国内でのCO2回収・貯留技術(CCS)の開発は、1990年の三菱重工業・関西電力による発電所のボイラ排ガスからのCO2回収に始まる。
火力発電所に設置されるCCSは、ボイラ排ガスからCO2を回収する燃焼後(ポストコンバッション)方式と、燃焼前の燃料からCO2源を回収する燃焼前(プレコンバッション)方式がある。現在の主流は燃焼後方式で、既設の火力発電所にCCS設備が付帯されて実証試験が行われている。
CCS開発の流れ
CCSとは?
CO2回収技術
国内でのCO2回収・貯留技術(CCS)の開発は、1990年の三菱重工業・関西電力による発電所のボイラ排ガスからのCO2回収に始まる。運転条件に応じてCO2を選択的に吸収・放出するアミン系吸収液が開発され、化学吸収法による技術実証が進められた。
排ガスが吸収塔に導入されると排ガス中に含まれるCO2がアミンに吸収され、吸収液はCO2リッチになる。この吸収液は再生塔に導かれてリボイラで加熱されるとCO2を放出し、CO2リーンに戻り、吸収塔で再びCO2を吸収する。これを繰り返すことで、排ガスからCO2を回収し貯留する。
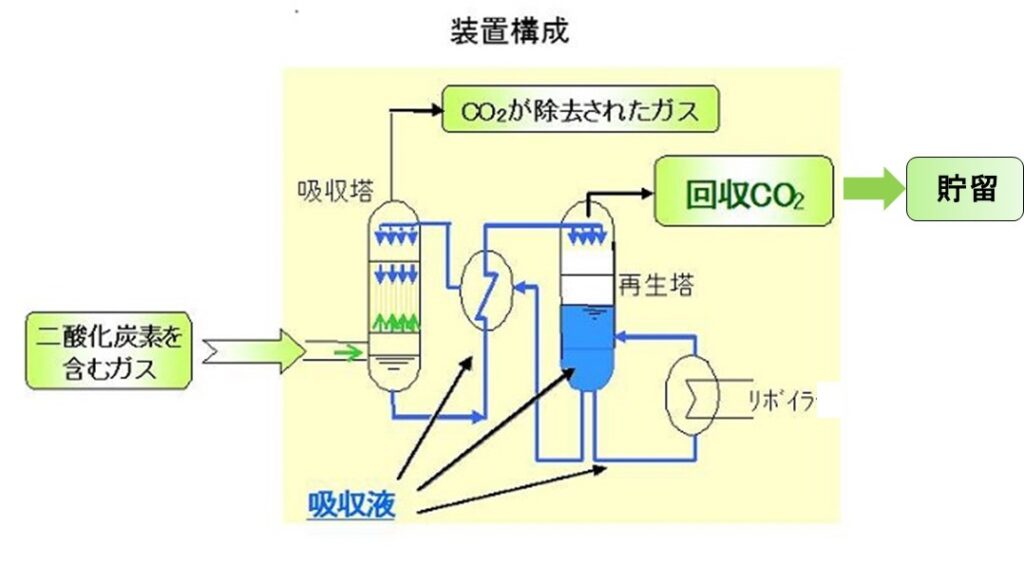
火力発電所に設置されるCCSには、ボイラ排ガスからCO2を回収する燃焼後(ポストコンバッション)方式と、燃焼前の燃料からCO2源を回収する燃焼前(プレコンバッション)方式がある。
現在の主流は燃焼後方式で、既設の火力発電所にCCS設備が付帯され実証試験が進められている。一方、大崎クールジェンの石炭ガス化燃料電池複合発電(IGFC)では、燃焼前方式のCCS実証試験が進められている。
「次世代火力発電の早期実現に向けた協議会」の技術ロードマップ(2015年7月)によると、化学吸収法は既に技術確立されて各種プラントへ適用されているが、回収コストが4200円/トンと高く、本格的な実用化には至っていない。
現在、2000円台/トンを目指して物理吸収法と固体吸収法によるCO2回収技術の開発が進められており、2030年に向けて1000円台/トンを目指し、安価な膜分離法の開発が進められている。
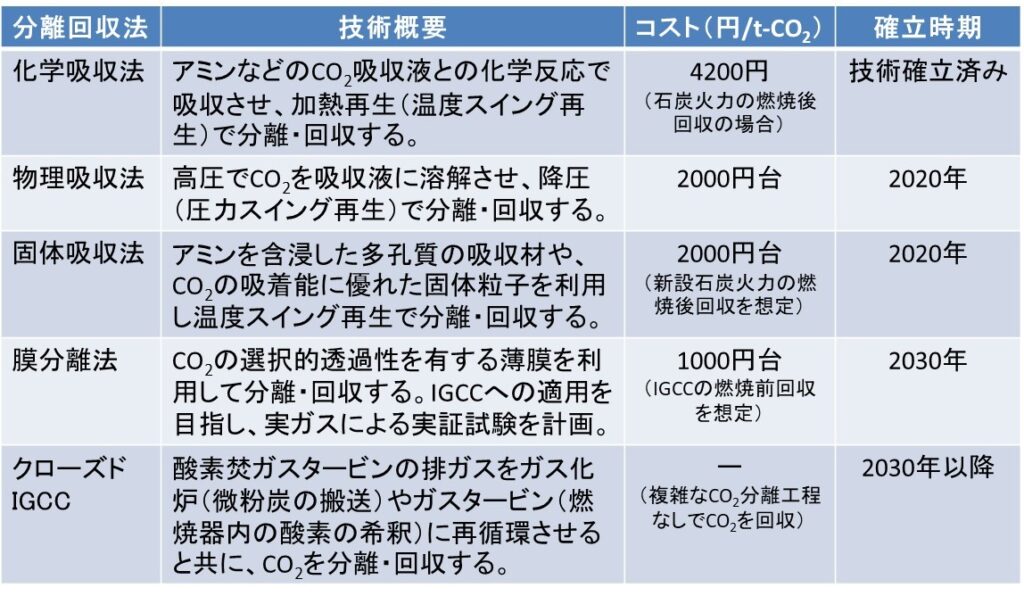
CO2貯留技術
2012年、北海道苫小牧港で、経済産業省、NEDO、日本CCS調査(JCCS)が中心となり、本格的なCCS実証試験のための設備建設が始まった。2016年4月、海岸から3~4km離れた海底下の約1000~1200mの地層、および約2400~3000mの地層にCO2を貯留する作業(圧入)を開始した。
製油所の排出ガス(PSAオフガス)から分離回収したCO2を約10万トン/年で地中へ貯留し、周辺地域での微小振動観測や海洋環境調査、CO2漏洩などをモニタリングした。2019年11月、累計CO2圧入量が30万トンに達し停止した。実証試験は2020年度末で終了し、圧入停止後は監視を続けている。

CO2輸送技術
2021~2026年、関西電力・日本CCS調査・エンジニアリング協会・伊藤忠商事・日本製鉄のコンソーシアムが、京都府舞鶴市の石炭火力発電所の排ガスからCO2を分離・回収後に液化し、大型船舶で約1000km離れた苫小牧港まで海上輸送する「CCUS研究開発・実証関連事業」が進められている。
CCSの事業化
化学吸収法
1990年より、三菱重工業と関西電力は独自のアミン化合物を使用した化学吸収法によりCO2回収技術の開発を始め、KS-1吸収液を使用した「KM CDR Process」を商業化した。
関西電力南港発電所でCO2回収量2トン/日、電源開発松島発電所で10トン/日、米国大手電力会社サザンカンパニー/米国電力研究所と共同で500トン/日などの実証試験を進め、排ガス中から90%以上を吸収して99%以上の純度のCO2回収が可能であることを示した。
三菱重工業は2023年までに世界14カ所でCCS設備の納入実績があり、2016年には米国テキサス州で世界最大級(CO2回収量:約5000トン/日)の「ペトラノヴァ」プロジェクトを受注・納入した。
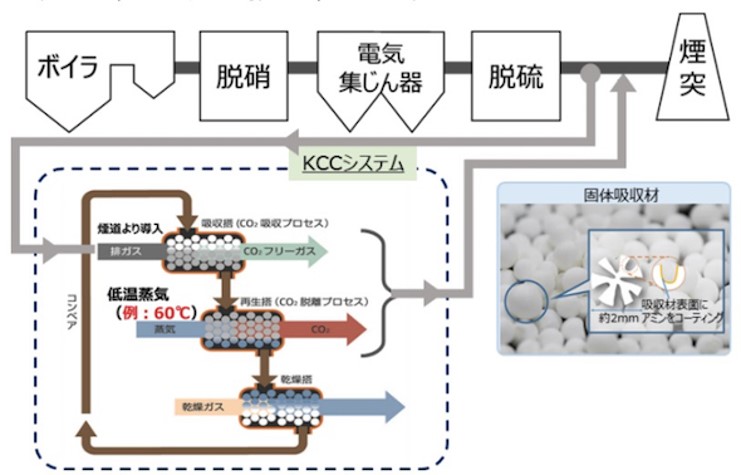
その後、プロセス改良を進め、2019年には揮発性が低く、耐熱性に優れ、排ガスによる劣化も少ないKS-21吸収液を使用した「Advanced KM CDR Process」が実用化された。
このCCSプロセスは、2021年6月、英国DRAXと共同でノースヨークシャー州のバイオマス発電所で採用された。また、2021年9月、三菱造船、川崎汽船、日本海事協会と共同で行われた洋上におけるCO2回収の実証試験でも採用している。
2021年10月、三菱重工エンジニアリング(MHIENG)は、ノルウェーの世界最大級のモングスタッドCO2回収技術センター(TCM)(CO2回収能力:約10万トン/年)での実証試験で、KS-21吸収液を使いガスタービン排ガスからのCO2回収率が最大99.8%に達したと発表した。
固体吸収法
2020年9月、地球環境産業技術研究機構(RITE)、川崎重工業、関西電力は、舞鶴発電所敷地内に40トン/日の固体吸収法による試験設備を設置し、2022~2024年度にNEDO事業「先進的二酸化炭素固体吸収材の石炭燃焼排ガス適用性研究」で、石炭火力発電所のCCS試験を開始した。
脱硫・脱塵・脱硝後に発電所の煙道から排出ガスを抜き取り、川崎重工業が開発した「Kawasaki CO2 capture(KCC)移動層システム」でCO2回収を行う。
固体吸収材はRITEが開発し、吸収素材表面に厚さ約2mmのアミン化合物をコーティングしたものである。従来のの化学吸収法ではCO2の再生回収に120℃の蒸気が必要であったが、60℃の減圧蒸気(発電所内の低温余剰排熱)を使えるため、エネルギー効率を優れている。
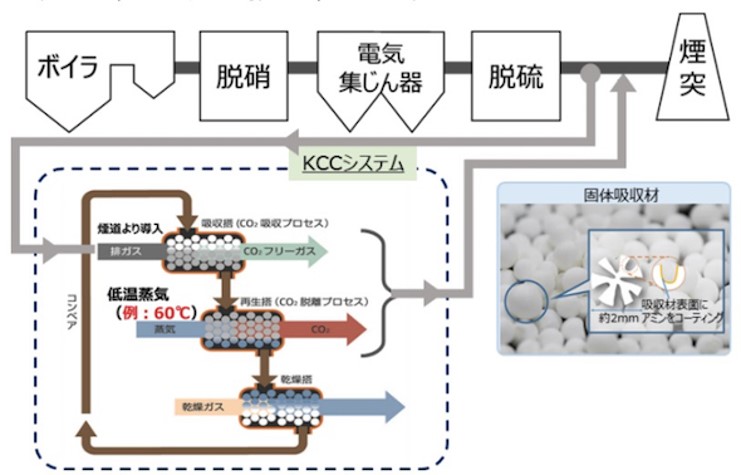
2022年6月、千代田化工建設、JERA、RITEは、LNG火力発電所からのCO2を固体吸収法により回収する実証試験を実施すると発表した。LNG火力発電所からの排ガスは石炭火力発電所に比べてCO2濃度が低いため、これまでCCS実証試験は行われていなかった。
2026年からJERAのLNG火力発電所で実証を開始する。回収コストを2000円台/トンに抑える目標を掲げ、回収したCO2はパラキシレンなどの化学品や持続可能な航空燃料(SAF)の製造への利用を検討し、将来的にLNGプラントからの排出ガス対策にも活用する。
2023年2月、川崎重工業は、ごみ焼却施設から排出される排ガス中のCO2を分離・回収する実証実験を福島県郡山市の「富久山クリーンセンター」で始めると発表した。2023〜24年度に調査を行い、2025年度から固体吸収法による試験設備を導入する。
コメント