国際海事機関 (IMO)は、2050年までにGHG総排出量を、2008年比で50%以上削減し、今世紀のできるだけ早い段階で排出量ゼロを目指す目標を掲げた。
そのため世界的に船舶のゼロエミッション化に向け、蓄電池を搭載した電気推進システムの推進に加えて、①バイオ燃料、水素、アンモニア、合成メタンなどの新たな次世代船舶燃料の使用と、②新燃料用エンジンの開発、③再生可能エネルギー(風力、太陽光)の援用などの検討が始まっている。
ゼロエミッション船の提案
2018年4月、国際海運における温室効果ガス(GHG)を削減するため、国際海事機関 (IMO)は削減目標や対策をまとめた「GHG削減戦略」を示した。すなわち、2050年までにGHG総排出量を、2008年比で50%以上削減し、今世紀のできるだけ早い段階で排出量ゼロを目指す目標などを掲げた。
その結果、世界的に船舶のゼロ・エミッション化に向けて、蓄電池を搭載した電気推進システムの開発に加え、①バイオ燃料、水素、アンモニア、合成メタンなどの新たな次世代船舶燃料の使用と、②新たなエンジンの開発、③再生可能エネルギー(風力、太陽光)の援用などの検討が始められている。

日本でも、2018年8月に「国際海運GHGゼロエミッションプロジェクト」が立ち上げられ、2020年3月にロードマップが策定された。2028 年までに対 2008 年比で 90%程度以上の効率改善が期待でき、長期的には国際海運のゼロエミッション化の実現を可能とする技術の絞り込みが行われた。
2021年12月、国土交通省はコンテナ船など国際海運に携わる船舶が排出するGHGを、2050年までに実質ゼロにする新目標をIMOに提出した。日本の領海・排他的経済水域(EEZ)は約447万km2あり、世界第6位の海洋国家として国際海運におけるGHG削減の積極的な推進と貢献を目指している。
このロードマップで示されたゼロエミッション船は、図1に示す①水素燃料船、②アンモニア燃料船、③船上CO2回収システム搭載船、④低速液化天然ガス(LNG:Liquefied Natural Gas)+風力推進船の4タイプであり、現在は建造に必要な技術開発が進められている。
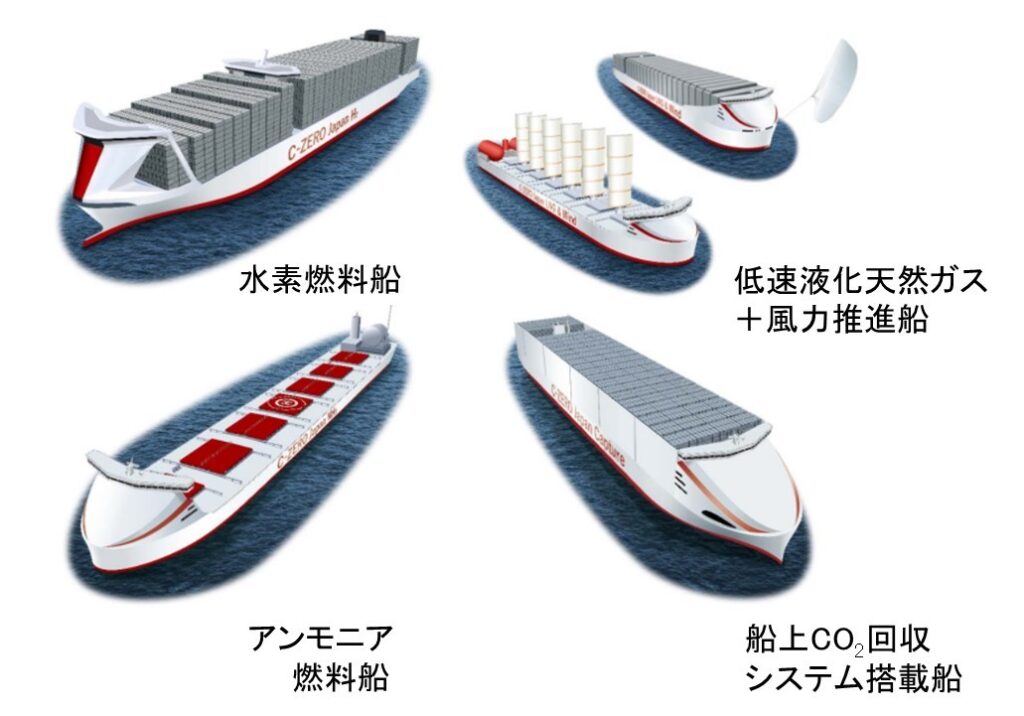
水素燃料船とアンモニア燃料船
水素燃料船とアンモニア燃料船は、使用時にCO2を排出しないクリーンなエネルギーで航行する船舶である。水素・アンモニア燃料の拡大シナリオが、図2(a)(b)のように示されている。
図2(a)のグラフ上端の点線は、対応策を講じなかった場合のGHG排出量(BAU:Business as usual排出量)である。ただし、縦軸にはCO2換算された排出量が示されている。下端の実線は諸対策により2050年ゼロエミッションの目標を達成するCO2排出量の推移を示す。
省エネ技術と運航効率化によるCO2排出量の削減に加えて、水素・アンモニア燃料が十分に供給されると仮定したシナリオであり、水素・アンモニアへの期待度の高さがわかる。水素とアンモニアにはそれぞれ異なる利点と課題があり、現時点でいずれが優位であるかの判断は難しいとしている。
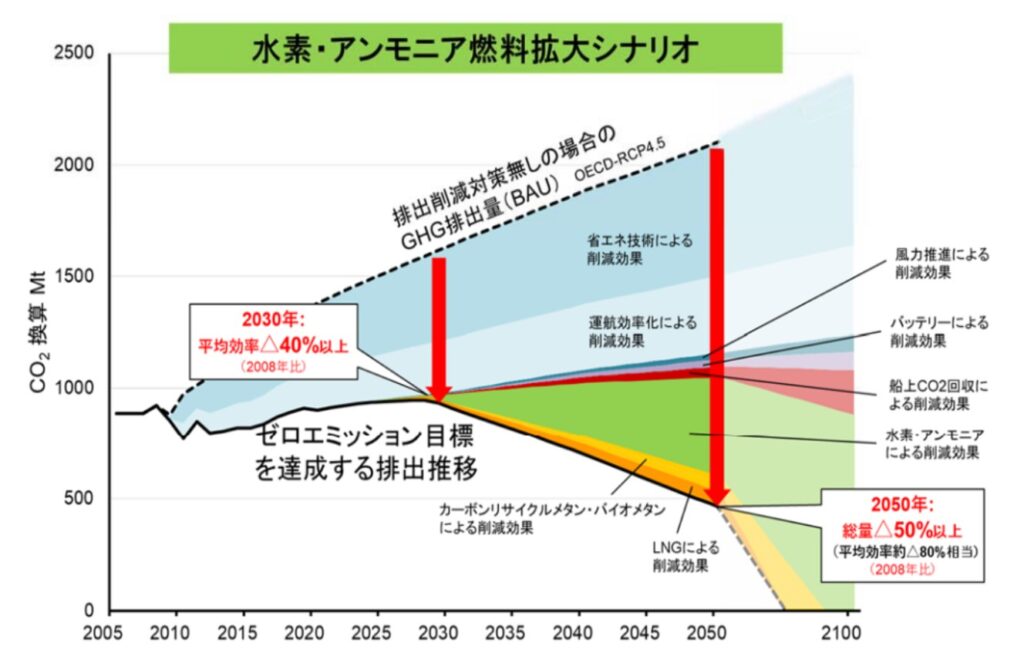
また、図2(b)にはエネルギー消費量に占める各燃料などの割合を示している。本シナリオにおいては、先行してLNG 燃料の使用が拡大すると仮定しており、次に示す合成燃料やバイオ燃料(カーボンリサイクルメタン・バイオメタン)とともに、CO2排出量の削減が見込まれている。
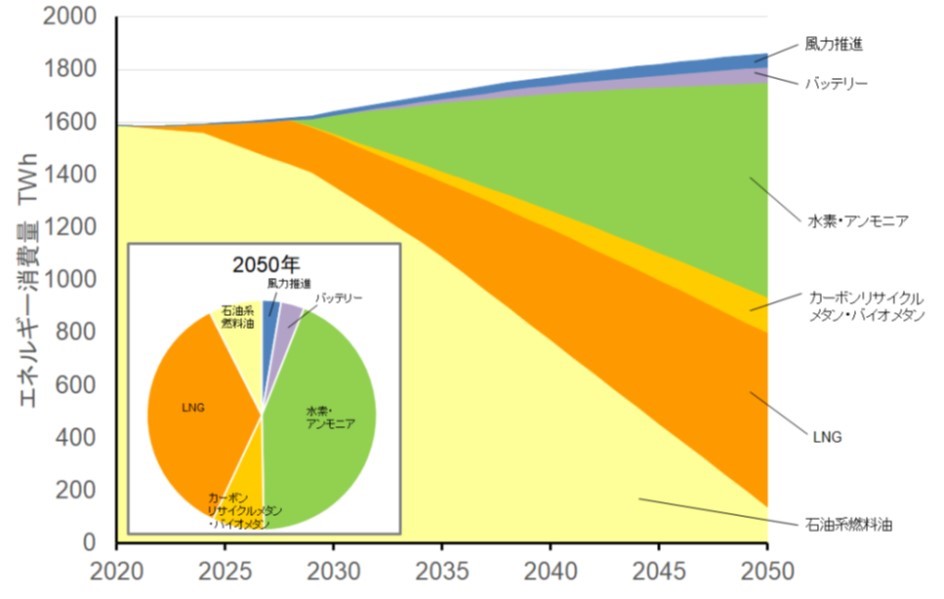
船上CO2回収システム搭載船
船上CO2回収システム搭載船は、陸上で実用化されたCO2回収装置を搭載してCO2排出量ゼロを目指す。将来的には回収したCO2を原料とするカーボンリサイクル燃料の導入で、ゼロエミッション化を目指す。LNG→カーボンリサイクルメタン移行シナリオが、図3(a)(b)に示されている。
図3(a)のように、省エネ技術および運航効率化によるCO2排出量の削減に加えて、カーボンリサイクルメタン・バイオ燃料が十分に供給されると仮定したシナリオである。カーボンリサイクルメタン燃料とバイオ燃料は、いずれもカーボンフリー燃料である。
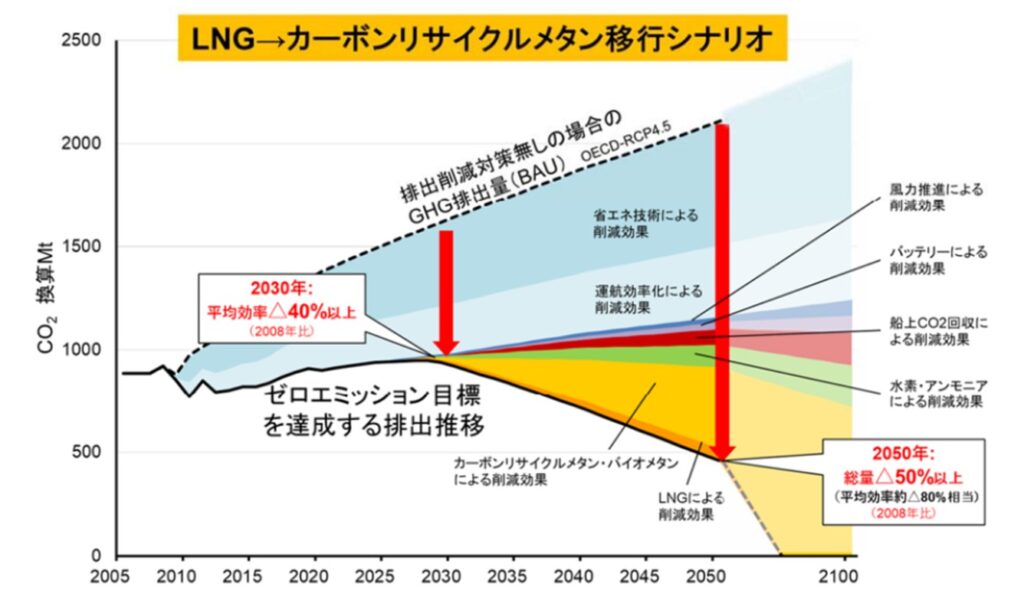
LNG 燃料がCO2 削減に及ぼす割合は大きくないが、図3(b)で示すように国際海運のエネルギー消費に占める割合は大きい。これはLNGの単位熱量あたりのCO2排出量が、対C重油比で0.74 と比較的多いことに起因する。
LNG燃料を使用することによるCO2削減効果は限定的であるが、LNG燃料の普及が2025 年以降のカーボンリサイクルメタン・バイオメタン燃料の導入の土台になると考えられている。
2050年以降においても主力のガス燃料として期待されるLNG・カーボンリサイクルメタン技術に関しては、未燃のままメタンが大気中に排気される「メタンスリップ」の問題がある。メタンはCO2に比べて25倍の温室効果があるため、メタンを排ガスから除去する技術の開発が必須とされている。
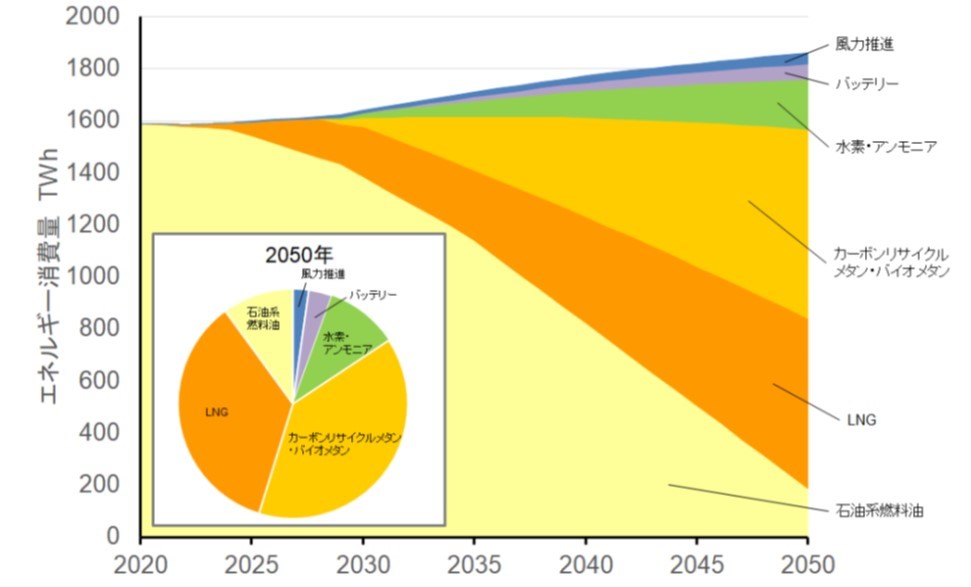
低速液化天然ガス+風力推進船
低速液化天然ガス+風力推進船は、現在主流である船舶用重油に代えてLNG燃料を採用し、再生可能エネルギーである風力推進などの技術を組み合わせてCO2排出量の削減率を高める狙いである。
図4には、「国際海運GHGゼロエミッションプロジェクト」での検討結果を示す。緑色は 2028 年までに実用化可能、黄色は技術開発課題が比較的小さく 2028 年までに実用化の可能性があるとしている。これらの検討結果を基に、図1の4タイプのゼロエミッション船の開発構想が示されたのである。
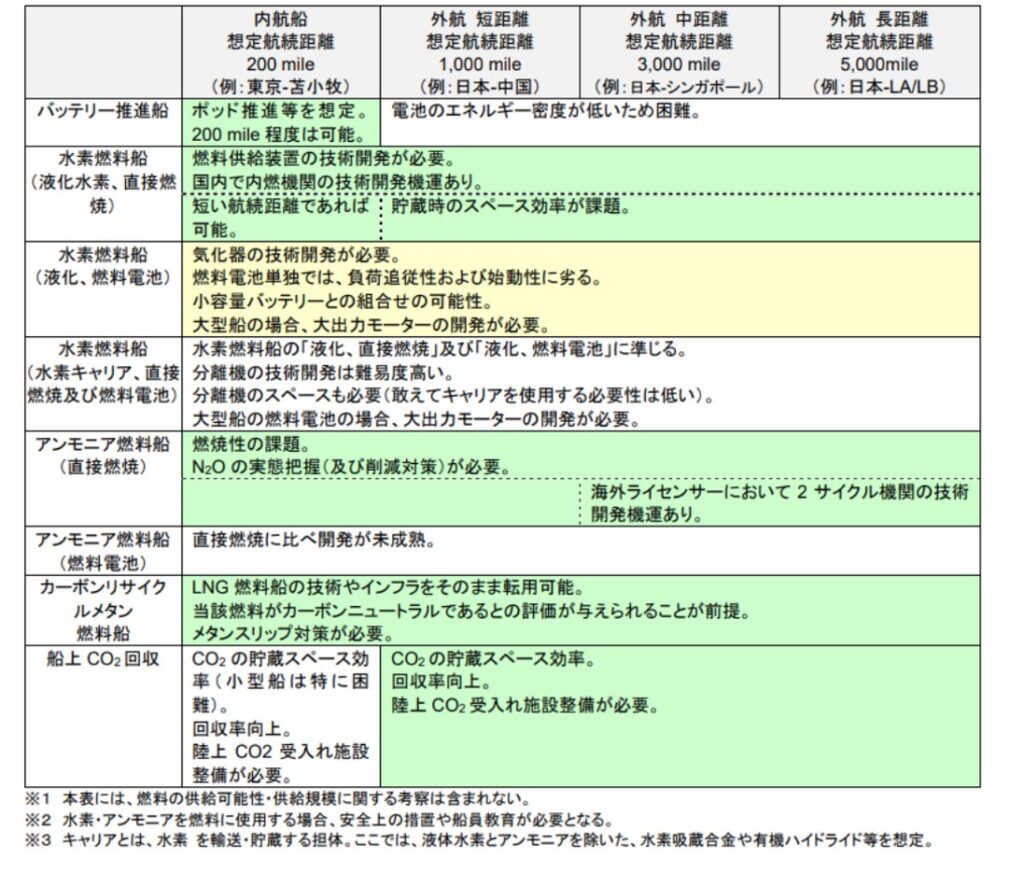
ゼロエミッション船の実現ロードマップ
ゼロエミッション船を実現するためのロードマップが、図5に示されている。2050 年目標達成に向けて、2028~2030 年の期間を、対 2008年比で90~100%の効率改善を達成するゼロエミッション船の投入開始時期としている。
これに向けて、研究開発、技術の実証及び導入促進を順次進めるとともに、ゼロエミッション船の建造・運航のための環境整備として、関連ルールの検証・策定・改正も並行して進める必要がある。
2030 年以降は、ゼロエミッション船の普及フェーズとなることを想定しているが、代替燃料の普及促進のためには、陸上における燃料供給体制の整備が必要としている。
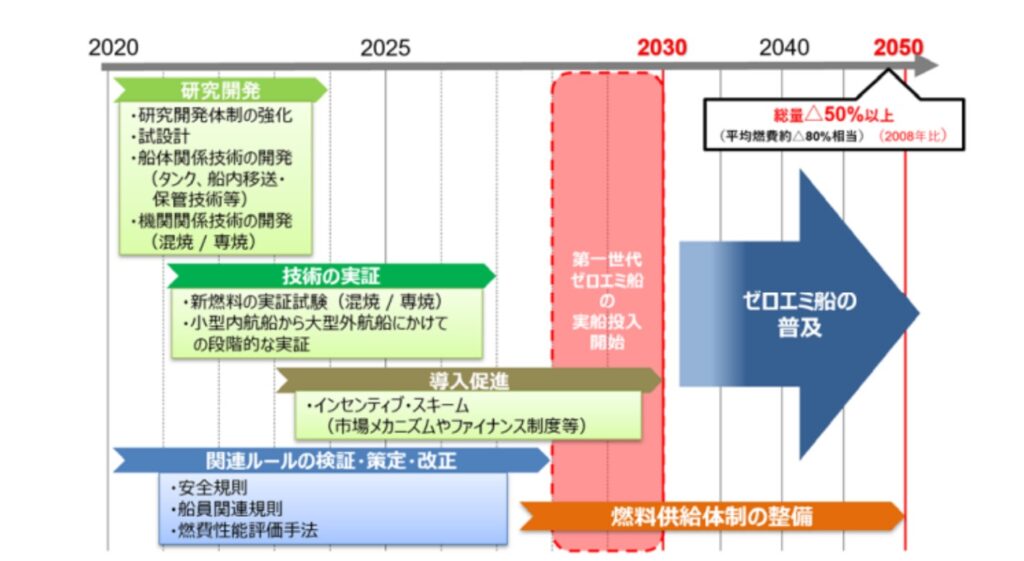
2022年7月、国土交通省はゼロエミッション船の技術開発に10年間で総額350億円を財政支援すると発表した。アンモニア燃料船は2026年、水素燃料船は2027年からの実証運航を計画し、アンモニア燃料船は2028年までに、水素燃料船は2030年以降の商業運航を目指す。
ゼロエミッション船の開発や導入にあたり、造船や海運各社は長期の低利融資が受けられる。
国土交通省や日本船主協会によると、ゼロエミッション船を年間100隻ほど建造する場合、建造費用は1隻あたり約100億円と想定する。年平均で約1兆円かかる計算で、関連コストも含めた2025~2050年の総投資額は25兆~30兆円になると推計されている。
水素・アンモニア燃料船
水素とアンモニアはCO2を排出しない脱炭素燃料であるが、コストや供給体制など実用化に向けての課題は多い。水素燃料船の実現を目指して、日本では燃料電池推進船と水素燃焼タービン推進船、欧州では燃料電池推進船、韓国と日本ではアンモニア燃焼タービン推進船の開発が進められている。
開発トレンドは?
一般に水素燃料については、FCEVと同様に高圧水素タンクを搭載した小型水素燃料船の実現の可能性が高いとみられている。すなわち、航続距離に関する要求の低い比較的小型の沿岸・内航船では水素タンク搭載の水素エンジン船が現実的と考えられる。
2021年9月、ヤンマーが開発した燃料電池推進船の動力は、水素を燃料とするトヨタ自動車のFCEV「MIRAI(ミライ)」に搭載されている燃料電池と、高圧水素タンクを船舶用にマリナイズしている。
2025年までの実用化を目指し、燃料電池システムを複数台連結させることによる大容量パッケージを開発し、38フィート(約12m)以上の大型艇への搭載も進める。

2015年10月、ツネイシホールディングス傘下のツネイシクラフト&ファシリティーズと神原汽船、およびベルギー海運大手CMBの3社は、ジャパンハイドロを設立し、2021年6月に水素/軽油混焼エンジンを2基搭載した水素燃料旅客船「Hydro BINGO」(総トン数:19トン)を竣工した。
2021年8月には、水素エンジンを搭載した中大型の水素燃料船を対象に、川崎重工業、ヤンマーパワーテクノロジー、ジャパンエンジンコーポレーションが合弁会社HyEngを設立した。
2023年1月、川崎重工業は大型船舶用の水素エンジンの開発を発表した。2023年度にジャパンエンジンコーポレーション本社工場で実証設備を作り、ヤンマーパワーテクノロジーなども参画し、2024年度に水素貯蔵~水素燃焼の試験を開始して、2027年度に大型液体水素運搬船に搭載する計画である。
エンジン起動時には通常の船舶用エンジンと同じ低硫黄重油を使うが、航行時は水素のみを燃料とする低速・中速・中高速エンジンの開発と、水素供給システムの実証試験を進める。実証設備には水素エンジンのほか、水素貯蔵タンクや配管など燃料供給システム全体を設置する。
2023年7月、ヤンマーパワーテクノロジーは、日本財団の「ゼロエミッション船の実証実験にかかる技術開発助成プログラム」で、水素燃料の内航船舶用の「水素専焼4ストローク高速発電エンジン」を開発すると発表した。小型船舶向けに2024年から陸上実証試験、2026年の実証運航を目指す。
具体的には、少量の着火用バイオ燃料と水素混焼によるパイロット着火式エンジンと、水素専焼による火花点火式エンジンを同時開発する。
また、上野トランステックは、水素エンジン発電機と蓄電池を組み合わせた「水素エンジン対応のハイブリッド電気推進船」を開発し、2025年6月の完成を目指す。全長100m、幅16m、総トン数4500トン、5000kLの石油を運搬する内航大型電動タンカーで、2026年9月に実証航行を計画している。
2024年4月、日本財団は、洋上風車作業船「HANARIA(ハナリア)」の水素燃料電池による航行に成功した。北九州市若松区沖約15kmにある浮体式洋上風力発電実証機「ひびき」への作業員輸送などで活用する。
水素とバイオディーゼル燃料のハイブリッド船で、全長:33m、全幅:10m、重さ:248トン、定員:約100人。商船三井グループなどが出資する「MOTENA―Sea(モテナシー)」などが開発した。
一方で、アンモニア燃料については、船舶エンジン大手のドイツMAN Energy Solutions(MAN、マンエナジーソリューションズ)が、2024年頃までのアンモニアエンジンの実用化を目指している。
2020年4月、MANはアンモニアエンジンを搭載した船舶について、日本の企業連合(今治造船、三井E&Sマシナリー、日本海事協会、伊藤忠エネクス、伊藤忠商事)との共同開発で合意した。保有・運航、アンモニア燃料導入、燃料の供給設備も含めた統合型プロジェクトを進める。
2023年12月、IHI原動機はアンモニア燃料舶用エンジンを完成し、日本海事協会から船級型式承認「往復動内燃機関の使用承認」を受けた。シリンダー直径が280mmの4ストロークエンジンで、2023年4月から太田工場で陸上試験を重ね、最大95%のアンモニア混焼率を達成した。
開発エンジンは、日本郵船グループの新日本海洋社が東京湾内で運航していた液化天然ガス燃料タグボート「魁」を改造した「A-Tug」に搭載される。アンモニア供給装置などを載せ、2024年6月に竣工する。
2024年1月、IHI原動機、日本郵船、日本シップヤード、ジャパンエンジンコーポレーション、日本海事協会が共同で開発中の外航船であるアンモニア燃料アンモニア輸送船(Ammonia-fueled Medium Gas Carrier:AFMGC)が、2026年に竣工する。
AFMGCは主機にジャパンエンジンコーポーレーション製の2ストロークアンモニア燃料エンジンを、補機(船内の電気を賄う発電機を駆動するエンジン)にIHI原動機製の4ストロークアンモニア燃料エンジンを採用する。混焼率は、主機で最大95%、補機で80%以上を目指しており、AFMGC全体としてGHGを80%以上減らす。
2024年8月、日本郵船はIHI原動機と開発した、アンモニアを燃料とする商用船の完成を発表。タグボート運航の日本郵船子会社の新日本海洋社のもと、東京湾で大型船をけん引などの業務を担う。2015年から運用したLNG燃料の商用船「魁」を、アンモニア燃料用にエンジン仕様を変え、2025年4月実証航海を完了した。
2024年11月、船舶用エンジンメーカーのジャパンエンジンコーポレーションは、アンモニア燃料と重油を混ぜて燃やし、エンジンを動かす試験運転が完了した。混焼エンジンの製造に着手しており、初号機は2025年4月からの試験運転を経て、同年9月に完成する。2026年完成予定のアンモニア輸送船へ搭載する。
開発するのは船舶用大型低速エンジンで、試験運転ではアンモニアを最大95%(熱量比)の高い割合で重油と混焼できた。燃焼時に、温暖化への影響がある亜酸化窒素(N2O)の発生を低い水準に制御できる。
ところで、水素とアンモニアにはそれぞれ異なる利点と課題があり、現時点でいずれが優位な燃料であるかの判断は難しい。しかし、いずれも燃料としての最大の課題は低コスト化であり、燃料貯蔵・燃料供給システムの開発も重要で、並行して安全基準の策定などの整備が必要である。
また、水素・アンモニア燃料船は実用化のための技術課題も多い。中でも、水素(H2)は火炎温度が高く燃焼速度が速いため大気中燃焼ではNOxの生成が多くなり、アンモニア(NH3)も燃焼時にNOxが生成されるため、低NOx燃焼技術の開発が必要である。
水素もアンモニアも燃焼時にCO2を排出しないが、化石燃料由来の場合には製造過程でCO2が発生するため回収・貯留の必要がある。また、水を原料に再生可能エネルギーの電力で水素を製造し、窒素と反応させてアンモニアを合成する検討も行われているが、プロセスが高コストである。
電力・水素・アンモニア燃料の棲み分け
図2には、海運会社である日本郵船のイメージする2030年代の電力・水素・アンモニア燃料の棲み分け構想を示す。大型高出力のコンテナ船、貨物輸送船、RORO船などはアンモニア燃料船で、中型の観光船や一般貨物船は水素燃料電池推進船、小型船舶は電気推進船としている。
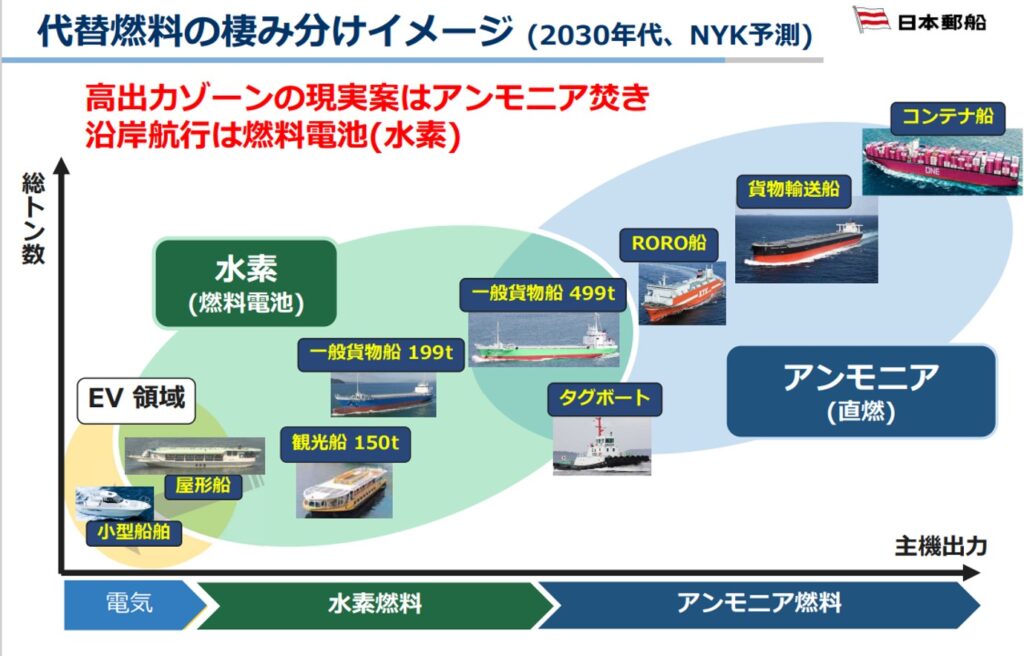
図3には、エンジンメーカーのヤマハHDが示す電力・水素・アンモニア燃料の棲み分け構想を示す。大型外航船はアンモニア燃料船、中型内航船やオフショア船は水素燃焼船、小型の沿岸航行船は蓄電池か燃料電池の電気推進船である。中小型漁船は機械推進エンジンを搭載したバイオ燃料船としている。
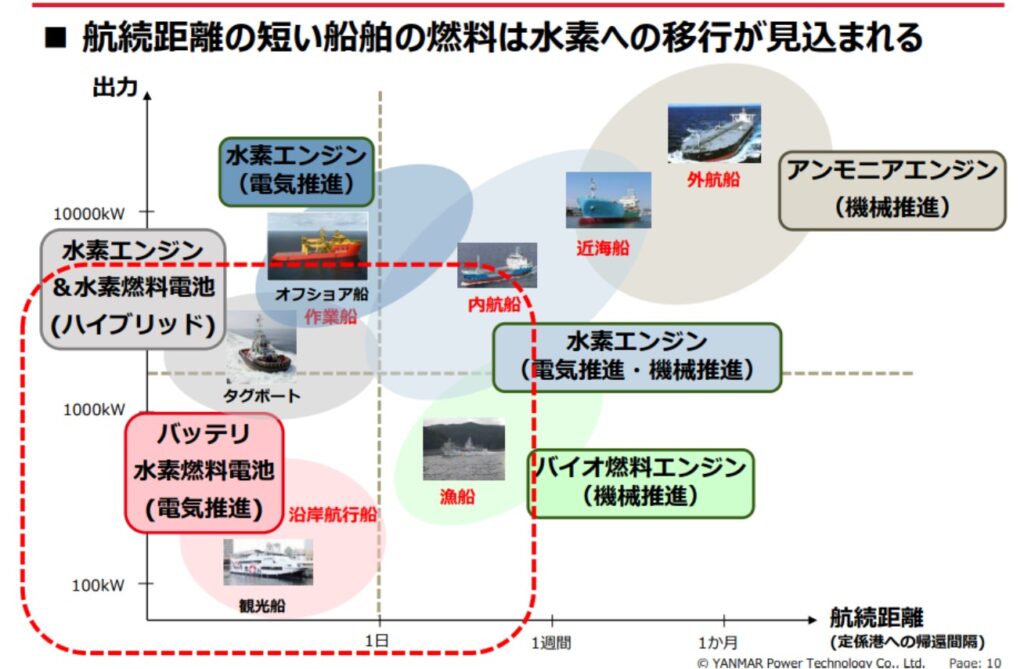
水素燃料船の開発動向
水素燃料船の実現のためには、①水素燃料タンク、②水素燃料供給システム、③水素燃焼エンジンの開発、④水素燃料のサプライチェーン構築が不可欠である。発電用の水素燃焼タービンや水素運搬船の開発で実績のある川崎重工業が、大型水素燃料船の開発で先行している。
水素燃料タンク
小型船については、FCEVで実績にある高圧タンクによる水素貯蔵が経済的に優れている。しかし、長距離運航が主体となる大型船では、液体水素貯蔵が主体になるが、極低温(-252.6℃以下)で貯蔵する必要があるため高コストとなる。
また、液体水素貯蔵でも重油の4.5倍の体積を必要とするため、貨物積載量への影響を最小限とするための船体構造設計や、タンク内で液体水素が気化して発生するBOG (boil off gas)による圧力変動管理対策などが必要となる。
水素燃料供給システム
燃料供給システムにおける水素リークや、構造材料(金属材料)の水素脆化などの問題への安全対策が重要である。加えて、港湾での水素燃料供給設備や大型船向けship to ship方式の水素燃料供給船の建造などインフラ整備も不可欠となるが、国内のインフラ整備は遅れている。
水素エンジン
水素エンジンとしては、燃料電池方式と水素燃焼タービン方式の開発が進められている。
2020年9月、日本郵船、東芝エネルギーシステムズ、川崎重工業、日本海事協会、ENEOSは、高出力燃料電池推進船(PEFC、出力:約500kW)の実用化に向けた実証事業を開始すると発表した。全長25m、幅8m、総トン数:150トン級(乗員数100人程度)の中型観光船が対象である。
2021年から本船・供給設備の設計に着手、2023年から建造・製作を開始し、2024年に横浜港沿岸にて実証運航を開始する。水素供給に至るまでのバリューチェーン全体を取り組みの対象とする。
また、欧州の「HySHIP 」プロジェクトでは、欧州研究助成プログラム Horizon 2020 から800 万ユーロの資金援助を受け、貨物と液化水素コンテナの両方を輸送する液体水素燃料輸送 RORO 船を建造・運航する計画が進められている。
2024 年に進水予定の実証船「Topeka」は燃料電池推進船(PEFC出力:3MW、蓄電池:1MW)で、ノルウェー西海岸に点在する海洋産業の拠点間を往来する貨物輸送手段として定期運航する計画で、25,000 台/年の大型トラック輸送を Topeka が担う計画である。
一方、国内では、発電用の水素燃焼タービンや水素運搬船の開発で実績のある川崎重工業が、大型水素燃料船の開発で先行している。
2021年1月、川崎重工業は液体水素を使う水素燃焼タービンを動力源とする大型運搬船(全長約300m、幅約50m、総トン数:約13万トン)を、2026年度中に完成すると発表した。
大型船の多くは重油燃料のディーゼルエンジンや蒸気タービンが主流であるが、水素を燃やして発生させた蒸気でタービンを回す独自方式を検討しており、最大で4基の液体水素タンク(水素運搬容積:40000m3)を搭載し、建造費は約600億円としている。
また、2021年4月、川崎重工業、ヤンマーパワーテクノロジー、ジャパンエンジンコーポレーションはコンソーシアムを結成し、外航・内航大型船向けの舶用水素燃料エンジンの共同開発を発表した。
基礎燃焼解析、素材、シール技術開発、船級規則対応などの共通技術要素で連携し、川崎重工業が中速4サイクルエンジン、ヤンマーパワーテクノロジーが中・高速4サイクルエンジン、ジャパンエンジンコーポレーションが低速2サイクルエンジンの開発を進め、2025年頃の市場投入を目指す。
2022年5月、川崎重工業は舶用水素ボイラの基本設計を完了した。波の揺動や設置スペースの制限が伴う船舶特有の条件や運用面などを考慮した設計で、このボイラを搭載した液体水素運搬船の推進システムは、日本海事協会から設計承認(AiP:Approval in Principle)を取得している。
開発されたボイラは蒸気タービンや燃料供給システムと組み合わせ、2020年代半ばに計画している大型液体水素運搬船に二元燃料推進システムとして搭載される。
2022年11月、川崎重工業は、水素燃料を使う二元推進エンジンの基本設計を完了し、日本海事協会からAiPを取得した。液化水素運搬中に外気熱で船内タンクが温められて気化するBOGを主燃料とし、着火に必要な低硫黄の重油と混ぜて燃やすことで発電(出力:2400kW)する。
2024年10月、 ヤンマーパワーテクノロジーは、内航船舶向け「発電用パイロット着火式水素4ストローク高速エンジン」の陸上実証試験で、定格出力:約500kWの運転に成功。少量のディーゼル油を点火源として水素と空気の予混合気を燃焼させる方式で、2026年の実証運航に向け船級認証の取得をめざす。
水素燃料のサプライチェーンチェーン構築
水素燃料船実現のために、水素燃料のサプライチェーンチェーン構築は必須であり、鍵となる水素燃料運搬船の開発が進められている。
液体水素は不純物除去が不要で、輸入後すぐに燃料として使える。しかし、比重が0.07g/mm3と軽く、沸点が-253℃と極低温のため、LNG(比重:0.424 g/mm3、沸点:-162℃)に比べ、安全性や断熱性についてより高度の技術が必要となる。
2013年9月、川崎重工業は小型の液体水素輸送船(運搬容積:2500m3)を世界で初めて2隻造り、2020年にオーストラリア・ビクトリア州ラトロブバレーから液体水素輸入の実証試験を開始した。
ロイヤン発電所炭田から産出される褐炭のガス化時に、CO2回収・貯留装置(CCS)によりCO2フリーの液体水素を現地製造し、液体水素を専用船で日本に輸送する計画である。
2016年2月、技術研究組合CO2フリー水素サプライチェーン推進機構(HySTRA)が設立され、岩谷産業(液体水素荷役)、川崎重工業(液体水素運搬船、貯蔵・液化・積荷設備)、シェルジャパン(液体水素運搬)、電源開発(褐炭ガス化)、丸紅(サプライチェーン)が取り組みを開始した。
2019年12月に進水式が行われた世界初の液体水素燃料運搬船「すいそ ふろんてぃあ」は全長116m、長さ109m、幅19m、深さ10.6m、総トン数:約8000トンで、日本海事協会から基本認証を得ており、容積:約1250m3の真空断熱二重殻構造の液化水素タンクを搭載している。
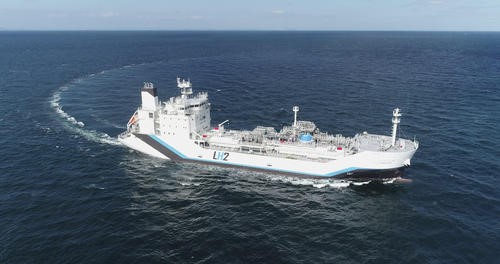
2021年12月、「すいそ ふろんてぃあ」は神戸港を出航し、オーストラリア・ビクトリア州のプラントで低品位の褐炭からガス化・精製された液体水素を積み込んだ。
その後、2022年2月に神戸港に帰港し、水素荷役施設「Hytouch神戸」に陸揚げし、ローディングアームシステムで陸上の液体水素タンク(直径:19m、容積:2500m3)に充填された。
2022年4月、技術研究組合(HySTRA)が、世界で初めて開発した液体水素燃料運搬船の実証に成功したと発表した。しかし、輸入された水素は化石燃料を改質したものであり、安定供給に関する持続可能性とエネルギー自給率の観点からは問題を残すものである。
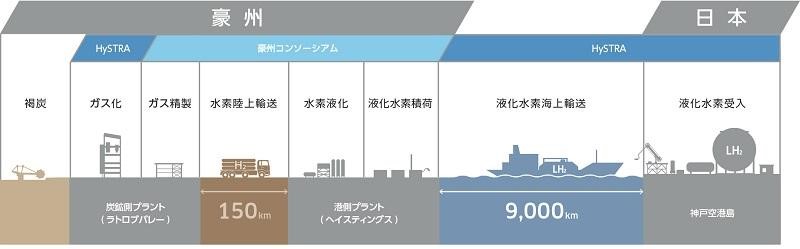
政府は2030年に300万トン/年の水素調達を目指している。大量運搬で水素のコスト低減を図り、現在約170円/Nm3(0℃、1気圧)の供給コストを、2030年に30円/Nm3程度まで下げる計画である。
そのため、2030年までに大型液化水素運搬船(水素運搬容積:160000m3)を2隻造り、サプライチェーンの本格稼働を開始する。2022年8月には、大型液化水素運搬船を受け入れる港湾を神戸港以外にも複数整備する調整に入ると公表した。
一方、欧州でも液体水素燃料のサプライチェーン構築プロジェクトが進められている。2019 年末、ノルウェー政府は、同国電力会社 BKK、Equinor、フランス Air Liquide を中心とした海運用液体水素燃料サプライチェーン構築プロジェクトへ、380万ドルの助成金を決定した。
ノルウェー西海岸のMongstad 産業パークに液体水素製造施設を建設し、2024 年から燃料供給を開始する。また、西海岸沿いのNorSea グループ・サービス拠点に、液体水素の貯蔵施設と燃料供給のターミナルを建設する。海運業の Wilhelmsenは、液体水素燃料運搬船「Topeka」の開発を進める。
アンモニア燃料船/燃料供給船
アンモニア燃料船の実現には、エンジン開発で①難燃性のアンモニアの燃焼制御技術、②排気ガス中のNOx低減対策が必須である。また、③アンモニアの腐食性・毒性対策を施した燃料タンク・燃料供給システムの開発、④重油と比べて大きな燃料タンクが必要で、船体設計から見直す必要がある。
アンモニアは肥料用途などで既にサプライチェーンが存在するが、船舶燃料として低コストで大量の製造(輸入)・貯蔵・供給体制を今後構築する必要がある。アンモニアは激しい毒性を有するため、安全性を確保して社会的な認知を得ることが、アンモニア燃料船の社会実装・普及拡大につながる。
アンモニア燃焼エンジンは、ドイツのMANエナジー・ソリューションズ(MAN Energy Solutions)がアンモニア焚き2ストローク型と4ストローク型のエンジン開発を進めており、2024年までに大型外航船向け、2025年までに既存船向けに改造パッケージの実用化を目指している。
2020年4月、MANと日本の企業連合(今治造船、三井E&Sマシナリー、日本海事協会、伊藤忠エネクス、伊藤忠商事)はアンモニア燃料船の共同開発に合意し、2025年を目途にアンモニア燃料船の保有・運航や舶用アンモニア燃料の導入、燃料の供給設備も含めた統合型プロジェクトを開始した。
MANと三井E&Sマシナリーらが提供するデータを使い、今治造船が貯蔵タンクや燃料供給システムを搭載するアンモニア燃料船の建造、日本海事協会はアンモニア燃料船の安全性を評価する。伊藤忠エネクスは燃料の配給ネットワーク、伊藤忠商事はアンモニア燃料船を保有・運航する。
2021年11月、三菱造船、商船三井、名村造船所はアンモニアを燃料とする大型アンモニア輸送船の共同開発で合意した。アンモニアは肥料原料としての利用が中心で海上輸送量も限定的であり、その増大を目指す。
2022年7月、伊藤忠商事とロッテケミカルが水素・アンモニア分野での協業を発表した。①アンモニアの取引、②日本及び韓国市場でのアンモニアインフラ活用調査、③日本及び韓国でのアンモニア市場調査、④クリーンアンモニア生産設備への共同投資調査、⑤水素分野での協業可能性調査などを行う。
2021年10月、三井E&Sホールディングスは艦艇事業を三菱重工業に売却し、商船事業について常石造船が三井E&S造船を子会社にするなど造船業からの撤退を進め、2022年7月には船舶エンジンや、港湾クレーンを中期計画のコア事業とすると発表した。
既に、アンモニアや水素を燃料とするエンジン開発を進めており、アンモニア燃焼エンジンは2024年3月に完成する。また、同年3月には燃料電池駆動のゼロエミッションクレーンを市場投入する。
2022年9月、日本郵船、ジャパンエンジンコーポレーション、IHI原動機、日本シップヤードは、研究開発中の「アンモニア燃料を使った大型アンモニア運搬船」について日本海事協会から基本設計承認(AiP)を取得し、2026年度の実証運航の実現を目指している。
現時点で、アンモニアを船舶用燃料として利用するための国際規則は存在しないため、4社はアンモニアを船舶用燃料として利用する際の安全性について、HAZID(安全性評価手法の一種)によりリスク評価を実施してAiPを取得している。
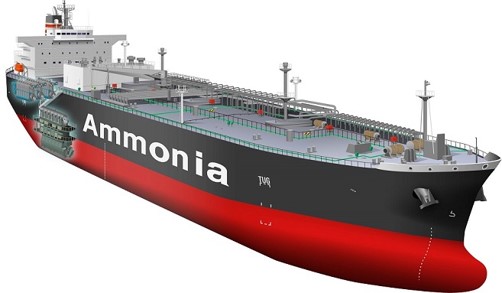
2023年12月、発電用燃料にアンモニアを使用するJERAは、船舶用燃料として日本郵船に販売することを発表。アンモニアの生産は化学大手のレゾナックが担い、他産業へも用途を拡大することで市場の成長を狙う。まずは、日本郵船のタグボート向けに2024年夏に供給する。
一方で、アンモニア燃料船の開発を、韓国の造船各社が積極的に進めている。
2020年7月、現代重工グループはアンモニア燃料船である5万重量トン級のプロダクト船を、ドイツのMANエナジー・ソリューションズ、英国船級協会ロイド・レジスター(LR)と共同開発し、LRから基本承認(AiP)を取得した。2025年の商用化を目指している。
また、2021年9月には、排出ガス中のNOXを除去するアンモニア燃料供給システムのAiPを、韓国船級協会(KR)から取得した。
2022年7月、ベルギーのタンカー大手ユーロナブが、アンモニア燃料を使用する大型原油タンカー(VLCC)とスエズマックスタンカーの共同開発プログラムを、現代重工、LR、ノルウェー船級協会(DNV)と立ち上げた。
また、2020年9月、サムスン重工はアンモニア燃料船のアフラマックスタンカーでAiPを取得した。マレーシア海運大手のMISC、MAN、ノルウェーのヤラ・インターナショナルなどとアンモニア燃料船の共同開発を進め、独自のアンモニア燃料供給システムを開発し、2024年の商用化を目指している。
2021年3月、韓国船級協会(KR)、韓国の造船エンジニアリング企業のKMSとEMEC、シンガポール船社ナビゲイトは共同で、アンモニアと船舶用ディーゼル油(MGO:Marine Diesel Oil)の両方を燃料とする二元燃料機関を搭載するアンモニア燃料供給船を開発している。
CO2回収システム搭載船
1990年代から、火力発電所からの温室効果ガス削減を目的に、ボイラ排ガスからCO2を分離回収して貯留する技術(CCS: Carbon dioxide capture and storage)の開発が進められてきた。
CO2回収システム搭載船は、火力発電用に開発されたCCSシステムを船舶用にカスタマイズしたもので、欧州と日本でエンジン排ガスからのCO2の分離回収実証が行われている。また、回収して貯留したCO2を有効利用するため、日本や北欧では液化CO2の海上輸送船の実証運航が行われている
船上CCS搭載に関する取り組み
2018年、三菱造船がゼロエミッション船構想を公表した。メタンやメタノールを燃料とするエンジンを開発し、航行中に発生するCO2を回収して船内タンクで液状で貯蔵し、寄港時に回収したCO2を使い再生可能エネルギーによる電力でメタンやメタノールを合成して使用するサイクルである。
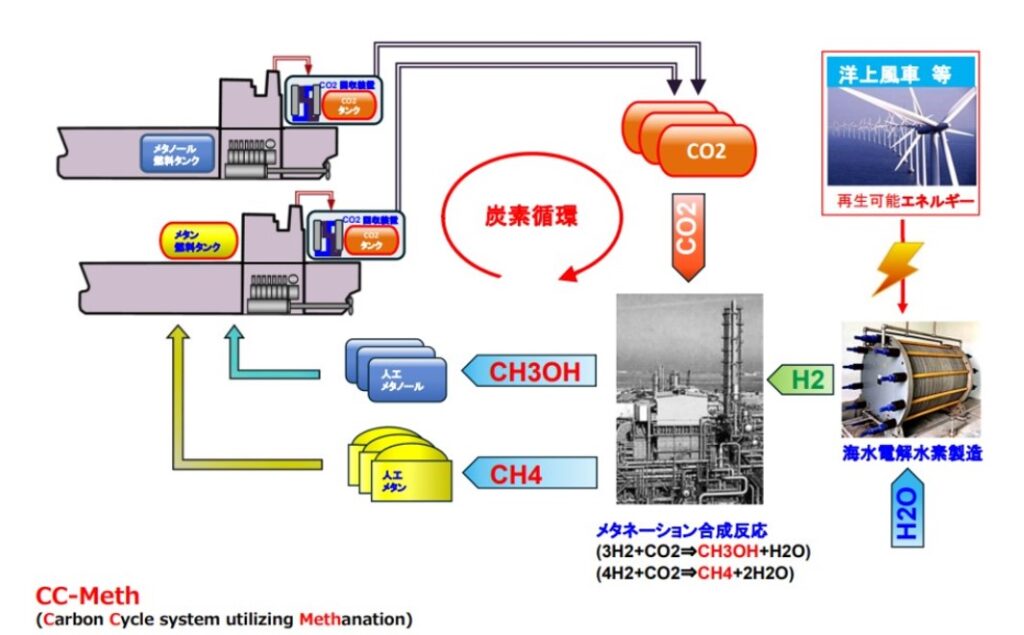
2020年8月、三菱造船、川崎汽船、日本海事協会は、国土交通省の補助事業で陸上用のCO2回収装置を実船搭載して試験運転すると発表した。2年間のCO2回収小型デモプラント(CO2回収能力:0.1t/日)による試験(「CC-Ocean (Carbon Capture on the Ocean)」プロジェクト)である。
三菱造船が液体アミンによる化学吸収法の小型デモプラントを製造して、川崎汽船の石炭運搬船「CORONA UTILITY」(積載重量トン数:8.8万トン)に搭載し、合計7か月間の実証試験を行う。日本海事協会はHAZID(HAZard IDentification:潜在危険および想定災害について判定)検証を行う。
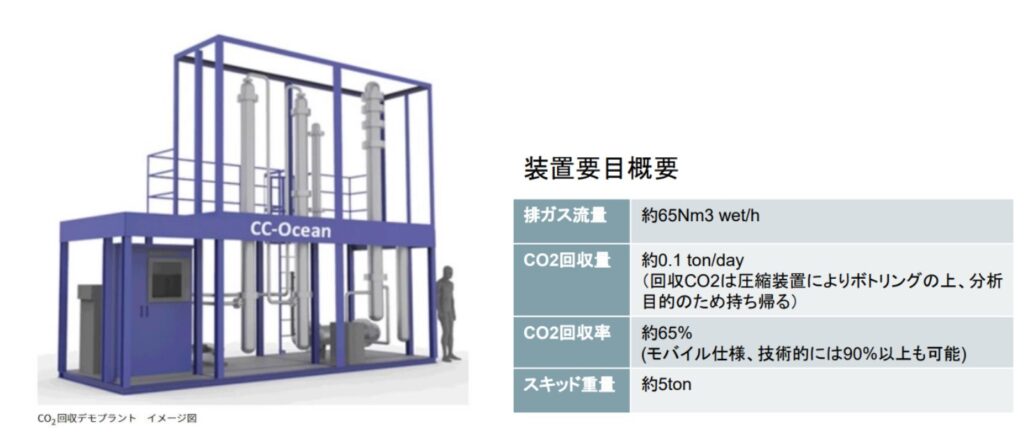
一方、欧州でも船上CCS搭載の積極的な取組が始まり、2019年10月にデンマークの海事研究開発センターを中心に「DecarbonICE」プロジェクトが立ち上げられた。将来的にバイオ燃料などと組み合わせ、排出するCO2よりも回収するCO2の量が上回る「カーボンネガティブ」構想も含む。
2019年12月、日本郵船は「DecarbonICE」プロジェクトへの参加を発表した。船舶から排出されるCO2を運航中に回収してドライアイスに変換し、深海へドライアイスを送り込み、液状や水和物として安全・永続的に海底堆積物中に貯蔵する。
2021年10月、ノルウェーのソルバングは、欧州の舶用機器大手バルチラと共同で、船上CCS搭載の実証試験を行うと発表した。ソルバングが運航する21000m3型エチレン船「Clipper Eos」にパイロットシステムを搭載し、CO2排出量の70%削減を目指す。丸紅も用船者の立場で協力する。
また、2022年7月、ドイツのIonada(イオナダ)はLNG船を対象とする船舶搭載用のCO2回収システムを開発した。モジュラー式のCO2回収システムの特許を取得し、中空糸膜コンタクターを開発・製造・販売する。設置面積は従来の50%で、消費電力は30%に抑えられるとしている。
2022年7月、シンガポール船主イースタン・パシフィック・シッピングは、尾道造船で建造中のMR型プロダクト船2隻に、2023年春までに排ガス浄化装置・CO2回収装置を搭載すると発表した。2週間運航による搭載船からのCO2排出量の40%を回収し、将来的には90%超を視野に入れる。
オランダのエンジニアリング会社バリューマリタイム(VM)と契約し、CO2を特殊な化学物質と反応させ、耐食コーティングを施した燃料油タンクに貯蔵する。この液体化合物は入港時にポンプでくみ上げ、バージまたはトラックでCO2の需要者まで輸送され、長期的には合成燃料を製造する。
液化CO2の海上輸送
脱炭素社会の実現に向けて、船上CCS搭載によりCO2を回収して貯留した後、CO2を有効利用する二酸化炭素回収・有効利用・貯留(CCUS:Carbon dioxide Capture Utilisation and Storage)の開発が重要である。
液化CO2の海上輸送はCCUSバリューチェーンの中で回収地と貯留地、もしくは回収地と有効利用地を効率的に結ぶ手段として重要な役割を担う。日本や北欧ではCO2海上輸送の実証試験が始まっている。
CCS事業化の課題
日本の沿岸域には1500~2400億トンのCO2貯留ポテンシャルがあるとされてる。貯留地点ごとに見ると、数億~数十億トン級のCO2貯留が可能な地点(適した地質条件を持つ)が全国に複数地点あることが、地質の調査から推定されている。
しかし、CO2を多く排出する工業地帯などが主に太平洋側の沿岸域にあるのに対し、貯留に適した場所は日本海側に多く位置している。そのため、日本では工業地帯で分離回収されたCO2はパイプラインなどの陸上輸送ではなく、船舶を使った海上輸送が鍵となる。
また、政府は2050年時点で約1.2億〜2.4億トン/年のCO2を貯留する目標を掲げる。2021年度時点の日本の温暖化ガス排出量(CO2換算で年11億7000万トン)の1〜2割に相当する量で、海外の貯留地などへの運搬も欠かせない。
現在、関西電力の舞鶴発電所(石炭火力)で分離・回収・液化したCO2を、貯留の実証試験を進めている北海道苫小牧市まで海上輸送する計画が進められている。液化CO2の船舶輸送について、日本では世界に先駆けて2024年の実証開始を目指している。
ところで、日本はCCSの法整備で遅れている。国内でCCS事業を行うには排ガス回収では「ガス事業法」、井戸掘削は「鉱業法」や「鉱山保安法」、海底へのCO2貯留は「海洋汚染防止法」などがあり、工程ごとに異なる法律への対応が必要である。
加えてコスト低減も大きな課題であり、現時点で地下にCO2を貯留する費用は8000~1万円/トン-CO2であり、CO2の分離・回収工程が約7割を占める。政府は法律や支援策などの整備を進め、2030年頃までに国内でCCS事業を本格化させるとしている。
船舶輸送の実証試験
2018年7月、経済産業省はCCSに必要なCO2の船舶輸送実証事業を始めると発表した。輸送用の船舶を建造すると共に、船舶関連の法令整備についても関係省庁との協議を開始した。
東芝エネルギーシステムズがシグマパワー有明の三川発電所で回収したCO2を液化してタンクに貯蔵し、船舶で目的地まで運搬して、海底とつなぐパイプを通じてCO2を貯留地まで搬送する構想である。船舶による輸送技術は東京大学、日揮、大成建設などが検討する。
ただし、海底貯留方式では地震で液化したCO2が海底から噴き出すトラブルなども想定する必要があり、コスト削減とともに地元の理解を得ての貯留地探しが課題である。
2021年1月、三菱重工業は世界初となるCO2運搬船を2025年度にも実用化すると発表した。子会社の三菱造船が開発する。発電所や製油所、製鉄所、化学プラントなどから排出されたCO2を陸上で液化し、地下貯留の設備がある地域の港まで船で運搬する計画である。
2021年3月、環境省「環境配慮型CCS実証事業」の一環で、CO2輸送船(圧入船Ready)の概念設計が三菱造船により行われ、日本海事協会から基本承認(AiP: Approval in Principle)を取得した。
全長約110mの船体には2基のタンクが搭載され、液化CO2を約1600トン貯蔵して運搬する。また、海底の地下にパイプを延ばしてCO2の圧入作業にも転用可能な船型の開発が進められた。
2021年3月、商船三井が産業向け液化CO2運搬船を管理するノルウェーの海運会社Larvik Shipping (ラルビック・シッピング)に25%出資し、2024年に液化CO2海上輸送事業を開始すると公表した。また、マレーシア国営のペトロナスとも液化CO2運搬の事業化検討を進めている。
2021年11月、商船三井と三菱造船は、液化CO2運搬船の主流となる船型の概念設計を実施した。
2021年11月、日本郵船と三菱造船は液化CO2を輸送する大型船の共同開発を発表した。小型の液化CO2運搬船は世界でも数隻あるが食品添加物向けが中心で、CCUSを目的とした大型運搬船はない。
2022年2月、三菱造船は、NEDOの「CCUS研究開発・実証関連事業/苫小牧におけるCCUS大規模実証試験/CO2輸送に関する実証試験」で活用する液化CO2運搬の実証試験船の建造契約を、山友汽船と締結した。
図9に液化CO2運搬船のイメージを示すが、船長72m、船幅12.5m、喫水4.55m、タンク容積:1450m3で、三菱重工業の下関造船所江浦工場で建造し、完成および引渡しは2023年度後半の予定である。エンジニアリング協会が山友汽船から液化CO2運搬船を傭船し、NEDO事業で運用する。
2022年5月、日本CCS調査、エンジニアリング協会、伊藤忠商事、日本製鉄は、NEDOからの受託で、北海道苫小牧市の北海道電力敷地内に液化CO2を受け入れる基地や貯蔵タンク(直径14m、高さ18m)の建設を開始した。2024年の完成を目指す。
関西電力の舞鶴発電所で液化したCO2を受け入れる計画で、CO2運搬船は一度に1000トンを輸送でき、1万トン/年を苫小牧に輸送する。2027年まで液化技術や輸送コストを検証する。出荷から保管までに必要な設備の建設コストは約160億円である。
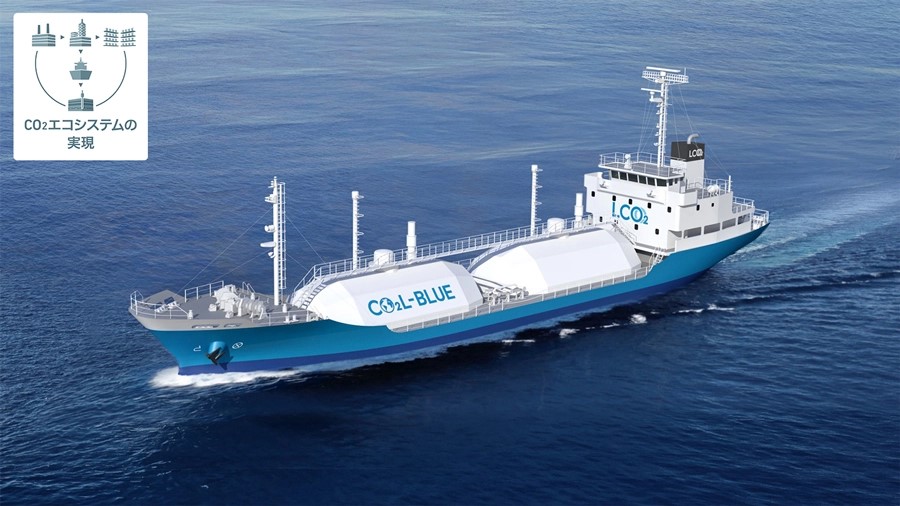
2022年2月、日本製鉄は、オーストラリアdeepC Store Limitedが開発するアジア太平洋地域初の大型洋上浮遊式CO2回収貯留ハブ・プロジェクト「CStore1」でCO2の回収・液化・海上輸送に関する共同研究契約を締結した。
同社製鉄所から排出される100万~500万トン/年のCO2を、CStore1に回収・液化し、液化CO2を海上輸送する事業の採算性を検証する。技術面からの検討と契約条件の協議などを提携企業と行う。
提携企業:JX石油開発、商船三井、東邦ガス、大阪ガス、九州電力、オーストラリア連邦科学産業研究機構(CSIRO)、大阪ガス オーストラリア Pty Ltd、Technip Energies(フランス)、Add Energy Group(ノルウェー)
一方、北欧では欧州の発電所や工場などから回収したCO2を、海上輸送して貯留する構想「ノーザンライツ」が進行中である。ノルウェーのエクイノール、英国石油大手シェル、フランスのトタルエナジーズが参画し、2024年から150万トン/年のCO2をパイプラインで海底下2500mの帯水層に圧入する。
総事業費2000億円超のうち8割をノルウェー政府が補助する。
2023年3月、三菱造船は2タンク(1450m3)の液化CO2を運搬できる小型CO2運搬船「えくすくぅる」を進水させた。2024年10月に輸送実証試験を始める。関西電力舞鶴発電所で液化したCO2を北海道苫小牧市へ運ぶ。
CO2は冷却しすぎると固体のドライアイスになり配管が詰まるリスクなどのため、運搬中は液体状態を維持するために-50℃程度で圧力をかけ続ける必要がある。
2023年4月、川崎汽船はノーザンライツに参画して液化CO2輸送船を2隻を受注し、乗組員を確保して運航する。ノルウェー国内で回収されたCO2を液化し、船で同国沖合に設置される中間受け入れ基地に運ぶ。船舶の輸送容量は既存船の約5倍の7500m3で、2隻合計で80万トン/年程度の輸送を見込む。
現在、運航する液化CO2船は中温中圧(-25℃、15〜18bar)である。開発中の薄鋼板タンクでは低温低圧(-50℃、6~8bar)を目指している。一方、常温高圧(0~10℃、35〜45bar)による輸送方式も検討されている。
2022年には日本郵船はノルウェーの海運会社クヌッツェン・グループと、液化CO2を輸送する船舶の開発などを手掛ける合弁会社を設立し、ノルウェー船級協会(DNV)から液化CO2を常温高圧で海上輸送・貯留可能な貨物タンクシステムの船級認証を取得している。
2023年5月、今治造船は外航大型船を想定した液化CO2輸送船分野で三菱造船との提携を発表。今治造船が51%出資し営業設計を担う日本シップヤードが、三菱造船と共同開発の検討を始めた。
海運会社などから初号機を2024年中に受注し、2027年の竣工を目指す。現時点で液化CO2運搬船は世界に数隻しかなく小型の炭酸飲料運搬向けに限られ、CCS向け運搬船市場は形成されていない。
再生可能エネルギー援用船
2017年6月、化石燃料を使わず、太陽光や風力など再生可能エネルギーを使って航行する8人乗りの白い双胴船Energy observer(エナジー・オブザーヴァー、長さ30.5m、幅12.8m、重量34トン)が、フランスを出港し、約6年をかけて50カ国を巡る話題が注目を集めた。
双胴船の上面は太陽光パネル(約130m2)で覆われ、後部両側には補助的に縦型風車2基が搭載されている。海水を淡水化した後、水電解により水素ガスを取り出して8基の炭素繊維強化アルミ合金タンクで最大62kgの水素を圧縮貯蔵する。
2020年2月からトヨタ自動車のFCシステム(出力:114kW、実質使用は40kW)を搭載して発電し、電動機2台(変換効率:97%)で推進する。補助的にリチウムイオン電池も搭載している。
以上のように再生可能エネルギーのみで小型船を運航する事例は多い。しかし、2020~2030年代には、大型の貨物船やコンテナ船を対象に、風力援用船や太陽光発電搭載船など再生可能エネルギーによる燃費削減を目的とした開発が進められる。
風力援用船
1986年、船舶整備公団が調査した帆走システムを有する新愛徳丸・愛徳丸(699GTタンカー)、扇蓉丸・日産丸(699GT貨物船)の3年間の運航実績で、帆による省エネ効果は全航海平均で夏季10%弱、冬季20%弱である。しかし、石油ショック後に石油が安値で安定したため、普及しなかった。
現在、地球温暖化問題に端を発して開発が進められている風力推進船は、船体形状を翼にした船型開発や、昔からのソフトセイル(軟質帆)の改良に加えた①ローターセイル式、②サクションウイング式、③ハードセイル(硬質帆)式、④凧(たこ)牽引式などの開発が進められている。
2020~2030年代、風力援用はLNG燃料船などと組み合わされることで燃費改善によるCO2排出量の抑制が進められる。将来的には、水素・アンモニア燃料やバイオ燃料などの使用によるゼロエミッション船などとも風力援用は組み合わされる。
ローターセイル式
1920年代、ドイツ人技術者アントンフレットナーが発明したローターセイル(Rotor Sail)が、世界の注目を集めている。甲板上に設置した円筒型ローターを回転させ、マグヌス(Magnus)効果によって推進力を得る風力推進補助装置である。
フィンランドのNorsepower(ノルスパワー)、英国アネモイ・マリン・テクノロジーズ、ドイツ エコ・フレットナーなどが、ローターセイルの実船搭載を進めている。また、韓国の大宇造船海洋も独自開発を行い、フェリー、RORO船、プロダクト船などに搭載している。
2018年4月、オランダ拠点のViking Line(バイキング・ライン)はクルーズフェリーの「M/S Viking Grace」(全長218m、幅31.8 m、総トン数:57565トン)に、ノルスパワーの円筒型ローターセイル(高さ24m、直径4m)を搭載したと発表した。
2013年就航のバイキンググレースは、LNGと重油を使用できる二元燃料エンジン船であるが、EUのHorizon 2020リサーチ&イノベーションプログラムの資金提供でローターセイルを追加設置した。フィンランドのトゥルク~スウェーデンのストックホルム間のバルト海に就航した。
バイキング・ラインは、中国で建造中のクルーズフェリー船2隻についてもローターセイルを搭載し、2020年に就航した。
2021年6月、ブラジル資源大手ヴァーレは、ローターセイルを搭載した大型鉱石船(VLOC)「Sea Zhoushan(シー・チョウシャン)」(全長340m、幅62m、総トン数:173666トン)が完成し、ブラジル~中国間に就航した。中国の上海船舶研究設計院が設計し、江蘇新時代造船が建造した。
ノルスパワーが開発した円筒型ローターセイル(高さ24m、直径4m)を5本搭載し、最大8%の推進効率向上と、3400トン-CO2/年の削減効果が見込まれている。外部の回転筒はCFRP/GFRP/ウレタンの積層構造で軽量化が図られている。
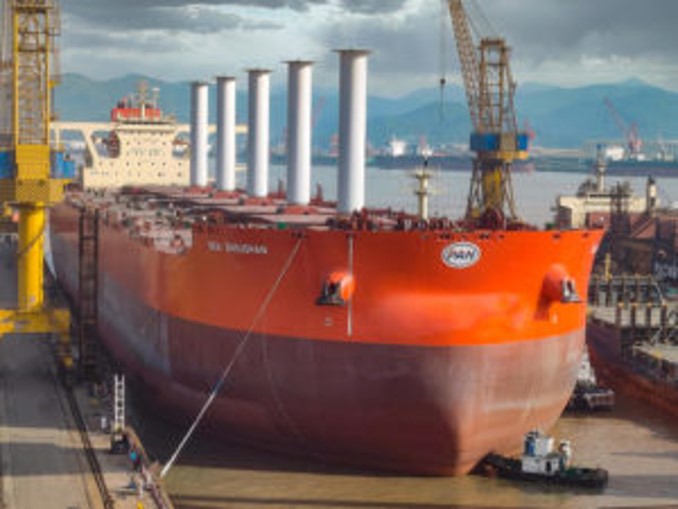
2021年1月、ノルスパワーはノルウェーの海運会社シーカーゴが運航するRORO船「SC Connector」(総トン数:12251トン)に、世界初となる起倒式ローターセイルを2基取り付けたと発表した。橋などをくぐる場合や、船の重心位置を下げるなど、状況に応じてローターセイルの角度調整が可能である。

サクションウイング式
翼の原理によると、翼の表面に比べて背面は空気の流れが高速になり、翼の後端部で流れが乱れて剥離する。これを防ぐため翼の後端部に吸い込み口を設けたものはサクションウイングと呼ばれる。
この翼面に安定した空気流を作りだすサクションウイングを船上に取り付け、風向に応じてサクションウイングを回転させることで、図12(a)に示す推力を得ることができる。(b)には、Econowind製の2本のサクションウイングユニットを船首に取り付けた例を示す。
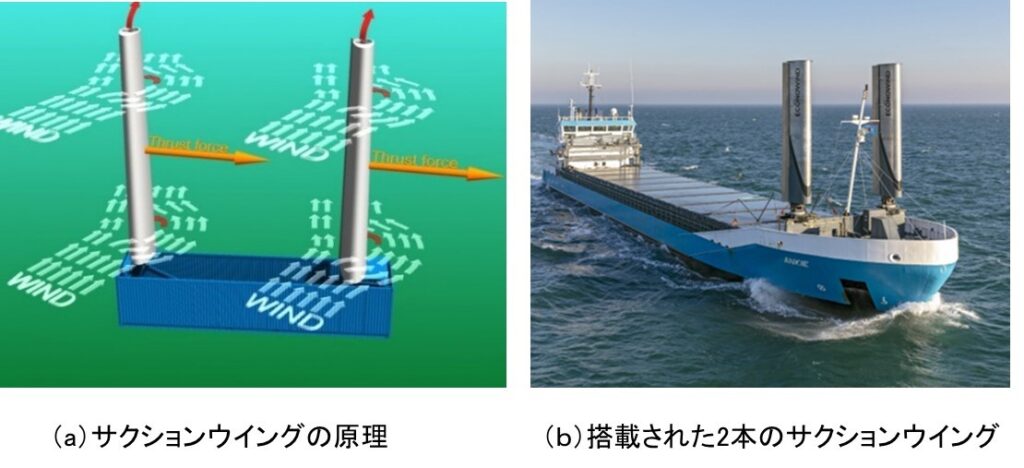
ハードセイル(硬翼帆)式
日本では、東京大学が中心の産学連携「ウインドチャレンジャー・プロジェクト」でハードセイル(硬翼帆)式の風力援用船の開発が進められた。
2019年10月、商船三井は大島造船所と共同で硬翼帆式風力推進装置「ウィンドチャレンジャー」の設計基本承認を取得した。強風時にはFRP製の上下伸縮式帆を使い、船底のタービン発電機を使い水電解により水素を製造して船内に貯蔵し、弱風時には燃料電池で発電して電動機を回して航行する。
2022年10月、商船三井は大島造船所で、硬翼帆(高さ53m、幅15m)を搭載したディーゼルエンジン石炭運搬船を公開した。運航中は設置したセンサーが帆の根元のひずみと風速・風向を計測し、自動で帆を伸縮・回転して効率よく推進力に変える。
硬翼帆は最大瞬間風速:70m/sに耐える強度を有し、台風の中や平均風速:20m/sを超える海域では帆を降ろす。帆1本の搭載によるCO2削減効果は、従来の同型船に比べて日本~オーストラリア航路で5%、日本~米西海岸航路で8%である。
2020年12月、商船三井は硬翼帆を搭載した石炭運搬船(全長23m、全幅43mで、総トン数:99000トン)による輸送契約を締結し、2022年2月には硬翼帆式風力推進装置が完成した。
次に風向きと硬翼帆の運用方法を示すが、正面風以外から硬翼帆は推進力を得ることができる。2020年代後半までに10~12隻への搭載をめざし、将来的には硬翼帆の外販も行う。
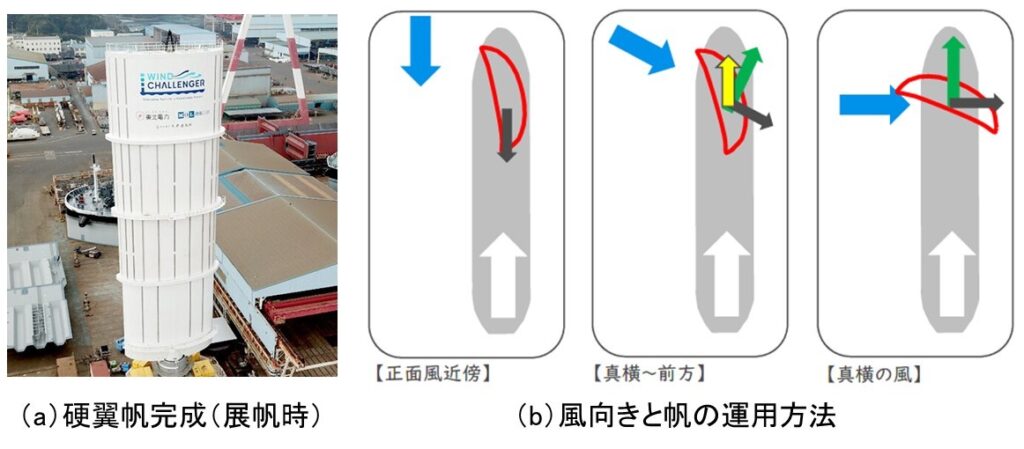
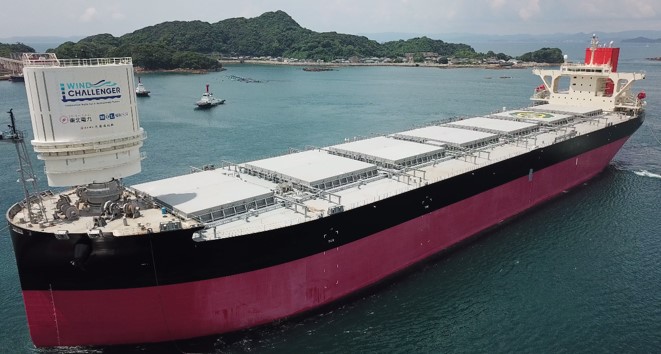
2022年8月、商船三井は2隻目の硬翼帆搭載船を発注した。「ウインドチャレンジャー」に加え、英国アネモイ・マリン・テクノロジーズの「ローターセイル(円筒帆)」と呼ばれる風力推進補助装置を複数取り付けたバルカー(ばら積み)船で、大島造船所で2024年に竣工する予定である。
新造船は商船三井ドライバルクが運航し、木質バイオマスエネルギー大手の米国エンビバ向け木質ペレットを輸送する。
また、商船三井は、帆走中に船内で水素を作り、その水素を燃料として活用するゼロエミッション船の開発計画「ウインドハンタープロジェクト」にも取り組み、ヨット「ウインズ丸」を使用して2021年11月から実証実験を進め、最終的には大型貨物船への実装を目指している。
2022年1月、商船三井は「ウインドハンタープロジェクト」 を公表した。最大高さ53mの硬翼帆を甲板に10基取り付け、船内で海水と風力エネルギーを活用して水素を生み出して陸上へ供給する。推進力にも風力と水素を活用し、環境に影響する廃棄物を排出しないゼロエミッション船を目指す。
*「ウインドハンタープロジェクト」の構想
風力で航行しながら船底のタービン発電機で発電し、海水からつくった純水を電気分解して水素を製造する。その水素とトルエンを化学反応させて水素キャリアのMCH(メチルシクロヘキサン)に変換して船内MCHタンクに貯蔵し、一定量を超えると陸上へ荷揚げする。
船は自動航行モードで、寄港地までの風況を踏まえた最適な航路を割り出しながら、風力と推進プロペラとのハイブリッド推進で航行する。途中で風が弱まると硬翼帆を自動で下げ、格納されていた推進プロペラが起動する。動力はMCHから分離した水素を活用した燃料電池推進による。
港に近づくと推進プロペラが作動するとともに、複数のドローンが船内から飛び立ち、ドローンが係船索(ロープ)を岸壁につないで着岸し、MCHを荷揚げする。空になった船内のタンクにトルエンを補給したのち、再び風の強いエリアへと、MCHの充填時間を予測しながら出航する。
小型の水素生産実証船は、2025年以降に建造を計画している。
その他、スウェーデンの船舶会社Wallenius Marine(Becker)が折畳式の硬翼帆(高さ80m)を5本搭載した大型貨物船「Oceanbird 」(長さ200m、幅40m、排水量:32000トン)について、2022年以降の竣工を予定している。縦に2つ折りで、全体に倒して格納も可能である。
2022年5月、商船三井ドライバルクと米国Enviva (エンビバ)が開発中の木質ペレットの海上輸送用ばら積み船(EFBC、総トン数:62900トン)が、2024年に大島造船所にて竣工予定と公表された。
この船に商船三井が手掛ける 硬翼帆と英国Anemoi Marine Technologiesが開発するローターセイルの併用が検討されている。これにより、CO2排出量の約20%削減が見込まれる。
2022年6月、ノルウェー肥料大手ヤラ・インターナショナルの子会社ヤラ・マリン・テクノロジーズは、開発した高さ45mの硬翼帆「ウインド・ウイングス」を、三菱商事のばら積み船「Pyxis Ocean」(総トン数:8万トン)に2本搭載、2023年に穀物メジャー米国カーギル向けに就航すると発表した。
2021年3月、日本海事協会と太陽工業は、強風の吹く遠洋まで自力で進みながら海水でプロペラを回して発電する帆船型風力発電船(OEHV :Ocean Energy Harvest Vessel)を、2030年までに実用化すると発表した。得られた電力は船内で蓄電して港に直接届ける。
船上で熱可塑性フッ素樹脂(ETFE)製の航空機翼形状である空中翼(セイル)を左右に傾け、風況に応じて生じる揚力を使い向かい風でも前進する。また、空中翼と海中の水中翼は連動し、空中翼に作用する風力により船体が転倒するのを防ぐ仕組みである。
2024年5月、電源開発は商船三井と共同で既存の石炭輸送船に帆を搭載すると発表。2025年後半にも運転を始め、燃料の消費量を5〜8%削減する。「ウインドチャレンジャー」を商船三井と長期契約している石炭輸送船に取り付ける。燃料の削減効果は日本―オーストラリア航路で5%、日本―米西海岸航路で8%を見込む。
2024年9月、商船三井は、米国石油大手シェブロン向けの新LNG運搬船に風力推進装置の導入を発表。シェブロングループ海運会社の長期間貸出船に、ウインドチャレンジャー2基を設置する。韓国ハンファオーシャンが、全長:約286m、全幅:約46m、貨物槽容積:約17.4万㎥の大型船を建造し、2026年の完成をめざす。
LNG運搬船は危険物運搬のほか、甲板にLNGタンクがあるため帆の設置は難しいとみられていた。現在、商船三井はウインドチャレンジャー設置船を2隻運航しているが、2035年までに80隻に増やす計画である。
2024年10月、住友重機械マリンエンジニアリングとオリックスは、バラ積み貨物船で風力を活用した省エネルギー運航の実証実験を開始した。甲板上に翼形状の特殊プラスチック製ソフトセイル(高さ:8m、横幅:13.2m)を搭載し、風向きに合わせて帆の角度を調整し、船の推進を補助する。実証期間は2025年1月まで。
凧(たこ)牽引式
2019年6月、欧州AIRBUSの関連会社AIRSEAS(エアシーズ)が開発した自動カイトシステム「Seawing(シーウイング)」を、川崎汽船が保有する大型バルクキャリアー(重量トン数:17~18万トン)に搭載すると発表した。
表面積1000m2のシーウイングは船首部に係留され、一定条件の風力・風向を受けて船橋からの操作により自動で展開・格納が行われ、風力を利用して推進力を補助する。気象データと海洋データをリアルタイムに収集・分析し、性能の最適化と安全性を確保して運用される。
カイトは8の字を描きながら大きな旋回を行い高速で船を牽引する。高高度の風を受けることで、同船型で20%以上のCO2排出量の削減効果があり、1 隻あたり5200トン/年の CO2 削減が期待できる。
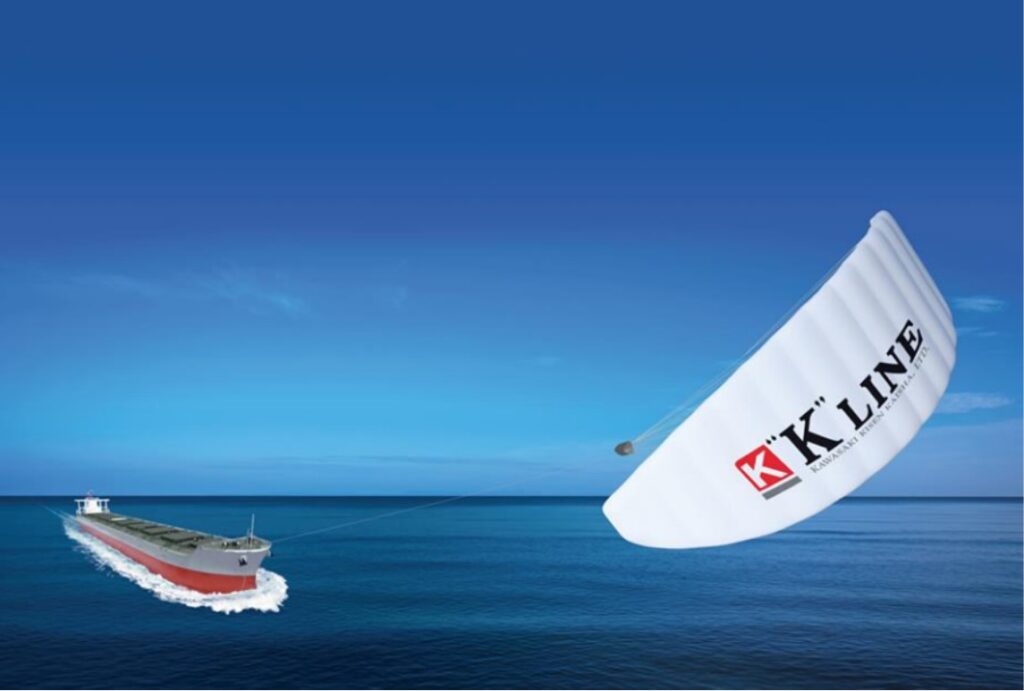
2020年8月、エアシーズは日本海事協会(ClassNK)からSeawingの設計に関する基本承認(AiP)を取得した。引き続き詳細設計を進め、川崎汽船が運航する船への搭載を目指す。川崎汽船はシーウイングをケープサイズバルカー2隻、ポストパナマックスバルカー3隻へ搭載すると発表している。
2024年7月、大西洋と地中海を結ぶジブラルタル海峡に面するモロッコの港湾都市ダフラに、「シーウイング試験飛行センター」が開所した。フランスに本社を置く川崎汽船傘下のオセアニックウイングが運営する。
シーウイングの小型テスト機は一部の船舶に搭載されているが、ダフラ付近で試験飛行を重ねて1年後をメドに約600㎡のカイトを実際の船舶に搭載する。将来的には800〜1000㎡にカイトを大型化する。1000㎡の大型カイトの場合には10%以上の省エネルギー効果が見込めるとしている。
太陽光発電搭載船
2000年代から太陽光発電搭載船の開発は進められてきたが、太陽光パネルの性能では十分な電力が得られないため照明など船内電源としての利用の域を出ていない。本格的な太陽光発電搭載船の実用化のためには、高効率で安価なパネルの供給が不可欠である。
2008年4月、日本郵船は「NYK クール・アース・プロジェクト」で、様々な環境対策に着手した。
2008年12月、本格的な太陽光発電装置(出力:40kW、出力電圧:440V、太陽光パネル:328枚)を搭載した自動車運搬船「AURIGA LEADER」(全長199.99m、全幅32.26m、水深34.52m、重量トン数:18758トン/総トン数:60213トン、三菱重工業製)が竣工した。
太陽光発電で得られた電力は、直流/交流変換機で船内のディーゼル発電機(定格電圧:440V)と連系した電源とした。また、塩害、振動、風圧などの対策検討も、陸上で実績のある5種類の太陽光パネルを搭載して行われた。その結果、太陽光発電の出力平滑化のための蓄電池の重要性が明らかにされた。
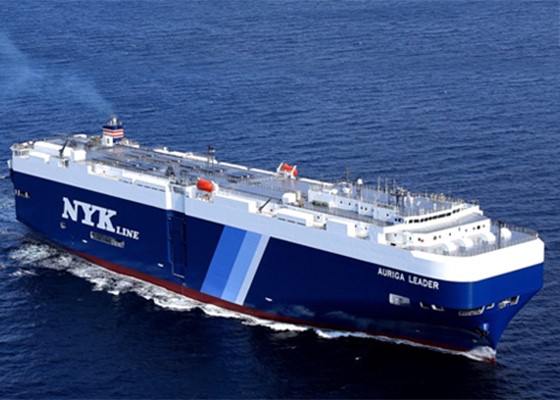
2012年6月、商船三井は太陽光発電を搭載した自動車運搬船「EMERALD ACE(エメラルドエース)」(全長199.99m、全幅32.26m、深さ21.25m、重量トン数:18334トン)の竣工を発表した。停泊中にディーゼル発電機を停止し、太陽光発電でまかなうことでCO2排出量削減を目指した。
商船三井、三菱重工業、パナソニックエナジーが開発した太陽光発電システム(面積:1000m2、パナソニックのHIT太陽光パネル:768枚、容量:160kW)と、蓄電システム(LIB312本のモジュールを1,040個搭載、総容量:約2.2MWh)を組み合わせたハイブリッド電力給電システムを搭載した。
川崎汽船は、高い省エネルギー性能と環境保全性能を両立する次世代船舶の実用化に向け「DRIVE GREEN PROJECT」を進めており、2016年2月、ジャパン マリンユナイテッドが「DRIVE GREEN HIGHWAY」を竣工した。
川崎重工業製の低NOxエンジン、三菱重工業と三菱化工機が共同開発したSOxスクラバーを採用し、甲板部分に912枚のソーラーフロンティア製CIS薄膜太陽光パネル(総出力:約150kW)を設置し、甲板用LED照明の電力を全てまかなう。
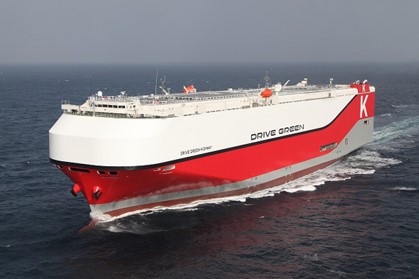
エコマリンパワーは、船上に硬帆(EnergySail)を多数立て、その表面に太陽光パネル(風力発電装置)を張付ける船舶用再生可能エネルギーソリューション「Aquarius MRE」を開発した。寺本鉄工所が製造し、各種センサーの取り付けや自動制御が可能で、電力を蓄電池に蓄えて運航に利用する。
2020年4月、LR2型タンカーへのAquarius MRE設置に向けたフィージビリティ・スタディを開始し、2021年5月、日本海事協会(ClassNK)の基本承認(AiP)を取得した。
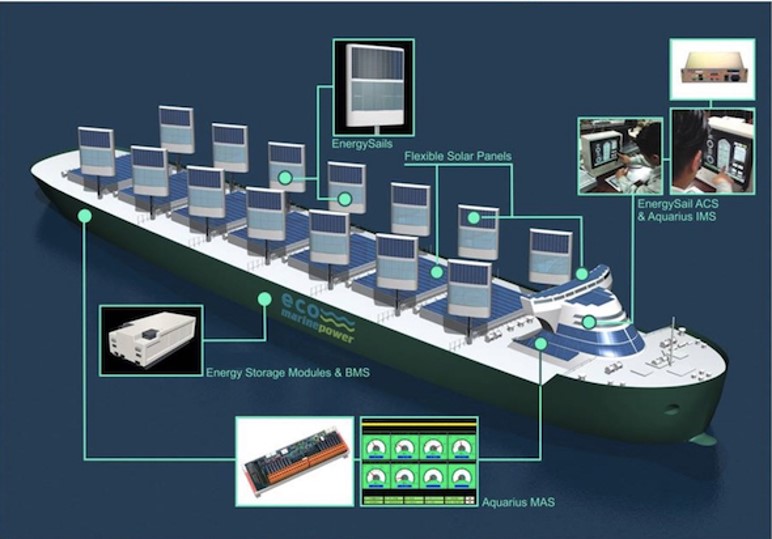
船舶の新展開
「地球環境問題」という重い課題を受け、これを直接に解決すべく苦しんでいるのが、現在の船舶関連業界の姿である。しかし、苦しんでばかりではいられない。新しいアイデアの中に希望の光を見いだすことも必要である。
原子力発電船
米国や欧州より一足先にロシアと中国は小型モジュール炉(SMR)の導入を進めている。ロシアは「海上浮体式」のSMRを実用化し、陸上での建造も計画している。
2020年5月、ロシア国営ロスアトムは、世界初の浮体式原発「アカデミック・ロモノソフ」の商業運転を極東チュクチ自治区で開始した。小型炉「KLT-40S」(出力:3.5万kW)を2基搭載した船で、地区エネルギーの50%をまかなう。
2022年8月、ロスアトムは、北極圏用「海上浮揚式原子力発電ユニット(NFPU)」(出力:10.6万kW、熱出力:17.5万kW~19万kW)の初号船体起工式を中国の造船所で行った。チュクチ自治区内バイムスキー銅鉱山向けで、小型炉「RITM-200」を2基搭載したNFPUを4隻建造する。
船体は長さ140m、幅30m、総重量2万トン近くになる見通しで、完成した船体が中国の造船所からロシアに納入されるのは2023年末の予定である。1隻目のNFPUは、チュクチ自治区の銅鉱山に近いナグリョウィニン岬に係留され、運転開始は2026年末頃である。
2023年1月、韓国のサムスン重工業は、デンマークのSeaborg(シーボーグ)製コンパクト溶融塩炉(CMSR)を搭載した海上浮揚式の原子力発電所「CMSRパワーバージ」の概念設計を完了した。米国船級協会から初期段階の実行可能性の原則承認(AiP)を取得し、2028年までの商業化を目指す。
CMSRパワーバージは電気出力:10万kWのCMSRを2~8基搭載し、24年間の稼働が可能である。係留点まではタグ・ボート等で曳航し、製造期間が約2年と短いため大幅なコスト軽減が実現できる。CMSR内で異常信号が発生した場合、液体燃料の溶融塩が凝固するため安全性に優れている。
LNG発電船
2015年9月、三菱重工業はコンバインドサイクル発電システム(総出力:25万kW)を搭載したLNG発電船の受注を開始した。従来から島嶼部などでは小型ディーゼル発電設備(重油)が多用されているが、火力発電船の採用により安価(従来の2/3程度)でCO2排出量の少ない電力を供給できる。
また、陸上での発電所建設に必要な環境アセスや用地買収などが不要で建設期間を短縮化できるため、インドネシアやフィリピンなど多数の島からなる国々へ売り込みを進めている。
2019年8月、川崎重工業もLNG発電船(総出力:3万~8万kW)の基本承認を取得した。工期は約4年で、長さ100m程度の台船にガスエンジン/ガスタービン、発電機、LNGタンク、送電設備などを設置する。造船所で建造後、曳航して需要地近くの海上に設置する。小型LNG供給船も合わせて提供する。
島しょが多い東南アジアなどの新興国に売り込む計画である。また、海や河川があれば設置できる分散型電源であり、国内では災害時の緊急電源として電力会社や自治体などに売り込む。
2019年8月、商船三井とトルコのKaradeniz(カラデニズ)の子会社Karpower Internationalが、KARMOL(カルエムオーエル)のブランドで、モザンビーク北部のナカラ港で世界初のLNG発電船事業(出力:12万kW)を共同で実施すると発表した。
商船三井が浮体式LNG貯蔵・再ガス化設備、カラデニズが発電船を担い、発電された電力は陸上にある送電設備を通じてモザンビークの国営電力会社に供給される。
電気運搬船
2021年8月、パワーエックスは電気運搬船「Power ARK」の開発計画を発表した。洋上風力で得られた電力を大型系統用蓄電池(100個積載、容量:222MWh)に充電し、日本近海を需要地に向けて航行する。2025年までにプロトタイプを開発する計画である。
2021年12月、パワーエックスは電気運搬船「Power ARK」の開発に向け、今治造船との資本業務提携契約を締結した。実証試験後には系統用蓄電池を1000個積載できるPowerARK1000や、3000個積載できるPowerARK3000などの超大型船の製造も想定している。
2022年1月、パワーエックスは船舶用蓄電池の開発と電気運搬船「Power ARK」及び電気推進船の試験運航に向け、日本郵船との協業に関する覚書を締結し、同年3月には「Power ARK」のプロトタイプ船の設計開発、試験運航に向け、日本海事協会と協業に関わる MOU(基本合意書)を締結した。
2022年6月、パワーエックスが岡山県玉野市に蓄電池組立工場「Power Base」の新設を発表した。敷地面積は約 28,272m2、生産能力は最大 5 GWh/年としている。2023 年にテスト生産を開始し、2024 年から船舶用蓄電池、EV急速充電器、定置用蓄電池などの製造・販売を開始する。
2023年5月、九州電力とパワーエックスは、世界初の蓄電池の海上送電事業について共同で検討すると発表した。送電線には容量に制約があり、再エネ電力を蓄電池にためて船で運搬することで補う。九州と本州間の送電のほか、遠隔地の再生エネ発電所から企業に直接電気を供給する検討を行う。
パワーエックスは、電気運搬船の初号機「PowerX Ark 100」(船長140m、容量241MWh、航続距離:300km)を2025年に完成、2026年に国内外で実証実験を始める。搭載する蓄電池は、安価で安全性が高いリン酸鉄リチウムイオン(LFP)電池を使用し、サイクル寿命は6000サイクル以上である。
また、九州電力と、電気運搬船を利用した海上送電事業を開始すると発表し、横浜市とは電気運搬船利活用を通じた横浜港のカーボンニュートラルに向けて連携協定を締結している。
2025年1月、横浜市、東京電力パワーグリッド、戸田建設、三菱UFJ銀行、運搬船スタートアップの海上パワーグリッドは、洋上風力で発電した電力を電気運搬船で運ぶ事業の実現に向けて覚書を締結。東京近郊で洋上風力が建設されることを念頭に、運搬に必要な港湾インフラの構築や金融面での支援などを協議する。
首都圏では相模湾や伊豆諸島周辺などで洋上風力の適地が多い。横浜市周辺の港湾に運搬船で洋上風力由来の電気を運び、送電線を通じて需要家に運ぶ計画だ。海上パワーグリッドは海上で発電した電力を蓄電池にためて運ぶ運搬船を2026年にも完成させる。水深が深く従来のように海底ケーブルを敷けない海からでも電力を運べるのが特徴で、首都圏近郊の洋上風力の拡大につながると期待されている。
2025年5月、九州電力は、電気運搬船スタートアップの海上パワーグリッドと資本業務提携した。蓄電池を積んだ電気運搬船で太陽光発電の余剰電力を離島に送電できるほか、海底ケーブルの設置が難しい場所にも洋上風力を設置できるなどの効果を想定している。
CCS搭載船とCO2運搬船
2019年10月、デンマークの海事研究開発センターを中心にCO2回収装置を搭載した船(CCS搭載船)を開発する「DecarbonICE」プロジェクト立ち上げられた。将来的にバイオ燃料などと組み合わせ、排出するCO2よりも回収するCO2の量が上回る「カーボンネガティブ」を構想に入れている。
2020年8月、三菱造船、川崎汽船、日本海事協会が、国土交通省海事局の補助事業で陸上用のCO2回収装置を実船搭載して試験運転すると発表した。「CC-Ocean (Carbon Capture on the Ocean)」プロジェクトである。
一方、脱炭素社会の実現に向けて、船上CCS搭載によりCO2を回収して貯留した後、CO2を有効利用する二酸化炭素回収・有効利用・貯留(CCUS:Carbon dioxide Capture Utilisation and Storage)の開発が必要である。
液化CO2の海上輸送はCCUSバリューチェーンの中で回収地と貯留地、もしくは回収地と有効利用地を効率的に結ぶ手段として重要な役割を担う。日本や北欧でCO2海上輸送の実証試験が始められている。
台風発電船
2022年5月、横浜国立大学の台風科学技術研究センターが、台風発電船の開発に乗り出した。台風の風を帆で受けた船が進む力を利用して水中に取り付けた発電機を回し、得られた電力は蓄電池に蓄えたり、海水から水電解により水素を製造する。
台風発電船の運航には台風の進路や強さを高精予測する技術が重要になる。海上のどこに船を配置してどのようなルートで走らせるかで、発電効率が大きく変わる。5年後には台風を再現した実験施設で模型船を走らせ、10年後までには小型の実証船を建造し、海上で実際に性能を調べる計画としている。
造船エンジニアリング事業
世界の造船業界は中国のシェア(新造船受注量ベース)が2021年に45%、韓国が39%と圧倒的に強く、日本は12%に留まる。2000年代に入り、低価格競争で中国・韓国勢に敗れ、国内造船メーカーは事業規模の大幅縮小を進めた。三菱造船はエンジニアリング事業に力点を移している。
造船業界の動向
世界の造船業界では中国のシェア(新造船受注量ベース)が2021年に45%、韓国が39%と圧倒的に強く、日本は12%、その他4%である。2000年代に入り、低価格競争を展開する中国、韓国勢との競合に敗れ、国内の造船メーカーは事業規模の大幅縮小を余儀なくされた。
一方で、日本の国際海運企業の保有船腹量は世界の11%を占め、世界第2位である。日本郵船、商船三井、川崎汽船は船隊規模で世界10位以内に入り、国際海事機関(IMO)から温室効果ガス排出規制を直接に受け、ゼロエミッション船の開発を積極的に推進している。
2025年5月、政府が、国内で縮小が続く造船業の再生に乗り出すと報じられた。造船業がデュアルユース(軍民両用)産業である点を重視し、国主導で休眠中の造船・修繕ドックの再整備と新たな造船ドックの建設を支援し、造船分野で日米協力を進めて関税を巡る交渉での切り札にするのが狙いである。
ブルーアンモニア燃料の次世代船建造を支援するため、GX関連予算を増やす。日本企業が海外で大規模ドックを建設し、事業展開のための支援も行う。日米企業で米国での修繕ドックの整備も支援する。現在、新造船建造量で7割、修繕で9割のシェアを握る中国に頼らない日米サプライチェーン(供給網)構築をめざす。
三菱造船の新展開
事業規模の縮小が進む中で、主要な国内造船メーカーはエンジニアリング事業に力点を移している。
2022年、三菱造船が新たに始めたエンジニアリング事業は、三菱造船性能推定&線図選定システム(MiPoLin:MITSUBISHI SHIPBUILDING POWER PREDICTION & LINES SELECTION)を核とした船舶の開発支援サービスである。
MiPoLinは、三菱重工業船型試験場において、100年以上に渡り蓄積された1200件以上の水槽試験データを利用して、船型創製とその性能推定が行えるWebベースのシステム。
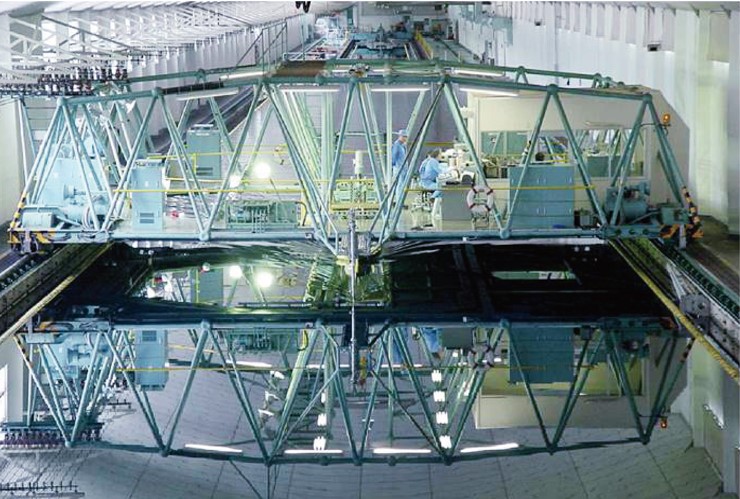
顧客が計画船の主要項目(船種、概略寸法、排水量など)を入力し、船型設計データベースから計画船に近い船型を検索し、抵抗カーブ等の試験結果を比較・評価できる。選択した船型をベースに計画船の要項に合わせた船型の創生を行い、エンジン出力やプロペラ設計などの性能を推定できる。
関連する開発支援サービスとして、流体設計(CFD)による最適船型検討、船首バルブ最適化/省エネデバイスの設計、水槽試験の請負などをラインアップしている。
また、三菱造船は、重油燃料に対する硫黄酸化物(SOx)スクラバー、次世代船舶燃料のLNGガス供給システム、CCSU(CO2分離回収・貯留、利用)など環境技術で強みを有しており、今後、環境規制が厳しくなる状況下で、技術を持たないアジアの造船会社の囲い込みを目指している。
顧客は造船会社や海運会社を想定しており、需要が見込めるアジアを中心に売り込みを進めた結果、受注を実現している。
アナロジー
1990年代まで”ものづくり”で日本経済を牽引した造船業界であったが、価格競争で中国・韓国勢に敗れた。生き残りを賭けた三菱造船のエンジニアリング事業の成否は興味深い。
シミュレーション技術が未発達な時代、大型水槽試験による船体モデル試験は設計の最終確認として重要な位置付けであった。しかし、様々なシミュレーション技術が高度化した現在、大型モデル試験の出番は激減しており、高額な装置の維持・管理を含めた使い方が他業界においても参考になる。
航空機、自動車業界では大型風洞試験、土木建設、電機・機械業界では大型加振試験などなど。