地球温暖化問題が注目される中でガスタービンの高温化による高効率化が進められ、ガスタービン・コンバインドサイクル発電システム(GTCC)の導入が進められた。ガスタービン高温部品(動翼、静翼、燃焼器)には冷却技術、構造材料、コーティング技術が高温化に大きな役割を果たしている。
コンバインドサイクル発電システムの高温・高効率化
地球温暖化問題がクローズアップされる中で、急速なガスタービンの高温化による高効率化が進められ、電力会社によるLNG焚ガスタービン・コンバインドサイクル発電システム(GTCC:Gas Turbine Combined Cycle)の導入が始まる。
『LNG焚ガスタービン・コンバインドサイクル発電システムの導入』
●1980年代中頃、1100℃級GTCC、発電端効率・LHV基準で47~49%の導入が始まる
●1990年代後半、ガスタービン入口の燃焼ガス温度を高温化した1300℃級改良型コンバインドサイクル(ACC:Advanced Combined Cycle)、発電端効率・LHV基準で54~56%の導入が加速
●2000年代後半、燃焼ガス温度をさらに高温化し、ガスタービン高温部品の蒸気冷却などの技術革新で、大容量の1500℃級コンバインドサイクル(MACC:More Advanced Combined Cycle)、発電端効率・LHV基準で58~59%が開発
●2010年代から、燃焼ガス温度をさらに高温化し、ガスタービン高温部品を空気冷却に戻し、高効率の1600℃級コンバインドサイクル(MACC2)、発電端効率・LHV基準で61~62%の導入が加速
現在は、CO2排出量と燃料費の削減を目指し、初期に導入された1100℃級ガスタービンを最新の高性能ガスタービンに置き換えるリプレース工事が始まっている。
発電用ガスタービン材料の高温化
発電用ガスタービンの主要な高温部品は動翼、静翼、燃焼器であり、冷却技術、構造材料、構造材料の表面に施されるコーティング技術が高温化に大きな役割を果たしている。図9には、ガスタービン高温材料の開発状況と、それに伴うタービン入口温度の上昇を示す。
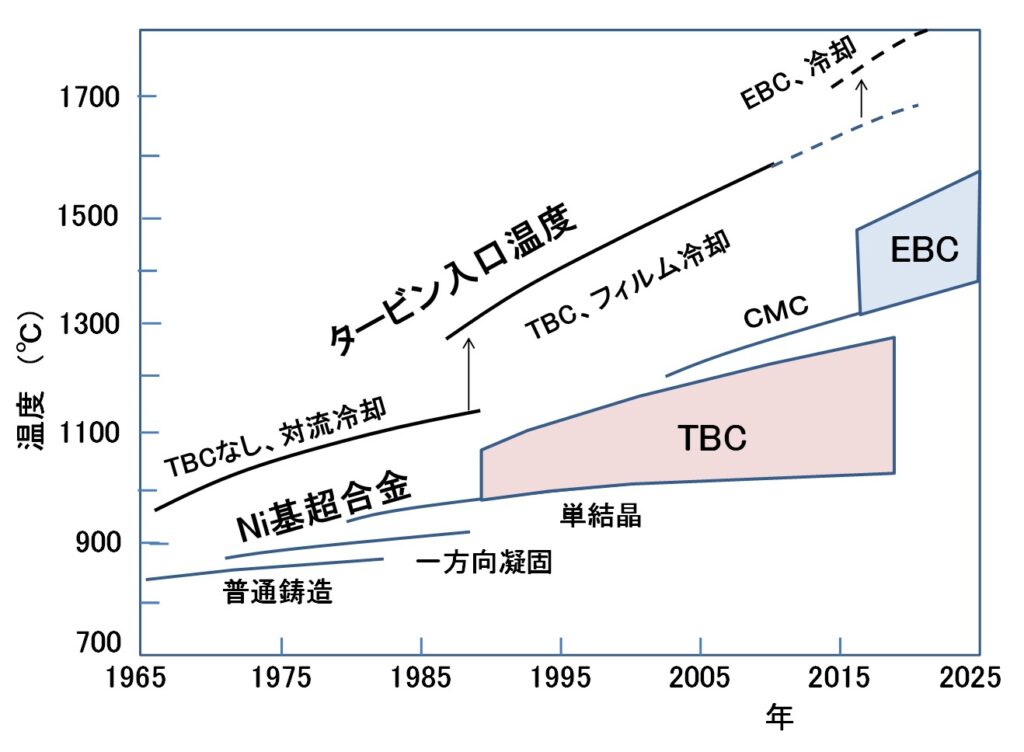
【燃焼器】
キャン型燃焼器はライナーと静翼に通じるトランジションピースから構成され、起動停止や負荷変動等による低サイクル熱疲労特性、燃焼振動による高サイクル疲労特性、高温クリープ特性、耐熱衝撃特性が要求される。また、局部加熱に対する耐高温酸化性や補修のための溶接性も必要である。
そのため加工性に優れた薄板のNi基やCo基合金が使われ、その内面には7~8mass%Y2O3-ZrO2の遮熱コーティング(TBC:Thermal Barrier Coating)が施され、外面は対流冷却が行われている。トランジションピースは内部で燃焼ガスが偏向して増速するため、ライナーよりも高温となる。
【静翼】
静翼はケーシング内面に拘束された状態で、動翼よりも高温の燃焼ガスに曝されるため高い熱応力が発生し、要求されるクリープ強度は動翼よりも低いが、曲げ応力に耐えうるクリープ強度、熱疲労特性が必要とされる。
また、製造・保守性の観点から、溶接性・補修性に優れたCo基合金が使われている。その外面にはTBCが施されており、翼に形成された複雑な冷却孔を通じて圧縮空気により内面の対流冷却、外面のフィルム冷却が行われている。
【動翼】
動翼は高速回転により高い遠心力が作用して高温の燃焼ガスに曝され、破損した場合のリスクが高いため、優れた高温クリープ特性、熱疲労特性、熱衝撃特性が求められる。γ‘相Ni3(Al,Ti)析出強化型の普通鋳造のNi基超合金(CC:Conventional Casting)のRene 80、IN738LCなどが使われてきた。
その後、動翼長手方向に直角な結晶粒界をなくした一方向凝固(DS:Directional Solidification)化によるMar-M200Hf、MS5002などで約20℃、弱化要因である結晶粒界を完全に排除した単結晶(SC:Single Crystal)化によるTMS196、CMSX-4、Rene N5で約30℃の耐熱温度の向上が進められた。
いずれも、動翼外面にはTBC、冷却孔内面にはアルミナイズ処理が施されており、翼に形成された複雑な冷却孔を通じて圧縮空気により内面の対流冷却、外面のフィルム冷却が行われている。
現在の単結晶Ni基超合金の耐熱温度は、約1100℃(強度設計上は安全をみて1000℃程度)でほぼ飽和傾向にある。そのため、TBCの厚肉化(0.3mm→1.0mm超)と冷却技術の高度化により、タービン入口温度の上昇に対応している。
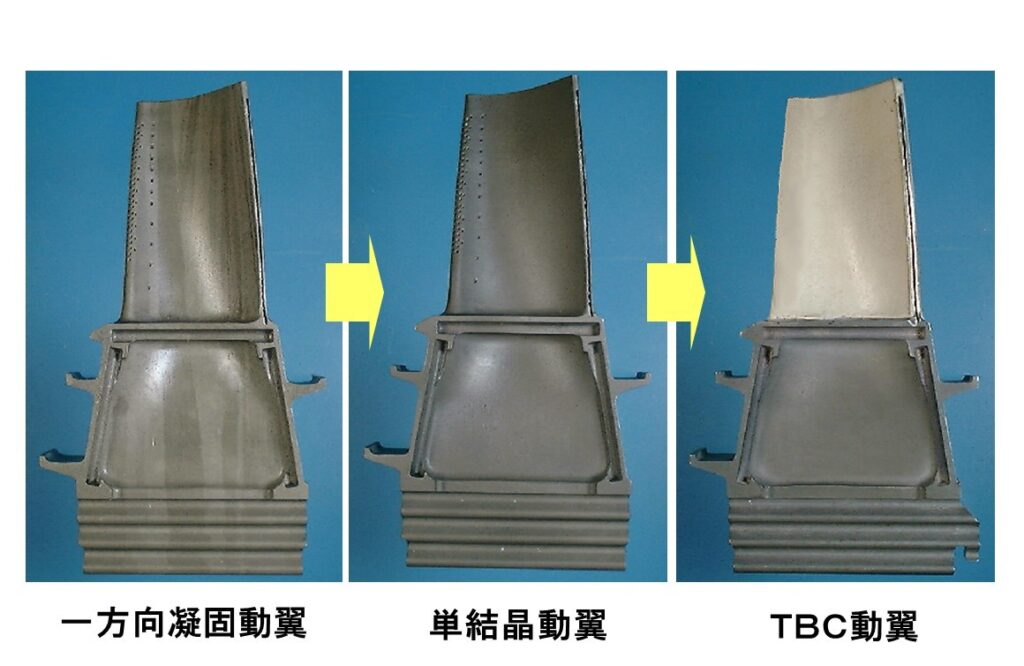
【セラミックス基複合材料】
次世代耐熱材料として期待されているセラミック基複合材料(CMC:Ceramic Matrix Composite)は、2000年初期に炭化ケイ素長繊維強化炭化ケイ素基複合材料(SiC/SiC composite、以下ではSiC/SiC複合材料)の基礎開発が終了している。
第一世代のSiC/SiC複合材料の耐熱温度は約1300℃であり、Ni基超合金(SC)に比べて約200℃と飛躍的な向上を実現し、航空機ジェットエンジンの高温部品への適用が始まっている。SiC/SiC複合材料の発電用ガスタービンへの適用は、今後の課題である。
SiC/SiC複合材料には、燃焼ガス雰囲気において高温水蒸気腐食の問題が生じる。そのため、これを回避するための耐環境コーティング(EBC:Environmental Barrier Coating)が施されている。
コメント