の仕組み
ナトリウムイオン電池(NIB:Natrium Ion Battery)の基本構成は、リチウムの代わりにナトリウムが用いられた二次電池である。中国CATLのNIBには、高価なニッケルやコバルトを使わないNFP(ナトリウム・鉄・リン)系正極材料が採用されている。
この正極材料と炭素(ハードカーボン)などの負極材料の間に、ポリオレフィンの微多孔フィルムなど絶縁性に優れたセパレーターを挟み、六フッ化リン酸ナトリウム(NaPF6)などの電解液が注入されている。
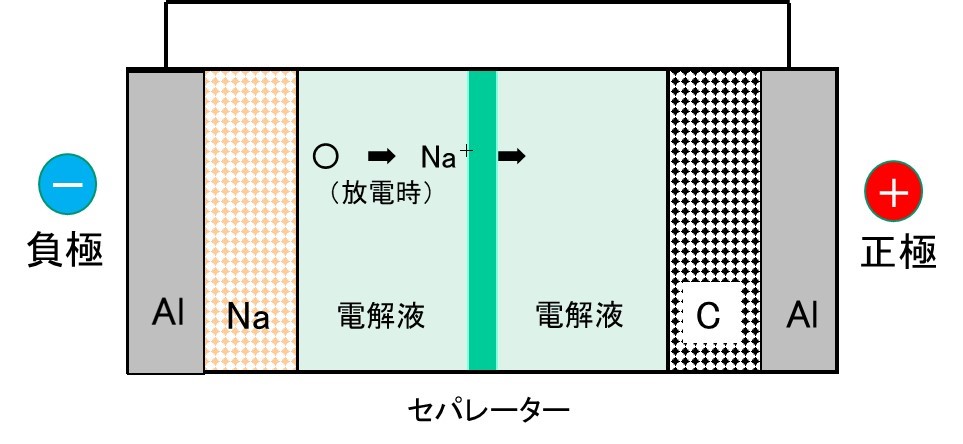
CATLが公表しているエネルギー密度は160Wh/kgである。LIB(150~270Wh/kg)に比べて高くはないが、原材料の調達リスクが少なく、将来を見通しての安定供給や量産による低コスト化が可能である。現在、200Wh/kgを目指した開発が進められている。
また、急速充放電性能はLIBよりも優れ、15分で80%以上を充電できる。-20℃の低温環境でも定格容量の90%を利用でき、-40℃でも動作が確認されている。
CATLはこの低温特性を生かして、EV向け蓄電池をNIBとLIBのハイブリッド構造として並列に接続すれば、極低温時にLIBが動作しなくてもNIBにより走行できるとした。中国科学院は2022年、負極に金属ナトリウムを使い、容量をリチウムイオン電池並みに高める技術を非公式に発表した。
一方、NIBの安全性に関して、金属ナトリウムが析出時に非常に活性であるため発火事故につながりやすく、電解液に有機溶媒系の材料を使用するため、LIBと同程度の安全性と考えられる。
全固体ナトリウムイオン電池の仕組み
ナトリウムイオン電池の電解質を固体にしたものが、全固体ナトリウムイオン電池(全固体NIB)である。エネルギー密度が低いNIBの改良版で、電解質を固体にすることで高エネルギー密度化を図り、液漏れや不燃化などの対策を施し、高い安全性を目指している。
日本電気硝子は正極材料、負極材料、固体電解質(β”アルミナ(Na2O・5.33Al2O3))を全て結晶化ガラスとした全固体ナトリウムイオン電池を発表した。エネルギー密度はLFP系LIB並みで、利用可能な温度領域が-40~200℃と広く、モジュールを多層化している。
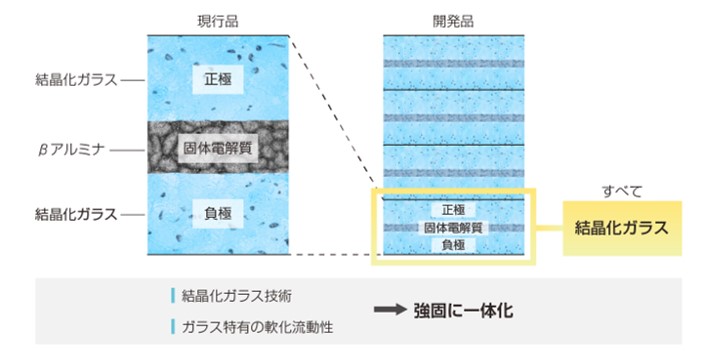
メーカー関連の動向
2021年7月、中国の寧徳時代新能源科技(CATL:Contemporary Amperex Technology Co. Ltd)は、リチウムを使わないナトリウムイオン電池を2023年までに市場投入すると発表した。エネルギー密度は160Wh/kgで、2023年までに部材などのサプライチェーンを構築する。
2021年12月、インド財閥最大手のReliance Industries子会社のReliance New Energy Solarは英国NIBベンチャーのFaradionを1億英ポンド(約155億円)で買収した。FaradionのNIBセルのエネルギー密度は、設計値が155Wh/kg(実効値は140Wh/kg)である。
2021年12月、ファーウェイ系ファンドの出資を受ける中科海鈉科技は、生産能力5GWh/年のNIB工場の建設を発表した。2023年3月時点での生産能力は2GWh/年である。生産のスケールメリットで、10GWh/年に達すればLIBと同コストになるとし、2025年までの達成を目指している。
2022年1月、中国の徳蘭明海科技(Shenzhen PowerOak Technology)が、個人向けにパワーコンディショナーを兼ねたポータブル電源にNIBを実装した「Bluetti NA300」と、NIBの拡張電池モジュール「B480」を発表した。
2023年3月、日本電気硝子は、オール結晶化ガラスによる全固体NIBを発表した。2025年の実用化を目指して開発を進めている。LIBよりも安価で安全な電池とし、定置用蓄電池を目指している。
現在のエネルギー密度はLFP系LIB並みで高くないが、全固体NBIは、理論上高いエネルギー密度を実現できる可能性があり、今後の開発動向に注目したい。
2023年3月、セントラル硝子は2024年にもNIB向けの電解液の量産を開始すると発表した。2024年に1GWh/年規模の生産を目指し、中国にある既存の合弁工場での生産も検討する。
2023年4月、中国CATLは、自社開発したNIBが中国Chery Automobile(奇瑞汽車)のBEVに採用されたと公表した。NIBが量産車に搭載されるのは世界初である。現時点で、BEVの車種や発売時期、NIBの搭載容量などは未公表である。
2023年5月、日経クロステックが、「NIB時代幕開け、関連メーカーが50社超で価格はLIBの1/2へ」と報じた。2年前にはNIBの開発・量産に取り組むのは世界で数社であったが、現時点では電池メーカーだけで少なくとも20社超、原材料や部材メーカーも含めると約50社に達する。
中国企業が主体であるが、フランスのTiamat Energy、英国のFaradionなども、NIBを使った定置用蓄電池を商品化している。
2023年8月、世界初の量産型ナトリウムイオン電池(NIB)電動二輪車が、中国山西省陽泉市で公表された。同省の華陽新材料科技集団と江蘇省の電動自転車メーカーの江蘇新日電動車が共同開発した。 NIBはLIBに比べて低温に強く、豊富で低価格な資源を使って製造される。
2025年4月、中国CATLはEV向けナトリウムイオン2次電池「Naxtra」を、6月に量産出荷すると発表。エネルギー密度が175Wh/kgで、同社の主力製品であるLFP系リチウムイオン2次電池とほぼ並ぶ。-40℃の極寒でも出力の低下は10%未満にとどまる。
ナトリウムイオン電池の課題
ナトリウムイオン電池(NIB)の最大の関心事は、現在主流となっているリチウムイオン電池(LIB)に置き換わる可能性の有無である。結論は、LIB市場の部分的なNIBへの置き換えは進むが、ポスト・リチウムイオン電池の本命とはいえない。
NIBの最大の強みは、原材料となる炭酸ナトリウム(Na2CO3)や食塩(NaCl)が非常に安価で入手性が容易なことである。LIB並みに量産化が進めば、NBIの製造コストはLIBの7割に抑えられるとの試算もある。また、既存のLIB製造ラインを大きく変更せずに使えるメリットも大きい。
最大の課題は、エネルギー密度が160~200Wh/kgと、LIB(150~270Wh/kg)やLFP系LIB(160~175Wh/kg)と同等な点である。エネルギー密度が同等で安価であれば良しとする経営判断で、定置用蓄電池や格安BEV向けに動くメーカーが中国企業を中心に広がっている。
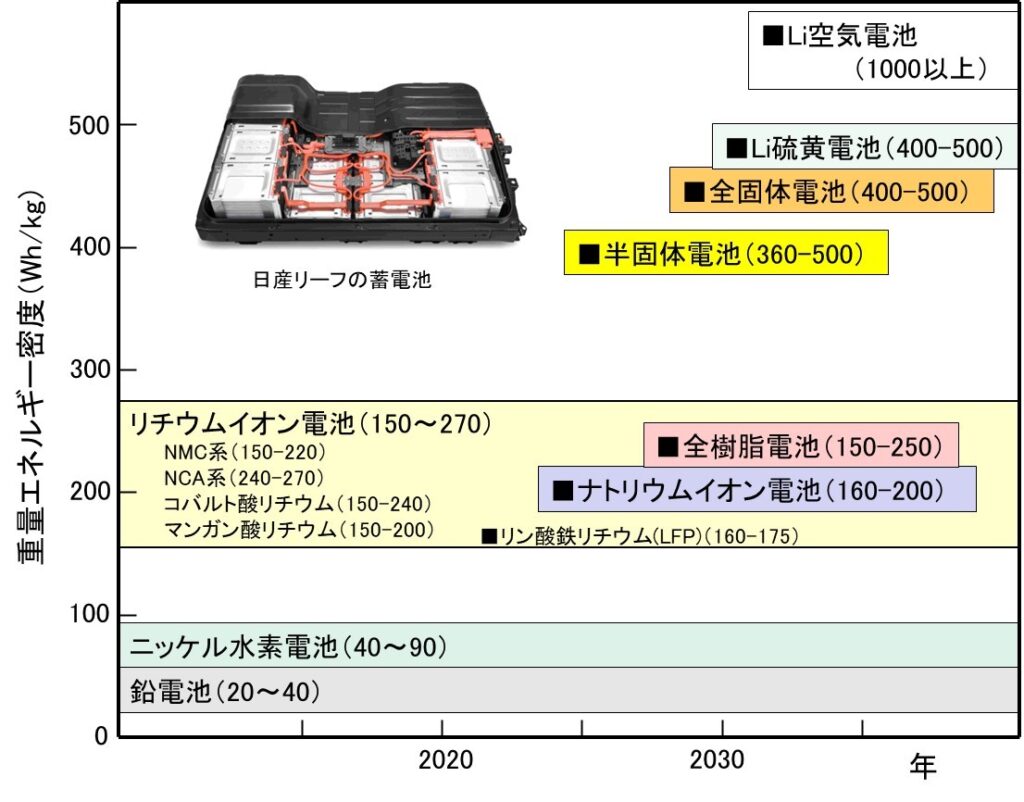
一方、他社との差異化のためには、現状LIBの2倍以上のエネルギー密度が必要である。そのため、NIBは、全固体化によるエネルギー密度と安全性の向上を目指し開発が進められている。
日本電気硝子が、2025年の全固体NIBの実用化を目指して開発を進めており、定置用蓄電池を用途に掲げている。現時点で、エネルギー密度がどの程度向上するか未定であるため、BEV向けのポスト・リチウムイオン電池の本命とはいえない。
2023年5月、中国自動車業界団体の全国乗用車市場信息聯席会(CPCA)は、自動車メーカーのNBI採用意欲が高まっていないと発表した。コストがLIB(0.51元/kWh)をわずかに下回る0.49元/kWhに留まり、一方、炭酸リチウム価格が、昨年秋のピーク時に比べて大きく低下していることが原因。
現時点で、自動車メーカーにとって搭載電池を換えるメリットは小さい。しかし、CPCAはサプライチェーンの整備後、NBIの材料コストが0.29元/kWhとなる見通しで、LIBは今後さらにサプライチェーンが整備されても0.4元/kWhまでしか下がらず、NBIの方が約3割安くなるとしている。
2024年11月、中国・比亜迪(BYD)が、主に定置用蓄電池向けにNIBの量産を開始した。100億(約2000億円)を投資した30GWh/年規模の工場も近く稼働する。EVや電動二輪車、電動フォークリフトなど向けにも量産を始める。また、中国・寧徳時代新能源科技(CATL)は、EV向けNIBを2025年6月に量産出荷する。
量産が進み製造コストが下がれば、リン酸鉄リチウム(LFP)系LIBを代替する可能性がある。
全固体リチウムイオン電池の開発動向
全固体LIBの仕組み
次世代電池の本命とされてきたのは、安全性に優れ、高エネルギー密度の全固体リチウムイオン電池(All-solid-state Lithium Ion Battery)である。電解液を固体電解質に換えるのが特徴で、固体電解質の探索や様々な正極材料、負極材料との組合せの検討が行われている。
全固体リチウムイオン電池(全固体LIB)の基本構成は、セラミックスなどの固体電解質を使用するため、従来のLIBと比べて電解液とセパレーターが不要となり、正極活物質や負極活物質に高容量な材料の採用が可能となる。車載用の全固体LIBは、開発途上にある。
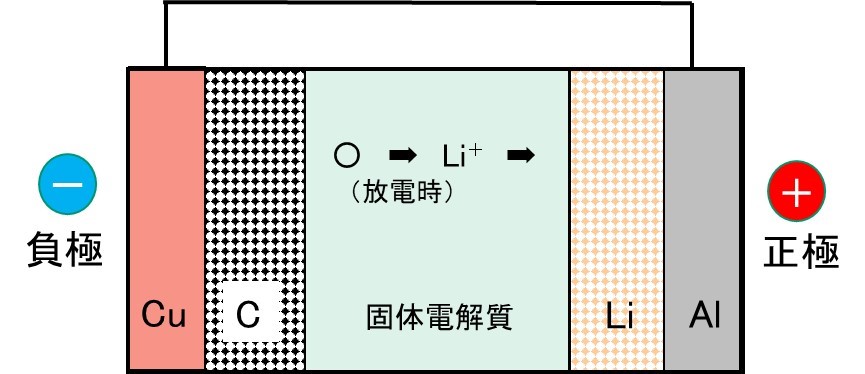
正極材料はLIBで使われてきたコバルト酸リチウム、マンガン酸リチウム、NCM(ニッケル・コバルト・マンガン)などが検討されている。また、負極材料には既存の炭素(黒鉛)が主流で、チタン酸リチウム、シリコン系、ケイ素、リチウムなども検討されている。
固体電解質は硫化物系と酸化物系に分類され、様々な材料が検討されてきた。2016年に硫化物系で有機電解液に匹敵するリチウムイオン導電率のLi10GeP2S12(LGPS)やLi9.54Si1.74P1.44S11.7Cl0.3が見出され、室温での加圧のみで電極と固体電解質の接合が可能なため、注目を集めている。
硫化物系は硫黄(S)を含み、水分とSが反応すると有害な硫化水素(H2S)が発生するため、安全対策が必要になる。BEVなど主に大容量電池への適用が進められている。一方、酸化物系は硫化物系と比較すると安全性は高いが出力が低く、主に小容量電池への適用が進められている。
一方、全固体LIBは製造方法により原材料の粉や粒を固めて製造するバルク型全固体LIBと、真空蒸着法やスパッタ法など気相法で製造する薄膜型全固体LIBに大別される。バルク型は大容量電池が製造可能でBEV向け、薄膜型は小容量であるが長寿命のために小型デバイス用途の開発が行われている。
固体電解質を使う全固体LIBは、現時点でもエネルギー密度が400~500Wh/kgと高く、液漏れや発火の危険性も極めて低い。また、超急速充電(10分以下)性能の向上や、寒冷地での性能劣化防止なども目指して開発が進められている。
しかし、固体電解質を使うために、充放電による電極の膨張・収縮で界面はく離を生じて性能が劣化する問題が生じている。また、現状の生産コストはLIBの4倍超ともいわれ、BEV向けのバルク型全固体LIBの量産技術は確立されていない。
全固体LIBの開発動向
2018年9月、NEDO事業「先進・革新蓄電池材料評価技術開発」の第1期(2013~2017年度)に続き、企業23社が参加する100億円規模の第2期(2018~2022年)の全固体電池開発プロジェクトが、技術研究組合「リチウムイオン電池材料評価研究センター(LIBTEC)」のもとで進められた。
2022年3月、経済産業省は官民協議会で「全固体電池に集中投資」した政策について異例の反省を表明した。全固体電池の開発が遅れ、半固体LIBやリチウム硫黄電池などの出現が影響している。早急に次世代電池の開発戦略を再構築する必要がある。
自動車メーカーの動向
2018年6月、ドイツ・フォルクスワーゲン(VW)は全固体電池を2025年までに実用化すると発表。中国電池大手Ganfengと提携し、2020年8月には100MWhの全固体電池パイロット生産ライン計画を発表、2024~2025年の量産を目指している。従来LIBと比較して2〜10倍の容量を目指している。
また、米国の全固体電池ベンチャー企業Quantam Scapeの株式を取得し、2018年に1億ドル、2020年に最大2億ドルの追加投資を行った。
2020年8月、トヨタ自動車は、全固体電池を搭載した試作車のナンバーを取得して試験走行を実施した。2021年9月には、全固体LIB電池をハイブリッド車から採用していく方針を発表した。

2021年8月、Mercedes-Benz(メルセデスベンツ)は、2030年までにBEVだけを生産すると発表し、カナダのHydro-Québecと全固体電池技術の開発で提携、その後も、米国スタートアップ企業Factorial Energy、ステランティス、現代自動車との共同開発契約を締結している。
また、2022年1月には台湾のProLogium Technologyとも共同開発で合意している。
2021年10月、米国ゼネラル・モーターズ(GM)は2022年半ばにミシガン州に車載電池の開発拠点を設けると発表した。LIBの生産コストを6割低減する目標に取り組み、韓国のPOSCO Chemicalと提携してリチウムメタルと全固体電池の開発に注力する。
2021年10月、韓国の現代自動車と傘下の起亜は、全固体電池開発の米国スタートアップFactorial EnergyとBEV向け全固体電池の共同開発契約を締結した。全固体電池について自社主導で先行開発し、搭載車の量産を2027年に開始すると公表した。
全固体電池は航続距離:500km以上で、18分で容量の80%まで充電できる。Factorial Energyは、Mercedes-Benz、ステランティス、現代自動車との共同開発契約により、全固体電池の実用化を目指しており、2022年にパイロット生産施設の建設開始を予定。
2021年11月、日産自動車は、全固体LIBの量産時期を2028年と公表した。自社開発の全固体LIBを搭載したBEVの市場投入を目指し、電池の量産化に向けたパイロットラインを、2024年度までに横浜工場内に設置する予定。
電池コストについて、2028年度に75ドル/kWh、その後、65ドル/kWhまで低減可能(BEVがガソリン車と同等のコストレベルになる価格)としている。
2022年1月、本田技研工業は全固体LIBの量産時期を2030年と公表した。開発中の全固体LIBについて実証ラインの建設を決定し、約430億円を投資して2024年春の立上げを予定し、2020年代後半に投入されるモデルへの採用を目指す。
2023年1月、BMWグループは、米国Solid Power(ソリッドパワー)との共同開発契約を拡大し、ミュンヘン近郊のパルスドルフにあるセル製造コンピテンスセンターに、全固体電池の試験生産ラインを設置すると発表。
2023年中にソリッドパワーはBMWグループに試験用のフルスケール電池セルを提供し、BMWは2025年までに全固体電池を搭載した実証車を生産、2030年までに市販モデルを投入する計画。
2024年4月、日産自動車の全固体電池の材料が公表された。固体電解質には硫化物系、負極にはリチウム(Li)金属、正極にはハイニッケルの三元系(ニッケル、マンガン、コバルトの酸化物を正極活物質の主成分とするNMC)を採用する。体積エネルギー密度は、従来比約2倍の1000Wh/Lをめざす。
2025年3月、横浜工場内に現在建設中のパイロット生産ラインを稼働開始、2026年度に、試作車の公道テストを実施する。2028年度には新型EVに全固体電池の搭載をめざす。
2024年11月、本田技研工業は全固体電池を2025年1月から実証生産を発表。延べ床面積:2.74万m2、総投資額:430億円で、2020年代後半に従来のEV電池と比べ航続距離を2倍、電池コストを25%低減、重量を35%低減、2040年代には同2.5倍、40%低減、45%低減をめざし、将来は二輪車や航空機への搭載も検討する。
本田技研工業は他社からの電池供給に頼り、中国ではCATLと組み、北米では韓国のLG系と合弁会社を設立したが、40年の「脱ガソリン」の目標達成に向けて、電池技術を内製化する。
トヨタ自動車は航続距離を現行EVから2.4倍伸ばし、航続距離:1200kmの量産車を2027〜28年に投入し、上海汽車集団傘下の高級EVブランド「智己汽車」には2027年から搭載する計画がある。
以上のように、現時点で全固体電池開発の先頭を走るトヨタ自動車でも、BEV用に十分なエネルギー密度、出力密度、寿命が達成できたとの発表はなく、2020年代前半とされてきた全固体LIBの量産時期が、2020年代後半にずれ込む可能性が示されている。
蓄電池メーカーの動向
2019年2月、日立造船は、硫化物系固体電解質を用いた全固体LIB「AS-LiB」をサンプルを出荷し、少量生産を開始した。2021年3月に、容量:1mAh、体積エネルギー密度:約 91Wh/L、利用温度:-40~100℃を発表し、人工衛星など特殊環境下での需要を想定している。
2019年6月、中国CATLは「硫化物系全固体LIBは開発中でサンプルも作った。だが、商品化するのは2030年以降になるだろう」と公表した。「現行の液系リチウムイオン電池を効率よく使いこなすことが、コスト面でも航続距離の面でも電気自動車(EV)にとって最善だ」と述べた。
トヨタの技術者によると、「電池セルの価格が50ドル/kWhまで下がってようやく、EVと内燃機関車のパワートレーンのコストは同等になる」という。
2021年5月、日本特殊陶業は酸化物系固体電解質(Li7La3Zr2O12)の全固体LIBを発表。容量:0.5~10Wh、体積エネルギー密度:300Wh/L、利用温度:-30~105℃で、ispaceの民間月面探査プログラム「HAKUTO-R」の探査機に搭載したが、2023年4月に月面着陸に失敗した。
液体の電解質を含まないため、真空だけでなく太陽の直射や宇宙線にも耐性を有している。
2021年11月、GSユアサは耐水性を高めた窒素含有硫化物固体電解質の開発に成功し、これを改良して、全固体LIBを2020年代に実用化すると発表。
2021年11月、マクセルはアルジロダイト硫化物系電解質を使用した容量8mAh、直径9mmのコイン形全固体LIBのサンプル出荷を開始した。耐熱性に優れ、利用温度:ー60℃~125℃の広い。京都事業所に20億円を投じて生産ラインを構築する。
2022年3月、サムスンSDIは、2023年に小型バッテリー、2025年に中型・大型バッテリーの技術検証を終え、セル組み立て設備をはじめとする新規工法、インフラなどを導入し、2027年中に全固体電池の量産に本格突入する方針を発表。
2015年に硫化物系全固体LIBでエネルギー密が300Wh/kg、2019年に負極側にAg-C複合体を用いた硫化物系全固体電池で体積エネルギー密度900Wh/Lを実現したと発表。正極にはNi90%のZrコートNCM、電解質はアルジロダイト電解質を使用した。
2022年6月、スタートアップの米国Solid Powerは、2022年初頭に自動車生産用の全固体電池のテストを開始しており、EV向け全固体電池セルのパイロット生産ライン設置を完了したと発表した。米国Ford、A123 Systems、Samsung Venture Investmentなどが出資している。
2023年3月、マクセルは京都事業所に20億円を投じ、4月に硫化物系固体電解質を用いた大容量全固体電池の生産ライン構築し、6月から産業用ロボット向けの量産品を試験出荷する。セラミックパッケージ型(容量:8mAh)で、耐用年数が10年程度と長く、零下~100℃の温度帯での使用。
2023年6月、出光興産は、全固体電池の固体電解質の生産能力を増強すると発表した。千葉事業所のプラントからサンプル品を出荷しており、2025年3月までに増強する。また、2023年7月には第2プラントを研究所に新設する。2地点で製造方法を変え、異なる特性を求める顧客の要望に対応する。
2025年3月には、千葉事業所の硫化リチウムの製造設備の建設に213億円を投じ、2027年に大型プラントを完成する計画を公表した。生産した材料は、トヨタ自動車が2027〜28年に実用化するEVに使う。
2023年9月、パナソニックHDは、全固体電池を2020年代後半に実用化すると公表した。安全性が高く、充電時間がリチウムイオン電池の1/20程度に短縮(3分程度で電池容量の8割を充電)、充放電回数は数万回で、ドローンや小型ロボットへの採用を目指す。将来的にはスマートフォン、家庭用乾電池なども視野に入れる。
2023年10月、マクセルは、セラミックパッケージ型の25倍となる容量:200mAhの円筒型全固体電池「PSB23280」の開発を発表。寸法は直径約23mm×高さ約2mm、-50~150℃の温度帯で使用できる。2027年頃には500mAhに引き上げて車載などに用途を拡大する。
2024年3月、韓国電池大手のサムスンSDIは、EVなどに搭載する全固体電池の2027年からの量産を発表。2023年秋にソウル近郊水原市の研究所に試作ラインを設け、2024年に入り世界の自動車大手にサンプル出荷を開始。自社製LIBと比べてエネルギー密度を40%向上、900Wh/Lの高性能品を2027年から量産する。
全固体リチウムイオン電池の課題
全固体電池の技術開発はトヨタ自動車やパナソニックホールディングスなど日本企業が先行すると言われて久しいが、韓国のサムスンSDIやLG化学など海外勢も追い上げており、BEV向けなどの大規模な量産で日本勢が優位性を保てるかが大きな課題になっている。
英国のスタートアップllika(イリカ)は、薄膜型の酸化物系全固体電池(シリコン負極)の開発を進めている。FiatグループのComuauとの提携で10kWh/週の全固体電池製造ラインを建設し、2022年上半期の初期製品販売を計画している。
また、イリカはEV向けに大型化した全固体電池「Goliath」の開発を進めている。
一方、ベルギーの研究機関imecは、2019年6月に体積エネルギー密度が425Wh/Lと高い固体電解質のLiイオン2次電池(LIB)を開発したと発表。正極活物質にはLFP(LiFePO4)、負極活物質には金属リチウムを採用。ただし、400Wh/L超はLIBの標準的な値である。
2024年には1000Wh/L、しかも充電速度を20~30分に短縮できるとしている。液体電解質を正極材料にしみ込ませ、これを乾燥させて電解質を固体化してから負極を形成するプロセスで、量産時に既存の液体電解質のLIB向け製造装置を多少変更するだけで製造可能としている。
以上のように、車載用全固体LIBの開発に関して、従来は硫化物系のバルク型固体電解質が主流であったが、最近では酸化物系の薄膜型固体電解質の開発でも進捗が認められる。また、半固体LIBやリチウム硫黄電池など新展開も相次いでおり、全固体電池の開発戦略を見直す必要がある。
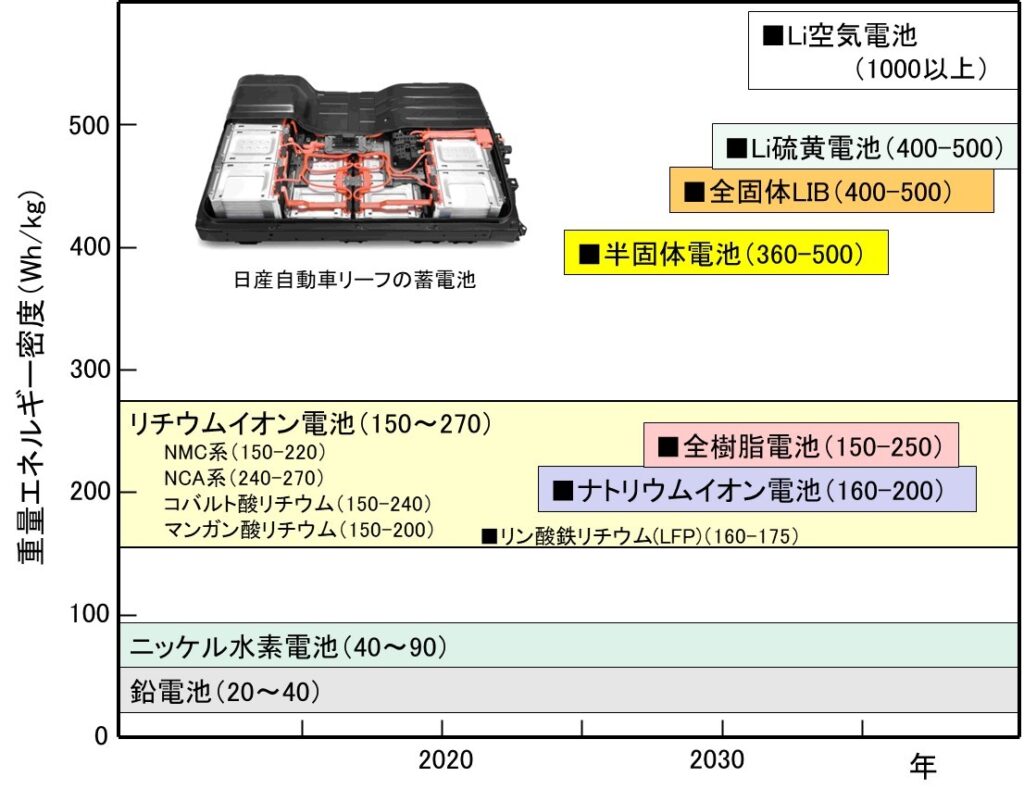
リチウム硫黄電池の開発動向
リチウム硫黄電池の仕組み
リチウム硫黄電池(LiSB:Lithium-Sulfur Battery )は、正極に絶縁体の硫黄(S)に活性炭などの導電助剤を複合化させ、負極に金属リチウム(Li)またはリチウム合金を用いる。電解質はリチウムイオン電池(LIB)と同様に有機溶媒を用いた電解液をはじめ、イオン液体なども検討されている。
放電時は負極でリチウムが酸化・溶解し、正極で硫黄が段階的に還元され、反応中間体である複数種の多硫化リチウム(リチウムポリスルフィド)を経て硫化リチウムに還元される。一方、充電時は負極でリチウムイオンが金属リチウムに還元・析出し、正極で硫化リチウムが硫黄へ酸化される。
リチウムイオン電池(LIB)と比べて原材料が軽量・安価で資源的にも豊富なため、供給リスクが低い。理論エネルギー密度は2500Wh/kgに達し、LIB(150~270Wh/kg)に比べて極めて高いが、現状は400~500Wh/kgに留まる。LIB製造プロセスの転用が可能で、新規投資の抑制が可能である。
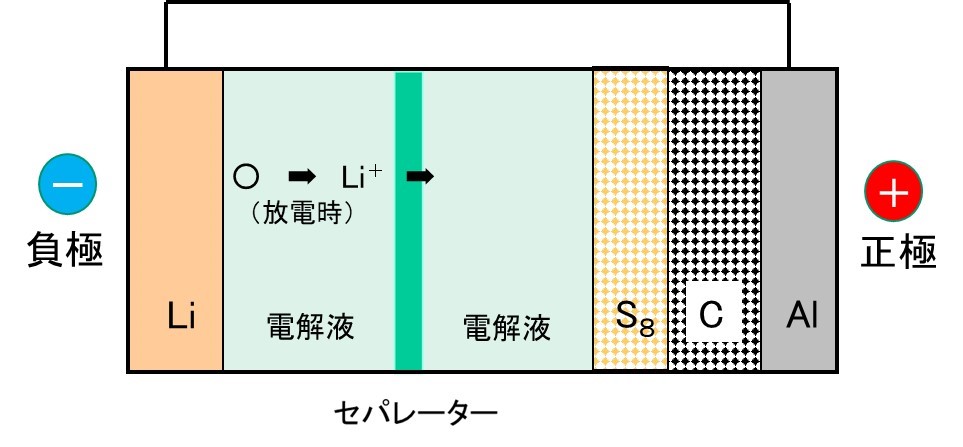
しかし、放電時に正極の硫黄が多硫化リチウムとして電解液中に溶解し、充放電に伴う膨張・収縮で劣化するため、充放電サイクル特性(サイクル寿命)が短い。負極では電解液との界面にリチウムの樹枝状組織(デンドライト)が形成され、容量低下や短絡に至る課題がある。
これらの課題を解決するために多くの研究開発が行われている。電解液に関しては、難燃性の溶媒和イオン液体[Li(G3)1][TFSA]を採用することで、正極の硫黄の溶出を抑制でき、充放電の効率が改善され長寿命化が確認されている。
2016年6月、産業技術総合研究所と筑波大学は、セパレーターに「イオンふるい」の機能を持つ複合金属有機構造体膜を用いて安定した充放電サイクル特性を実現している。多硫化イオンは通過させないサイズのミクロ孔を持つ金属有機構造体に酸化グラフェン層を混合して柔軟性を持たせている。
オーストラリアのMonash University(モナーシュ大学)では、正極の硫黄にグルコース添加剤を加えて硫化を防止し、少量のポリマー材料を加えて硫黄活物質間にスペースを設けている。LiSBの試作品により、従来の最大500回程度のサイクル寿命を、1000回まで長寿命化している。
2022年2月、米国Drexel University(ドレクセル大学)では、多孔質カーボンナノファイバー上に硫黄を担持させた集電体兼正極材を使用し、多硫化リチウムを経ずに硫化リチウムとすることに成功し、驚異の4000回の充放電サイクル寿命を発表したが、詳細は不明である。
また、OXIS Energyは、負極のリチウム表面にポリマーとセラミックの保護膜を設けることで金属リチウムの析出を防止し、サイクル寿命を約1.5倍に伸ばしている。また、金属リチウムの析出は電位で生じるため、比較的電位が高いケイ素系(Si、SiO)を負極に使うことも有効である。
全固体リチウム硫黄電池の仕組み
リチウム硫黄電池の電解液を固体電解質に置き換えたものが、全固体リチウム硫黄電池(All-solid-state Lithium-Sulfur Battery)である。液体電解質の課題(樹枝状組織形成、漏液、可燃性など)を固体電解質に置き換えることで軽減でき、エネルギー密度をさらに高くできる可能性がある。
全固体リチウム硫黄電池(全固体LiSB)には、硫化物系固体電解質が検討されたが、空気中で発火し易く、分解して硫化水素ガスを発生するために、電池製造時の取り扱いが困難であった。そこで、より安全な酸化物系固体電解質が検討されているが、エネルギー密度を高める必要がある。
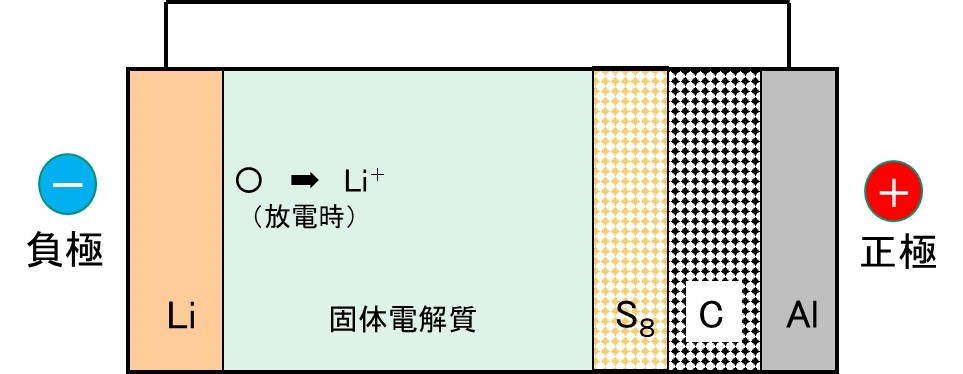
そのため、酸化物系固体電解質の実現に向け、正・負極材料の革新が進められており、注目を集めているのが金属リチウムを用いないLiSBである。ただし、正・負極材料の導電性が問題である。
2021年11月、産業技術総合研究所は酸化物系固体電解質(Li2O-LiIガラス)を複合化した正・負電極で全固体LiSBの室温作動に成功した。正極活物質に硫化リチウム(Li2S)、負極活物質にケイ素(Si)を用いた全固体LiSBを試作し、エネルギー密度:283Wh/kgを達成した。
しかし、硫化物系固体電解質(Li3PS4-LiI)を用いており、今後、酸化物系固体電解質のイオン伝導率改善および薄膜化を検討し、置き換えを進めるとしている。
以上のように、全固体LiSBは未だ研究の初期段階にあり、将来的に達成可能な最大エネルギー密度についても必ずしも明確ではない。全固体LiSBの実用化は早くても2030年以降との見方が強い。
メーカーと研究機関の動向
2021年11月、GSユアサは、LIBを超えるエネルギー密度:370Wh/kg以上のリチウム硫黄電池の開発に成功したと発表。硫黄を保持する微細な穴を持つ炭素粒子を開発して、炭素を介して電気を流れやすくするほか、硫黄が電解液に溶けにくくした。2023年には500Wh/kgを目指す。
リチウム硫黄電池は関西大学と共同で開発し、電動航空機への搭載を目指しており、2030年には1000Wh/kgの達成を目標に要素技術研究を進めている。
2022年2月、ADEKAは、LIBの約2倍のエネルギー密度のLiSBを実現したと発表。正極活物質として、硫黄変性ポリアクリロニトリル(SPAN)というSを含む有機分子重合体を用いる。SPANは2009年に産業技術総合研究所と豊田自動織機が製造方法を確立した硫黄系繊維材料である。
2030年をめどに電極材販売の事業化を目指し、2021年にはエネルギー密度:500Wh/kgのLiSBを試作。2022年11月に、重量エネルギー密度が100Wh/kgなら5000サイクル以上、450Wh/kgでも200サイクル以上充放電サイクルを上回る。
2022年9月、関西大学・旭化成・東亜合成は、リチウム硫黄電池向けの正極材料を開発した。旭化成は炭素材料にあけた細かい穴に硫黄を閉じ込め、硫黄が電解液に溶け出すのを防いで耐久性を高めた。
東亜合成は急速充放電の実現につながるバインダー(接着剤)を開発した。今後、製造技術などを改良し実用化を目指すとしている。
2022年11月、英国のOXIS Energy(オックスフォードシャイア)が生産拠点をブラジルと英国に建設する計画を進めていたが、残念ながら2021年に破綻したことが報じられた。
一方で、オーストラリアのBrighsun New Energy(ブライスン・ニュー・エナジー)やノルウェーのMorrow Batteries(モロー・バッテリーズ)などが商業化を目指していることも報じられた。
現状、LiSBの商業化に取り組む企業は複数社あるが、特に積極的なのがブライスンである。同社はリン酸鉄リチウム正極材LiBを製造し、自社のEVバスなどに搭載しているが、併行してLiSB(ブランド名「2U Battery」)の商業化に向けて実証試験を行っている。
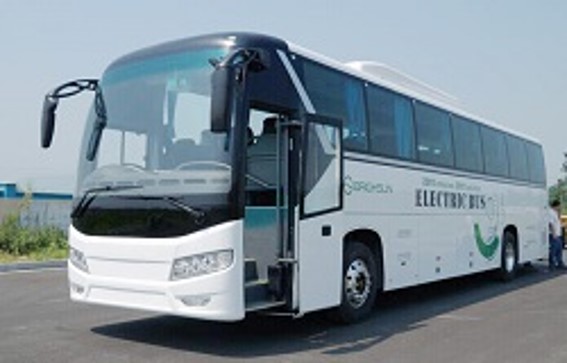
ブライストンは独自技術によりLiSBのサイクル寿命を改善し、エネルギー密度もLIBよりも大幅に高く、EVの航続距離:2000kmを実現するとしている。また、オーストラリア産の硫黄を有効活用し、量産時のコストを100豪ドル(約64ドル)/kWhと現行LIBの半分程度に抑えている。
一方、モローは、ノルウェー南部のアグデルに42GWh/年のLIB工場を2023年に着工し、2024年末から稼働させる計画を進めている。低コストの蓄電池を開発・製造・販売していくことを目指し、将来的にはLiSBも手がけるとしている。
2023年5月、ドイツ・フラウンホーファー研究機構は硫黄を正極材に使う全固体電池の開発プロジェクトを立ち上げたことを発表。現在主流のLIBに比べてエネルギー密度を高め、EVなどへの応用を目指している。
2023年5月、欧州Stellantis(ステランティス)は、Stellantis Ventures(ステランティス・ベンチャーズ)が、EV向け電池を開発中の米国Lyten(ライテン)に出資したと発表。ライテンは独自技術の「3D グラフェン」を使ったLiSB「LytCell EV」の事業化を進める。
リチウム硫黄電池の課題
リチウム硫黄電池(LiSB)は、現在主流となっているリチウムイオン電池(LIB)に置き換わるであろうか? 結論はNOである。すなわち、現時点ではエネルギー密度と充放電サイクル特性のいずれも、全固体LIBを凌駕する特性が得られていない。
LiSBの理論エネルギー密度は2500Wh/kgで、LIB(150~270Wh/kg)に比べて極めて高いといわれてきたが、現状は400~500Wh/kgに留まり、全固体LIBと同等である。今後、開発が進みエネルギー密度向上の見通しが明らかとなれば、ポスト・全固体リチウムイオン電池に位置付けられる。
LiSBの実用化に関しては、2022年11月、英国OXISエナジーが生産拠点をブラジルと英国に建設する計画を進めていたが、2021年に破綻したことが大きな痛手である。
2020年1月には、容量20Ah、エネルギー密度:471Wh/kgのセルを発表し、500万セル/年、合計で220MWh/年以上の生産能力を持つLiSB製造プラントに関し、2023年稼働を目指してブラジルに建設中で、英国ウェールズ地方で電解液と負極の製造プラントを建設している途中であった。
また、全固体リチウム硫黄電池は、液体電解質の課題(樹脂状組織形成、漏液、可燃性など)を固体電解質に置き換えることで軽減でき、エネルギー密度をさらに高くできる可能性がある。しかし、研究は未だ初期段階にあり、全固体LiSBの実用化は早くても2030年以降との見方が強い。
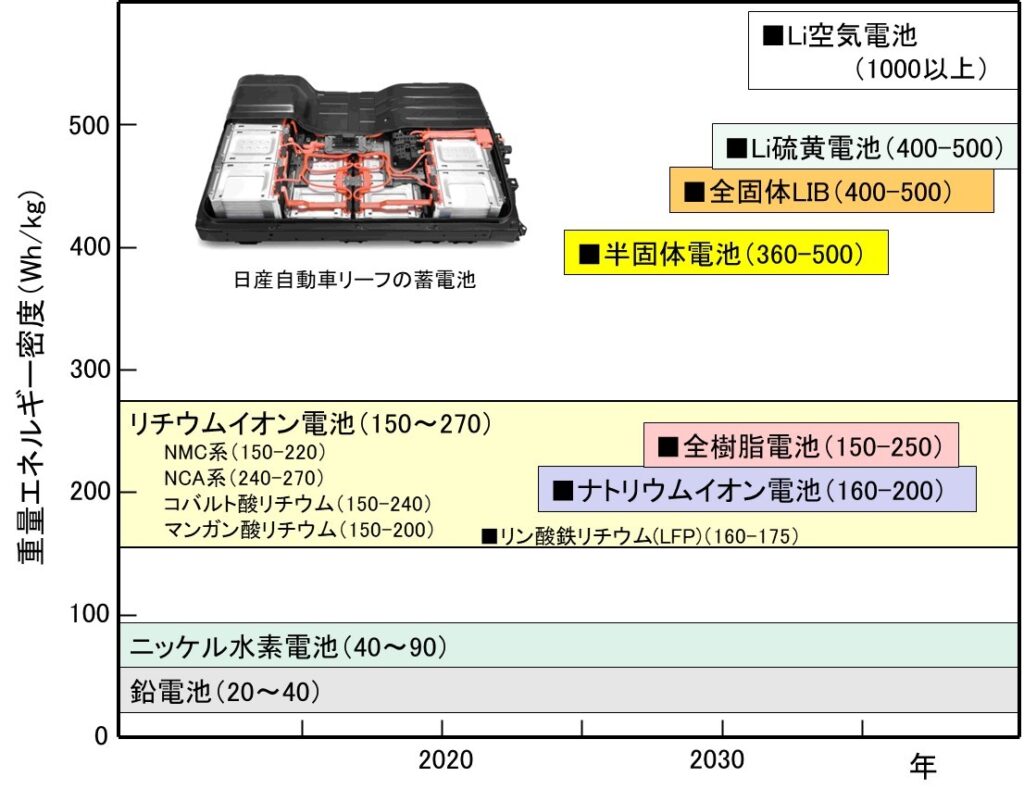
リチウム空気電池の開発動向
リチウム空気電池の仕組み
リチウム空気電池(LAB:Lithium Air Battery)は、正極に空気中から取り込んだ酸素、負極に金属リチウム、電解質として非水系の有機電解質溶液、セパレーターには微多孔フィルムが主に用いられて研究開発が進められている。
LABでは、放電時にリチウムが負極から溶け出し、正極で酸素と反応して超酸化リチウム(LiO2)、あるいは過酸化リチウム(Li2O2)が生成される。充電時は逆に、超酸化リチウム、あるいは過酸化リチウムが分解して酸素を放出し、負極表面でリチウムに戻る。
従来のリチウムイオン電池(150~270Wh/kg)に比べてエネルギー密度が1000Wh/kg以上と非常に高いことが特徴で、原材料の調達リスクやコスト面でも優位とされている。しかし、LABは研究開発段階にあり、実用化までには負極活物質の劣化や液漏れ対策など多くの課題が残されている。
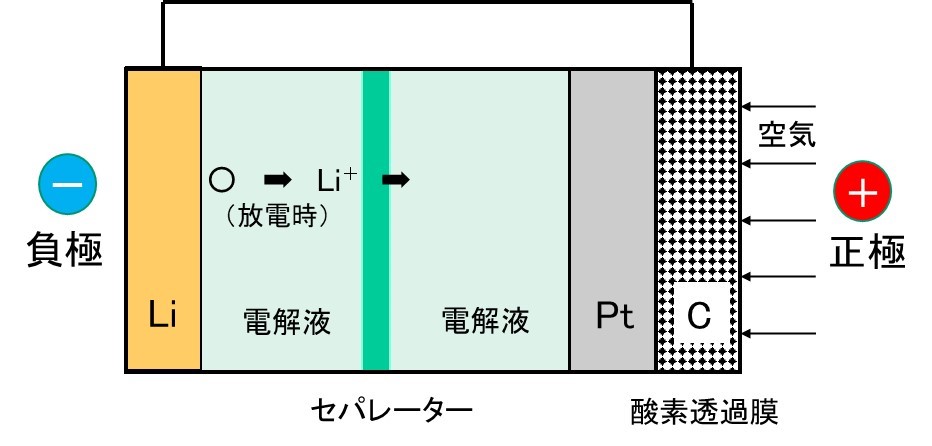
LABの最大の課題は、充放電を繰り返すと正極側と負極側の異なる電解液が混合したり、充電中にリチウムイオンが負極表面に樹枝状組織(デンドライト)として析出・成長し、短絡を生じることである。そのため、セパレーターや負極の耐性を高め、サイクル寿命向上を目指す研究が行われている。
一方、LABは空気中の酸素を正極材料として利用するため、空気中の湿度や汚れが電池性能に悪影響を及ぼす。そのため、活性が落ちにくい貴金属触媒(Pt)を利用したり、フィルターを使って空気中の不純物を取り除くなどの工夫が行われている。
全固体リチウム空気電池の仕組み
リチウム空気電池の電解液を固体電解質に置き換えたものが、全固体リチウム空気電池(All-solid-state Lithium Air Battery)である。液体電解質の課題(樹枝状組織形成、液漏れ、可燃性など)を固体電解質に置き換えることで軽減でき、エネルギー密度をさらに高くできる可能性がある。
全固体リチウム空気電池(全固体LAB)には、酸化物系電解電解質や固体ポリマー電解質が検討されており、従来のLIBと比較して液漏れの心配がなく、安全性にも優れている。しかし、全固体LABも研究開発段階にあり、実用化までには負極活物質の劣化対策によるサイクル寿命の延伸が必須である。
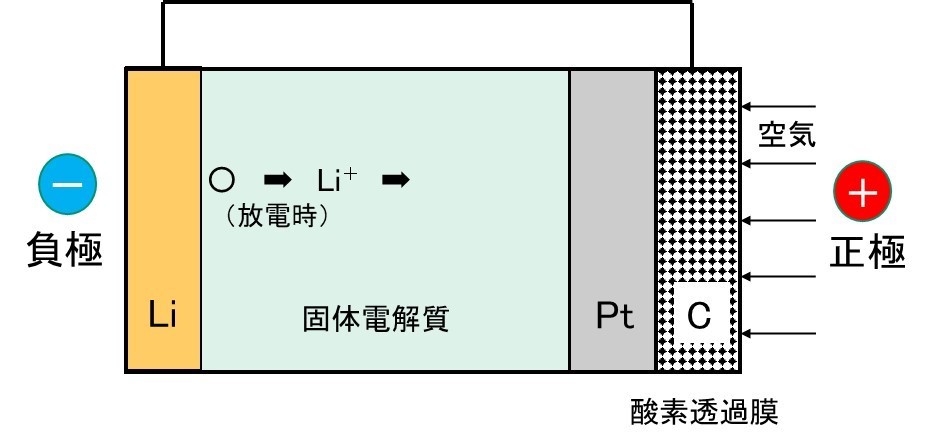
メーカー・研究機関の動向
2020年12月、イオン導電性ポリマーに強みを有するベルギーのSolvay(ソルヴェイ)は、リチウム空気電池の実用化に向けて中国EVメーカーであるGAC Groupと提携し、共同開発を発表した。
2021年6月、ソルヴェイは、LABの研究開発で三菱ケミカルと協力することを発表した。三菱ケミカルはLABの材料開発に向け、量子コンピューターでの基礎研究に取り組んでいる。
2021年12月、物質・材料研究機構 (NIMS) とソフトバンクは、エネルギー密度:500Wh/kg級リチウム空気電池を開発し、室温での充放電反応を確認した。負極に金属リチウム、セパレーターを挟んで正極に多孔質カーボンを使用した。サイクル寿命は明らかにしていない。
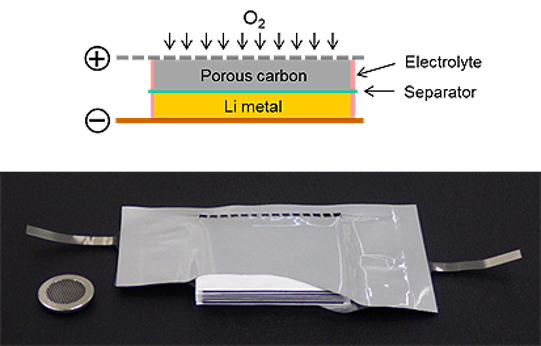
出典:NIMS
2022年5月、東レは、リチウム空気電池用の無孔イオン伝導ポリマー膜の開発に成功したと発表。セパレータに適用することで、充放電サイクル試験において、従来の微多孔フィルムに比べて10倍以上のサイクル寿命を確認している。
リチウムイオンがホッピングで通過可能な新規ポリマーを設計し、リチウム塩を複合化することで3×10-5S/cmと高いイオン伝導性を実現した。ポリマー膜は無孔であるため、異なる電解液の分離性に優れ、リチウムの樹枝状組織の析出・成長の抑制が原理的に可能としている。
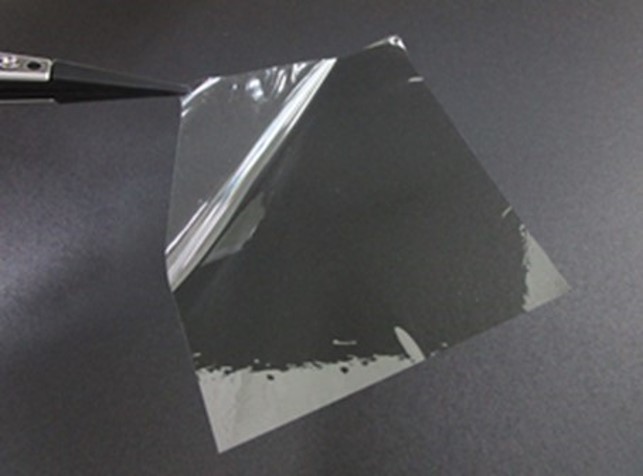
2023年2月、NIMS・ソフトバンク・オハラは、酸化物型固体電解質のシート(厚さ:6μm)をLABの正極と負極間に挟み、負極のリチウムを保護して寿命を2倍に延ばした。正極で電解液などと反応して生じた水やCO2が、負極側に移動して負極が劣化するのを固体電解質で防止した。
NIMSはエネルギー密度:500Wh/kgのLABを開発していたが、10回ほどの充放電で容量が8割以下に低下した。保護シートを電極間に挟んだ電池(400Wh/kg)では、負極の劣化が抑えられて20回以上の充放電を繰り返した後でも容量を8割ほど維持できた。
2023年2月、米国イリノイ工科大学・アルゴンヌ国立研究所は、LIBに比べて4倍高いエネルギー密度(1200Wh/kg)の全固体LABを開発したと発表。(「Science」誌に掲載)
リチウム化合物のナノ粒子をポリマーに埋め込んだ複合材料の固体ポリマー電解質を開発し、試験セルでは1000サイクルの充放電に対する安定性を実証した。
2023年5月、山梨大学・早稲田大学は、負極活物質に水素イオンを可逆的に取り込む酸化還元活性な有機化合物を用い、水素イオン伝導性の高分子電解質薄膜を組み合わせ、繰り返し充放電可能な全固体LABを開発した。(ドイツ化学会「Angewandte Chemie International Edition」に掲載)
負極活物質は有機レドックス化合物ジヒドロキシベンゾキノン(およびその重合体)、電解質は高分子薄膜(ナフィオン)、正極は白金触媒を含むガス拡散電極(活物質は酸素)を組み合わせ、全固体LABの原理実証に成功。電解質膜との界面はカーボン粉末とナフィオンを混合した負極構造を採用した。
リチウム空気電池と全固体LABの課題
リチウム空気電池は研究開発段階にあり、実用化には多くの課題が残されている。主な課題は、負極であるリチウムのデンドライトの析出・成長の防止と、正極である空気極側に供給される空気の影響である。加えて、車載用電池としては急速充放電性能や利用温度範囲などを検証する必要がある。
最近になって、国内外の研究機関から全固体リチウム空気電池に関する新たな報告が相次いでおり、リチウム空気電池を通り越して全固体リチウム空気電池の可能性も出てきている。今後、実用化に向けて企業の動きが加速される可能性は高い。
しかし、研究開発状況を見る限り、実用化は早くても2030年以降と見られている。
ポスト・リチウムイオン電池のまとめ
ナトリウムイオン電池(NIB)
ナトリウムイオン電池(NIB)が、現在主流となっているリチウムイオン電池(LIB)に置き換わる可能性はある。ただし、定置式蓄電池や格安BEV向けなど、LIB市場の部分的なNIBへの置き換えであり、ポスト・リチウムイオン電池の本命とはいえない。
その理由は、NIBのエネルギー密度が160~200Wh/kgと、LIB(150~270Wh/kg)やLFP系LIB(160~175Wh/kg)と同等な点にある。自動車メーカーにとって、既に完成しているLIBのサプライチェーンを、NIB向けに再構築するモチベーションとはならない。
全固体ナトリウムイオン電池も、エネルギー密度の大幅向上が示されない限り同様である。
全固体リチウムイオン電池(全固体LIB)
ポスト・リチウムイオン電池本命とされている全固体リチウムイオン電池は、現時点でもエネルギー密度:400~500Wh/kgと高く、液漏れや発火の危険性も極めて低い。また、超急速充電(10分以下)性能や、寒冷地での性能劣化防止などの開発が進められている。
現状の全固体LIBの生産コストは、LIBの4倍ともいわれている。今後、量産効果により低コスト化が進めば、一挙に全固体LIBへの転換が進む可能性が高い。課題は、量産に至るまでの過渡期の製品である。「全固体LIBでないと成立しない魅力ある製品とは何か?」を模索する必要がある。
リチウム硫黄電池(LiSB)と全固体LiSB
リチウム硫黄電池(LiSB)と全固体LiSBは、現在主流のLIBに置き換わることはない。現時点ではエネルギー密度と充放電サイクル特性のいずれも、全固体LIBを凌駕する特性が得られていない。未だ研究開発段階にあり、車載用の実用化は早くても2030年以降との見方が強い。
LiSBの理論エネルギー密度は2500Wh/kgで、LIB(150~270Wh/kg)に比べて極めて高いといわれてきたが、現状は400~500Wh/kgに留まり、全固体LIBと同等である。今後、開発が進みエネルギー密度向上の見通しが明らかとなれば、ポスト・全固体リチウムイオン電池に位置付けられる。
リチウム空気電池(LAB)と全固体LAB
リチウム空気電池は研究開発の初期段階にあり、実用化には多くの課題が残されている。最近、国内外の研究機関から全固体リチウム空気電池に関する新たな報告が相次いでおり、リチウム空気電池を通り越して全固体リチウム空気電池の可能性も出てきている。
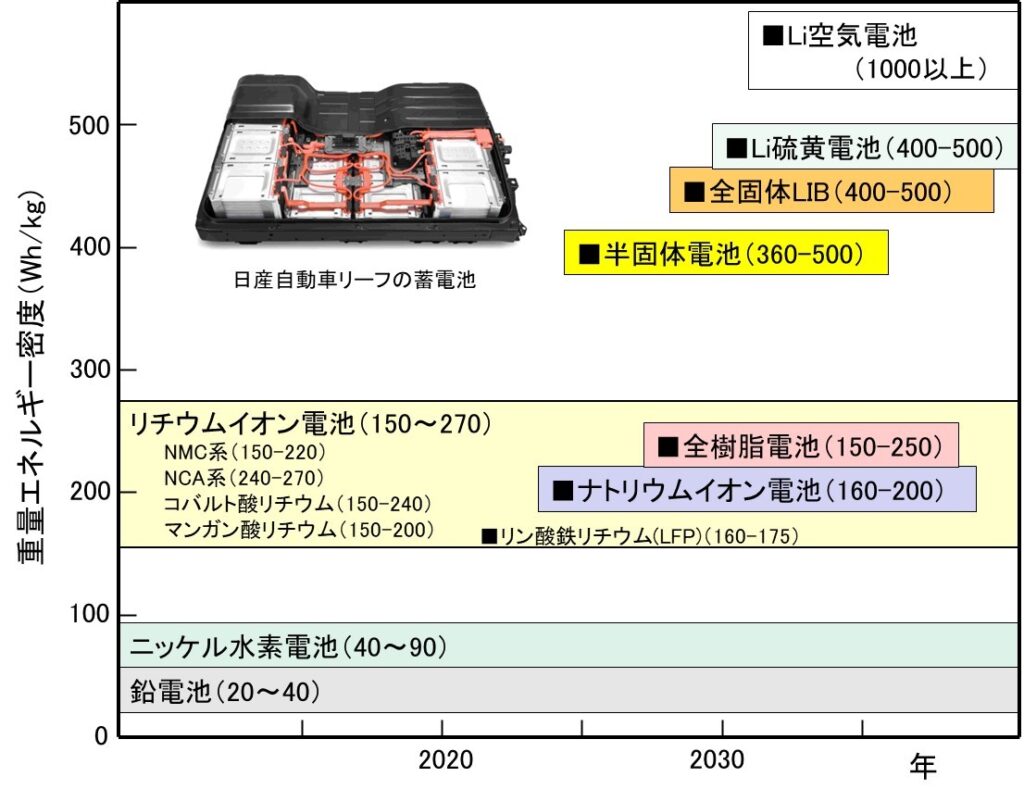
使用済み蓄電池のリユース
欧州の蓄電池リユース
2016年5月、米国の電力管理業Eatonと欧州日産自動車(Nissan Design Europe)は、共同開発した家庭用蓄電池「xStorage」(容量:4.2kWh)の欧州販売を発表した。設置を含めた価格は3200ポンドで一般的な家庭用蓄電池と比べて大幅に安く、「リーフ」などの使用済みEV蓄電池を活用している。
2016年6月、BMWも家庭用蓄電池(容量:21.8kWh、33kWh)の概念を発表し、「i3モデル」や「MINI E」と同じ蓄電池パックを採用する。蓄電池共通化の利点は、開発費の抑制とEVの使用済み蓄電池を再利用できる。家庭用蓄電池の設置時には、新品と再利用品のいずれかを顧客が選択できる。
2016年9月、ドイツのBMW、ボッシュ、スウェーデン・バッテンフォールの共同事業体は、100台超のEV用蓄電池を再利用した蓄電システム(容量:2800kWh、出力:2000kW)を設置した。
2016年9月、ドイツのダイムラー、Mobility House、GETECの合弁会社は、ドイツ西部リューネンにEVの使用済み蓄電池を再利用した大規模蓄電システム(容量:12.8MWh)を稼働させた。ダイムラーは2017年にハノーバーで、同様の定置用蓄電システム(蓄電容量:17.4 MWh)の運用を開始した。
2018年6月には、ダイムラーはドイツ西部エルフェリングセンにEVの使用済み蓄電池を利用した蓄電池システム(容量:9。8MWh)を稼働し、電力調整用に使用している。
2017年3月、スウェーデンの電力会社バッテンファルは、BMWのEVの使用済み蓄電池を再利用した大規模蓄電システム(容量:22MWh)を英国の風力発電所(出力:230MW)に併設し、負荷変動抑制を行っている。
日本の蓄電池リユース
2018年1月、中部電力とトヨタ自動車が、EVの使用済み蓄電池を再利用した大容量蓄電システムの構築とリサイクルの実証で合意した。トヨタ自動車がEVから回収した蓄電池を、中部電力が再生可能エネルギー導入の拡大に伴う需給調整や、周波数変動および配電系統の電圧変動への対応などに活用する。
2020年には蓄電システム(出力:約10MW(蓄電池1万台相当))の導入を目指す。リユース蓄電池は、HVに使用されているニッケル水素電池と、EVやPHVで使用されるリチウムイオン電池を使う。使用済み蓄電池からレアメタル(希少金属)を取り出し、電池原料とするリサイクルも検討する。
2018年3月、日産自動車と住友商事の合弁会社フォーアールエナジー(4R)が、福島県浪江町にEVの使用済み蓄電池の再利用拠点工場(旧型リーフで2250台/年の電池処理能力)を開所している。
2021年から本格的な中古電池回収(約5000パック/年)始まる。リーフには48個のモジュールを1パックにして搭載しており、各モジュールの劣化度合いは異なる。そのため4Rでは1モジュールを5分で解析し、1パックを解析するのに4時間を要する。
容量が80%を超えるモジュールは、リーフ向け交換用電池として日産自動車に販売する。80%以下のモジュールは、4Rが開発したシミュレーション技術で顧客の利用条件に合わせて寿命予測などを行い、電動フォークリフト、ゴルフカート、街灯向けなどの蓄電池として販売する。
2018年4月、日本ベネックス、住友商事、富士電機は、リーフ24台分の使用済み蓄電池を20フィートコンテナに格納した蓄電システムを共同開発し、日本ベネックス本社工場で1号機(容量:400kWh、出力:400kW)が稼働した。富士電機は同システムの商品化計画を発表している。
2018年9月、エネチェンジはバッテリーマネジメントシステム(BMS)技術を有する英国ブリルパワー(BrillPower)と事業提携契約を締結した。各セルの充電率や劣化度を監視しながら均一放電する制御技術により、使用済み蓄電池の寿命を最大60%伸ばし、充電容量を最大46%増加させることできる。
2020年12月に発売した2人乗り超小型EV「C+pod(シーポッド」に搭載する蓄電池の規格化(容量:9.06kWh )をトヨタ自動車が発表した。出力、容量、耐久性能などの下限を定めて高性能蓄電池との入れ替えを容易にし、数年単位のリース形式でBEVを販売し、電池回収して劣化状況を検査する。
C+podに搭載する蓄電池を家庭用蓄電池と同等の容量とし、電池回収して劣化が進んでいれば家庭蓄電池としてパナソニックに販売する。また、送配電網向けの大規模蓄電システムとして、中部電力などの電力会社への販売も想定している。
2021年12月、日産自動車は2022年欧州、2025年米国に車載用蓄電池のリサイクル工場を1カ所ずつ新設すると発表した。住友商事と共同出資する子会社のフォーアールエナジーと、蓄電池のリユース/リサイクルを行う。電池の劣化度合いに応じて、EVの交換用電池や工場設備の非常電源などに組み直す。
2022年9月、大阪ガスは蓄電池制御技術を持つNExT-e Solutionsと資本業務提携し、EVの使用済み蓄電池を活用した系統用蓄電池の事業化を発表した。2023年3月から、EVとフォークリフトから回収した使用済み蓄電池と新品蓄電池を用い、劣化状況が異なる蓄電池の組み合わせで検証試験を実施する。
2022年10月、ダイヘンはEVの使用済み蓄電池を再利用し、パワーコンディショナー(PCS)を一体化した自家消費型太陽光発電向け「リユースバッテリーパッケージ」の販売を開始した。フォーアールエナジーから日産自動車「リーフ」の使用済み蓄電池の提供を受け、導入コストを約30%低減する
2022年10月、JERAとトヨタ自動車は、中古の電動車用バッテリーを活用した蓄電システムのコストを大幅に抑える技術を開発したと発表した。トヨタ自動車が開発した大容量スイープ蓄電システム(容量:1260kWh)は四日市火力発電所内で稼働しており、2022年度内に送電網に接続する。
中古バッテリーを使う蓄電システムは、各バッテリー性能に差があると全体の性能が低下するが、開発システムは、異なる種類や性能の電池が交ざった状態でも高い性能を出せ、出力を変換するコンバーターや電力の質を整えるパワーコンディショナーも不要となり、大幅にコストを低減できる。
2023年1月、関西電力と東京センチュリーは、リース後のEVなどで使った使用済み蓄電池の回収・リユースに向けて業務提携した。電力需給の安定につながる系統用蓄電池などとして活用する検討を進め、2025年度をめどに全国で事業展開する。
2023年10月、本田技研工業と三菱商事は、新事業創出に向けた覚書を締結した。電池のライフタイムマネジメントは、2024年春に発売予定の軽商用タイプBEV「N-VAN e:」を対象に、電池のモニタリング機能を高度化することで、車載用から定置用へ転用し、その後のリサイクルまで想定する。
電力需給に合わせてEVの充電タイミングを自動制御するスマート充電や、最良のタイミングで電力網とBEVへの充放電を自動で行うV2G(Vehicle to Grid)サービス、グリーン電力の提供などのエネルギーマネジメントシステムについても事業化を検討・協議する。
蓄電池リユースに関する政府の動き
2015年の自動車リサイクル法審議会合同WGで、LIBの適正処理のセーフティネット構築の必要性が示された。これを受けて日本自動車工業会は回収・リサイクルの仕組み構築を支援すべく、自動車再資源化協力機構を窓口に無償回収システムを構築し、2018年10月より運用を開始した。
2019年7月、企業、自治体、政府などの連携・情報共有により、電動車普及上の課題解決に向けた検討を深めていく場として、経済産業省主導で「電動車活用社会推進協議会」が立ち上げられ、車載用電池のリユースを促進するため、協議会の下に「車載用電池リユース促進WG」が設置された。
さらに、2020年6月、EVの使用済み蓄電池のリユースに不可欠となる残存性能を評価するための「電池性能見える化ガイドライン」が策定された。それに伴い使用済み蓄電池を再利用する市場を整備する検討が行われている。
使用済み蓄電池のリサイクル
既存鉱山からのリチウムイオン電池の原料供給量が、2024年以降では不足するとの試算がBASCで示されている。この不足分を補うのが、B2B(Battery to Battery)リサイクルの概念である。
2017年12月、米国は大統領令で希少金属の確保を指示し、コバルトなど35種類を重要鉱物に指定してリサイクルや資源発掘を進める方針を示した。2019年2月、米国DOEの予算でリサイクル研究拠点をイリノイ州に新設し、使用済みリチウムイオン電池から希少金属を取り出す技術開発を加速している。
一方、欧州連合(EU)の行政執行機関である欧州委員会は、車載用蓄電池に関して新たな「電池規則」の導入を進めている。蓄電池のライフサイクルでみたCO2排出量の削減を求めており、今後、低炭素・低コストに加えてリサイクルが容易なグリーン電池の開発が求められる。
そのため、再生可能エネルギーの導入で先行する欧州域内で蓄電池を製造することが有利になる。地球温暖化への対策と同時に、BEVの心臓部である蓄電池関連のEU内産業を保護・強化する狙いである。
2020年12月、欧州委員会が示した蓄電池規制案は、LIBに使う希少金属のリサイクル比率を2030年までにコバルトは12%、リチウムとニッケルはそれぞれ4%とした。2024年7月以降、蓄電池の「カーボンフットプリント」(CO2総排出量)の提示なしで、EU域内での蓄電池やBEV販売が不可となる。
CO2排出量が一定量以上の蓄電池の流通を制限するため、鉱石を採掘・精鉱する段階から蓄電池の製造工程を見直し、使用済み蓄電池のリサイクル技術も抜本的に変え、正極材料の生産とリサイクル時のCO2排出量をそれぞれ従来比で5割減らし、2030年には業界全体で8割減を目指している。
欧米での蓄電池リサイクル
既に、欧米では多くの金属リサイクル企業が使用済み蓄電池のリサイクル事業を進めている。
欧州では、ベルギーのホーボーケンにある素材メーカーUmicore(ユミコア)が、世界最大級のリチウムイオン電池、ニッケル水素電池の専用リサイクル施設(処理量:7000トン/年、EV蓄電池:約3万5000個相当)を保有し、売上高の約20%をリサイクル事業が占めている。
ユミコアでは、乾式精錬と湿式精錬を組み合わせて、コバルト、ニッケル、銅の抽出と合わせて、スラグからリチウムとレアメタル(稀少金属)を回収している。
2020年6月、スウェーデンLIB製造のNorthvolt(ノースボルト)とアルミニウム製造のHydro(ハイドロ)が、車載用LIBをリサイクルするための合弁会社を設立した。ノルウェーにパイロット工場を立ち上げ、回収された使用済みLIBの破砕と分別を行い、電極材料とアルミニウムを回収する。
2022年には、スウェーデンの工場敷地内に量産規模(処理量:8000トン/年、EV蓄電池:2万台以上)のリサイクル施設を設置する計画である。
ドイツのフォルクスワーゲンはLIBリサイクルの自社技術構築を目指して、Salzgitter工場のパイロットライン(処理量:1200トン/年)を2020年内に稼働する。長期的には各拠点に大規模設備を分散設置し、自社のリサイクルによりEVが搭載するLIBの97%の原料回収を目指すとしている。
米国Retriev Technologies(リトリーブ・テクノロジーズ)は、2002年からカナダのブリティッシュコロンビア州トレイル工場(処理量::1200トン/年)でLIBリサイクルを行っており、コバルト、ニッケル、銅を回収している。2015年には米国のオハイオ工場を拡張している。
2021年2月、丸紅とリトリーブ・テクノロジーズは、LIBのリサイクルに関する事業開発に係わる戦略的パートナーシップ契約を締結した。廃電池からコバルトやニッケルを精製し、電池材料分野向けに活用する事業を共同で開発する。
2022年1月、テスラ・モーターズの米国ネバダ州スパークスのギガファクトリーで、パナソニックからスクラップや使用済み蓄電池を回収しているRedwood Materials(レッドウッド・マテリアルズ)が、パナソニックに正極用銅箔の供給を2022年に開始すると発表した。
ネバダ州カーソンが拠点のレッドウッド・マテリアルズは、35億ドルを投じてギガファクトリー近くの新工場で2024年に負極材料、2025年までに正極材料の生産を開始し、100GWh/年の蓄電池製造に必要な量を生産し、原材料供給のみならず蓄電池の再生産も目指している。
提携先はパナソニックの他に、フォード・モーター、フォルクスワーゲン、アウディ、トヨタ自動車、ボルボ、プロテラなどが相次いで発表している。
2021年9月、フォード・モーターと韓国のSKイノベーションはテネシー州とケンタッキー州で2025年稼働に向けて電池工場を計画しており、同工場で使用済みLIBをリサイクルする仕組みをレッドウッドマテリアルズと立ち上げることを発表している。
カナダ・ケベック州のLithion Recycling(リチオン・リサイクリング)も、使用済みLIBからレアメタルなどを約95%回収できる技術を保有し、EV用蓄電池を200トン/年処理できる試験プラントを持つが、2022年中にも処理能力を7500トン/年に増強して商業運転に移行すると発表している。
また、カナダではAmerican Manganese (アメリカン・マンガネーゼ)が、本来は低品質マンガン鉱を処理するために開発された技術を活用して、使用済み蓄電池に含まれるリチウムの他、コバルト、ニッケル、マンガン、そしてアルミニウムも100%の回収を目指している。
中国・韓国における蓄電池リサイクル
中国には20社以上、韓国には少なくとも6社のリサイクル処理業者が存在する。国外からの使用済み電池の調達を含めて、2018年に中国で6.7万トン、韓国で1.8万トンが処理され、世界のリサイクル可能な電池在庫の88%に相当する。韓国で再生処理された正極材料のほぼ全量は中国で製品化されている。
中国の大手LIBリサイクル企業は格林美(GEM)、湖南邦普循環科技(Hunan Brunp Recycling Technology)、Huayou Cobalt New Material、Highpower Technology、Guanghua Guanghua Sci-Techの5社が知られている。
2015年、中国車載電池最大手の寧徳時代新能源科技(CATL)は、湖南邦普循環科技を傘下に収め、2018年に3万トンの使用済み蓄電池をリサイクル処理している。その湖南邦普循環科技は第二工場(8.5万トン/年)の増設計画を公表した。
2021年10月、CATLは使用済み蓄電池のリサイクル工場を国内で新設すると発表した。総投資額は最大320億元で、自社向けにリン酸鉄リチウムなどの原料を回収し再利用できるようにする。
2020年4月には、GEMと韓国EcoProが合弁会社を設立し、中国CATLの拠点である寧徳に4.8万トン/年のリサイクル工場の設立を発表した。
2024年4月、寧徳時代新能源科技(CATL)は、スウェーデンのボルボ・カーズと、持続可能な発展に関する協力を深めるための戦略的協力に関する覚書を締結した。
ボルボが使用済み・廃蓄電池を回収し、川下のサプライヤーでニッケル、コバルト、リチウムなどの金属材料を抽出する。CATLは得られた再生材を利用して新しい蓄電池を生産し、ボルボの新車に搭載する。
日本における蓄電池リサイクル
2015年から、本田技研工業はLIBリサイクルの処理費低減を目指し、高付加価値なニッケル水素電池や水素貯蔵設備などに活用する資源ダイレクトリサイクルを検討している。松田産業や日本重化学工業などと共同で、回収された正極材(Ni、Co)の水素吸蔵合金の基本性能を確認している。
その後、2018年10月から日本自動車工業会に各自動車メーカーが参画し、EVに搭載されているLIBの共同回収を開始している。
しかし、LIB共同回収システムにより回収されたEV電池は、2020年度はわずか3648台分であり、同年度のEV国内販売台数は約1万4000台であり、回収率は26%程度に留まっている。今後、リサイクル処理能力を高めると共に、使用済み蓄電池を回収する仕組みの整備が急務である。
2019年4月、住友金属鉱山は使用済み蓄電池を砕いた電池粉を加熱し、乾式精錬により不純物を一括して分離した後、ニッケル、コバルト、銅を合金として選択的に回収する。その後に湿式精錬で合金を溶解・精製してニッケル、コバルト、銅を単離する技術を構築している。
2010年からEV車載蓄電池のリユース・リサイクル事業に取り組んできたトヨタ自動車は、2019年7月に、中国CATLと新エネルギー車(NEV)向け蓄電池で包括提携した。蓄電池の供給だけでなく、新技術の開発やリユース・リサイクルなど幅広い分野での検討を始めている。
2020年から、JX金属は日立市の事業所で車載用LIBを熱処理で無害化して電池粉を生成し、ニッケルとコバルトを硫酸で浸出後、溶媒抽出技術により硫酸コバルトと硫酸ニッケルを抽出する湿式精錬を進めてきた。2022年にも正極材料向けに硫酸コバルトの生産、高純度リチウムの回収を開始する。
2021年6月、DOWAホールディングスは秋田県大館市のグループ会社(エコシステム秋田)の焼却施設で、大型車載用LIBを解体せずに不活性化する前工程を採用し、再資源化ラインで鉄、アルミニウム、銅、コバルト・ニッケル混合物、リチウムなどに分離回収し、2024年の事業化を公表した。
2022年11月、子会社のDOWAエコシステムでブラックマスの製造をしているが、秋田大学との共同研究結果としてブラックマスから正極材の製造に成功したと発表している。
2021年8月には、車載用LIBのリサイクル事業・電池材料事業を推進するため、新会社「JX Metals Circular Solutions Europe」(JXCSE)をドイツ・フランクフルトに設立した。また、2022年6月にはドイツでVWなどのコンソーシアムに参画し、LIBリサイクルに向けた実証実験を開始した。
2021年12月、日産自動車は2022年度に欧州、2025年度に米国に車載用蓄電池のリサイクル工場を新設すると発表した。住友商事と共同出資する子会社のフォーアールエナジーと蓄電池のリユース/リサイクルを行うのが狙いである。
2022年1月、住友金属鉱山は関東電化工業の湿式精錬法を用いて LIB用電解液に再利用可能な高純度リチウム化合物を取り出す技術を確立した。2021年10月から、実用化に向けて重量トンレベルでの技術開発や実証試験を開始する。2024年度にもコバルトを含めたリサイクルを事業化する。
2022年12月、三菱マテリアルが金属リサイクル業のエンビプロ・ホールディングスと組み、LIBリサイクルへの参入を発表した。ブラックマスから薬品などを用いてレアメタルを取り出す「湿式精錬」の技術を共同開発し、2025年からの本格参入、2030年度をめどに処理能力は6000トン/年に高める。
2024年9月、三菱ふそうトラック・バスは2025年始めに川崎製作所に実証プラントを建設し、シンガポールのスタートアップTrue 2 Materials (T2M)と共同で、EV使用済み電池から正負極材などの材料を回収する実証実験を開始する。小型EVトラック「eCanter(eキャンター)」や、他社のEVから回収した使用済み電池を使う。
電池への再利用が可能な品質が確保できれば、回収した材料を電池メーカーに販売する計画で、日本における事業化をめざす。
LIBリサイクル技術の進化
この数年でLIBリサイクル技術は急速に進化している。従来はLIBを破砕して正負極材料が混合した電池粉(ブラックマス)を1300~1500℃の炉で溶融し、還元されやすい金属元素から順に還元して分離する「乾式精錬」が主流であった。しかし、工程でのCO2排出量が多く、高精度分離が困難である。
一方、低温(100℃以下)で硫酸、塩酸、硝酸などによりブラックマスから所定の金属イオンを浸出し、化学的な処理を加えて各金属を硫酸塩などの形で単離する「湿式精錬」も良く知られたリサイクル技術であった。しかし、工程が複雑で強酸を使うため腐食・廃液処理などに問題がある。
ベルギーのユミコアなどは、乾式精錬と湿式製錬を組み合わせ使用した。最近では、クエン酸、コハク酸、アスパラギン酸、乳酸、酢酸、リンゴ酸などの扱いやすい有機酸を使うことで、低コスト化でCO2排出量の少ない分離技術が開発され、現在では湿式製錬が主流となっている。
さらに、次世代に向けて湿式製錬の中でも注目されているのが、米国Ascend Elements(アセンドエレメント)が開発したHydro-to-Cathode技術である。ブラックマスから金属を単離せず、正極活物質であるNi-Mn-Co(NMC)を直接製造する「ダイレクトリサイクル」である。
今後、蓄電池リサイクルが進む場合に大きな問題となるのが不純物(忌避物質)対策であろう、また蓄電池は進歩を続けているため、B2Bリサイクルがどこまで可能かの見極めも必要である。そのため蓄電池のリサイクルには、トレーサビリティとモニタリングシステムが不可欠となる。
Hydro-to-Cathode法は、ブラックマスから黒鉛などの炭素材料をろ過などで除去し、その後に酸で浸出して銅、鉄、アルミニウムなどの不純物を除去し、さらに水酸化ナトリウムを加えてpHをアルカリ性にして残留アルミニウムなどの不純物を除去する。残った材料には所定の正極材料(NMC組成)になるよう、ニッケル、マンガン、コバルトの硫酸塩を添加し、炭酸リチウム(Li2CO3)を加えた後、450℃×9時間、次に900℃×14時間の焼成を行う。これにより直径約10nmのNMC粒子を製造することができる。
日経X手ch、https://xtech.nikkei.com/atcl/nxt/column/18/01948/00005/
その結果、製造工程のコストは従来の約1/2、CO2排出量は従来の93%に軽減されることが明らかとなった。この再生NMCを用いて作製したLIBのセル性能は、新品のNMCで作製したセル特性(サイクル寿命、充放電性能など)を大きく上回ることが確認されている。
日本の『蓄電池産業戦略』とは?
日本は火力発電への依存度が高く、蓄電池や素材の製造段階、蓄電池のリサイクル段階において電力使用量が多いためライフサイクル評価ではCO2排出量が多くなる。一方で、LIBは再処理コストに比べて含まれている資源価値が低いため、採算が合わないのが現状である。
そのため、蓄電池のリサイクルを推進する業界団体JBRCによると、LIBの再資源化率は2017年度から52~53%と頭打ちになっており、国際競争力を維持するためにも対策が急務である。
再資源化率(%)=再資源化物重量×金属元素含有率/処理対象電池重量(付属部品を除く)×100
2022年1月、経済産業省は蓄電池の普及を念頭に置き、EVを中心に蓄電池を回収・再利用する枠組みや、調達・製造・廃棄の全過程での温室効果ガス排出量の算定方法、鉱物資源など調達網の人権・環境対応を調査しリスクを減らす基盤整備について有識者による研究会を開催した。
その結果、経済産業省は2021年11月に「蓄電池産業戦略検討官民協議会」を立ち上げており、本研究会と連携しながら蓄電池産業全体の戦略を検討することになった。
2022年4月、経済産業省は蓄電池製造を支援するために、2030年に蓄電池容量:600GWh(国内:150GWh、海外:450GWh)の生産能力を確保する目標を公表した。2020年の生産能力の約20倍となる高い目標で、民間企業の投資を促すため補助金を拡充し、世界シェアを維持するのが狙いである。
2022年8月、経済産業省の蓄電池産業戦略検討官民協議会から「蓄電池産業戦略」が公表された。この戦略の基本的な考え方は次に示すとおりで、蓄電池のサプライチェーン(供給網)の構築を主として、次世代電池の実用化加速、蓄電池のリユース・リサイクルにも焦点をあてた。
- 【1st Target】 従来の戦略を見直し、我が国も民間のみに委ねず政府も上流資源の確保含め、液系LiBの製造基盤を強化するための大規模投資への支援を行い、国内製造基盤を確立。
- 【2nd Target】 グローバルを意識して国内で確立した技術をベースに、グローバル市場をリードするプレーヤーが競争力を維持・強化できるよう、海外展開を戦略的に展開し、グローバルプレゼンスを確保。
- 【3rd Target】 全固体電池など次世代電池を世界に先駆けて実用化するために技術開発を加速し、次世代電池市場を着実に獲得。
併せて、人材育成、国内需要拡大の環境整備、リユース・リサイクル、再エネ電源による電力供給の拡大と電力コスト負担の抑制といった環境整備も進めていく。
これらの基本的な考え方に基づいた蓄電池産業戦略の目標値は、図5に示すものである。国内の自動車メーカーによるHEV、BEVの安定製造を支えるのが一義で、政府補助金により蓄電池メーカーの投資意欲を高めて世界シェア20%をキープし、先行する全固体電池の開発を加速するのを狙いとした。
技術開発で先行したリチウムイオン電池であるが、市場は中国・韓国勢の後塵を拝している現状を打破するために産業戦略は重要である。蓄電池メーカーの投資意欲が高まるのは確実な国内市場の拡大であり、蓄電池ユーザーの購買意欲が高まるのは高性能・低コスト化である。この機軸が見えてこない。
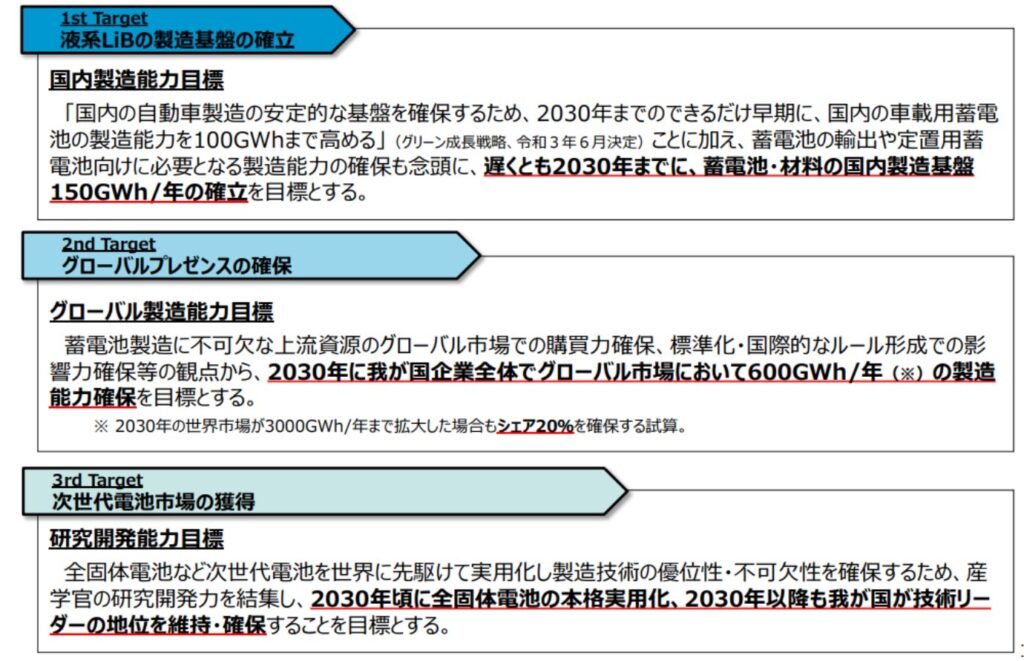
2023年9月、日本とカナダはEV蓄電池の分野で覚書を締結した。日本企業のカナダでの資源開発や現地生産を促進し、蓄電池のサプライチェーン強化を図る。米国はインフレ抑制法で北米でのEVや電池生産を優遇しており、日本企業の北米ビジネス拡大を支援する狙いもあるとみられる。
日本はコバルト、グラファイト(黒鉛)、リチウムなど重要鉱物の多くを、中国や南米などからの輸入に依存しており、黒鉛は約9割を中国から輸入している。カナダは黒鉛やリチウムなどの豊富な資源を有し、日本は中国への依存を減らし、経済安全保障の強化につなげる。
2023年9月、自動車大手や電池メーカーなどから成る一般社団法人「電池サプライチェーン協議会」に蓄電池の再利用を促すための作業部会を設置した。東芝、富士通、デンソー、プライムプラネットエナジー&ソリューションズ、三菱UFJ銀行、三井住友海上火災保険など関連20社が連携する。
作業部会では、中古電池を適正価格で流通させるリユース市場のあり方、廃棄電池から取り出した希少金属をリサイクルするための協力体制、電池劣化の状態を正確に把握する方法などについて議論し、充電された電池と使用済み電池を街中で交換するサービスの普及に向けた共同研究も行う方針。
2024年9月、トヨタ自動車、日産自動車、SUBARU、マツダの4社と電池メーカーなど8社が、EV用電池の量産に向け、2028年までに国内で新たに計約1兆円の投資を計画。政府は経済安全保障推進法に基づき、費用の1/3(3500億円)を補助し、EV市場の世界的な拡大に備え、海外に依存しないサプライチェーン構築をめざす。
EV用電池の生産は2015年に5割あったが、2020年には2割、2022年は1割弱に減り、現在は中国と韓国のメーカーが計約9割の世界シェア(占有率)を握る。政府は2030年までに、国内の電池生産能力を150GWhに高める目標を掲げる。今回の認定事業で、生産能力は80GWhから約120GWhにまで上昇する見通しである。
■SUBARUとマツダはそれぞれ、パナソニックホールディングス(HD)と共同で投資:
スバル向け電池では群馬県に約4600億円を投じ、16GWh/年(EV20万~30万台分)の生産能力を備えた工場を建設し、2028年8月に生産を始める。
マツダ向けは、パナソニックの大阪府の工場に生産ラインを設け、2025年7月の生産開始をめざす。
■トヨタ自動車は傘下の電池メーカー2社(プライムアースEVエナジー)と約2500億円を投資:
福岡県に工場を新設するなどして生産能力を9GWh/年分増強し、2028年11月以降に稼働させる。
■日産自動車は約1500億円を投資:
福岡県に新型電池「LFP電池(リン酸鉄リチウムイオン電池)」の新工場を設ける。LFP電池はレアメタルを使わず、製造コストが安く、2028年7月に生産を始める。
■これまでの経済安全保障推進法に基づく投資:
蓄電池や半導体といった重要物資に対する補助金は2023年度から始めており、これまでに本田技研工業と電池大手ジーエス・ユアサコーポレーションの工場に約1600億円、トヨタ自動車には約1200億円の補助を決めている。