CO2を回収・貯留するCCSだけでは、地球温暖化問題に関する継続的な対策にはなり得ない。そのため、分離回収したCO2の有効利用(Utilization)は必須課題である。
当初、欧米では石油増進回収(EOR)を目的としたCCS設備の設置が行われたが、最近では国内企業によるカーボンリサイクル(化学品、燃料、鉱物など)事業への参画が相次いでいる。
CCUS/カーボンリサイクル
CO2を回収・貯留するCCSだけでは、地球温暖化問題に関する抜本的な対策にはなり得ない。そのため、分離回収したCO2の有効利用(Utilization)は必須課題である。
そのために、二酸化炭素回収・有効利用・貯留(CCUS: Carbon dioxide Capture, Utilization and Storage)が重要であり、米国で実用化が進む石油増進回収法(EOR:Enhanced Oil Recovery)やCO2の産業界における直接利用が検討されている。
最近では、CO2を炭素資源として捉え、これを回収して多様な炭素化合物として再利用(リサイクル)するカーボンリサイクルの重要性が指摘され、バリューチェーンの可視化が始まっている。
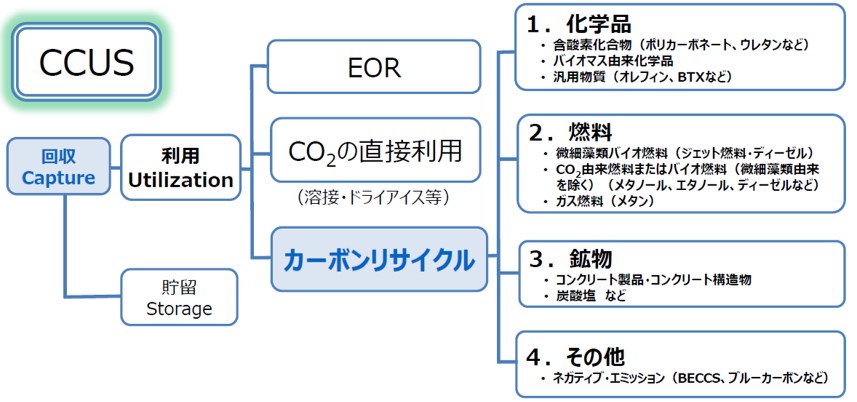
石油増進回収(EOR)
CO2は臨界圧力・臨界温度が低いが、比重が大きく、油の溶解度が高い。枯渇した油田の圧入井からCO2を圧入し、地中に残された原油をCO2により完全溶解状態にし、流動性を高め、膨張させて生産井から原油を回収する採油法が石油増進回収(EOR:Enhanced Oil Recovery)である。
回収したCO2をEORに使う技術は、1970年代には米国テキサス州で実用化されたのが最初である。しかし、EOR技術は費用対効果が悪く、必ずしも順調に拡大していない。転換期は、2016年のパリ協定の発効であり、気候変動対策が世界で解決すべき共通課題として認識されてからである。
2016年12月、三菱重工業中心の日米連合体が、米国テキサス州のW.A.パリッシュ石炭火力発電所に建設したCCSプラント(4776トン/日)が稼働した。化学吸収法(KM-CDR Process)を採用し、排出されるCO2の90%以上を回収、油田まで130kmのパイプラインで送給して地中に圧入する。
通常では油田に存在する原油の25%程度しか汲み出せないが、EORを使うと60%程度まで汲み出すことが可能で、原油生産量が40倍に増大した。
国際エネルギー機関(IEA)によると、2021年時点でCCSや回収したCO2を使い油田などに注入するEORプロジェクトは27件が稼働中であり、開発計画は163件と、前年比2.8倍に急増している。
2021年2月、米国エクソンモービルは、CO2排出削減の新事業「低炭素ソリューション」を発表した。2025年までに30億ドルを投じ、ヒューストンではメキシコ湾海底にCCSハブを建設し、シェブロン、ダウ、ドイツBASFなど世界中の企業と連携し、排出されたCO2をまとめて貯留する計画。
CO2貯留量は2030年までに5000万トン/年とする計画である。2024年にノルウェーで稼働開始する欧州最大級のCCS「ノーザンライツ」の33倍以上の規模となる。
2022年11月、三菱重工エンジニアリングと関西電力が米国エクソンモービルと、CO2回収技術の共同開発に向けた提携を発表した。三菱重工業が基盤技術のライセンスをエクソンモービルに供与し、エクソンモービルは回収したCO2を地層に注入して保管するプロジェクトを手掛ける。
CO2の直接利用
CO2の直接利用は、冷却用ドライアイス(昇華温度:−78.5℃)や炭酸飲料として広く用いられているが、約100万トン/年といわれている。
工業用途としてはシールドガスにCO2を利用した炭酸ガスアーク溶接、液化されたCO2を高圧容器に入れた二酸化炭素消火器、洗浄物の表面にドライアイス粒を吹きつけるドライアイスブラスト洗浄などがあげられるが、用途は限定されており大きなCO2削減量は望めていない。
カーボンリサイクル
CO2を炭素資源として捉え、これを回収して多様な炭素化合物として再利用(リサイクル)することを「カーボンリサイクル」と呼び、急速に注目度が高まっている。
2019年8月、三菱ケミカル・電源開発・三菱日立パワーシステムズ・IHI・川崎重工業など16社は、カーボンリサイクルファンドを立ち上げると発表した。
発電所などから出るCO2を回収し再利用することが目的で、衣料や建材の素材、燃料などを作る技術を確立し、商用化を目指してコスト低減技術を軸に企業や研究者に資金を提供する。
化学品
1999年、三菱重工業はマレーシアに尿素肥料増産用にCO2回収装置(20トン/日)を納入した。その後、インド、中東諸国を中心に尿素肥料増産用のCO2回収装置が納入され、現在も安定稼働している。2017年には、日本液炭向けに13基目が納入され商業運転を行っている。
2016年8月、佐賀市清掃工場では、廃棄物発電所(出力:450kW)から排出されるCO2を回収するため、東芝製のCCS設備(10トン/日)が稼働した。
タンクに貯蔵したCO2を隣接する藻類培養施設に供給し、医療品の原料になる微細藻類ヘマトコッカスの培養を行っている。ヘマトコッカスからは抗酸化作用の強いアスタキサンチンを抽出でき、アルビータなどと商用化を進めている。
また、佐賀市水浄化センターでは、下水汚泥を発酵させたバイオガスからCO2を回収・貯蔵し、微細藻類ユーグレナの培養施設に供給している。ユーグレナは健康食品や、油分を抽出分離してジェット燃料(SAF)の原料として商品化を進めている。
2021年7月、京都大学発のSymbiobe(シンビオーブ)は、紅色光合成細菌を使うCCSプラント構想を発表した。同細菌は海中などに生息して光合成により水中のCO2と窒素を取り込み固定し、水産物の養殖用飼料や窒素肥料や、分解されやすいバイオプラスチック原料などに活用できる。
京都府北部で試験プラントを計画し、2025年以降には量産プラントの製造を目指している。
2021年8月、日本製鉄・大阪市立大学・東北大学は、酸化セリウム触媒を用いて常圧のCO2とジオールを反応させ、水を蒸発除去してカーボネートの合成が可能なことを明らかにした。今後、固体触媒の改良を進め、有機カーボネート、カーバメート、尿素などの合成の可能性を検討する。
2021年9月、東京ガスは排ガスに含まれるCO2と水酸化物を反応させ、洗剤や肥料などの原料となる炭酸カリウムを、都市ガスの利用先で製造するオンサイトCCUS技術を開発している。
カナダのCleanO2 Carbon Capture Technologies製の炭酸カリウムが製造できるCO2回収装置「CARBiN-X」を利用する計画で、小型(幅0.85m×高さ1.9m×奥行2.0m)のため、商業施設などスペースが限られる場所への導入が可能で、今後、実証試験を進め商用化を目指す。
燃料
現在、最も注目されているのは、再生可能エネルギーなどの余剰電力で水電解により水素(H2)を製造し、回収貯留したCO2と共にメタネーション(Methanation)装置に入れ、加熱することで都市ガスの主成分であるメタン(CH4)を合成する方法である。
2021年6月、メタネーション技術の確立と社会実装に向けた「メタネーション推進官民協議会」が設立され、官民両面での取り組みが加速。政府は、2030年までに都市ガス導管に注入するガスの1%をカーボンニュートラルメタンとし、2050年までに90%とする目標を掲げた。
2019年5月、IHIはシンガポール科学技術庁の化学工学研究所(ICES)と共同で触媒を開発し、メタネーション技術の試験装置を開発して1Nm3/日のメタン製造に成功した。また、SOFCの逆反応を使いメタンを製造する高温水蒸気電解(SOEC)共電解メタン合成も検討している。
2019年10月、国際石油開発帝石と日立造船は、メタネーション試験設備を長岡鉱場の越路原プラント敷地内に完成させた。越路原プラントで天然ガス生産時に付随するCO2を回収し、固体高分子水電解装置(32Nm3/h)により製造された水素と反応させてメタンを合成する。
日立造船製のプレート型メタネーション反応器は、熱回収効率が87%と高く、運転温度:200℃、運転圧力:0.7MPaである。生成ガス(メタン濃度:91.2%)をガス精製器を通し、高濃度化(99.6%)が可能である。メタン製造能力は8Nm3/hで、4500h以上の安定製造を確認している。
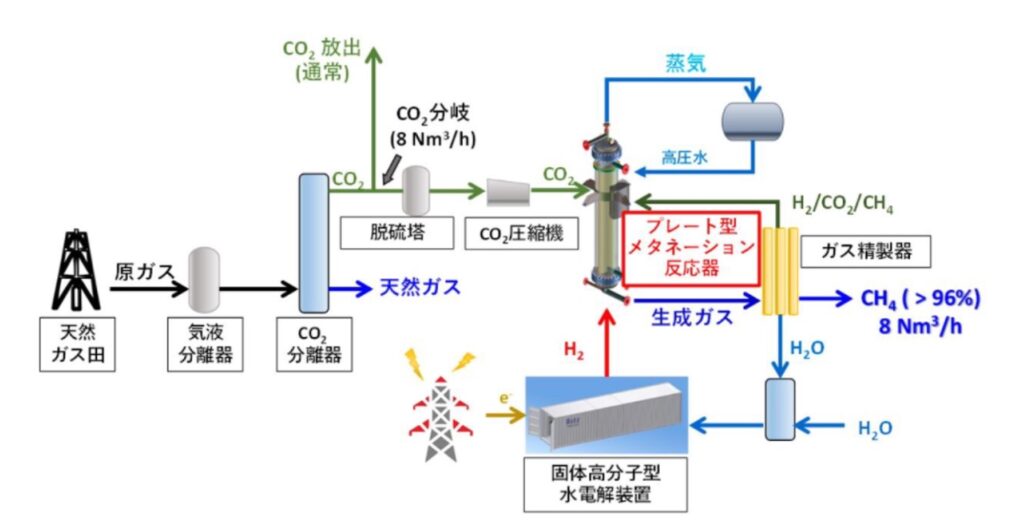
2020年7月、デンソーは安城製作所のアルミ溶解炉などから出たCO2を回収し、太陽光発電でつくった水素からメタンを合成するメタネーション実証実験を始めた。合成メタンは生産設備の燃料に使い、CO2を工場内で循環させる。2025年から社外での実証実験、2030年の事業化を予定している。
2021年8月、日立造船が小田原市環境事業センターのごみ焼却施設から排出されるCO2を回収し、水素と反応させるメタネーション装置の建設を進めており、2022年春以降に稼働すると発表した。エア・ウォーターの排ガスからCO2を分離する技術を活用している。
2021年10月、INPEX・大阪ガスは、大規模メタネーション装置(製造能力:約400Nm3/h)の導入によるNEDO「CO2排出削減・有効利用実用化技術開発事業」(~2025年度末)を開始した。
実証試験はINPEX長岡鉱場の越路原プラントからCO2を回収し、水素と化学反応させて製造した合成メタンを、INPEXの都市ガスパイプラインへ注入する。
2021年12月、大阪ガスの子会社Osaka Gas Australia Pty Ltdは、100カ国以上でエネルギーインフラ事業を展開するATCO Ltdの子会社ATCOオーストラリアと、オーストラリアでのメタネーション事業の実現可能性調査に関する基本覚書を締結し、共同研究を開始した。
両社はメタネーション実験設備の建設に向けた立地や、CO2や水素の供給方法と輸送・販売方法に関する検討、国内・輸出向けのビジネスモデル構築や経済性評価などを、2022年中に実施する。
2022年3月、東京ガス・太平洋セメントは、セメント製造過程から出るCO2と水素から合成した都市ガスを供給するための事業化調査を開始した。メタネーションの実証プラントは太平洋セメントの国内工場内に設置し、ガス導管を通じて合成メタンを需要家に供給する。
2022年3月、東京ガスは横浜テクノステーションで、メタネーション実証試験を開始した。横浜市らとの連携により、地域のカーボンニュートラル化に向けた地産地消モデルの検討を行う。2020年代中頃に製造能力を数百Nm3規模に拡大し、2030年にガス販売量の1%に合成メタンを導入する。
太陽光発電などの電力で、英国ITM Power製固体高分子型水電解装置(水素製造能力:30.9kg/h、圧力:1MPa未満)で水素製造を行い、DAC装置で回収されたCO2を用い、日立造船製の多管シェル&チューブ型メタネーション装置(CH4製造能力:12.5Nm3/h)によりメタン合成する。
2022年4月、大阪ガスは、回収されたCO2とSOECで製造された水素からメタネーションを行う試験設備を大阪市酉島地区に建設すると発表。2027年度までに200世帯程度の都市ガス製造設備を建設し、2030年度までに1万世帯に拡大。その後、製造コスト削減を進め、2040年頃の事業化を目指す。
2022年4月、大阪ガスは大阪市や大阪広域環境施設組合と、再生可能エネルギー由来水素と、生ごみを発酵させて製造したバイオガス(メタン約60%とCO2約40%)中のCO2からメタネーションでメタンを合成する開発を、環境省「水素サプライチェーン構築・実証事業」(~2025年度)で行う。
2022年8月、日本特殊陶業はメタン製造設備の販売を目指して2023年4月頃から小牧工場で実証実験に乗り出す。ゼオライト膜を利用してガスエンジンから出たCO2を回収し、水電解で得られた水素と反応させ、1Nm3/h(0℃、1気圧)の合成メタンを製造し、ガスエンジンの燃料として再利用する。
将来的に、4Nm3/hのメタン製造設備を開発し、2030年に中小規模工場への販売を目指す。製造コストは100円台/Nm3と、現状の1/3程度に引き下げる計画。
2022年9月、豊田自動織機は高浜工場でメタネーションの実証実験を始める。ボイラにCCS設備を付帯し、化石燃料由来のグレー水素と混ぜて合成メタンを製造し、別ボイラの燃料で再利用する。将来的に全工場にメタネーション設備を導入、太陽光発電によるグリーン水素へ切り替える。
2022年10月、IHIは、合成メタンを製造できる小型メタネーション装置の販売を開始した。開発したメタネーション装置は、サバティエ方式で反応器型式にはシェル&チューブを採用し、12.5Nm3/hのメタン製造が可能である。外形寸法は、幅2250mm×長さ6100mm×高さ2850mm。
工場や研究所、事業所などにおけるカーボンニュートラル実現に向けた検討のために試験運用したいという多数のニーズに対応する。
鉱物
2019年7月、日米両国は石炭火力発電所から出るCO2の再利用で連携し、建材の原料に再生する共同開発計画を発表した。日本の石炭エネルギーセンターや米国ワイオミング州、コロンビア大学などが参加して覚書を締結した。商用化に伴い大規模化するのに必要な技術検証を行う計画である。
米国ワイオミング州の石炭火力発電所(出力:40万kW)を使い、排出ガスに含まれるCO2を石炭灰や廃棄物と混ぜ合わせて化学反応を起こし、コンクリートや道路の資材として使われる炭酸カルシウムを製造する。基礎技術はコロンビア大学の試験装置で実証されている。
2021年5月、伊藤忠商事はオーストラリアMineral Carbonation International(MCi)とCO2固定化技術を活用する協業契約を締結した。MCiのCO2固定化技術は、一定以上のCO2濃度の気体ではCO2の分離・回収工程を必要とせず低コスト化が可能である。
MCiは製鉄工程で生じるスラグや火力発電所で生じる石炭灰、廃コンクリートなどカルシウムやマグネシウムを含む様々な物質とCO2を反応させることで、炭酸カルシウム、炭酸マグネシウム、シリカなどを製造する技術を有し、セメント、コンクリート、建設用資材など幅広い用途が見込まれる。
2022年4月、アイシンと大成建設は、アミノ酸水溶液に排気ガスを吹き込み炭酸カルシウムでCO2を固定化し、製鉄所の高炉スラグと反応させて「T-eConcrete®/Cabon-Recycle」(カーボンリサイクル・コンクリート)を製造・活用する共同開発契約を締結し、2030年頃までの実用化を目指す。
コメント