水素の供給コストは氏0℃、1気圧の標準状態に換算して100円/Nm3程度と、液化天然ガス(LNG)の10倍近い。政府は水素とアンモニアを国内外で製造、海外から運搬する供給企業に対し、期間限定で差額の一部を補助する制度を検討している。それでも経済性の見通しは立っていないのが現状である。
水素
化石資源由来のグレー水素
二次エネルギーである水素の製造方法は、表1で示すように使用する原材料により化石資源由来と非化石資源由来とに大別できる。現在、生産されている水素の大部分は化石資源由来でグレー水素(製造コスト:1ドル/kg程度)と呼ばれている。
工業プロセスの副産物として生成する副生水素や、化石資源を改質する方法(水蒸気改質、部分酸化、接触改質など)が主体であるが、化石燃料で発電した電力を用いた水電解法も商用化されている。
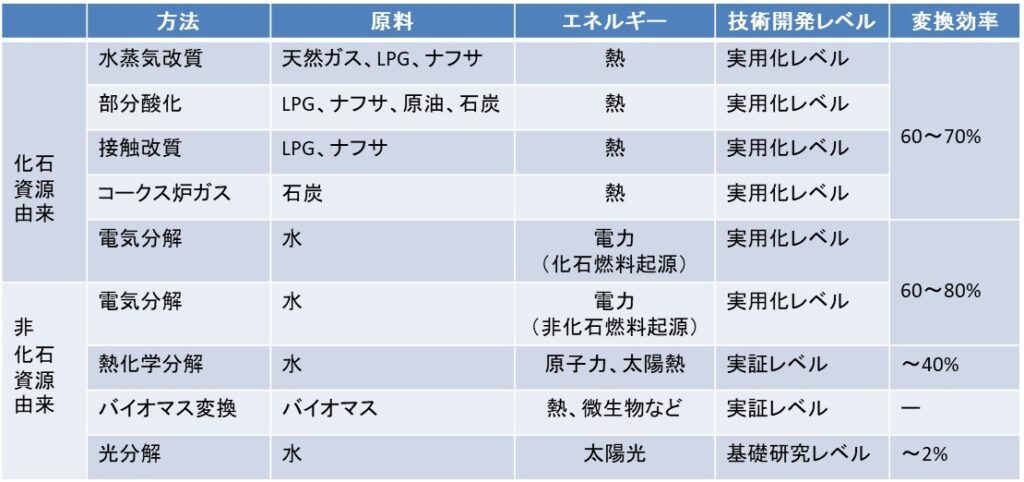
出典:科学技術・学術政策研究所
水蒸気改質ではニッケル系触媒が用いられるが700℃以上の高温が必要で、放出されるCO2を削減することが課題である。JXTGエネルギー(現ENEOS)は独自の分離膜技術により石油精製過程で発生するCO2を分離して100%に近い高純度水素を生産する技術を開発している。
また、水素サプライチェーン構築の一環で、千代田化工建設や川崎重工業は化石燃料の改質による水素製造過程で発生するCO2を炭酸ガス回収・貯留(CCS:Carbon capture and storage)技術で除去する技術を開発している。
グレー水素の製造過程で出るCO2を除去したものはブルー水素(製造コスト:2ドル/kg以下)と呼ばれ、日本は本命視している。しかし、クリーンとみなす基準を欧米は次のように厳しく設定している。
- 2022年1月、EUでは持続可能な経済活動を分類するタクソノミーで、化石燃料採掘から水素製造、消費までに発生するCO2を7割超減らした水素をクリーンとみなす規則を施行している。
- 米国は、2021年11月に成立したインフラ法で、水素メーカーへの助成金の基準として、水素製造時のCO2を8割以上減らすことを規定している。
- 英国では、2021年に化石燃料の採掘から水素製造までに生じるCO2を、85%削減する基準案を政府が示している。
非化石資源由来のクリーン水素
非化石資源由来の水素製造方法として、再生可能エネルギー電力を用いた水電解法がある。この再生可能エネルギー水素は、グリーン水素(製造コスト:5ドル/kg程度)と呼ばれ本命視されている。
再生可能エネルギー水素は、風力発電や太陽光発電のような大きな出力変動を水素製造・貯蔵で平準化したり、遠隔地の発電所から送電を行い需要地で水素を製造・燃料電池発電するなどエネルギー輸送対策として有効である。現在、低コスト化を目指して国内外で実証試験が進められている。
水の電気分解法で多くの実績を有するのはアルカリ水電解法であるが、最近は固体高分子型燃料電池(PEFC:Polymer Electrolyte Fuel Cell)の逆反応を利用したコンパクトな固体高分子型水電解法(PEEC:Polymer Electrolyte Electrolysis Cell)が商品化されている。
また、最近は固体酸化物型燃料電池(SOFC: Solid Oxide Fuel cell)の逆反応を利用した固体酸化物型水蒸気電解法(SOEC: Solid Oxide Electrolysis Cell)の研究開発が進められている。作動温度が高いが、電解効率が極めて高いのが特長である。
一方、2022年1月、EUはタクソノミーで原子力発電を脱炭素に貢献するとの方針を公表し、原子力発電由来の水素をクリーンなエネルギーと位置付け、イエロー水素あるいはピンク水素(製造コスト:2.5ドル/kg程度)と呼ばれている。原子力発電所の設置リスクを伴う点が問題である。
その他、次世代技術として高温ガス炉や太陽熱による高温での水の熱化学分解、微生物などによるバイオマス変換、太陽光による水の光分解の研究開発が進められている。いずれも、水素製造時のCO2排出量がゼロとなるが、低コスト化が課題である。
欧米におけるグリーン水素製造の加速
2022年3月のロシアによるウクライナ侵攻で、原油や液化天然ガス(LNG)の価格が高騰した結果、再生可能エネルギーの価格競争力が上がったこと、加えてEU内でのエネルギー自給率向上を狙い、グリーン水素をつくる水電解装置の量産が欧州で始まっている。
2022年3月、ドイツのシーメンス・エナジーはベルリンの工場で2023年に数百万kW/年規模の装置「Silyzer300」(容量:1.75万kW級)の量産を始めると発表した。東レはシーメンス・エナジーに電解質膜を提供している。
2022年4月、ノルウェーのネル・ハイドロジェンは同国南部ヘロヤの水電解装置の量産工場(電力:50万kW/年)を稼働させた。グリーン水素を1.5ドル/kgで提供すべく、伊藤忠商事とも提携して2025年までに米国と欧州で400万kWずつ、アジアで200万kWと1000万kW/年の生産体制を目指す。
2022年5月、2030年までにEU域内で1000万トン/年のグリーン水素を製造する目標を発表した。これは従来目標の2倍であり、化石燃料に替えて自給自足のエネルギー源としてグリーン水素を促進する方針を明確に示したものである。
また、英国ITMパワーは2024年までに入力電力:500万kW/年の生産体制を構築するとしている。
ITMパワーとは、2018年7月に住友商事が戦略的パートナーシップ契約を締結し、2021年7月には、東京ガスと住友商事が、ITMパワー製である2MW級のPEEC水電解装置(水素製造能力:30.9kg/h)を使用した水素利用の共同実証実験を実施することで合意している。
欧州に比べて、出遅れ感が否めないが、
2021年7月、ブルームエナジーは固体酸化物型水蒸気電解装置(SOEC)の開発を発表した。開発したSOECは、一般の水電解技術に比べて15%の省エネが可能で、アルカリ水電解やPEECよりも外部熱源を利用すると最大で45%の省エネを発表している。
2022年8月、米国のLNG生産企業ニュー・フォートレス・エナジーと米国燃料電池システム開発のプラグパワーは、テキサス州に商用規模の固体高分子型水電解法(PEEC)によるグリーン水素製造施設(電力:120MW)の建設を発表した。50トン/日のグリーン水素製造が可能としている。
日本におけるグリーン水素製造の状況
2020年8月、日立造船はNEDOが山梨県で行っている実証事業にPEEC大型セルスタックを供給した。日立造船が開発した大型水素発生装置「HYDROSPRING」がベースで、入力電力:500kWの電解槽を3槽並べ、合計1.5MWの電力から400Nm3/hの水素を供給できる。
日立造船はラオスでもグリーン水素製造の実証実験を計画しており、電解装置の量産時期は早くても2030年前後になる見通しである。
2021年1月、旭化成は大型アルカリ水電解システム「Aqualyzer」を開発中であると公表した。1ユニットあたりの最大入力電力:1万kWの規模で、2025年の販売を目指している。
2021年10月、高砂熱学工業は再生可能エネルギーによる大型水素製造装置の開発に着手する。電力が変動しても安定的に水素を製造できる方式で、水素製造能力は100Nm3/hとし、国内で同型を手がける日立造船や神戸製鋼よりも高効率化を目指している。
2022年8月、神鋼環境ソリューションは、ヤマト・H2Energy Japanを通して日本建設工業の関東総合センターの水素発電実証モデル設備に、PEEC水電解式高純度水素発生装置「HHOG」(水素製造能力:10Nm3/h)を納入した。センターの敷地内にある太陽光発電を利用してグリーン水素を製造する。
以上のように、欧米に比べて水素製造装置の量産では明らかに出遅れているのが現状である。
2022年8月、経済産業省は水素とアンモニアを国内外で製造、海外から運搬する供給企業に対し、期間限定で発電所の燃料として使う石炭や天然ガスなどの化石燃料との差額の一部を補助する制度を設け、コンビナートでの貯蔵タンクやパイプラインなどのインフラ整備も支援対象とする検討を始めた。
既に、価格差に着目した支援制度は英国やドイツで先行して準備が進められている。しかし、水素の供給コストは氏0℃、1気圧の標準状態に換算して100円/Nm3程度と、液化天然ガス(LNG)の10倍近い。アンモニアは20円/Nm3程度で石炭の3倍ほどの水準であるため、経済的には厳しい。
化石燃料由来の水素やアンモニアは製造時にCO2を排出するが当面は支援対象とし、将来的にCCSなどでCO2排出量の実質ゼロを確約するなどの条件を設定するなどの対策を行う。今後、水素サプライチェーン全体を見ての低コスト化が大きな課題となっている。
水素サプライチェーン構想の実現
2005年に、千代田化工建設は「水素サプライチェーン構想」を提唱している。
「水素サプライチェーン構想」
岡田佳巳、安井誠、水素の大規模貯蔵輸送技術と今後の展望、日本機械学会誌、119-1169, (2016)p.186-189.
海外で製造された水素を液体のトルエンに反応させて液体のメチルシクロヘキサン(MCH:Methylcyclohexane)に転換し、MCHの状態で水素を貯蔵・輸送する。このMCHを用いる有機ケミカルハイドライド法(OCH法:Organic chemical hydride method)を使えば、水素ガスを約1/500の容積の常温・常圧の液体として貯蔵・輸送することが可能である。その後、水素の利用地において触媒を用いた脱水素反応により、MCHから水素を分離して需要家に供給する。脱水素反応で得られるトルエンは、再びMCH生成の原料として再利用する。
2013年4月から同社の子安リサーチパークに実証プラント(製造能力:50Nm3/h、MCHタンク容量:20m3)を建設し、MCH転換比95%を目指して実証試験が進められ、2014年11月までに約10000hの運転を実施した。
2017年7月、国際間水素輸送の実効性を確認するため、千代田化工建設、三菱商事、三井物産、日本郵船の4社が、次世代エネルギーチェーン技術研究組合(AHEAD)を設立し、NEDOの助成を受けて2015年に世界初の「国際間水素サプライチェーン実証」を開始し、2020年12月に完了した。
すなわち、ブルネイ・ダルサラーム国に水素プラント、川崎市臨海部に脱水素プラントを建設し、ブルネイで調達した水素を常温・常圧下のMCHで日本へ海上輸送し、川崎市臨海部で気体水素に戻して需要家に発電燃料を供給する水素サプライチェーンを構築し、10カ月間の運用で100トン超を供給した。
2018年からENEOS、千代田化工建設、クイーンズランド工科大学が、オーストラリアにおいて集光型太陽光発電の電力を利用して有機ハイドライド電解合成法でMCHを製造し、CO2フリー水素のサプライチェーン構築を進めた。水とトルエンから直接MCHを製造できるため、工程を大幅に簡略化できる。
一方、2013年9月、川崎重工業が液体水素を運搬する小型水素輸送船(運搬容積:2500m3)を2隻建造し、オーストラリアのロイヤン発電所の炭田から産出される褐炭をガス化し、CO2回収・貯留装置を併用してCO2フリーの液体水素を現地製造し、液体水素を日本に輸送する実証試験を開始した。
2016年2月、「技術研究組合CO2フリー水素サプライチェーン推進機構(HySTRA)」が設立され、NEDO助成を受け、岩谷産業が液体水素荷役、川崎重工業が液体水素運搬船、貯蔵・液化・積荷設備、シェルジャパンが液体水素運搬、電源開発が褐炭ガス化、丸紅がサプライチェーンに取り組む。
「液化水素運搬船」
https://www.sankei.com/economy/news/210524/ecn2105240023-n1.html
液体水素は不純物除去の手間が不要で、輸送後に直ぐ使える。しかし、液体水素輸送船では液体水素の比重が0.07g/mm3と軽く、沸点が-253℃と極低温のため、従来のLNG輸送船のLNG(比重:0.424 g/mm3、沸点:-162℃)に比べ、安全性や断熱性について高度の技術が必要となる。特に、LNG輸送船の製造で培った溶接技術を進化させて、液体水素貯蔵用大型タンクの開発が行われた。
液化水素運搬船は日本海事協会から基本認証を得ており、全長:116m、船体重量:8000トンで、容積:約1,250m3の真空断熱二重殻構造の海上輸送用液化水素タンクを搭載する。2021年5月には世界初の液化水素運搬船「すいそ ふろんてぃあ」の進水式が行われ、2021年度に、オーストラリア・ビクトリア州で採掘した低品位の褐炭をガス化・精製して液化し、神戸まで約9000km輸送する実証実験が行われた。すなわち、2021年12月に神戸港を出航し、液化水素を積んで2022年2月に神戸港に帰港し、神戸市内の水素荷役施設「Hytouch神戸」に陸揚げした。2030年までに大型水素輸送船(水素運搬容積:160000m3)を2隻造り、商用水素チェーンの本格稼働を開始する計画で、水素発電所への水素供給も検討している。
2021年1月、川崎重工業は液体水素の水素燃焼タービンを動力源とする大型運搬船の建造計画を発表した。大型船の多くは重油燃料のジーゼルエンジンや蒸気タービンが主流であるが、船舶の環境規制が強化される中、液体水素タンク(容積:40000m3)を最大4基搭載し、2026年の完成を目指す。
2020年3月、産業技術総合研究所、日立製作所、デンヨー興産が、福島県で導入が進められている再生可能エネルギー電力を化学変換(トルエン→MCH)、貯蔵、輸送して、ディーゼルエンジンによる水素混焼バイオマス発電システムで発電する水素サプライチェーンの実証実験を実施している。
2022年9月、住友商事は韓国化学大手のロッテケミカルと、水素やアンモニアの共同調達や貯蔵などでの協力を発表した。オーストラリアや南米での生産事業への共同出資も目指す。両社は日韓が水素やアンモニアの大規模な輸入国になると見込み、覚書を締結した。
今後、2年をかけて、海外からの調達や貯蔵ターミナルの開発、新技術の導入、生産過程で発生したCO2の回収・地下貯留・再利用(CCUS)などについて検討する。
IEAによるNet Zero by 2050
2021年5月、国際エネルギー機関(IEA)は「Net Zero by 2050 Roadmap for the Global Energy Sector」を公表した。この2050年ネットゼロを達成するNZEシナリオ(Net Zero Emissions by 2050 Scenario)実現のための水素・水素ベース燃料の生産量が図7のように示されている。
- 2020年には、8700万トン(化石資源由来:7800万トン、化石資源由来+CCUS:855万トン、水電解:45万トン)であった。
- 2030年には、2億1200万トン(化石資源由来:6200万トン、化石資源由来+CCUS:6900万トン、水電解:8100万トン)に増加すると予測。
- 2050年には、5億2800万トン(化石資源由来:80万トン、化石資源由来+CCUS:1976万トン、水電解:3224万トン)に増加すると予測。
2020年の水素ベース燃料の生産量の約90%は化石資源由来であるが、2030年には約30%、2050年にはほぼ0%とするIEAの計画である。そのためには、従来の水素製造の主体が化石資源由来のオンサイト生産であるのに対し、水電解の商用生産に移行する必要があるとしている。
一方で、水素ベース燃料の消費量は、図6に示すように従来は製油所や一般産業用途に少量が使われていたのに加え、新たに水素やアンモニアによる発電用途、輸送用燃料など、製造業の脱炭素化で需要が激増すると予測している。
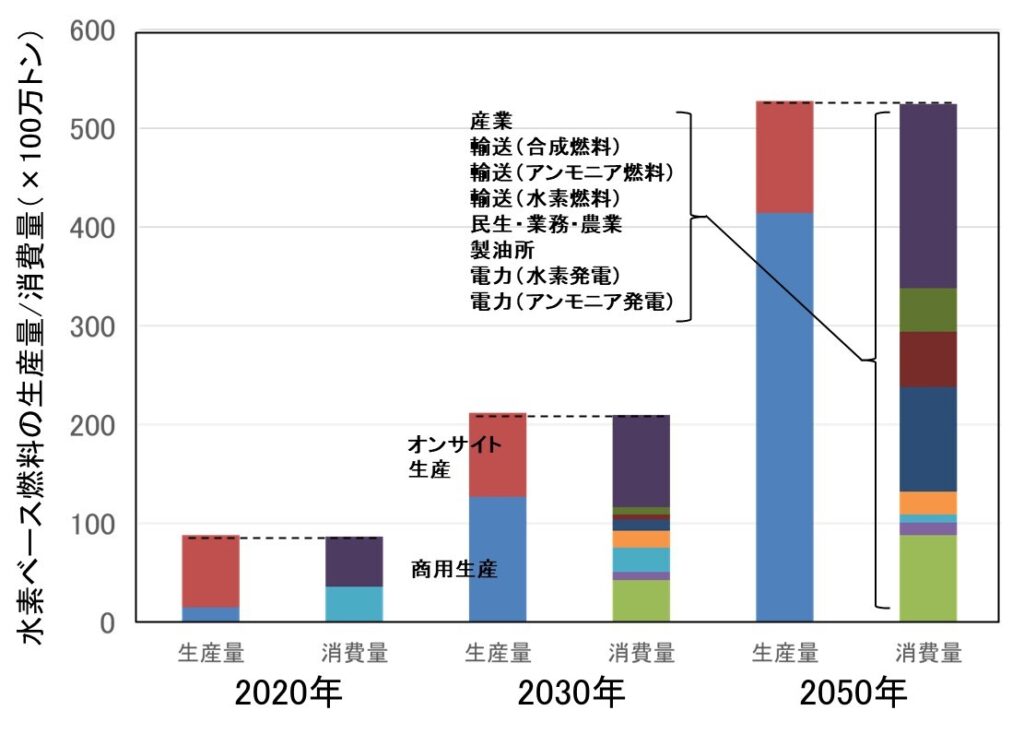
出典:国際エネルギー機関(IEA)、2021年6月
コメント