日本のCO2排出量は約12憶トン/年である。資源エネルギー庁によると、2050年カーボンニュートラルを実現するには、CCSによるCO2貯留量を1.2億~2.4億トン/年にする必要があるとし、2030年までに600万〜1200万トン/年のCO2を地下貯留する目標を掲げている。
火力発電所や製油所などからCO2を回収し、船舶やパイプラインで国内外に輸送して貯留する構想で、2023年度にはCO2回収設備の設計や貯留地域の選定に向けた調査が進められる。今後、CO2貯留適地調査を進めて周辺住民の同意を得ること、貯留したCO2の有効利用が大きな課題である。
CCS/CCSUによるCO2回収・貯留
世界の動向
国際エネルギー機関(IEA)によれば、パリ協定の目標「2100年までに世界の気温上昇を2℃以下に抑える」を達成するために、2070年カーボンニュートラル時までの累積CO2削減量は、各国の目標値からさらに約358億トン/年の削減が必要とされている。
多くCO2削減施策が進められる中で、当面は火力発電への依存や脱炭素が困難な鉄鋼業などを対象として、カーボンニュートラル時までの二酸化炭素回収・有効利用・貯留技術(CCUS)の削減貢献量として約69億トン/年が必要とされている。これは約358憶トン/年の15%を占める量である。
すなわち、産業活動により排出されたCO₂を回収して貯留する二酸化炭素回収・貯留技術(CCS: Carbon dioxide Capture and Storage)に加え、有効に利用する二酸化炭素回収・有効利用・貯留技術(CCUS: Carbon dioxide Capture, Utilization and Storage)の重要性が示されている。
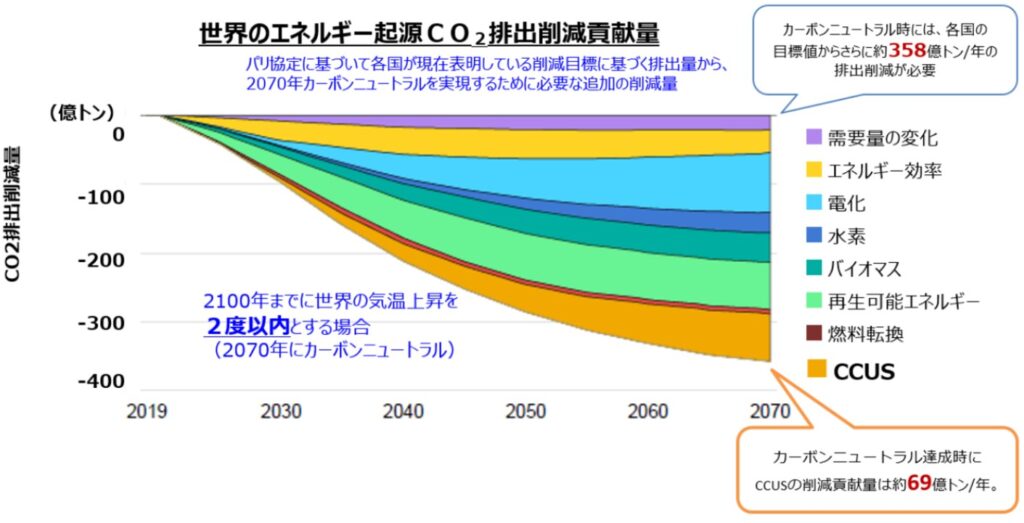
CCS施設自体は利益を生まないが、欧米では、CCS/CCUS事業に関して初期投資から操業後まで、政府が補助金や税額控除で後押しを行っている。オーストラリアのGlobal CCS Instituteによると、2022年に世界で稼働中のCCSは約30件で、160件以上の大規模開発計画があるとしている。
例えば、米国ではメキシコ湾の海底下に大規模なCCS計画があり、ノルウェーでは欧州各国から集めたCO2を陸上貯蔵した後に地下貯留する計画が進められている。英国では国内各地にCCS設備を設置する計画が進められている。
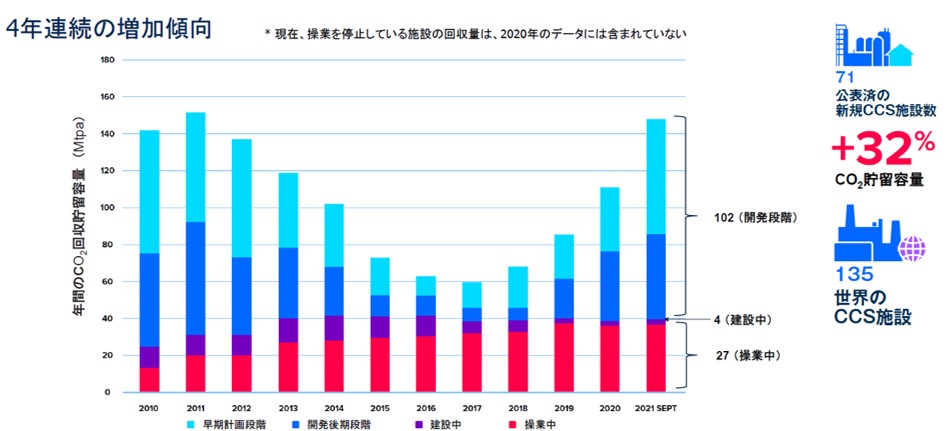
増加ペースが顕著になったのは2020年以降で、計画中の案件を含めると、CO2回収貯留容量が1億トン/年を超え、2024年は4億トン/年を超える。世界で操業中の50施設のうち米国が19施設を占める。
欧州の中でも積極的なのは英国とノルウェーで、北海油田での原油や天然ガス生産で回収したCO2を海底貯留してきた。オランダ、デンマーク、ドイツ、フランスなども積極的だ。脱炭素の機運が高まるなか、中東諸国やオーストラリアなど資源国でも導入が進められている。
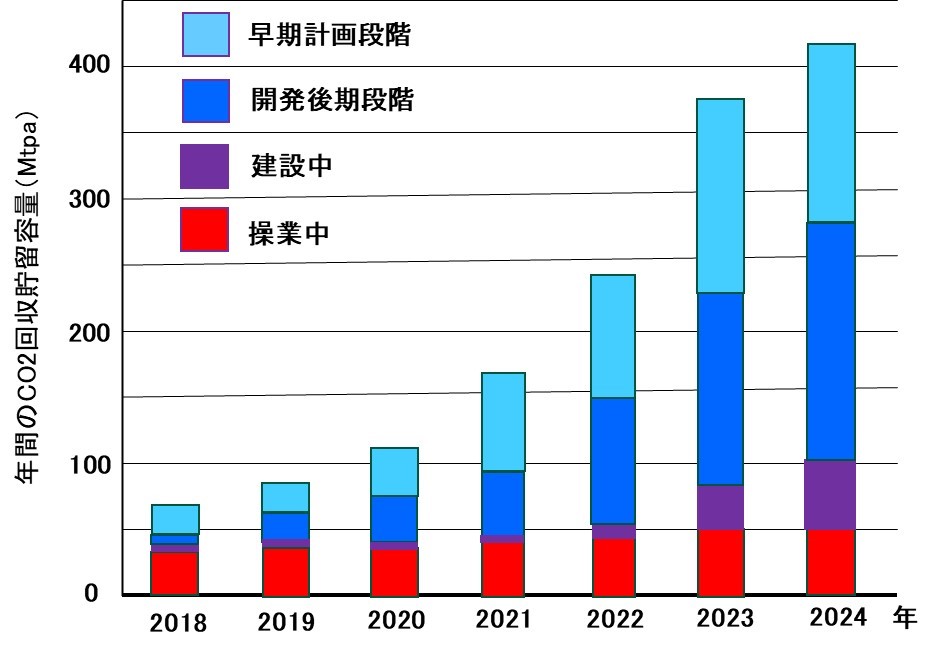
国内の動向
パリ協定の目標「2100年までに世界の気温上昇を2℃以下に抑える」を達成するために、2020年1月に策定された「革新的環境イノベーション戦略」では、国内の温室効果ガスの大幅削減にとどまらず、世界全体の排出削減に日本として最大限貢献することを目指すとした。
そのためには世界のカーボンニュートラル、さらには過去のストックベースでのCO2削減(ビヨンド・ゼロ)を可能とする革新的技術の実現が必要で、2050年までの確立を目指している。
2023年1月、経済産業省はCCSの国内事業化に向けて新法制定を表明した。2030年までのCCS事業開始を目指し、2023年秋の臨時国会への法案提出を進めている。CCSでは海底貯留などで深さ1000~3000m掘削する必要があり、新法でCCSのための貯留事業権を定める。
また、CO2漏出などのトラブルが発生した場合に事業者が負う責任の範囲や期間なども明確化し、事業者に保険加入を義務づける規定も設ける。
日本のCO2排出量は約12憶トン/年(2018年)である。政府は、2050年カーボンニュートラルを実現するにはCCSによるCO2貯留量を1.2億~2.4億トン/年とし、第一歩として2030年までに600万〜1200万トン/年のCO2を地下貯留する目標(通常の石炭火力発電2~3基分に相当)を掲げた。
政府は、民間のCCS事業参入を後押しするため、新法制定を急ぐとともに、2023年度予算案には関連費用として35億円を計上し、先進的な取り組みについて財政支援する。
2024年2月、「CO2の貯留事業に関する法律(CCS事業法)」が閣議決定された。2030年までに民間事業者がCCS事業を開始するための事業環境の整備である。必要な試掘・貯留事業の許可制度及び貯留権等の創設、貯留事業に係る事業規制・保安規制、CO2の導管輸送事業に係る事業規制・保安規制等が整備される。
政府がCCSの実現性のある地区を指定し、公募により選ばれた事業者に試掘したり、CO2を貯留する権利を与える。一方で、事業者はCO2の漏洩を監視する義務が生じ、漏洩が生じた場合の賠償責任を負う。
2024年7月、経済産業省はCCS事業化に向け国内外の9か所を「先進的CCS事業」に選出。いずれも日本企業が主導し、各プロジェクトに参加する企業はエネルギー・金属鉱物資源機構(JOGMEC)と業務委託契約を結び、2023年度にはCO2回収設備の設計や貯留地域の選定に向けた調査などを進める。
先進的CCS事業は2030年までの事業開始を目指し、2023年度から支援を開始しており7案件を選定した。2024年度は、CCSに関わるチェーン全体の設計作業や貯留ポテンシャルを評価する「先進的CCS事業にかかる設計作業等」の公募を新たに実施し。重点的に支援する事業を9案件選定した。
選定された9案件は、国内排出量の約2%にあたる合計約2000万トン/年のCO2貯留を目標としており、5案件が国内での貯留、4案件がアジア太平洋地域での貯留である。
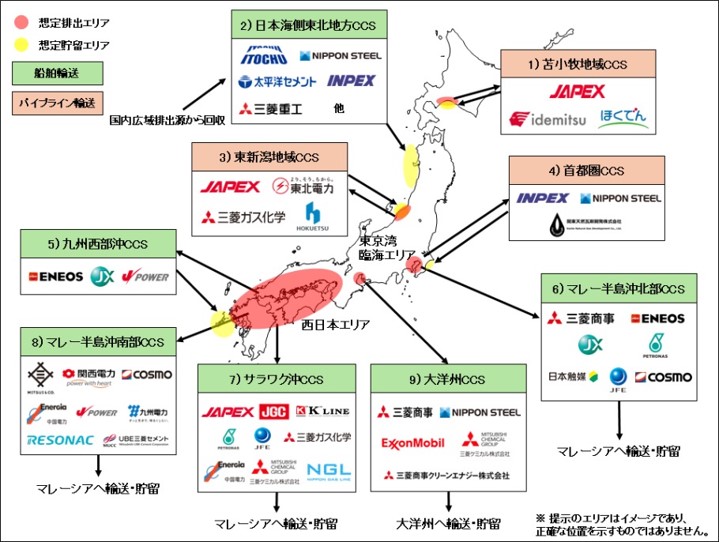
●苫小牧地域CCS事業:苫小牧地域の製油所・発電所が排出するCO2を、同地域の帯水層に約150万~200万トン/年貯留する。(石油資源開発、出光興産、北海道電力)
●日本海側東北地方CCS事業:日本製鉄九州製鉄所大分地区、太平洋セメントグループのデイ・シイ川崎工場と貯留候補地の地場排出事業者が出すCO2を、日本海側東北地方沖の海域帯水層に約150万~200万トン/年貯留。(伊藤忠商事、日本製鉄、太平洋セメント、三菱重工業、INPEX、伊藤忠石油開発等)
●東新潟地域CCS事業:新潟県内の化学工場・製紙工場・発電所が排出するCO2を、県内の既存油ガス田に約140万トン/年貯留する。(石油資源開発、東北電力、三菱瓦斯化学、北越コーポレーション)
●首都圏CCS事業は、日本製鉄東日本製鉄所君津地区および京葉臨海工業地帯の複数産業が排出するCO2を、千葉県外房沖の海域帯水層に約140万トン/年貯留。(INPEX、日本製鉄、関東天然瓦斯開発)
●九州西部沖CCS事業:瀬戸内・九州地域の製油所・火力発電所が排出するCO2を、九州西部沖の海域帯水層に約170万トン/年貯留する。(西日本カーボン貯留調査、ENEOS、JX石油開発、電源開発)
●マレーシア マレー半島沖北部CCS事業:東京湾臨海コンビナートの鉄鋼・化学・石油精製などを含む複数産業が排出するCO2を、マレーシア・マレー半島北東沖の減退油ガス田に約300万トン/年貯留する。(三菱商事、ENEOS、JX石油開発、JFEスチール、コスモ石油、日本触媒、Petronas CCS Solutions)
●マレーシア・サラワク沖CCS事業:瀬戸内地域の製鉄・発電所・化学工場などが出すCO2を、サラワク州沖の海域枯渇ガス田に約190万~200万トン/年貯留。(石油資源開発、日揮ホールディングス、川崎汽船、Petronas CCS Ventures 、JFEスチール、三菱瓦斯化学、三菱ケミカル、中国電力、日本ガスライン)
●マレーシア・マレー半島沖南部CCS事業:近畿・中国・九州地域などの発電・化学・セメント・石油精製を含む複数産業が出すCO2を、マレー半島東海岸沖の海域減退油ガス田と帯水層に約500万トン/年貯留。(三井物産、中国電力、関西電力、コスモ石油、電源開発、九州電力、レゾナック、UBE三菱セメント)
●大洋州CCS事業:中部(名古屋、四日市)の製鉄所を含む複数産業が排出するCO2を、大洋州の海域減退油ガス田と帯水層に約200万トン/年を貯留。(三菱商事、日本製鉄、三菱ケミカル、三菱商事クリーンエナジー、ExxonMobil Asia Pacific)
2024年12月、経済産業省はCCS事業で2024年度中にも支援先を選び、2025年には民間企業による国内での試掘が始まると報じられた。政府は2030年度までの事業開始をめざしている。今後も火力発電の活用を見込むため、政府は脱炭素の実現にCCS事業は不可欠としている。
現在、国内5カ所の候補地で検討されており、試掘は1候補地で2カ所ほどを想定し、1カ所あたり100億円程度かかる。経済産業省は2024年度の補正予算案に320億円を計上し、一部の案件の補助を行う。
海外ではノルウェー政府が2025年にも世界で初めて回収から地下貯留までのCCS事業を開始する。英国政府もおよそ4兆円を投じ、2020年代後半の稼働をめざす方針を示している。
2025年1月、経済産業省は2030年頃の国内CCS事業の開始にあわせ、10~15年間にわたり必要経費を補助する仕組みを導入する。CCSは開発途上のため事業規模が小さい2030年時点では1万〜1.8万円/トンCO2程度が見込まれる。支援制度の原資はGX経済移行債を想定し、2025年夏頃までに方針を固める。
ドイツ調査会社スタティスタによると、欧州ではCO2の排出枠価格が70ユーロ(約1.1万円)/トンCO2程度で推移しており地下貯留より安い。そのため、ノルウェーでは10年間、英国では最長15年の期間、CO2貯留費用と排出対策コストの価格差を補助する仕組みを作る。
政府は2024年12月に、新たな温暖化ガスの排出削減目標を2035年度に2013年度比60%減、2040年度に同73%減とする地球温暖化対策計画をまとめたが、脱炭素の実現にはCO2貯留技術の実用化が欠かせないとし、2027年度の企業の投資決定に合わせて、設備投資の補助も2027年度から始める方針だ。
2025年2月、経済産業省は、国内初のCCS事業化に向けた候補地として北海道苫小牧市沖を「特定区域」に指定した。地層の試掘調査に100億円規模の支援を行い企業の参入を促す。月内に事業者の公募を始め、今秋の試掘開始を進めて地下1000~1500mの地質を調べ、2026年までに大規模貯留の適否を確認する。
苫小牧地域では2019年までに約30万トンのCO2圧入の実証実績があり、石油資源開発(JAPEX)、出光興産、北海道電力が共同でCCS事業の調査を進めている。必要経費の補助も検討し、苫小牧市沖での貯留量を2030年までに150万トン/年に引き上げる。
2025年4月、日本とマレーシアはCO2地下貯留で協力する。日本国内の火力発電所などから出たCO2を液体にして専用船で運び、マレーシア沖の天然ガス田跡に封入する事業が2030年にも始まる。ロンドン条約の議定書で国外輸送には2国間合意が必要で、今夏までにマレーシアとの覚書に署名する
三井物産や関西電力などがマレーシアの国営石油会社ペトロナスと進めている。マレーシア沖には大規模ガス田が複数あり、枯渇後の空洞部への圧入を計画する。3事業が進行中で、合計で最大1000万トン/年程度を貯留できる。マレーシアのほか、オーストラリアなどとの協力もINPEXと中部電力が計画を進めている。
CCS事業を目指す企業動向
2022年2月、三菱商事と三井物産はオーストラリア西部沖合の海底でのCCS事業を発表。資源大手の英国BP、豪州ウッドサイドと共同で、現地工場などで排出するCO2をパイプラインで受け入れ、2030年頃のCCS設備の稼働を目指す。将来的には、日本からCO2を海上輸送する。
2022年5月、電源開発とENEOSホールディングスは2030年までに国内CCSの事業化を目指す。電源開発は石炭火力発電、ENEOSは石油精製過程で発生するCO2を回収する。2023年以降に設計を進め、2026年を目途に事業化を判断する。他社が排出したCO2の貯留も視野に入れる。
2022年11月、三井物産は、CO2を地下貯留するCCS権益を2035年までにアジア太平洋地域を中心に1500万トン/年を確保すると発表。2022~2024年にCCSに適した地下貯留層の探索・調査を進め、2030年にも日本企業などからのCO2回収から輸送・貯留までを請け負う。
インドネシア国営プルタミナと、スマトラ島中部にある陸上油田・ガス田地帯での貯留量を調査する。マレーシア国営石油ペトロナスとは、貯留量や同国外からのCO2受け入れのCO2運搬船の航路などを調査する。実際に、タイ石油公社系が持つガス田ではCCS実証実験を始める。
2023年6月、三井物産は、マレーシアでCCS事業を2030年頃までに始めると発表。マレーシア国営石油会社のペトロナスやフランスのトタルエナジーズと貯留地を共同で開発する。日本、韓国、台湾の製造業から排出されるCO2の受け入れを見込んでいる。
2023年1月、伊藤忠商事、出光興産、ENEOSの3企業連合はCCS事業化の調査を開始した。
■伊藤忠商事・三菱重工業・INPEX・大成建設:
回収されたCO2を、船舶を使って国内の貯留地まで運搬する事業の共同調査を開始
■出光興産・北海道電力・石油資源開発(JAPEX):
北海道苫小牧港を拠点としたCCSや、CO2再利用事業の検討を開始
■ENEOS・電源開発・JX石油開発:
共同で調査会社を同年2月に設立、自社の製油所や発電所から出るCO2の2030年貯留開始を目指して、西日本で適地選定の準備を開始
2023年7月、丸紅は、CCS事業を手掛けるカナダのバイソン・ロウカーボン・ベンチャーズと協業する契約を締結。額は不明であるが、2023年中には投資する予定。
バイソンがカナダに建設する2カ所のCCS事業への総投資額は420億円程度で、それぞれ世界最大級となる300万トン/年を受け入れる計画。トラック輸送やパイプラインを通じ、主にカナダ域内のアンモニア工場や石油化学工場から排出されるCO2を貯蔵する。
2023年9月、住友商事はCCSの適地を調査する事業に乗り出すと発表。調査技術を持つスタートアップ、超電導センサテクノロジー(SUSTEC)の株式を10%取得した。日本でも2050年までにCCS開発投資が少なくとも2兆4000億円に上り、拡大に向けて低コストの調査技術は世界で求められていた。
SUSTECは、超電導量子干渉素子(SQUID: Superconducting QUantum Interference Device)を応用した高感度磁気センサで、地下の比抵抗構造を調査する機器(SQUITEM)の高性能化に成功した。従来の人工地震による地震波探査に比べ、可搬式で広範囲で調査でき、費用も最大1/5程度で済む。
2024年4月、三菱重工業はドイツのハイデルベルク・マテリアルズから、カナダのアルバータ州の同社セメント工場向けCCUS設備(CO2回収量:約100万トン/年)の基本設計を受注した。北米の大手建設・エンジニアリング企業のキーウィット・エナジーグループと共同受注である。最終的な投資は2024年中に決定される。
2024年5月、三菱重工業は、千代田化工建設とCCSの包括ライセンス契約を締結した。CO2回収プラントに欠かせない周辺インフラの実績と技術を有する千代田化工と協業し、両社の強みを生かして国内プラントのEPC(設計・調達・建設)対応力を強化する。
2024年5月、INPEXとJERAは、オーストラリアでCCSで協業を発表。JERAは国内火力で排出したCO2を回収・液化してオーストラリアの油田やガス田跡地の地下貯留、INPEXはオーストラリア北部の天然ガス開発事業「イクシス」で採掘時に出るCO2をオーストラリア北部の別鉱区に2030年までに埋めることを検討している。
2024年5月、三菱重工業は、欧州鉄鋼大手アルセロール・ミタルなどと共同で高炉ガスからのCCS実証実験を開始した。ベルギーにあるミタルのゲント製鉄所高炉で0.3トン/日のCO2回収を、今後1〜2年程度稼働させる。実証実験には豪資源大手BHP、三菱商事子会社の三菱デベロップメントが参画する。
その後、鉄の圧延工程で使われる再加熱用の炉の排ガスに含まれるCO2の分離、回収にも取り組む。
2024年9月、伊藤忠商事、日本製鉄、太平洋セメント、三菱重工業、INPEX、大成建設、伊藤忠石油開発は、7社共同で提案した日本海側東北地方CCS事業構想が独立行政法人エネルギー・金属鉱物資源機構(JOGMEC)の公募事業である「先進的CCS事業に係る設計作業等」に採択されたと発表した。
日本製鉄の九州製鉄所大分地区と太平洋セメントグループのデイ・シイ川崎工場から分離回収したCO2を貯留適地候補に船舶で輸送し貯留するもので、2023年度に実施したCO2の分離回収・輸送・貯留の事業性調査に基づき、基本設計作業、試掘調査等を行い、2030年度の操業開始に繋げていく。
2024年10月、 三井物産は米国で最大2000万トン×30年間のCCS事業への10%投資を発表。テキサス州コーパス・クリスティ沖の地中貯留計画で、スペイン石油大手レプソル、CCS事業者の米国カーボンバートと共同で事業会社を立ち上げる。今後5年程度での操業開始を見込む。
排出者の候補としては製油所のほか、製造工程で発生するCO2をCCSで受け入れて大気中への排出を実質ゼロにする「ブルーアンモニア」の事業者などを想定している。
地球環境産業技術研究機構(RITE)の試算によると、CO2回収・輸送・貯留のコストは1.3万〜2万円/トン程度である。EUでの排出量取引の相場より高いため、経済産業省は2050年までにコストを現状の6割以下にするための技術開発を促している。
CCS開発の流れ
CCSとは?
CO2回収技術
国内でのCO2回収・貯留技術(CCS)の開発は、1990年の三菱重工業・関西電力による発電所のボイラ排ガスからのCO2回収に始まる。運転条件に応じてCO2を選択的に吸収・放出するアミン系吸収液が開発され、化学吸収法による技術実証が進められた。
排ガスが吸収塔に導入されると排ガス中に含まれるCO2がアミンに吸収され、吸収液はCO2リッチになる。この吸収液は再生塔に導かれてリボイラで加熱されるとCO2を放出し、CO2リーンに戻り、吸収塔で再びCO2を吸収する。これを繰り返すことで、排ガスからCO2を回収し貯留をおこなう。
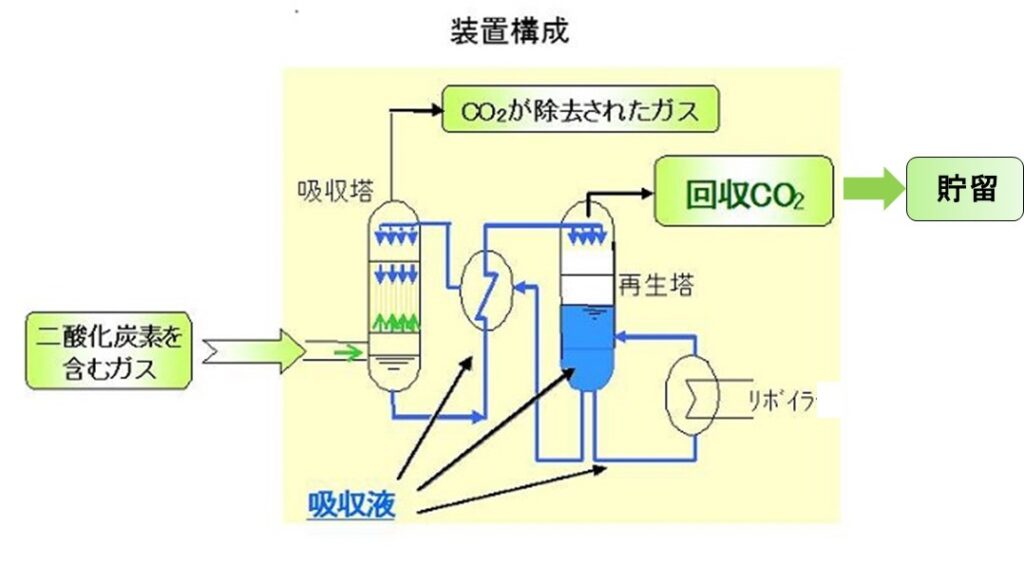
火力発電所に設置されるCCSには、ボイラ排ガスからCO2を回収する燃焼後(ポストコンバッション)方式と、燃焼前の燃料からCO2を回収する燃焼前(プレコンバッション)方式がある。
現在の主流は燃焼後方式で、既設の火力発電所にCCS設備が付帯され実証試験が行われている。ただ、大崎クールジェンの石炭ガス化燃料電池複合発電(IGFC)では燃焼前方式が採用されている。
「次世代火力発電の早期実現に向けた協議会」の技術ロードマップ(2015年7月)によると、化学吸収法は技術的に確立され各種プラントに適用されているが、回収コストが4200円/トンと高く、本格的な実用化には至っていない。
現在、2000円台/トンを目指して物理吸収法と固体吸収法によるCO2回収技術の開発が進められており、2030年に1000円台/トンを目指し、安価な膜分離法の開発が進められている。
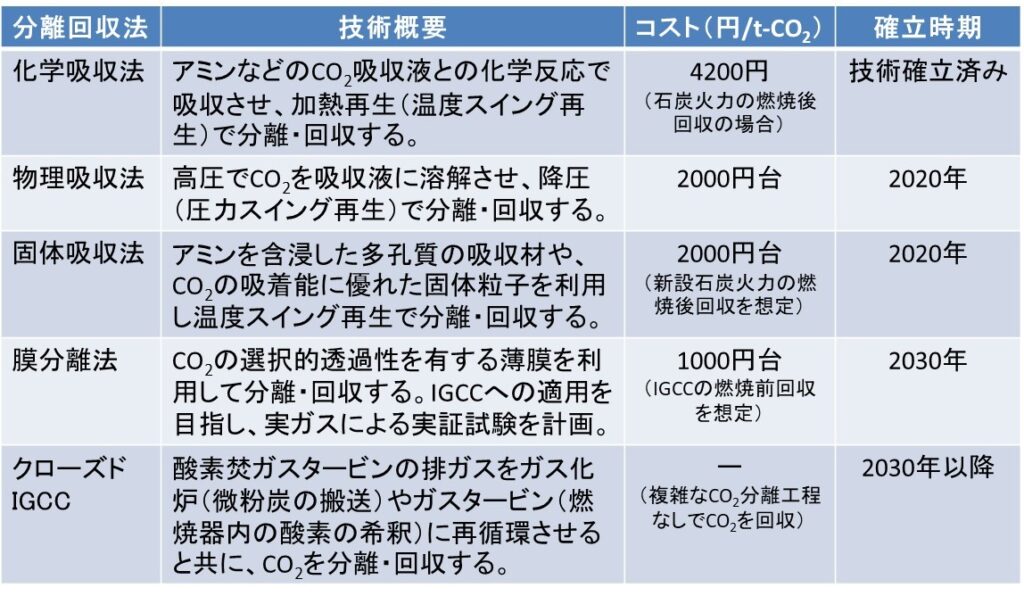
CO2貯留技術
2012年、北海道苫小牧港で、経済産業省、NEDO、日本CCS調査(JCCS)が中心となり、本格的なCCS実証試験のため設備建設が始まった。2016年4月、海岸から3~4km離れた海底下の約1000~1200mの地層、および約2400~3000mの地層にCO2を貯留する圧入作業が開始された。
製油所の排出ガス(PSAオフガス)から分離回収したCO2を約10万トン/年で地中へ貯留し、周辺地域での微小振動観測や海洋環境調査、CO2漏洩などをモニタリングした。2019年11月、累計CO2圧入量が30万トンに達して停止された。実証試験は2020年度末で終了し、圧入停止後も監視を続けている。

ところで、従来のCO2漏洩の監視は大型振源装置を利使い、1回のモニタリング調査に1億円単位の費用を要するため、モニタリング調査を繰り返し実施し、貯留したCO2の挙動の連続的な把握は困難であった。
東京大学発スタートアップのウェーブレットが開発した超小型振源装置(PASS)は、縦52cm×横66cm×高さ47cmの箱型で低コストで、地下2200m超の深さまで監視が可能なため、定常設置により連続的なデータ収集が容易で、急なCO2の動きを捉えることが可能となるため、2027年度の事業化が期待される。
CO2輸送技術
2021~2026年、関西電力・日本CCS調査・エンジニアリング協会・伊藤忠商事・日本製鉄のコンソーシアムが、京都府舞鶴市の石炭火力発電所の排ガスからCO2を分離・回収後に液化し、大型船舶で約1000km離れた苫小牧港まで海上輸送する「CCUS研究開発・実証関連事業」を進めている。
2024年9月、川崎汽船、商船三井、日本郵船、三菱造船、今治造船、ジャパンマリンユナイテッド、日本シップヤードの7社は、共同でタンクの設計や輸送方法の標準化検討を進める低圧仕様の液化CO2輸送船について、アメリカ船級協会と日本海事協会から基本設計承認(AiP)を取得した。
同年10月以降、NEDOが新たに輸送船を建造し、大量輸送に最適な条件を探る実証実験を行う。
2024年11月、発電事業者などが出資する日本CCS調査は、北海道苫小牧市で液化したCO2を受け入れる基地や貯蔵タンクの竣工式を行った。NEDO受託事業で京都府舞鶴市と苫小牧の間で、液化したCO2を専用船で繰り返し運んで貯蔵する実証試験を実施し、2027年3月末まで液化技術や輸送コストを検証する。
実証試験では、関西電力の発電所から出る3万〜5万トンのCO2を受け入れ、専用船で一度に最大800トン程度を輸送してタンクで貯蔵する。CO2の温度や圧力などの条件を変え、低コスト輸送技術を構築する。
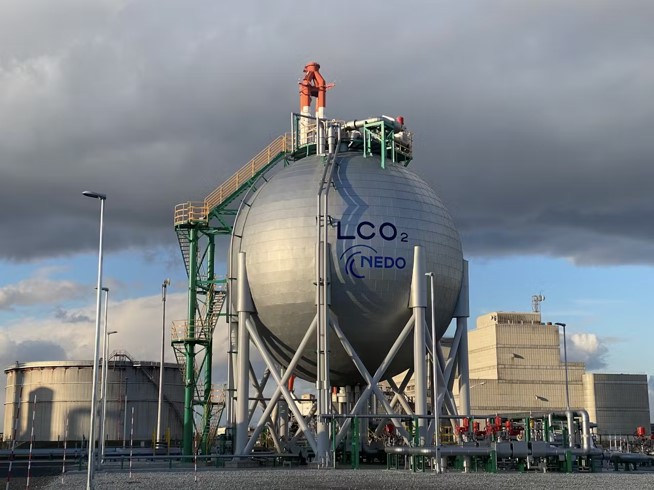
CCSの事業化
化学吸収法
1990年より、三菱重工業と関西電力は独自のアミン化合物を使用した化学吸収法によりCO2回収技術の開発を始め、KS-1吸収液を使用した「KM CDR Process」を商業化した。
関西電力南港発電所でCO2回収量2トン/日、電源開発松島発電所で10トン/日、米国大手電力会社サザンカンパニー/米国電力研究所と共同で500トン/日の実証試験を進め、排ガス中から90%以上のCO2を吸収し、99%以上の純度のCO2を回収できることを示した。
三菱重工業は2023年までに世界14カ所でCCS設備の納入実績があり、2016年には米国テキサス州で世界最大級(CO2回収量:約5000トン/日)の「ペトラノヴァ」プロジェクトを受注・納入している。
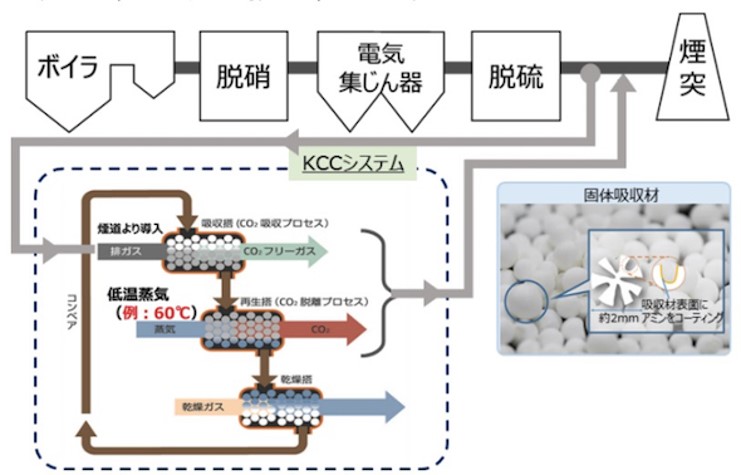
その後、プロセス改良が進められ、2019年には揮発性が低く、耐熱性に優れ、排ガスによる劣化も少ないKS-21吸収液を使用した「Advanced KM CDR Process」が実用化されている。
このCCSプロセスは、2021年6月に英国DRAXと共同でノースヨークシャー州のバイオマス発電所で採用された。また、2021年9月には、三菱造船、川崎汽船、日本海事協会と共同で、洋上でのCO2回収の実証試験が行われた。
2021年10月、三菱重工エンジニアリング(MHIENG)は、ノルウェーにおける世界最大級のモングスタッドCO2回収技術センター(CO2回収能力:約10万トン/年)の実証試験で、KS-21吸収液を使いガスタービン排ガスからのCO2回収率が最大99.8%に達したと発表した。
2025年5月、関西電力は、姫路第2発電所で排ガス中のCO2回収の実証実験を始めた。三菱重工業と試験設備(5トン/日)を建設し、プロセスの改良やCO2を回収する際に必要な「吸収液」の開発を加速する。規模や効率性を高めて新たに実証を始める。
2025年4月、AGCは、工場排ガス(5~20%)や空気中(約0.04%)のCO2を回収する新しい化学吸収液体を開発した。従来は吸収液からCO2を分離するのに100℃近くまで加熱する必要があったが、新吸収液ではLNGが気化する際に発生する熱を使い約25℃で分離できる。2035年までの事業化を目指す。
固体吸収法
2020年9月、地球環境産業技術研究機構(RITE)、川崎重工業、関西電力は、舞鶴発電所内に40トン/日の固体吸収法による試験設備を設置し、2022~2024年度にNEDO事業「先進的二酸化炭素固体吸収材の石炭燃焼排ガス適用性研究」で、石炭火力発電所のCCS実証試験を進めている。
脱硫・脱塵・脱硝後に発電所の煙道から排出ガスを抜き取り、川崎重工業が開発した「Kawasaki CO2 capture(KCC)移動層システム」でCO2回収を行うものである。
固体吸収材はRITEが開発し、吸収素材表面に厚さ約2mmのアミン化合物をコーティングしたものである。従来の化学吸収法ではCO2の再生回収に120℃の蒸気が必要であったが、60℃の減圧蒸気(発電所内の低温余剰排熱)が使えるため、エネルギー効率が高い。
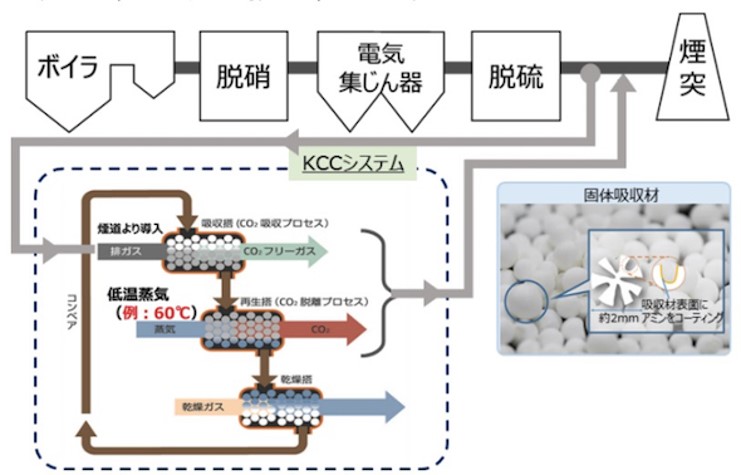
2022年6月、千代田化工建設、JERA、RITEは、LNG火力発電所からCO2を固体吸収法で回収する実証試験を行うと発表。LNG火力発電所からの排ガスは石炭火力発電所に比べてCO2濃度が低いため、2026年からJERAのLNG火力発電所で実証試験を進める。
回収コストを2000円台/トンに抑える目標を掲げ、回収したCO2はパラキシレンなどの化学品や再生航空燃料(SAF)製造への利用を検討し、将来的に液化天然ガス(LNG)プラントからの排出ガス対策にも活用する。
2023年2月、川崎重工業は、ごみ焼却施設から排出される排ガス中のCO2を分離・回収する実証実験を福島県郡山市の「富久山クリーンセンター」で始める。2023〜24年度に調査を行い、2025年度から固体吸収法による試験設備を導入する。
2023年10月、川崎重工業とRITEは、固体吸収材を使い関西電力の舞鶴発電所で排ガスからCO2を分離・回収する実証運転を始める。2023年内をに実証試験を開始し、2030年ごろには石炭火力発電所で大規模なCO2回収・貯留(CCS)を実用化する計画。
吸収したCO2を60℃で取り出せるため、セメントや石油精製、化学のプラントにも応用できる。
火力発電所へのCCS設備の導入
三菱重工業を筆頭にCCS設備の開発では先行した日本であるが、火力発電所などへのCCS設備の導入に関しては実証試験に留まっており、欧米に比べて明らかに出遅れ感がある。
実証試験から本格的導入に向けて
2009年9月、東芝は、福岡県大牟田市の三川火力発電所(出力:5万kW)内に三川CO2分離回収パイロットプラント(10トン/日)を設置し、実証試験を開始した。アミン化合物による化学吸収法による燃焼後方式のCCS実証設備である。
2012年から、広島県大崎上島で中国電力と電源開発が進めているNEDO「大崎クールジェンプロジェクト」で、2020年度にCO2分離・回収型のIGCC(石炭ガス化複合発電)/IGFC(石炭ガス化燃料電池複合発電)実証試験が進められた。化学吸収法による燃焼前方式のCCS設備である。
2016年から、IHIは相生工場(20トン/日)と豪ビクトリア州の石炭火力発電所(0.5トン/日)で、新吸収液「ISOL-160系」で化学吸収法による燃焼後方式のCCS実証試験を開始した。
2016年12月、三菱重工業を中核とする日米連合体が、米国テキサス州W.A.パリッシュ石炭火力発電所に建設した世界最大のCO2回収プラント(4776トン/日)が稼働した。化学吸収法「KM-CDR Process」を採用し、燃焼後方式で排出されるCO2の90%以上を回収する。
CO2は130km離れた油田までパイプライン送給して地中に圧入し、石油増進回収法(EOR:Enhanced Oil Recovery) に使われる。分散する原油とCO2が混ざり合い、原油生産量が40倍に増大する。通常は油田に存在する原油の25%程度しか汲み出せないが、EORで60%程度まで汲み出せる。
2022年4月、東京ガスは横浜市・三菱重工グループと、横浜市資源循環局鶴見工場の排ガスからCO2を分離・回収し、CO2を資源として利活用するCCUS確立の実証試験を2023年1月から開始する。CO2をメタネーションの原料としてだけでなく、汎用性の高い産業ガス等に資源化する検討を行う。
2022年6月、電源開発と丸紅は、スイスのグレンコアが進めるオーストラリアの石炭火力発電所から出るCO2を回収・貯留するCCS実証事業に参画する。日本での実用化に生かすのが狙い。
オーストラリア東部で英国インタージェンなどが運営する石炭火力発電所にCCS設備を設置し、2025年から回収したCO2を約100km離れた平地にある井戸から地中に貯留する。貯留量は11万トン/年で同発電所が排出するCO2の数%で、総事業費は約200億円である。
2022年6月、三菱重工エンジニアリングは、太平電業に小型CO2回収装置の商用初号機を納入し、稼働した。小型CO2回収装置(回収能力:0.3トン/日)は、広島市の複合機能都市「ひろしま西風新都」にあるバイオマス発電所(出力:7000kW)に設置された。設置面積は全長:5m×全幅:2mと、コンパクトである。
2022年7月、三菱重工エンジニアリングは、カナダ・アルバータ州のGTCC発電所向けCO2回収プラントに関する基本設計(FEED:Front End Engineering Design)を、キャピタル・パワーから受注した。対象となるCO2回収プラントは、ジェネシー発電所の1、2号機向けに設置予定で、Advanced KM CDR Processが採用される。
CO2回収量は約300万トン/年で、回収したCO2は地下に貯留される予定。キャピタル・パワーは、石炭から天然ガスへの燃料転換に向け、三菱重工製ガスタービンによるGTCC方式の導入を進めています。同方式による1号機の稼働が2023年、2号機については2024年の予定である。
2022年8月、三菱重工業、三菱重工エンジニアリングは、スコットランド・アバディーンシャーのピーターヘッド発電所で建設が予定されているGTCC発電設備(M701JAC型GT)とCO2回収プラント(Advanced KM CDR Process)に関する基本設計(FEED:Front End Engineering Design)を受注した。
このプロジェクトは、英国スコティッシュ・アンド・サザン・エナジーとノルウェーのエクイノールが進めており、約150万ト/年のCO2を回収し、北海の沖合へ回収したCO2を貯留する計画で、GTCC発電設備とCO2回収プラントを同時に建設する。
2024年4月、レゾナックHDは、CO2の地下貯留事業で三井物産と覚書を締結した。2030年頃までに、レゾナックの大分コンビナートで排出されるCO2をマレーシアで地下貯留する計画で、CO2分離・回収の技術開発も進める。三井物産は、マレーシア国営石油会社などとマレーシア沖で貯留地を共同開発する計画である。
レゾナックはCO2の分離・回収や液化、三井物産がマレーシアまでの海上輸送と地下貯蔵を担う。
2024年4月、UBE三菱セメントも三井物産とCCS事業で覚書を締結した。宇部セメント工場で排出されたCO2を分離・回収して海上輸送し、マレーシア沖で地下貯蔵を検討する。2030年までに、工場からの積み出し開始をめざしている。
2024年9月、佐賀市は、清掃工場の排ガスから分離回収したCO2について、バイオマスなど持続可能な原材料由来を証明する国際認証の「ISCC PLUS認証」を取得したと発表。
佐賀市清掃工場では市内で排出されるごみ(廃棄物)を焼却し、バイオマス発電している。さらに分離回収した高濃度CO2を隣接する農業ハウスで農作物の栽培やバイオ研究を行う企業に提供している。
2024年1月、三菱重工業は、関西電力と、姫路第二発電所にCO2回収パイロットプラントを設置することで合意した。次世代CO2回収技術を検証する新たな試験設備(約5トン/日)で、2025年度の稼働をめざす。
エクソンモービルとの提携(注)に基づくもので、三菱重工のデジタルイノベーションブランドである「ΣSynX(シグマシンクス) Supervision」の遠隔監視システムを実装する。
2025年6月、JERAと川崎重工業は、横須賀火力発電所でCO2分離・回収を2030年度までに実証する。特殊な固体吸収剤で排ガスからCO2を分離し、蒸気を吹きかけて回収する。アミン方式に比べて低温蒸気での回収が可能で、低コスト化をめざす。回収したCO2はセメント生成や園芸向けなどへの利用を検討する。
川崎重工は関西電力とも舞鶴火力発電所で同じ方式を実証中。
火力発電所のCCSコスト試算
国際エネルギー機関(IEA)によると、火力発電システムの脱炭素化とカーボンニュートラルへの移行に関して、CCS設備は①既存の火力発電施設の有効利用、②電力システム制御への柔軟性の提供、③バイオマス発電への付帯によるネガティブエミッションで大きな役割を果たすとしている。
特に、①に関してはCO2分離・回収設備の後付けの経済性評価が重要であり、発電コストに及ぼすCCSのコスト試算が行われている。
米国エネルギー省(DOE)
DOEは、中西部の平地に建設する石炭火力発電所(出力:55万kW級)を対象に、資本費、運転維持費、燃料費のコスト試算を行った。
また、CCS設備の付帯コストは、資本費に化学吸収法(Shell Cansolv)のCO2分離回収設備費を加算し、運転維持費には吸収液・修繕費などを加算し、燃料費には分離・回収に要する蒸気・電気代などを加算した。さらに、CO2輸送(昇圧・輸送)・貯留(圧入・モニタリング)費用を加算した。
対象は、亜臨界微粉炭火力発電所(蒸気圧:16.5MPa、蒸気温度:566℃)、 超臨界微粉炭火力発電所(蒸気圧:24.1MPa、蒸気温度:593℃)、LNGコンバインドサイクル発電所について行われた。
その結果、亜臨界微粉炭火力発電所ではCCS設備の後付けで発電コストは1.75倍、超臨界微粉炭火力発電所ではCCS設備の後付けで発電コストは1.74倍となる。LNGコンバインドサイクル発電所ではCCS設備の後付けで発電コストは1.51倍と報告された。
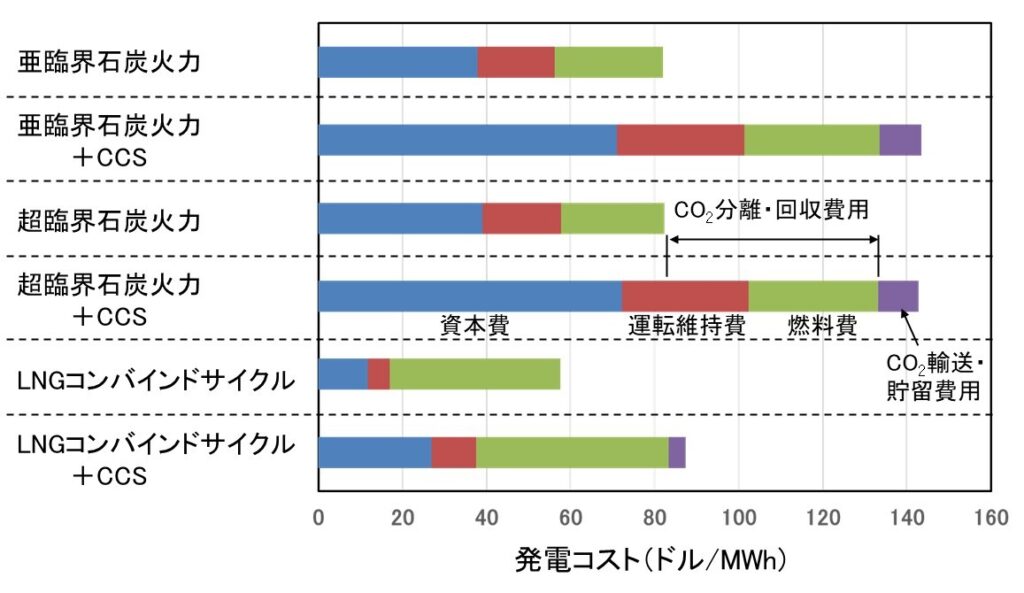
英国エネルギー技術研究所
英国エネルギー技術研究所は、微粉炭火力発電所(出力:100万kW級)とLNGコンバインドサイクル発電所を対象に、資本費、燃料関連コスト、発電コスト(均等化発電原価)のコスト試算を行った。
微粉炭火力発電所ではCCS設備の後付けで発電コストは1.55倍、LNGコンバインドサイクル発電所ではCCS設備の後付けで発電コストは1.44倍となる。
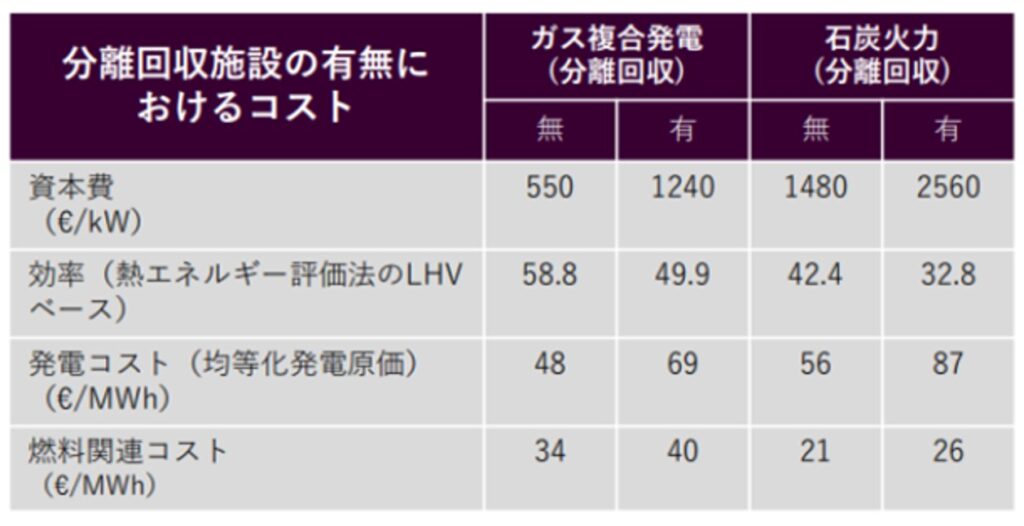
日本の電力中央研究所
電力中央研究所は、微粉炭火力発電所(出力:70万kW級)とLNGコンバインドサイクル発電所(出力:80万kW)を対象とし、第2回CCS長期ロードマップ検討会(2022年2月24日)で発表された水素・アンモニア発電コストおよび CCS設備付帯の火力発電コストを試算した。
資本費と運転維持費は発電設備(+CCS設備)で、燃料費にはH2あるいは製造設備の資本費と運転維持費を含めた。社会的費用は海外および日本におけるCO2地中貯留費で、政策経費は電源種類ごとに必要とされる税金等で賄われる費用(技術開発の予算など)である。
微粉炭火力発電所ではCCS設備の後付けで発電コストは1.9倍、LNGコンバインドサイクル発電所ではCCS施設の後付けで発電コストは1.55倍となる。
前提条件が必ずしも同一ではないため、各国で試算結果に差が認められるが、石炭火力発電所ではCCS設備の後付けで発電コストは1.55~1.9倍、LNGコンバインドサイクル発電所ではCCS施設の後付けで発電コストは1.44~1.55倍と、無視できるレベルではない。
そのため、現時点では化石燃料を使う火力発電設備へのCCS設備の付帯には大きな壁がある。
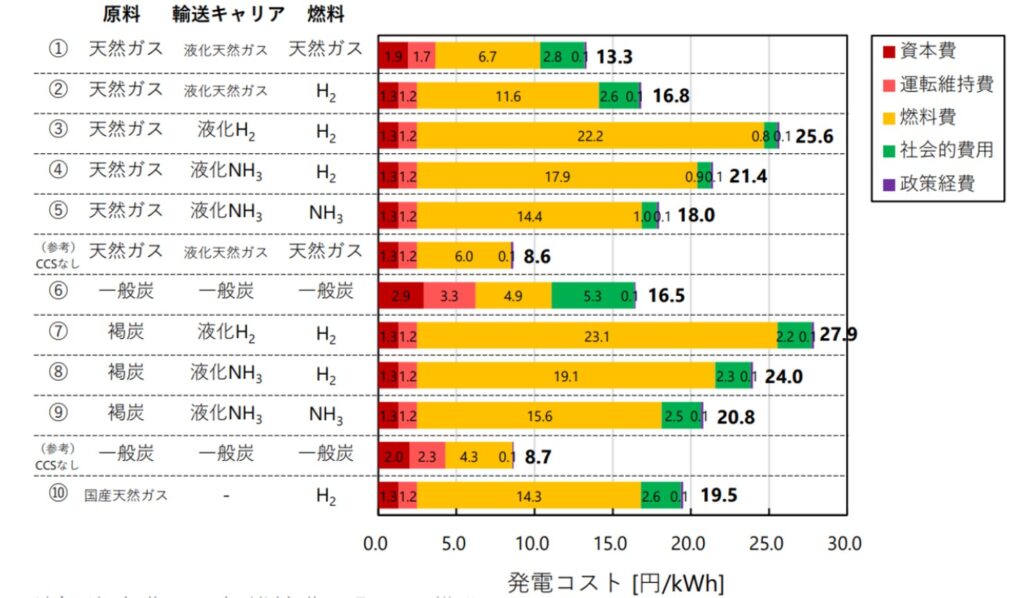
また、LNG燃料の場合の発電コストは、①LNG輸入→LNG-GTCC→燃焼後CCS < ②LNG輸入→H2製造CCS→H2-GTCC < ⑤LNG→NH3製造CCS→NH3輸入→NH3-GTCC < ④LNG→NH3製造CCS→NH3輸入→H2化→H2-GTCC < ③LNG→H2製造CCS→H2輸入→H2-GTCCの順に低いことがわかる。
すなわち、LNG燃料を輸入しGTCCにCCS設備を後付けする方式が最も低コストである。これを基準にすると、燃焼前CCSにより水素を製造するGTCCの電電コストは1.26~1.92倍、燃焼前CCSによりアンモニアを製造するGTCCの発電コストは1.35~1.61倍と高くなる。
一方、石炭燃料の場合の発電コストは、⑥一般炭輸入→石炭火力発電→燃焼後CCS < ⑨褐炭→NH3製造CCS→NH3輸入→NH3-GTCC < ⑧褐炭→NH3製造CCS→NH3輸入→H2化→H2-GTCC発電 < ⑦褐炭→NH3製造CCS→NH3輸入→NH3-GTCCの順に低いことがわかる。
すなわち、石炭火力発電所へのCCS設備の後付けする方式が最も低コストである。これを基準にすると、燃焼前CCSにより水素を製造するGTCCの発電コストは1.18~1.69倍、燃焼前CCSによりアンモニアを製造するGTCCの発電コストは1.26倍と高くなる。
電力中央研究所の試算結果からは、天然ガスや石炭など化石燃料を使う火力発電について、CCS設備付きの発電コストは、水素・アンモニア発電より低いことを示している。
これは化石燃料の輸送コストが、液体水素や液体アンモニアよりも安価なこと、燃焼前CCSの場合には化石燃料から水素やアンモニアを製造する際にエネルギー損失が生じるためである。 (ただし、この試算は2030年のLNG、H2、NH3の燃料価格を想定しており、今後の技術進展により変わる可能性があるとしている。)
CCUS/カーボンリサイクル
CO2を回収・貯留するCCSだけでは、地球温暖化問題に関する抜本的な対策にはなり得ない。CCSを持続的に行うためには、分離回収したCO2の有効利用(Utilization)は必須課題である。
そのために、二酸化炭素回収・有効利用・貯留(CCUS: Carbon dioxide Capture, Utilization and Storage)が重要であり、既に米国で実用化が進む石油増進回収法(EOR:Enhanced Oil Recovery)やCO2の産業界における直接利用が検討されている。
最近では、CO2を炭素資源として捉え、これを回収して多様な炭素化合物として再利用(リサイクル)するカーボンリサイクルの重要性が指摘され、バリューチェーンの可視化が始まっている。
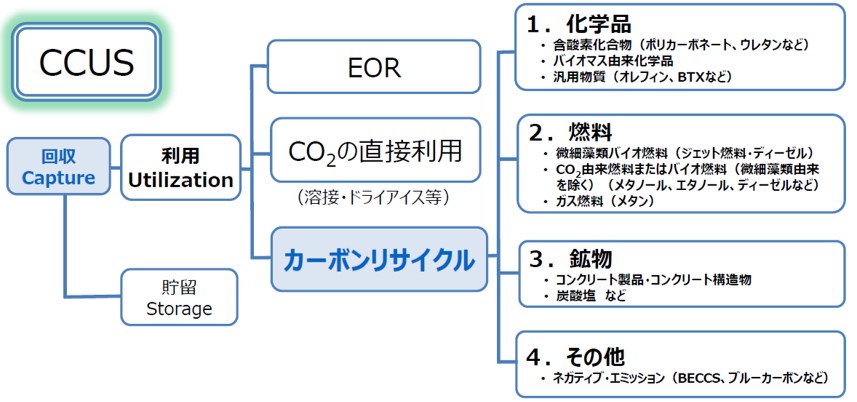
石油増進回収(EOR)
CO2は臨界圧力・臨界温度が低いが、比重が大きく、油の溶解度が高い。枯渇した油田の圧入井からCO2を圧入し、地中に残された原油をCO2により完全溶解状態にし、流動性を高め、膨張させて生産井から原油を回収する採油法が石油増進回収(EOR:Enhanced oil recovery)である。
回収したCO2をEORに使う技術は、1970年代に米国テキサス州で実用化されたのが最初である。しかし、EOR技術は費用対効果が悪く、必ずしも順調に拡大していない。転換期は、2016年のパリ協定の発効であり、気候変動対策が世界で解決すべき共通課題として認識されてからである。
2016年12月、三菱重工業中心の日米連合体が、米国テキサス州のW.A.パリッシュ石炭火力発電所に建設したCCSプラント(4776トン-CO2/日)が稼働した。化学吸収法(KM-CDR Process)により排出されるCO2の90%以上を回収、油田まで130kmのパイプラインで送給して地中に圧入する。
通常では油田に存在する原油の25%程度しか汲み出せないが、EORを使うと60%程度まで汲み出すことが可能で、原油生産量が40倍に増大した。
国際エネルギー機関(IEA)によると、2021年時点でCCSや回収したCO2を使い油田などに注入するEORプロジェクトは27件が稼働中であり、開発計画は163件と、前年比2.8倍に急増している。
2021年2月、米国エクソンモービルは、CO2の排出削減の新事業「低炭素ソリューション」を発表した。2025年までに30億ドルを投じ、ヒューストンではメキシコ湾海底にCCSハブを建設し、シェブロン、ダウ、ドイツBASFなど世界中の企業と連携し、CO2をまとめて貯留する計画である。
CO2貯留量は2030年までに5000万トン/年とする計画である。2024年にノルウェーで稼働開始する欧州最大級のCCSプラント「ノーザンライツ」の33倍以上の規模となる。
2022年11月、三菱重工エンジニアリングと関西電力が米国エクソンモービルと、CO2回収技術の共同開発に向けた提携を発表した。三菱重工業が基盤技術のライセンスをエクソンモービルに供与し、エクソンモービルは回収したCO2を地層に注入して保管するプロジェクトを手掛ける。
CO2の直接利用
CO2の直接利用は、冷却用ドライアイス(昇華温度:−78.5℃)や炭酸飲料として広く用いられているが、約100万トン/年といわれている。
工業用途としてはシールドガスにCO2を利用した炭酸ガスアーク溶接、液化されたCO2を高圧容器に入れた二酸化炭素消火器、洗浄物の表面にドライアイス粒を吹きつけるドライアイスブラスト洗浄などがあげられるが、用途は限定されており大量のCO2削減は望めない。
カーボンリサイクル
CO2を炭素資源と捉え、これを回収して多様な炭素化合物として再利用(リサイクル)することを「カーボンリサイクル」と呼ぶ。
2019年8月、三菱ケミカル・電源開発・三菱日立パワーシステムズ・IHI・川崎重工業など16社は、カーボンリサイクルファンドの立ち上げを発表した。
発電所などから出るCO2を回収し再利用することが目的で、衣料や建材の素材、燃料などを作る技術を確立し、商用化を目指してコスト低減技術を軸に企業や研究者に資金を提供する。
化学品
1999年、三菱重工業はマレーシアに尿素肥料増産用にCO2回収装置(20トン/日)を納入した。その後、インド、中東諸国を中心に尿素肥料増産目的にCO2回収装置が納入され、現在も安定稼働している。2017年には、日本液炭向けに13基目が納入され商業運転を行っている。
2016年8月、佐賀市清掃工場では、廃棄物発電所(出力:450kW)から排出されるCO2を回収する東芝製のCCS設備(10トン/日)が稼働した。
タンクに貯蔵したCO2を隣接する藻類培養施設に供給し、医療品の原料になる微細藻類ヘマトコッカスの培養を行っている。ヘマトコッカスからは抗酸化作用の強いアスタキサンチンを抽出でき、アルビータなどと商用化を進めている。
また、佐賀市水浄化センターでは、下水汚泥を発酵させたバイオガスからCO2を回収・貯蔵し、微細藻類ユーグレナの培養施設に供給している。ユーグレナは健康食品や、油分を抽出分離してジェット燃料(SAF)の原料として商品化を進めている。
2021年7月、京都大学発のSymbiobe(シンビオーブ)は、紅色光合成細菌を使うCCSプラントの開発を発表した。同細菌は海中などに生息して光合成により水中のCO2と窒素を取り込み固定し、水産物の養殖用飼料や窒素肥料や、分解されやすいバイオプラスチック原料などに活用できる。
京都府北部で試験プラントを計画し、2025年以降には量産プラントの製造を目指している。
2021年8月、日本製鉄・大阪市立大学・東北大学は、酸化セリウム触媒を用いて常圧のCO2とジオールを反応させ、水を蒸発除去してカーボネート合成が可能なことを明らかにした。今後、固体触媒の改良を進め、有機カーボネート、カーバメート、尿素などの合成の可能性を検討する。
2021年9月、東京ガスは排ガスに含まれるCO2と水酸化物を反応させ、洗剤や肥料などの原料となる炭酸カリウムを、都市ガス利用先で製造するオンサイトCCUS技術を開発している。
カナダのCleanO2 Carbon Capture Technologies(CleanO2)製の炭酸カリウムが製造できるCO2回収装置「CARBiN-X」を使用する計画で、小型装置(幅0.85m×高さ1.9m×奥行2.0m)のため、商業施設など小スペースへの導入が可能で、今後、実証試験を進め商用化を目指す。
2023年8月、旭化成はCO2と水からつくる樹脂原料のエチレン製造を電気分解で実用化すると発表。2026年に国内で数十kW級の小型設備、2030年に1万kW級の大型設備で数千トン/年規模のエチレン生産を目指す。再生可能エネルギー由来の電力で樹脂製造時のCO2排出量が大減らすのが狙い。
エチレンを生成する反応を促す最適な触媒にめどをつけており、CO2と水素を反応させてエチレンの原料をつくる手法に比べて、工程が少なくてすむ特徴があるが、課題はコストである。
2024年6月、東ソーは工場で排出したCO2を回収し、化学製品(断熱材などウレタン製品)の原料へのリサイクルを始める。山口県周南市の南陽工場でCO2回収設備(約4万トン/年)が10月末にも稼働し、事業所内で塩水の電気分解で製造する水素を化学反応させて、ウレタン原料である一酸化炭素(CO)を製造する。
従来、ナフサを熱分解してCOを生産していたが、ナフサの一部をLNGに切り替え、回収したCO2も原料とする。製造コストは従来以下に抑えられる。塩ビモノマー、合成ゴム、石英ガラスなどの製造も進める。
燃料
現在、開発が進められているのは、再生可能エネルギーなどの余剰電力で水電解により水素(H2)を製造し、回収貯留したCO2と共にメタネーション(Methanation)装置に入れ、加熱することで都市ガスの主成分であるメタン(CH4)を合成する方法である。
2019年5月、IHIはシンガポール科学技術庁の化学工学研究所(ICES)と共同で触媒を開発し、メタネーション技術の試験装置を製造して1Nm3/日のメタン製造に成功した。また、燃料電池の逆反応を使いメタンを製造する高温水蒸気電解(SOEC)共電解メタン合成も検討している。
2019年10月、国際石油開発帝石と日立造船は、メタネーション試験設備を長岡鉱場の越路原プラント敷地内に完成させた。越路原プラントで天然ガス生産時に付随するCO2と、固体高分子水電解装置(32Nm3/h)により製造された水素を合成することでメタンを製造する。
日立造船製のプレート型メタネーション反応器は、熱回収効率が87%と高く、運転温度:200℃、運転圧力:0.7MPaであり、生成ガス(メタン濃度:91.2%)をガス精製器を通し、高濃度化(99.6%)が可能である。メタン製造能力は8Nm3/hで、4500h以上の安定製造を確認している。
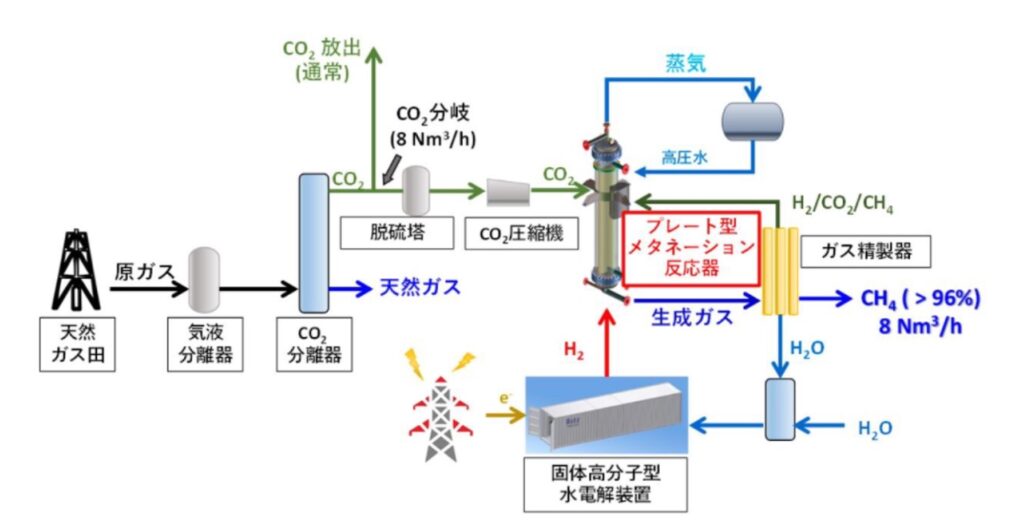
2020年7月、デンソーは、安城製作所のアルミ溶解炉などから出たCO2を回収して太陽光発電で製造した水素を使いメタネーションの実証実験を始めた。合成メタンはガス燃料に使い、CO2を工場内で循環させる。2025年度から社外での実証実験も取り組み、2030年度の事業化を目指す。
2021年6月、メタネーション技術の確立と社会実装に向けた「メタネーション推進官民協議会」が設立され、官民両面での取り組みが加速する。政府は、2030年までに都市ガス導管に注入するガスの1%をカーボンニュートラルメタンとし、2050年までに90%とする目標を掲げた。
2021年8月、日立造船が小田原市環境事業センターのごみ焼却施設から排出されるCO2と水素を反応させるメタネーション装置の設置を進めており、2022年春以降に稼働する予定を発表している。エア・ウォーターの排ガスからCO2を分離する技術を活用している。
2021年10月、INPEXと大阪ガスは、大規模メタネーション装置(製造能力:約400Nm3/h)の導入によるNEDO「CO2排出削減・有効利用実用化技術開発事業」(~2025年度末)を開始した。
INPEX長岡鉱場の越路原プラントからCO2を回収し、メタネーション設備を接続して製造した合成メタンをINPEXの都市ガスパイプラインへ注入する。
2021年12月、大阪ガスの子会社Osaka Gas Australia Pty は、100カ国以上でエネルギーインフラ事業を展開するATCO の子会社ATCOオーストラリアと、オーストラリアでのメタネーション事業の実現可能性調査に関する基本覚書を締結し、共同研究を開始した。
両社はメタネーション実験設備の建設に向けた立地や、CO2や水素の供給方法と輸送・販売方法に関する検討、国内・輸出向けのビジネスモデル構築や経済性評価などを、2022年中に実施する。
2022年3月、東京ガス・太平洋セメントは、セメント製造過程から出るCO2と水素を合成した都市ガスを供給する事業化調査を開始した。実証プラントは太平洋セメントの国内工場内に設置し、メタネーションにより得られた合成メタンを既存のガス導管に入れて需要家に供給する。
2022年3月、東京ガスは横浜テクノステーションで、メタネーション実証試験を開始した。主に、太陽光発電の電力で英国ITM Power製の固体高分子型水電解装置(製造能力:30.9kg/h、圧力:1MPa未満)で水素製造を行い、大気中から回収されたCO2を用いる。
日立造船製の多管シェル&チューブ型メタネーション装置(CH4製造能力:12.5Nm3/h)でメタン合成を行う。横浜市らとの連携で、カーボンニュートラル化の地産地消モデルの検討を行う。2020年代中頃に数百Nm3規模に拡大し、2030年にガス販売量の1%に合成メタン導入の目標を掲げている。
2022年4月、大阪ガスは金属支持型SOECで水素を製造し、回収されたCO2から都市ガスを製造するメタネーション試験設備を大阪市酉島地区に建設する。
2027年度までに200世帯程度、2030年度までに1万世帯分の都市ガス製造を実現し、設備の大型化などで製造コスト削減を進め、2040年頃の事業化を目指す。2023年8月には、石油元売りのENEOSと共同で大阪湾岸での大規模な施設の建設に向けた検討に入った。
2022年4月、大阪ガスは大阪市や大阪広域環境施設組合と、再エネ由来の水素と生ごみを発酵させて製造したバイオガス(メタン約60%とCO2約40%)中のCO2でメタネーションを行い、合成メタンを需要家に供給する。環境省「水素サプライチェーン構築・実証事業」(2022年度~25年度)で行う。
2022年8月、日本特殊陶業はメタン製造設備を開発し、2023年4月頃から小牧工場で実証実験を行う。ゼオライト膜を使いガスエンジンから出たCO2を回収し、水電解で得られた水素と反応させて1Nm3/h(0℃、1気圧)の合成メタンを製造し、ガスエンジンの燃料として再利用する。
将来的に、4Nm3/hのメタン製造設備を開発し、2030年に中小規模工場への販売を目指す。製造コストは100円台/Nm3と、現状の1/3程度に引き下げ計画である。
2022年9月、豊田自動織機は高浜工場でメタネーションの実証実験を始めた。ボイラにCCS設備を付帯し、化石燃料由来のグレー水素と混ぜて合成メタンを製造し、別ボイラの燃料で再利用する。将来的に全工場にメタネーション設備を導入、太陽光発電によるグリーン水素へ切り替える。
2022年10月、IHIは、合成メタンを製造できる小型メタネーション装置の販売を開始した。シンガポール科学技術庁と共同開発した技術で、合成には触媒を用いるサバティエ方式を採用し、反応器型式にシェル&チューブで、合成メタン製造量:12.5Nm3/hで、外形寸法は幅2250mm×長さ6100mm×高さ2850mmである。
開発したメタネーション装置は、工場や研究所、事業所などでのカーボンニュートラル実現に向けた検討のために試験運用したいというニーズに対応している。
2024年5月、IHIは、東邦ガス知多e-メタン製造実証施設向けに二酸化炭素(CO₂)と水素(H₂)からe-メタン(合成メタン、CH₄)を製造する「メタネーション標準機」を納入した。製造されたe-メタンが都市ガスの原料として利用されるのは国内初であり、東邦ガスでは5Nm³/hで運転する。
2030年には大型装置(数千~数万Nm³/h)の商用化も予定している。2022年にJFEスチールから500Nm³/hの実証機を受注し、高炉排ガスからのCO2回収(20トン/日)も含めて、2025年の稼働を予定。CO2回収は吸熱反応、メタネーションは発熱反応であるため、組み合わせることでエネルギー効率を高められる。
2025年4月、太平洋セメントは、CO2回収技術の確立を目指す「C2SPキルンプロジェクトチーム」を設立する。子会社であるデイ・シイ(川崎市)の工場に、セメント製造時のCO2を効率的に回収する仮焼却炉「C2SPキルン」を使った技術の確立や、メタネーションなどのCO2利用・貯留技術の開発に取り組む。
鉱物
2019年7月、日米両国は石炭火力発電所から出るCO2の再利用で連携し、建材原料に再生する共同開発を発表した。日本の石炭エネルギーセンターや米国ワイオミング州、コロンビア大学などが参加する計画で覚書を締結し、商用化に伴い大規模化するのに必要な技術検証を行う計画である。
米国ワイオミング州の石炭火力発電所(出力:40万kW)を使い、排出ガスに含まれるCO2を石炭灰や廃棄物と混ぜ合わせて化学反応を起こし、コンクリートや道路の資材として使われる炭酸カルシウムを製造する。既に、基礎技術はコロンビア大学の試験装置で実証されている。
2021年5月、伊藤忠商事はオーストラリアMineral Carbonation International(MCi)とCO2固定化技術を活用する協業契約を締結して出資した。MCiのCO2固定化技術は、一定以上のCO2濃度の気体ではCO2の分離・回収工程が不要であり、低コスト化に有利である。
MCiは製鉄工程で生じるスラグや火力発電所で生じる石炭灰、廃コンクリートなどカルシウムやマグネシウムを含む様々な物質とCO2を反応させ、炭酸カルシウム、炭酸マグネシウム、シリカなどを製造する技術を有し、セメント、コンクリート、建設用資材など幅広い用途が見込まれる。
2022年3月、トクヤマは、三菱重工エンジニアリングと、セメント製造時に排出されるCO2の回収技術の共同実証試験の実施について合意。2022年6月から9か月間の予定で、徳山製造所南陽工場セメント製造部で、のCO2回収装置をセメントプラントに設置し、排ガスからCO2の回収を行う。
石灰石(炭酸カルシウム、CaCO3)を原料とするため、トクヤマではCO2の排出量は約180万トン/年に上る。長期連続運転の信頼性評価を行い、回収したCO2ガス内の不純物などのデータを分析し、セメント工場における最適なCO2回収技術の適用性を検証する。
2022年3月、Mitsubishi Heavy Industries EMEAと三菱重工エンジニアリングは、バーレーンの国営アルミニウム精錬会社nアルバとの間でCO2回収技術の適用可能性検討の覚書(MOU)を締結した。
2022年4月、アイシンと大成建設は、アミノ酸水溶液に排気ガスを吹き込み炭酸カルシウムとしてCO2を固定化し、製鉄所の高炉スラグでカーボンリサイクル・コンクリート「T-eConcrete®/Cabon-Recycle」を製造・活用するために共同開発契約を締結した。2030年頃までの実用化を目指す。
2022年10月、製鉄大手のアルセロール・ミタル、三菱重工エンジニアリング、鉱業会社のBHP、Mitsubishi Development Ptyの4社は、アルセロール・ミタルの製鉄所におけるCO2回収技術に関する協業契約を締結。
実証試験はアルセロール・ミタルがベルギーのゲントと北米に保有する製鉄所にて行われ、CO2削減が困難なHard-to-Abate分野といわれる製鉄業界におけるCCUS技術の促進をめざす。
2024年4月、三菱重工業はドイツのハイデルベルク・マテリアルズから、カナダのアルバータ州の同社セメント工場向けCCUS設備(CO2回収量:約100万トン/年)の基本設計を受注した。北米の大手建設・エンジニアリング企業のキーウィット・エナジーグループと共同受注である。最終的な投資は2024年中に決定される。
2024年5月、三菱重工業は、千代田化工建設とCCSの包括ライセンス契約を締結した。CO2回収プラントに欠かせない周辺インフラの実績と技術を有する千代田化工と協業し、両社の強みを生かして国内プラントのEPC(設計・調達・建設)対応力を強化する。
2024年5月、三菱重工業は、欧州鉄鋼大手アルセロール・ミタルなどと共同で高炉ガスからのCCS実証実験を開始した。ベルギーにあるミタルのゲント製鉄所高炉で0.3トン/日のCO2回収を、今後1〜2年程度稼働させる。実証実験には豪資源大手BHP、三菱商事子会社の三菱デベロップメントが参画する。
その後、鉄の圧延工程で使われる再加熱用の炉の排ガスに含まれるCO2の分離、回収にも取り組む。
2024年5月、清水建設は、バイオ炭を混入してコンクリート内部にCO2を固定する環境配慮型コンクリート「SUSMICS-C」のCO2削減効果が、第三者審査機関であるソコテック・サーティフィケーション・ジャパンの確認を得たと発表。コンクリートへのCO2固定量が、CO2排出量を上回るカーボンネガティブを達成した。
SUSMICS-Cは、1kgあたり実質2.3kgのCO2を固定化したバイオ炭を60kg/m3混和した配合を採用している。コンクリート練混ぜ時にバイオ炭を投入するだけで製造できるコンクリート材であり、既存の生コンプラントをそのまま利用して製造でき、普通コンクリートと同様にポンプ圧送による打ち込みもできる。
今後、アスファルト合材の混合材料としてバイオ炭を利用し製造過程で生じるCO2排出量を実質ゼロにする「SUSMICS-A」、改良対象土に溶融スラグとバイオ炭を混入することで施工に起因するCO2排出量を実質ゼロにする地盤改良工法「SUSMICS-G」等を現場のニーズに合わせて展開する。
2024年6月、中国電力、鹿島建設、デンカが開発した「CO2-SUICOM」は、製造時にCO2を吸収・固定する環境配慮型コンクリートとして世界で初めて算定され、CO2固定量が国際連合に報告された。
従来のセメントの半分以上を、化学工場の副産物である副生消石灰(γ-2CaO・SiO2)を主成分とした特殊混和材に置き換えたもので、高濃度のCO2と反応して吸収・硬化する。火力発電所の排気ガス中のCO2を利用する技術も確立した。産業副産物の有効利用と、CO2の大量固定によりネガティブエミッションをめざす。
2025年3月、 鹿島建設と川崎重工業は、DAC技術(5kg/日)で大気から回収したCO2を利用し、CO2吸収コンクリート「CO2-SUICOM®」にCO2を吸収・固定させる炭酸化養生槽を組み合わせたシステムを構築した。
このシステムをプレキャストコンクリート製品工場に設置して実証実験を行った結果、所定のCO2固定量ならびにコンクリートとしての品質が得られることを確認した。
ネガティブエミッション技術とは
「2050年カーボンニュートラル」の達成には、最大限の温室効果ガス(CO2など)の排出削減を行っても、排出が避けられない分野からの排出(残余排出)を相殺する必要が生じる。この手段として、大気中のCO2除去(CDR:Carbon Dioxide Removal)が必須となる。
世界的には、2050年に約20~100億トン/年のCO2除去が必要とされている。既に、米国、欧州(EU)、英国などではネガティブエミッション技術(NETs:Negative Emission Technlogies)と今後の取組方針を公表し、導入拡大・社会実装に向けた積極的な政策支援を開始している。
日本でも、産業・運輸部門を中心に想定される約0.5~2.4億トン/年の残余排出を相殺するためには、同量のCDRが必要である。しかし、希薄な大気中からのCO2除去には、発電所などからのCO2分離固定(CCS)に比べ高コストとなる。
2023年6月、経済産業省は「ネガティブエミッション市場創出に向けた検討会」を開催し、国内外におけるNETsの技術開発動向、ビジネス動向、NETsの産業化にあたり重視すべき要素等を整理し、今後の方向性やルール形成や、市場創出に向けた方針を検討している。
様々なネガティブエミッション技術
ネガティブエミッション技術(NETs)は、大気中のCO2を回収・吸収し、貯留・固定化することで、現状よりも大気中に含まれるCO2濃度を下げる(負にする)ための技術と定義される。
すなわち、植林や海洋吸収など自然界で進むCO2吸収・固定化の過程に、人為的な作業を加えることで大気中のCO2除去を加速させる技術やプロセスの総称である。
植林や海洋吸収などの多くは、グリーン社会の実現に向けた国土交通省の重点プロジェクト「国土交通グリーンチャレンジ」や、ブルーインフラの拡大により進められているが、近年、より積極的に大気中のCO2を分離・吸収し、貯留・固定化する技術が注目されている。
すなわち、バイオエネルギーを使って炭素を回収・貯留するBECCS(Bio Energy with Carbon Capture and Storage)と、大気中から直接炭素を回収・貯留するDACCS(Direct Air Carbon Capture and Storage)である。
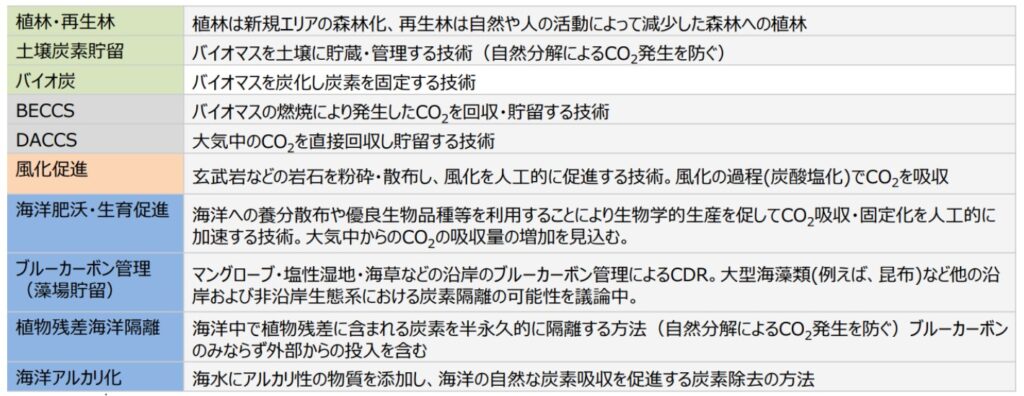
CO2の除去コストと削減ポテンシャル
海洋アルカリ化を除き、ネガティブエミッション技術の多くが2050年に1トンあたりのCO2除去コストが200ドル以下になると予測されている。しかし、海洋関連、風化促進、DACCS、バイオ炭など、今後、実効性の検証も含めて開発途上にある技術が多い。
自然界にCO2を貯留するネガティブエミッション技術は、低濃度のCO2を低コストで固定できる能力を有すると考えられている。しかし、気象や気候による変動が顕著で、実際のCO2削減量のカウントが困難な場合が多い。今後、CO2削減量の評価方法や、国際的な認証システムが必要である。
実際に、植林(新規植林・再植林)によるCO2除去コストは、他の方法より大幅に安い5~50ドル/トンで、2050年のCO2削減ポテンシャルは41億トン/年と予測されている。しかし、植林で多量のCO2削減を実現するには、多くの土地や水が必要になる。
一方、工学プロセスを活用するDACCSやBECCSは、気象や気候による影響を受けず、CO2除去効果の定量的評価が可能で、2050年のCO2削減ポテンシャルはDACCSが29億トン/年、BECCSが50億トン/年と予測されている。しかし、CO2除去コストは110~180ドル/トンと割高である。
また、いずれの場合のCO2削減ポテンシャルも、分離したCO2の貯留方法を確保できるか否かによって大きく変化することに注意が必要である。
気候変動に関する政府間パネル(IPCC)の「地球温暖化1.5度特別報告書」では、BECCSのCO2除去コストは100~200ドル/トン、2050年のCO2削減ポテンシャルは5~50億トン/年。また、DACCSにのCO2除去コストは100~300ドル/トン、CO2削減ポテンシャルはBECCSと同じと推計している。
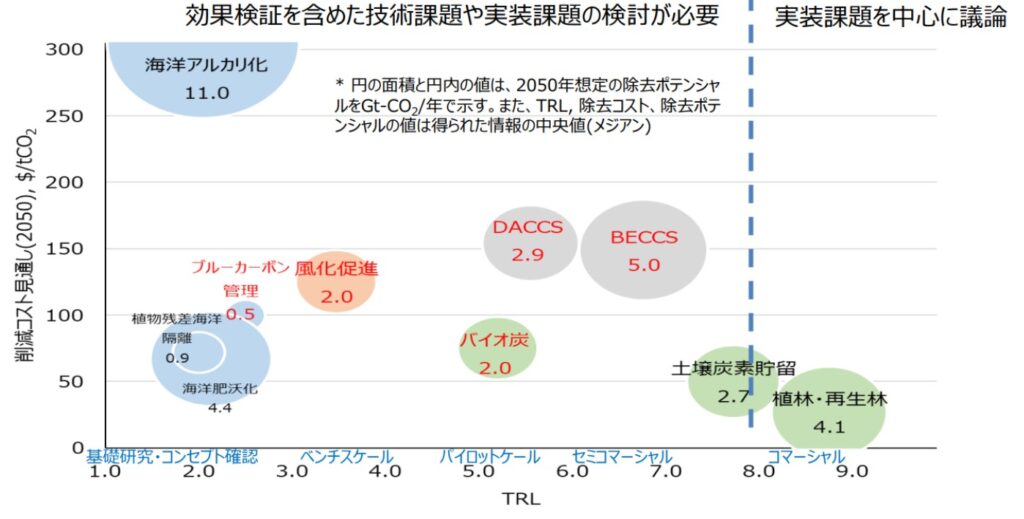
注目されるBECCSとDACCS
主要国の温暖化対策の長期シナリオでは、温室効果ガス(GHG:GreenHouse Gas)排出抑制やカーボンニュートラルの達成に向け、過去に排出されたCO2を人為的に回収・除去するネガティブエミッション技術の決め手として、BECCSとDACCSが大きな役割を果たすことを期待している。
すなわち、2050年におけるBECCSとDACCSによるCO2除去率を、2020年のGHG総排出量に対して中国は6.4%、フランスは3.4%、英国は12%、EUは6.1%と計画している。ドイツは2045年におけるCO2除去率を8.8%、日本は2015年のGHG総排出量の14%をDACCSで除去するとしている。

*1ドイツの除去量は2045年、*2日本のGHG排出量は2015年の数字
CO2除去コストの削減とCO2削減ポテンシャルの実現を目指し、各国で支援が始まっている。■2021年7月、EUイノベーション基金は、アイスランド・ヘトリスヘイジ地熱発電所で、溶剤の替わりに水でDACCSを行うSilverstoneプロジェクトへの補助金を決定。
■2021年11月、EUイノベーション基金は、スェーデン・ストックホルムでのBECCSプロジェクトへの補助金を決定。
■2021年11月、米国エネルギー省は、DACCSのコストを1トンあたりCO2除去コストを100ドル未満にする「カーボン・ネガティブ・ショット」目標を発表。
バイオマス発電所へのCCS設備導入
2020年代に入ると、急速にバイオマス発電所へのCCS設備の導入が始まった。基本的にバイオマス発電所はCO2排出量が実質ゼロとみなされるため、付帯したCCS設備が稼働すれば大気中のCO2を減らすネガティブエミッション(負の排出)発電所となる。
バイオエネルギーを使って炭素を回収・貯留するプロセスはBECCS(Bio Energy with Carbon dioxide Capture and Storage)と呼ばれ、気候変動に関する政府間パネル(IPCC)の第5次評価報告書でも、BECCSが脱炭素の有力な手段になる可能性を指摘している。
また、バイオマス発電とCCSを組み合わせた技術が代表的なBECCSであるが、バイオマスからの水素製造やバイオプロセスで発生するCO2を回収・貯留するプロセスもBECCSに含まれる。
世界の動向
2017年、米国Archer Daniels Midlandは、トウモロコシからエタノールを製造する施設に100万トン/年のCO2回収能力のCCS設備を付帯し、イリノイ州産業炭素貯留プロジェクトを進めている。
2021年現在、エタノール発酵で発生するCO2を対象とするCO2回収能力100万トン/年規模の複数のBECCSが北米で稼働中である。
2020年6月、大手電力会社の英国Draxと三菱重工エンジニアリングは、ノースヨークシャー州に保有するバイオマス発電所からCO2を回収する実証実験(約300kg/日)を、2020年秋から1年間実施すると発表した。
BECCSを導入することで、最大1600万t-CO2/年の削減計画を立てており、これは2050年までにCO2排出量を正味ゼロにする英国の政策達成目標1/3に相当する。
2021年3月、英国の木質ペレットを燃料とするDrax発電所が、CO2回収能力800万トン/年のBECCSプラント開発を英国政府に申請。2024年に建設開始、2027年に2基のうち最初のユニットが運転を開始する予定である。
同社は、2019年にノースヨークシャーのSelby火力発電所の燃料を石炭からバイオマスに転換し、2020年に三菱重工業からCCS装置を導入して運転実績を積んできた。
その他、スウェーデンStokholm Exergi は、木質バイオマス発電所に80万トン/年のCO2回収能力のBECCSプラント開発を計画中で、ノルウェーFortum Oslo Varmeは、廃棄物発電所に20万トン/年のCO2回収能力のBECCSプラント稼働を2024~2027年に予定している。
また、オランダTwenveは、廃棄物発電所に10万トン/年のCO2回収能力のCCS装置を設置し、2021年の稼働を予定している。回収されたCO2は温室で使用される。
一方、CO2の貯留については地下貯留以外にも、生物資源を原材料として生物の活性化や環境の改善に効果のある炭化物(バイオ炭)によるCO2貯蔵や、バイオマスを熱分解によって液化したバイオリキッドを地中に注入する研究開発などが行われている。
今後、より低コストで信頼性に優れた新しいCO2貯留方法が開発されるであろう。
国内で進む導入状況
2020年10月に、環境省「環境配慮型CCS実証事業」で、東芝エネルギーシステムズはグループ会社のシグマパワー有明が所有する福岡県大牟田市の三川発電所(出力:5万kW)でCCS実証設備(500トン/日)の運転を開始。主燃料はパーム椰子殻(PKS)で、排出されるCO2の50%以上を回収する。
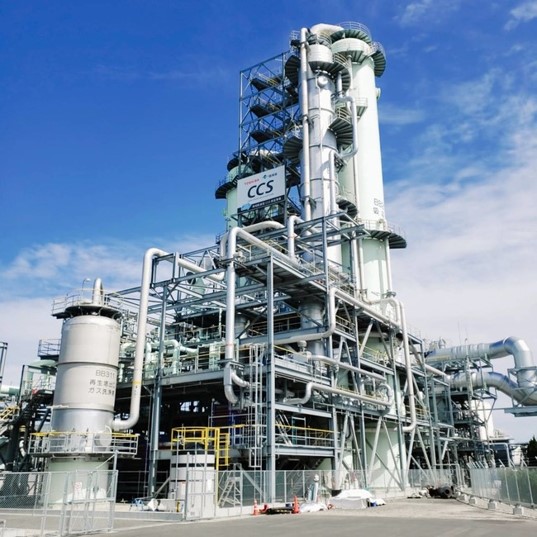
出典:東芝エネルギーシステムズ
2021年6月、三菱重工エンジニアリングと英国電力大手Drax Groupは、ノース・ヨークシャー州のバイオマス発電所で、「Advanced KM CDR Process」を長期使用する契約を締結した。
2022年2月、日本製紙とタクマは、北海道苫小牧市の勇払バイオマス発電所(出力:7.5万kW)で、バイオマス発電に適した高効率CCS装置の開発を2023年から始めると発表。苫小牧CCS実証試験センターのCO2地下貯留施設と組み合わせて、2030年の導入・稼働を計画している。
タクマはアミン化合物を溶かす溶媒に一般的な水を使わない方式で、100℃以下でも効率的にCO2を分離でき、分離に必要な熱量を1.5GJ/トン-CO2と従来比の半減を目指している。
2022年6月、三菱重工エンジニアリングは、太平電業から受注した小型CO2回収装置の商用初号機の稼働を発表した。「ひろしま西風新都」のバイオマス発電所(出力:7000kW)に導入され、CO2回収量は0.3トン/日で、ほぼ全量を回収して構内の農業ハウスで活用する。
小型CO2回収装置はモジュール化を進め、設置面積が長さ5mX幅2mで、製造工場からトラック輸送し、短期間で設置することができる。
BECCSの課題
バイオマス発電とCCSを組み合わせたBECCSは、既に完成した技術の組合せであり、技術的な開発課題は多くはない。ただし、2050年のBECCSのCO2削減ポテンシャルは50億トン/年と予測されているが、このCO2削減ポテンシャルは、分離したCO2の貯留地を確保できるか否かで大きく変化する。
そのため、地下貯留以外の様々なCO2貯留・固定化方法の開発が、低コスト化の開発と並行して継続的に進められている。
また、BECCSのCO2削減ポテンシャルを達成するには、バイオエネルギー資源の持続可能な供給量や食料生産との競合が課題としてあげられている。すなわち、生物多様性などの自然環境保護や食料の安定供給などに悪影響を与えずにBECCSを進めるには、社会的な認知・合意が不可欠である。
直接空気回収技術(DAC)
火力発電所や化学プラントなど大規模なCO2発生源からの排気ガスにはCO2が10~15%程度含まれているのに対し、最近では、大気中に400ppm(0.04%)程度しか含まれない希薄なCO2の直接空気回収(DAC:Direct Air Capture)技術が注目されている。
DACで大気中から直接CO2を回収し、貯留まで行う技術はDACCS(Direct Air Carbon Capture and Storage)と呼ばれ、ネガティブエミッション技術(NETs)の一つとして、急速に注目を集めている。
脱炭素へ再生可能エネルギーなどを最大限導入しても航空機や船舶、一部の発電施設などでは化石燃料に一定量を頼らざるを得ず、CO2排出をゼロにはできず「残余排出」と呼ばれる。
国際エネルギー機関(IEA)や気候変動に関する政府間パネル(IPCC)によれば、世界では2050年時点で20億〜100億トン/年、日本でも0.5億〜2.4億トン/年にのぼる。これらを相殺してカーボンニュートラルを実現するには、CO2排出量をマイナスにする「ネガティブエミッション」技術が必須であり、DACは本命とされている。
国際エネルギー機関(IEA)によると、既に、DAC設備はスイス、カナダ、米国など世界で18カ所に設置・稼働しており、CO2回収量は約1000トン/年程度である。しかし、2050年の温暖化ガス排出量を実質ゼロにするには、DACで2030年に6000万トン/年のCO2を回収する必要がある。
DACCSでは、CO2を大気から液体溶剤や固体吸着材に吸収・吸着させ、CO2を分離・回収して貯留する。回収したCO2を吸収・吸着材から分離させる再生段階には、熱を用いる「温度スイング吸着」、気圧変化を用いる「圧力(真空)スイング吸着」があり、大量のエネルギーを必要とする。
DACで回収したCO2は、地下に貯留されたり(従来のCCS)、化学品、燃料、セメントなどの製造原料(CCUS)に使われて固定化・貯留される。
海外で進むDACCSの動向
2017年、スイスのスタートアップClimeworks(クライムワークス)は、アイスランドのHellisheidiでCO2回収能力50トン/年の小型DACCSを建設し、地下注入して鉱物化による貯留の研究を開始した。
同年、スイスのHinwilではCO2回収能力900トン/年の小規模商用DACCSプラントを開設しており、回収されたCO2は温室・飲料用に使われている。
2021年9月、クライムワークスは、アイスランドのHellisheidi(ヘトリスヘイジ)地熱発電所の隣接地で、CO2回収能力4000トン/年のOrca(オルカ)プラントの運転を開始した。現時点で世界最大のDACCSプラントである。
ON Power(オンパワー)の地熱発電所から電力供給を受け、地下CO2鉱物化を専業とするCarbfix(カーブフィックス)が、回収されたCO2と水を混ぜて地下深くに注入し、鉱物化プロセスによりCO2の固定化を行う。
2022年6月、クライムワークスは、アイスランドの首都レイキャビク近郊でDACCSプラント(CO2回収能力3.6万トン/年)の建設に着工した。運転には隣接の地熱発電所の電力を使い、2024年5月に一部が稼働し、年内の完成をめざす。クライムワークスは、2050年までにCO2回収能力10億トン/年を目標に掲げている。
アミン系吸収材とγ- Al2O3やゼオライトを組み合わせた多孔質固体にCO2を吸収させる固体吸収法を採用し、回収したCO2は鉱物化プロセスにより固定化・貯留を行う。CO2地下貯留を手掛けるカーブフィックスと提携、回収したCO2を水に溶かして地下に送り、火山国特有の玄武岩層に固定する。
2030年に数百万トン/年規模が実現できれば250~350ドル/トンで回収可能で、長期的には100~200ドル/トンを目標としている。CO2を除去した分を、排出枠を取引する「カーボンクレジット」として企業に売る。米マイクロソフトや金融機関などすでに180社以上が購入した実績がある。
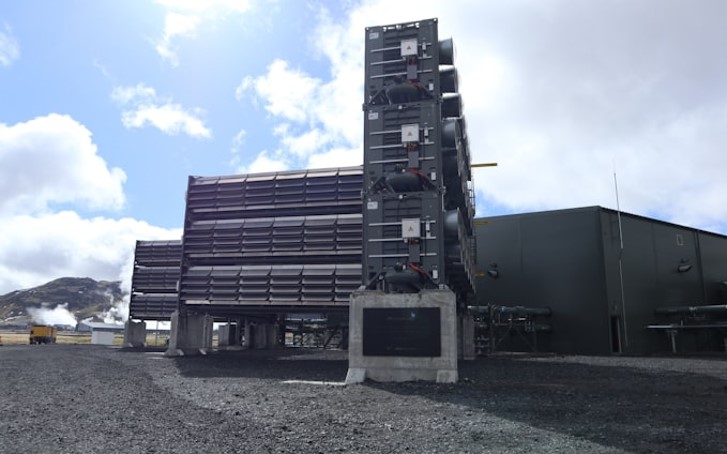
2019年6月、米国エクソンモービルが米国スタートアップのGlobal Thermostatと提携。アミン系吸収材とハニカムセラミック「モノリス」を組み合わせた多孔質カーボン吸着材を利用したDAC装置を商品化した。吸収されたCO2は、低温蒸気(85~100℃)で分離・回収する。
グローバル・サーモスタットは、2019年頃にアラバマ州のHunstsvilleにCO2回収能力0.4万トン/年の小規模DACCSプラントを開設しており、回収したCO2は食料・飲料用途に使われている。
2022年5月、米国政府はルイジアナ州など国内4カ所に拠点を設け、5年間で補助金35億ドルをDACCS事業に投じる方針を表明。100万トン/年以上のCO2を回収するプロジェクトが対象で、事業化調査やプラント設計などの費用の一部を補助する。
また、経済的な支援策でも米政府は「インフレ抑制法」に基づき、DACによるCO2回収1トン当たり最大180ドルを税額控除すると表明している。
2022年8月、米国オキシデンタル・ペトロリアムと子会社1PointFive(ワンポイントファイブ)は、テキサス州にDACCSプラント(CO2回収能力が最大50万トン/年)の建設を発表した。水酸化カリウム溶液(KOH)でCO2を回収する方法を開発している。
2024年後半に稼働し100万トン/年まで拡張可能。回収コストは300ドル/トン以上、量産化で150ドル/トン以下を目指す。回収分をクレジット(排出枠)として販売し、欧州エアバスや日本のANAホールディングス、米アマゾン・ドット・コムなどが購入を表明している。
2015年、カナダのスタートアップCarbon Engineerigは、ブリティッシュコロンビア州でCO2回収能力365トン/年の小型DAC設備を設置して研究を進めてきた。
2022年、ベンチャー企業のOxy Low Carbon Venturesが設立したワンポイントファイブとともに、米国テキサス州Permian盆地に、CO2回収能力100万トン/年のDACCSプラントの建設を開始した。
ワンポイントファイブはカーボン・エンジニアリングとも協力し、最大100万トン/年のDACCSプラントを、2035年までに70基つくる計画も発表し、需要があれば最大135基を建設するとしている。
2023年11月、2020年に発足した米国エアルームは、米国初の空気からCO2を直接回収する商業用施設をカリフォルニア州で稼働させた。米国IT大手から最大31万トン規模の除去を受注した。同社は水酸化カルシウムがCO2と反応して石灰岩になる性質を利用し、大気中のCO2を地中に貯留する。
2018年創業の米国チャーム・インダストリアルは、バイオマスを熱分解してバイオオイル(液体)にして枯渇した油井に注入する技術の開発を進め、2023年6月までに1億ドルを調達した。
2021年創業の米国キャプチュラは海水から炭素を取り除く技術を開発し、ノルウェー企業などと連携して2025年に1000トン規模の除去事業を立ち上げる計画を示している。
2024年2月、米国アーカンソー州で、スタートアップのグラファイトが運営するバイオマスと呼ぶ農林業廃棄物を加工して炭素を貯蔵する施設が稼働した。バイオマスに含まれる炭素を分解する微生物を除去してブロック状に圧縮し、特殊な包装を施して地中に埋めてCO2を放出しないようにする。
本格稼働する2025年からは5万トン/年の除去を見込み、米国内で2施設を建設する準備を進め、東南アジアなどバイオマスが豊富なグローバルサウスでの建設もめざす。
CO2除去に関するデータを集計・公開しているCDR.fyiによると、2023年の世界のCO2除去サービス市場は17億ドル(約2530億円)と公表している。2021年との比較では36倍に増え、2023年のCO2の除去量も2021年比43倍の466万トンに増えた。
一方、CDR.fyiによるとバイオオイルを利用するCO2除去の価格は2023年に1トンあたり平均505ドル、エアルームの直接空気回収は715ドルであり、低コスト化がCO2除去の大きな壁になっている。
2024年7月、クライムワークスは直接空気回収(DAC)の巨大施設を2027年にも米国で稼働する。米国ルイジアナ州の南西部で2026年に着工。CO2回収能力は2027年に最大25万トン/年で稼働し、2030年までに100万トンに引き上げる。2024年5月に北欧アイスランドで稼働した施設は3.6万トン/年で約30倍である。
クライムワークスは、CO2回収に膨大な電力を使うため、再生可能エネルギーが豊富にあるオーストラリア、ノルウェー、ケニアを次の建設候補地に掲げている。
EUの排出量取引制度(EU―ETS)でCO2の取引価格は80ドル/トン前後であるが、現時点でCO2回収・除去に1000ドル/トン以上を要するため、政府支援制度を含めたコスト削減が最大の課題である。一方、マイクロソフトやJPモルガン・チェースと、埋設したCO2を「炭素クレジット」として販売する契約を締結している。
一方、米国石油・ガス大手オキシデンタル・ペトロリアムは、DACを手がける子会社を通じてテキサス州で100万トン/年のCO2を回収可能な超大型プラントの構想を公表。インフラ投資法関連の政府支援を活用する。
また、2023年、石灰石を使ってDACに取り組む米国エアルーム・カーボンは、1000トン/年のCO2回収施設の操業をカリフォルニア州で始めた。同社もマイクロソフトに炭素クレジットを販売する。
国内のDACCSの動向
2021年2年、IHIは、そうまIHIグリーンエネルギーセンターで開発したDAC装置により100%濃度のCO2回収に成功し、4月から植物工場で実証試験に入る。回収したCO2は太陽光発電で生成した水素と反応させ、メタネーション実証装置(製造能力:12m3/h)でのグリーンメタン合成実証も行う。
アミン系吸収溶液へ球体基材を浸し、引き上げて乾燥させたCO2固化吸収材を使い、ブロワーで空気を吸い込みCO2を吸収させ、CO2の分離時には加熱する。
2021年12月、川崎重工業は固体吸収法によるDAC装置を実用化し、回収後のCO2貯蔵技術と組み合わせたDACCSの商品化を発表した。5㎏/日の実証試験を進め、2025年に500~1000kg/日(15~30万トン/年)に高めて、ビルや商業施設などでの設置を目指す。
凹凸が多く表面積が大きい粒状物質の表面に特殊な溶液を塗り、大気と接触させてCO2を吸着させ、その後に60℃程度の低温蒸気で加熱してCO2を分離・回収する。
2022年4月、三井物産はDACCSの事業化を発表した。英国スタートアップ企業とDAC技術の共同調査などで包括提携を締結した。水酸化カリウムや水酸化カルシウムの溶液などでCO2を回収する。
2022年9月、三菱重工エンジニアリングはRITEと共同で、DAC試験装置(数kg/日)を開発した。今後、CO2固体吸収材の評価を進めて、2020年代後半にパイロットスケールのDAC試験装置の設計と経済性評価を実施する。
2022年11月、日本碍子は、プラント大手とDAC設備(数百~数千トン/年)を建設し、2025年に実証試験を開始する。自動車排ガス浄化用セラミックス「ハニセラム」内部に固体吸収材を塗布、ファンで空気を送り、CO2を吸着させたハニセラムを100℃程度に加熱してCO2を分離・回収する。
2023年9月には、大気中のCO2を直接回収するDAC用セラミックスを公開した。
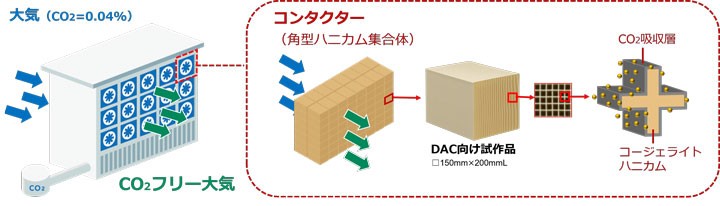
2023年10月、日本ガイシは、自動車排ガス浄化用セラミックスで培ったセラミック製ハニカム構造体の技術を応用し、「コンパクトかつ表面積が大きい」「圧力損失が低い(大量の空気を効率よく処理できる)」などの特長をもつDAC向けハニカム構造吸着材を開発中で、2025年に実証実験、2030年の欧州市場投入をめざす。
2023年8月、全日本空輸は、世界の航空業界で初めてDACCS事業を手がける米国1ポイントファイブと、2025年から3年間で3万トン以上のカーボンクレジット(排出権)を購入する契約を結んだ。
大気中などのCO2除去(CDR:Carbon Dioxide Removal)由来のカーボンクレジットは、現在300〜1800ドル/トンで取引されており、米国マイクロソフトは310万トン分、欧州エアバスは40万トン分の購入を決めている。
2024年1月、住友商事は大気中などからのCO2回収事業を開始すると発表。ノルウェーのインへリット・カーボンソリューションズなどに出資し、2030年に200万トン/年以上のCO2回収をめざしている。得られるカーボンクレジット(排出権)を、2025年から販売する。
インへリットは家畜のふん尿などから出るバイオガスからメタンを抽出して発電し、その過程で発生するCO2を回収・地中貯留している。
2024年7月、鹿島建設は、大気中のCO2をコンクリート内部に固定する製造法を年内に構築する。川崎重工業のDAC技術で回収した高純度CO2を固まる途中のコンクリートに固定する。セメントにCO2を吸収する特殊材料を混ぜ、製造時の排出量をマイナスにする「カーボンネガティブ」技術である。
まずは、工場生産するコンクリートブロックや法面保護パネルの製造に導入する。将来的には大型のコンクリート部材の置き換えにも応用する見込みだ。社会への普及を優先するため、CO2排出量を既製品の25%程度に抑えた低炭素コンクリートの製造を進める。価格は従来の2倍程度となる見込み。
スイスのクライムワークスはアイスランドで大規模なDAC施設を運用しており、米国ではCO2をコンクリートに吸収させる技術を持つカナダのカーボンキュア・テクノロジーズがDACと組み合わせたコンクリート生産を実現している。
2024年10月、大阪ガスは、「金属有機構造体(MOF)」と呼ばれる多孔質材料を組み込んだDAC実験装置を、大阪市内の研究所で稼働。比表面積の大きいMOFとアミンを組み合わせて、CO2の吸着効率を高める。e-メタンの原料にCO2を調達する手段として開発を進める。
2025年6月、カルシウムやマグネシウムなどの成分を含む玄武岩などを粉砕して農地などに散布し、大気中のCO2を吸収・固定化する「エンハンスト・ロック・ウェザリング(ERW)」が注目されている。粉砕で表面積を増やした岩石が溶解してCO2と結合し、炭酸塩や炭酸イオンとして固定化され土壌改善への期待も高い。
自然環境下での岩石の風化には1000〜1万年程度を要するが、玄武岩などを破砕して表面積を拡大し、岩石風化促進により人為的に炭酸塩化を加速させる。2020年に英国シェフィールド大学のデビッド・ベアリング教授らが発表した論文が発端で、2023年にスタートアップの米国テラドットがブラジルで事業を開始した。
注目されるのは、米国のグーグルやマイクロソフト系のファンドなどが、2024年12月にテラドットへ5820万ドルを出資。グーグルはテラドットから20万トンのカーボンクレジットも購入。2025年4月、マイクロソフトも1万2000トンのCO2除去でテラドットと合意している。
2025年6月、セイコーエプソンは工場排ガスや大気中からCO2を直接回収する装置の販売を、2028年度にも始める。厚さ10nmの膜分離法で複合機サイズ(電源:100V)に小型化し、既存工場の中にも設置できる。数百万円/台程度を想定し、4台連結で10kg/日以上の高濃度CO2が回収でき、薄膜単体での販売も検討する。
国内におけるDACの研究開発:
■2019年から名古屋大学発スタートアップのSyncMOFは、約20社の工場で金属有機構造体(MOF)を使ったCO2回収の実証試験を進めている。MOFは狙った気体だけを大量に吸着する性質があり、アミン系溶液を使う従来方法に比べてコストを1/10にできる。
■2020年1月、九州大学カーボンニュートラル・エネルギー国際研究所とナノメンブレンは、高分子分離膜によりCO2を分離する膜分離法の開発を進めている。2022年2月には、双日と厚さ約30nmの薄膜でCO2を分離する技術の社会実装に向けた覚書を締結した。
■2022年2月、三菱瓦斯化学・神戸学院大学はアミン系化合物を吸収材にしたDAC実証試験と吸収材開発の共同研究を発表した。メタキシレンジアミン(MXDA)用いると、大気中の水分の影響を受けずCO2のみを吸収できるため、CO2脱離時の効率を大幅に改善できる。
■2022年5月、東邦ガスは名古屋大学などとLNGの未利用冷熱を活用するDAC試験装置(1トン/年)を2024年度までに試作し、2029年度に大型プラントの稼働を目指す。CO2吸収液をLNGでー140℃以下に冷却してCO2を固化、常温で復温・気化させ高圧CO2を直接回収する。
■2024年5月、九州大学発スタートアップのJCCLは、吸収剤を使ったCO2回収装置(50℃程度の低温蒸気使用)と、分離膜で低濃度CO2を95%以上に濃縮する2つ装置販売を発表。従来の1/4程度のコストで、ボイラーなどの排ガスから97%以上の濃度のCO2を2kg/日で回収できる。
■2024年5月、東京都立大学、大気社、ウシオ電機のチームがDACの実験装置を稼働。現時点のCO2回収能力は約10g/日と小規模だが、能力を高めて大気社グループが運営する植物工場や関係農場のビニールハウスの近隣に置き、回収したCO2を農業で活用する。
「イソホロンジアミン」という液体に空気を通すとCO2を吸収し、固体になり液体中に漂い、これを60℃に加熱するとCO2が分離回収できる。
■2024年6月、スタートアップのプラネットセイバーズが開発したDACのパイロット装置が稼働する。触媒などに使われるゼオライトという吸着材を使い、約10kg/日のCO2を回収する実証研究である。圧力の上下で吸着・分離する新タイプである。2026年までに最大1トン/日の装置開発をめざす。
DACCSの課題
大気中のCO2濃度は工場や発電所の排ガス中の濃度の約1/300と低いため、DACによる回収コストは300~600ドル/トンと排ガスからの回収コストの5~10倍とされる。一方、温暖化ガス排出量の取引価格(先物)は近年上昇しているが、EUではCO2換算で80ユーロ/トン(約70ドル/トン)前後である。
現時点で欧米ではDAC設備の普及に関して補助金などによる支援を行っているが、持続可能なDAC設備とするための最大の課題は、高効率化と低コスト化である。現在は、米国で100万トン/年の大規模DACプラントの建設が始まっており、量産効果に期待が集まっている。
2050年のCO2削減ポテンシャルはDACCSが29億トン/年と予測されている。ただし、CO2削減ポテンシャルは、分離したCO2の貯留地を確保できるか否かで大きく左右される。そのため、地下貯留以外の様々なCO2固定化方法の開発が、低コスト化開発と並行して進められている。
DACで回収したCO2の利用法については、高付加価値な化学品や燃料、鉱物が製造できれば、DACCSプラントとしての普及が進む可能性がある。
そもそも日本はCO2排出量取引で欧米より大きく遅れており、DAC支援策もこれからの課題である。
CO2排出量取引では経済界が長く難色を示し、2023年度から約750社が参加して自主的な取り組みが始まったが不参加企業もあり、政府は2026年度から電力や鉄鋼業界などに参加を義務づける方針を示した。
DACも経済産業省が専門家による検討会を設けたが、開発支援や市場づくりなど今後の課題が山積の状態である。
2021年設立されたカリフォルニア工科大学のスピンオフ企業キャプチュラは、地球表面の70%を占める海洋を活用する直接海洋回収技術(DOC:Direct Ocean Capture)を使い、大気中のCO2を低コストで除去する施設の建設を目指している。
海水は大気からCO2を吸収するため、ろ過した海水をプラント内に引き込み、再生可能エネルギーを使って海水を電気分解してCO2を除去して貯留する。
海水からの直接CO2回収技術(DOC)
国際エネルギー機関(IEA)によると、「2050年カーボンニュートラル」達成のためには2050年時点で約10億トンCO2を回収する必要がある。大気中からのダイレクト・エアー・キャプチャー(DAC)の検討が先行しているが、CO2は空気中に0.04%しか含まれず、回収効率を上げにくいのが現状である。
そのため、海水から回収するダイレクト・オーシャン・キャプチャー(DOC)が注目されている。海水は大気からCO2を吸収し海水1㎥中のCO2は95gで、大気中の数十倍のため高効率で回収できる可能性がある。海水中のCO2を減らすことで、大気中から海水に溶ける量が増え、大気中のCO2を減らすことができる。
2023年、米国スタートアップのCaptura(キャプチュラ)は、カリフォルニア州のロサンゼルス港にCO2回収施設(100トン/年)を稼働した。また、カリフォルニア工科大学にも実験プラントを保有する。
弱いアルカリ性である海水をくみ上げ、電気透析で海水の一部を酸性にする。酸性の海水を残りの海水と混ぜると、CO2が気体になり炭酸水が発生するため、独自開発したガス分離膜を使って直接にCO2を回収し、CO2を除去した海水は海に戻す。海水を汚染したり、海水温を変えることもない。
日本では日本の海洋研究開発機構(JAMSTEC)を中心にDOCに取り組んでいる。海水に電気透析をして酸性の海水を作る。酸性になった海水からは高濃度のCO2が発生するため、DACシステムを使い回収する。使用する電力は洋上風力発電を使い、回収したCO2は定期的に輸送船で運搬する構想である。
現在、清水建設と共同で装置の大型化を研究しており、2025年ごろからプロトタイプでの実験を始め、2040年頃の事業化をめざしている。課題は低コスト化で、海水のくみ上げや循環でポンプを使うほか、海水に含まれる金属イオンなどの不純物の除去も必要であり、現状ではDACよりも高コストとなる。
一方、DOCは水産業にも利点がある。CO2が除去されて酸性度が下がった海水を放出すると、周辺海域の海洋酸性化を解消できる。貝などの養殖場の近くで装置を稼働させれば、海洋酸性化の影響で貝殻が溶け出したり成長が遅くなったりするのを抑えられる可能性がある。

2024年11月、キャプチュラは2026年にも「ダイレクト・オーシャン・キャプチャー(DOC)」を商用化する。同社には日本航空(JAL)や日立製作所のベンチャーキャピタル(VC)も出資しており、日本での展開も計画する。また、サウジアラビアの国有石油会社サウジアラムコや北欧石油大手のエクイノールのVCも出資している。
2025年初め、同社はエクイノールと数百万ドルを投じて実証の最終段階となる大規模プラント(1000トン/年)をハワイで稼働させ、飲料工場や養殖業者などに販売する。2026年の商用段階では回収量を1万トン超に増やし、プラントは原子力発電所や洋上風力に併設し、余剰電力を動力に使う。
課題は回収コスト低減で、キャプチュラのDOCプラントは商用化段階でも数百ドル/トンとなる見通しで、政府の補助がないと収益化は難しい。米国カリフォルニア大学ロサンゼルス校(UCLA)発の新興エクアティックも、2026年にもカナダで商用プラントを稼働させ、10万トン/年のCO2を回収する計画である。
ブルーカーボンによるCO2固定
2009年10月に国連環境計画(UNEP)の報告書で、大気中から海洋生態系に取り込まれたCO2が「ブルーカーボン」と命名された。ブルーカーボンの活用は、海の豊かな生態系を育成するだけでなく、「グリーンカーボン」と共に、大気中のCO2を捕捉して吸収する「ネガティブエミッション技術」の一つとして有効である。
ブルーカーボンとは?
ブルーカーボンとグリーンカーボン
2009年10月に国連環境計画(UNEP)の報告書において、大気中から海洋生態系に取り込まれたCO2が「ブルーカーボン」と命名された。これは森林などの陸域生態系に取り込まれたCO2が「グリーンカーボン」と呼ばれることに対比して付けられた名称である。
このブルーカーボンを捕捉して貯留する海洋生態系は、「ブルーカーボン生態系」と呼ばれる。国内での森林によるCO2吸収量は2022年度に約450万トンとされているが、人工林の高齢化により減少する見通しであり、森林よりも長期間にわたり炭素を固定し続けると考えられている。
ブルーカーボン生態系
■ 海草藻場:アマモ、スガモなど、主に温帯~熱帯の静穏な砂浜、干潟沖合の潮下帯に分布
■ 海藻藻場:コンブ、ワカメ、主に寒帯の沿岸域の潮間帯から水深数十mの岩礁海岸に分布
■ 湿地・干潟:海岸部に砂や泥が堆積し勾配がゆるやかな潮間帯で、水没~干出を繰り返す
■ マングローブ林:熱帯・亜熱帯の河川水と海水が混じり合う汽水域で砂~泥質の環境に分布
(国内では鹿児島県以南の海岸に分布し、従来からCO2吸収源として報告している)
出典:国土交通省
植物プランクトン、海草や海藻などの植物は、光合成によって海水中のCO2を有機物として固定する。そのため、海水中のCO2濃度が減少し、大気から海水へCO2が吸収・貯留される。
特に注目されるのは、海洋面積の0.5%以下にすぎない沿岸浅海域が、海洋全体のCO2貯留ポテンシャルの80%近くを占める点である。また、沿岸浅域の単位面積当たりのCO2の吸収速度は、森林生態系に比べて5~10倍も高いことから、ブルーカーボンが注目されている。
日本は国土は小さいため陸域生態系でのCO2貯留ポテンシャルには限界があるが、海岸線の長さと海洋面積はともに世界6位であり、ブルーカーボンを手掛ける余地は大きい。
ところで、森林は長期的に木としてCO2を貯留するが、海洋生態系ではCO2の貯留のメカニズムが異なる。海草や海藻は光合成により大気中のCO2を吸収するが、短期間で枯れてしまうためである。
光合成によって海草や海藻などの海洋生態系に有機物として固定されたCO2の多くは枯れて大気中に放出されるが、枯れた後に海底に堆積物として長期間貯留される分がある。また、海藻の成長過程において生成された難溶解性有機物は、外洋に運ばれて海中や海底に長期間貯留される。

海洋におけるネガティブエミッション技術
ネガティブエミッション技術(NETs)は、大気中のCO2を回収・吸収し、貯留・固定化することで、現状よりも大気中に含まれるCO2濃度を下げる(負にする)ための技術である。
ブルーカーボン生態系が保有するCO2の吸収・貯留の能力を、人為的に加速・増大させる取り組みも、ネガティブエミッション技術といえる。
海洋生態系を利用したネガティブエミッション技術
■沿岸ブルーカーボン生態系利用:CO2の吸収・貯留の能力が高い生態系の新たな創出
■外洋大型藻類の養殖:高い成長速度の大型藻類の養殖と、深海へのCO2の輸送貯留
■鉄分散布による海洋肥沃化:外洋域への鉄分散布による植物プランクトン成長促進
■海洋深層水の人工湧昇:栄養分に富む深層海水の汲み上げによる生態系の成長促進
■微生物ポンプ:植物プランクトンが生成した有機物を微生物により難分解化させる
等など 出典:産業技術総合研究所
なお、記載された技術が全て実現可能ではなく、海洋肥沃化などは現状では国際条約によって実施が規制・禁止されている技術で、将来展開が期待される。
また、ブルーカーボン以外のネガティブエミッション技術として、海洋がCO2を吸収・貯留する物理化学的な性質・能力を利用する技術で、海洋隔離・海底貯留、アルカリ化、再生可能エネルギーによる電気化学反応によるCO2固定などの検討も行われている。

ブルーカーボンの取り組み
国内のブルーカーボン生態系は、海草藻場(620㎢)、海藻藻場(1720㎢)、塩性湿地(470㎢)、マングローブ林(30㎢)であり、CO2吸収量は合計で132~404万トンCO2/年と推定されている。最大の海藻藻場は、天然藻場が主たる算定対象である。
従来、日本は温室効果ガスインベントリに海域は含めておらず、湿地ガイドラインによる沿岸湿地の算定を行なってこなかった。そのため、2017年に学識経験者及び関係団体等で構成される「ブルーカーボン研究会」が設立され、ブルーカーボン生態系によるCO2吸収量の推計について研究が始まった。
2019年、国土交通省港湾局海洋・環境課を中心に「ブルーカーボン生態系の活用に向けた取組の推進~地球温暖化防止に貢献するブルーカーボンの役割に関する検討会の設置~」が行われ、ブルーカーボンをCO2吸収源として活用していくための具体的な検討が進められた。
2020年7月、国土交通省認可法人のジャパンブルーエコノミー技術研究組合(JBE)が設立され、ブルーカーボン生態系とその他の沿岸域・海洋における気候変動対策への取組みを加速すため、ブルーカーボンクレジット化に向けた制度設計が行われ、クレジットの認証や発行手続きをおこなう。
2024年4月、環境省は、2022年度の温室効果ガス排出・吸収量は、約10億8500万トンCO2で、2021年度比で2.3%(約2510万トン)の減少、2013年度比では22.9%(約3億2210万トン)の減少を国連に報告した。特に、ブルーカーボンについて合計約35万トンの値を報告したことが特筆される。
ブルーカーボンは、2021年度のマングローブ林による吸収量の算定・報告に加え、国土交通省(面積データ)、農林水産省(藻場タイプ別の吸収係数)との連携により、世界で初めて海草・海藻藻場の吸収量を合わせて算定・報告した。今後は、塩性湿地・干潟の算定についても検討していくとした。
ブルーカーボンクレジット
Jブルークレジットの仕組み
「Jブルークレジット®」は、国土交通省認可法人のジャパンブルーエコノミー技術研究組合(JBE) が独立した第三者委員会による審査・意見を経て、認証・発行・管理する独自のクレジットで、2020年度に始まった。
JBEでは、一般的な国際標準とされる100年間以上の長期にわたり沿岸域・海洋に貯留されるCO2の数量を客観的方法論に基づき科学的合理的に算定し、これを認証・発行している。
クレジット創出者(NPO、市民団体など)は、ブルーカーボン生態系の再生や創出の活動資金を獲得できる。一方で、クレジット購入者(企業、団体など)は、CO2排出権を買う(オフセット)できるだけでなく、海の環境保全活動に貢献できる。

CO2貯留量の算定式について
科学的知見に基づくクレジット認証のためには、CO2貯留量を正確に見積る必要がある。そのため海洋観測技術の開発や、ブルーカーボンの貯留メカニズムの解明に関する研究が進められた。
その結果、海草・海藻藻場のブルーカーボン貯留量評価モデルが農林水産技術会議プロジェクトでまとめられ、式1で示す藻場のCO2貯留量の算定式が示された。
植物プランクトン、海草、大型藻類、マングローブなど光合成生産の出発点となる植物、有機物の堆積や外洋への流出、大気と海洋でのCO2の交換速度などプロセスが複雑で、海域によっても吸収係数は異なる。そのため各係数の詳細は、「海草・海藻藻場のCO2貯留量算定に向けたガイドブック」にまとめられた。
最終的には、科学的な根拠に基づいて、自国や自社に不利にならない算定法を提案し、それを公的なものとして国連に報告しているのが現状である。国連による算出方法の検証を経て、正式にインベントリとして認められるかどうかが決定される。

2024年4月、環境省が国連に報告する温暖化ガスのインベントリ(排出・吸収量)に、海藻・海草由来のブルーカーボンを世界に先駆けて取り入れた。脱炭素対策の有効な手法として注目が集まり、ブルーカーボンクレジットの動きが国内でも始まっている。
具体的なクレジットの売買状況
2009~2012年に、国交省関東地方整備局が造成し、その後、横浜市漁業協同組合や海辺つくり研究会、金沢八景-東京湾アマモ場再生会議が、様々な活動によって藻場の保全を続けてきた。
2017年度、ドローン撮影により藻場の面積が把握できたため、1年間のCO2吸収量が算定された。クレジットの対象は、横浜港にある横浜ベイサイドマリーナ横の約16ヘクタールの藻場である。
JBEが運営事務局となり、第三者機関による審査認証委員会を設けて審査・認証が行われた結果、Jクレジットの発行量は22.8トンCO2であった。JBEが申請した50.8トンCO2の半分程度の評価であるが、海の中の不確実性などを踏まえて過剰評価とならないよう吸収係数が設定された。
Jブルークレジット購入者は、住友商事、東京ガス、セブン-イレブン・ジャパンの3社で、総量配分方式により購入金額に応じてクレジットが配分された。各社の購入金額は明かにされていない。
森林など陸域生態系のグリーンカーボンに比べて、CO2吸収量の定量化が難しいブルーカーボンクレジットの普及は遅れ気味である。
しかし、2020年度の実績は1ヶ所/22.8トンCO2であったが、2022年度は21ヶ所/3,733トンCO2、2023年度は29件/2170.3トンと拡大しており、商船三井、東京海上日動火災保険、東京ガスなど100社以上が購入した。
JBEによれば、ブルーカーボンクレジットの取引価格は5万~10万円/トンCO2で生物多様性確保などの環境価値が評価され、森林由来のグリーンクレジットの5~10倍以上高値で取引されている。
ブルーカーボン関連の活動状況
最近になり、国内でもブルーカーボンに関連した製品開発や事業参入の発表が相次いでいる。
2022年11月、日本製鉄は、森から海に供給される鉄分を鉄鋼スラグ製品「ビバリーユニット」(鉄鋼スラグと廃木材チップを発酵させた腐植土を原料とした鉄分施肥材)を開発し、2004年から全国38カ所の沿岸へ提供を進めてきた。今回、全国6カ所の漁業協同組合と協業して新たな設置試験の開始を発表した。
日本の沿岸海域では、過去数十年にわたり磯焼けという海の砂漠化が進み、鉄分をはじめとする栄養塩の不足が原因の一つとされていた。「ビバリーユニット」の適用海域では藻場が再生・回復し、漁獲高向上の効果も報告され、ブルーカーボン推進の観点からも有効であることが分かってきた。
また、日本製鉄は、北海道増毛町で増毛漁業協同組合と共同で、2004年から海藻藻場の造成事業に取り組み、Jブルークレジットから、直近5年間の2018~2022年に吸収・固定化されたCO2量として、49.5トンCO2の認証発行を受けた。
2023年2月、電源開発は、オーストラリアのセントラルクイーンズランド大学と 地域産出の産業副産物を多量に使用した低炭素素材(コンクリートの代替材料)を開発し、海洋ブロックとして実装することで、同素材表面に付着する海藻類によるブルーカーボンの実証試験を行うと公表した。
2023年11月、東洋製缶グループHDは「イオンカルチャー(藻類増殖材)」を製品化し、2023年度中に地方自治体などに向けた販売を開始すると発表。港や岸壁の消波ブロックの表面に貼り付けて海藻の成長を促すことで、ブルーカーボン生態系が構築されることを期待している。
イオンカルチャーは、海洋植物の成長を促進する二価鉄、ケイ酸、リン酸イオンなどの成分が、ゆっくりと水に溶け出すよう成分調整を行ったガラス製品で、不動テトラと共同開発し1993年に製品化された。
2023年には高性能なイオンカルチャーの開発に成功し、従来品は溶け切るまでに約10年を要したが、成分調整により約3年で溶け、光合成促進効果の向上や有効範囲の拡大が見込める。
2023年11月、電源開発は、北九州市と連携して「北九州港港湾脱炭素化推進協議会の特別講演会(2023年11月29日開催)」をゼロ・カーボン会議とすると発表。会議開催で発生するCO2(9.1トンCO2)を、北九州市内で実施したプロジェクトで認証を受けたJブルークレジットでオフセットする国内初の事例である。
Jパワーの茅ヶ崎研究所は、北九州市若松総合事業所の構内で、Jブルーコンクリート(産業副産物を多量に活用した低炭素素材)を用いた消波ブロックによるブルーインフラ整備を進めており、同ブロックに付着した海藻が吸収するCO2をJブルークレジットとして認証を受けている。
2024年2月、ENEOSは、産官学で2040年までに100万トン超/年のブルーカーボン創出をめざすと発表。参画するのは、港湾空港技術研究所、海洋研究開発機構、産業技術総合研究所、東京大学で、2025年度までに海藻・海草の種類などを詰め、2026年度以降にENEOS事業所の護岸などで実証を始める。
これまでENEOSは、磯焼けの原因の一つであるウニを除去することで藻場の再生を進めるウニノミクス(東京・江東)や、養殖を起点に海洋の計測技術を手掛けるウミトロン(東京・品川)のシンガポール法人などに出資しており、これら出資先の技術も取り込みビジネスモデルを構築する。
2024年6月、海洋事業等を展開する岡部は、ブルーカーボン事業への参入を発表。2023年9月より島根県隠岐郡海士町の海域で、海藻種苗培養技術を生かした「多段式養殖施設」を設置して検証試験を実施している。沿岸浅場から30m以上の深場まで、種類の異なる大型褐藻の収穫量の増大が期待される。
2024年9月、大阪府阪南市の沿岸部から約100〜400mの沖合で、日立製作所、月島JFEアクアソリューション、大阪公立大学など18の企業や団体、自治体が産官学連合でブルーカーボン創出の実証を進めている。下水処理後に海に放流される水の栄養価を高めることで、周辺域の海藻を増やす試みである。
日立製作所は下水処理工程の微生物濃度や送り込む酸素の量などを調節して、栄養塩濃度を適切に制御し、月島JFEアクアは下水処理水由来の栄養塩類を必要な箇所に届ける放流方式、KDDIは水中カメラを使って藻場の生育状況を精度高く計測できるシステムの活用を進める。
実際に下水処理場で栄養塩濃度を高めて放流するのは自然界への影響が大きいため、自治体や漁業関係者などとの調整が必要である。
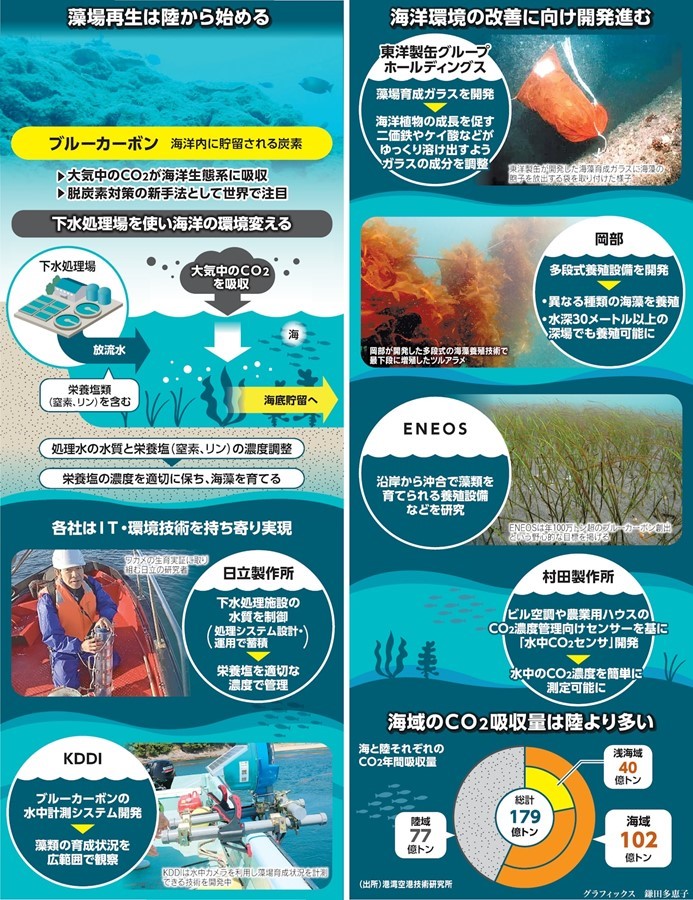
2024年10月、ブルーカーボン事業で出光興産や商船三井など約10社が連携する。東京海上アセットマネジメントが主催し、鉄鋼メーカー、地方銀行、富士通、日建工学などが定例で情報交換会を行う。漁業組合との交渉ノウハウ、沖合に出る際の課題を共有し、海藻の生育を監視する技術の開発・共同導入などを行う。
2024年10月、健康食品や化粧品を手掛けるヴェントゥーノは、福岡県糸島市や糸島漁業協同組合と組み養殖したワカメが吸収するCO2について、2025年12月にもクレジット(排出枠)の認証取得をめざす。同社の健康食品などの原料になる海藻を作る過程でCO2の吸収効果が生じると見込みで、今後、吸収量を算定する。
2024年10月、富士通は、ブルーカーボン事業で新会社「BLUABLE(ブレアブル)」を設立した。社内の新規事業創出プログラムから生まれた出向企業で、海藻が集まる藻場の造成に向けて全国16か所の海域で実証実験をし、2025年10月から商談開始をめざす。
ブルアブルは藻場の造成から、海藻類によって海底に吸収・埋没されるCO2の測定、そのCO2吸収量を認証する「Jブルークレジット」の申請まで一貫して手掛ける。提供する「藻場造成キット」は、海藻が着生しやすい物質を海へ投下するだけで藻場が造成でき、従来の藻場造成方法と比較して短期間で安価に導入できる。
2025年5月、中部電力、中部電力ミライズ、三井住友海上火災保険は、「ブルーカーボン」のサービス事業化で合意書を締結。中部電力は愛知県田原市や三重県志摩市で藻場の再生を進めており、吸収するCO2算定方法を開発し、回収分をカーボンクレジット(排出枠)として、金融サービスの提案につなげる。
海外におけるブルーカーボンの動向
ブルーカーボン生態系を多く保有するオーストラリアや米国は、ブルーカーボンの研究が積極的に進められている。しかし、世界的にマングローブ林が主たる対象となっており、オーストラリアなどが国連の認定を得ている。しかし、海藻・海草に関しての実績は、ほとんどないのが現状である。
一方、欧州委員会では、水資源に関わる経済活動や「ブルーエコノミー」の観点から、海藻養殖や海洋資源としての海藻の利活用に向けた取り組みが主体である。
豪州、米国、英国、マルタの4か国では、ブルーカーボン生態系による温室効果ガス排出・吸収量を算定・報告しており、ブルーカーボン先進国といえる。
一方、海外では、ブルーカーボンの「ボランタリークレジット制度」が整備されてきている。ボランタリークレジットは、NGOなどの民間セクターが認証するカーボンクレジットの仕組みである。
国内JBEも、「Jブルークレジット」によるCO2の吸収・貯留だけでなく、それに伴う漁獲量の増加や水質浄化、生物多様性の増加などの利益も含めた「ボランタリークレジット」を発行している。
以下には、ブルーカーボン生態系を多く有する国々での、ブルーカーボン生態系の特徴や取り組みがについてまとめる。
オーストラリア
オーストラリアのブルーカーボン生態系は、海草藻場の面積は世界1位(52,051㎢)であり、マングローブ林の面積が世界2位(9,780㎢)、塩性湿地の面積が世界2位(13,259㎢)と、ブルーカーボン大国といえる。
温室効果ガス排出・吸収量としてマングローブ植林、塩性湿地の消失、海草藻場の消失について算定しており、年間のCO2吸収量は約30万トンCO2である。
2015年12月のパリ協定が採択された中に、オーストラリア政府が中心となり「International Partnership for Blue Carbon」を設立した。
オーストラリアは、「気候変動に関する政府間パネル(IPCC)」の湿地ガイドラインを用いてブルーカーボン(沿岸湿地に関連)を自主的に報告しており、ブルーカーボン生態系によるCO2排出量削減の数値目標を示している数少ない国の一つである。
一方で、オーストラリアは、膨大なブルーカーボン生態系を保全することでクレジットを創出し、自国のCO2排出のオフセットに利用することで、火力発電などによるCO2排出量削減には非協力的との批判もある。
米国
米国のブルーカーボン生態系は、塩性湿地の面積が世界1位(18,849㎢)である。IPCCの湿地ガイドラインを用いてブルーカーボン生態系としてマングローブ、干潟の創出・消失について算定しており、年間のCO2吸収量は約1,000万トンCO2である。
近年、非営利団体「Restore America’s Estuaries (RAE)」を中心にした多くの湿地再生プロジェクトが、米国海洋大気庁(NOAA)も協力して進められている。
また、マサチューセッツ州ヘーリング川河口部の再生活動に関して、カーボンオフセットプロジェクトによるボランタリークレジットの実証試験(Voluntary carbon market)が実施されている。
中国
中国沿岸では、1950年~現在までにマングローブ、塩性湿地、海草藻場などのブルーカーボン生態系は9,236~10,059㎢が消滅し、現在、天然のものが1,326~2,149㎢、再生・造成されたものが2~15㎢ある。また、海藻養殖は1,252~1,265㎢で、天然のものと同程度の面積と報告されている。
年間のCO2吸収量は海草藻場が15.18万トンCO2、塩性湿地が96~272万トンCO2、マングローブが39.9万トンCO2と推定されている。これらは日本とほぼ同程度の規模である。
近年、中国の海藻養殖生産量は約1,800万トンと1位のインドネシアの1,000万トンを引き離して世界一となり、海藻養殖をブルーカーボンとして算入することに関心は高まっている。しかし、養殖された海藻は主に食用であるため、海藻の収量をバイオ燃料生産や土壌改良用のバイオ炭生産に利用する必要がある。
インドネシア
インドネシアのブルーカーボン生態系は、マングローブ林面積が42,550㎢、海草藻場面積が30,000㎢と広大であり、インドネシアのマングローブは世界の23%を占めるともいわれている。マングローブの保全による年間のCO2吸収量は2億トンCO2推定されており、中国についで海藻養殖の生産量が世界第2位である。
ブルーカーボンのポテンシャルが高いインドネシアは当然ブルーカーボンへの関心も高く、インドネシア・ブルーカーボン戦略フレームワークが「国家中期開発計画(RPJMN)2020-2024」で策定されており、開発・計画、海洋政策、漁業、天然資源保全の各担当機関で実施される予定である。
大統領令でも、2045年までに182万ヘクタールのマングローブ生態系を回復させることを目標に掲げており、これを達成するためには年間6万ヘクタールを修復する必要があると数値目標を掲げている。インドネシアはブルーカーボンを国の温室効果ガスインベントリに統合することをめざしている。
しかし、現状ではマングローブの伐採が植林や再生の速度を上回り、減少が止まらないとの指摘がある。