マルチマテリアル化
自動車の燃費向上を目的に、エンジン効率向上、車体(ボディ)の空気抵抗低減、タイヤの低ころがり抵抗化などの研究開発は継続的に進められてきた。2010年代に入ると新構造材料による車両の軽量化に注目が集まり、新エネルギー・産業技術総合開発機構(NEDO)のプロジェクトが発足している。
すなわち、新構造材料研究組合(ISMA)では、30を超える企業・大学・研究機関と連携し、自動車を中心とした輸送機器の抜本的な軽量化(重量半減)に向けて、主要な構造材料の高性能化とマルチマテリアル化の技術開発を行う「革新的新構造材料等研究開発」プロジェクトが推進されている。
図1には、車体の軽量化に向けた適切な材料選択の例を示す。このようなマルチマテリアル化を実現するために、プロジェクトでは次のような開発が行われた。
・新構造材料研究組合HP、http://isma.jp/ja/works/
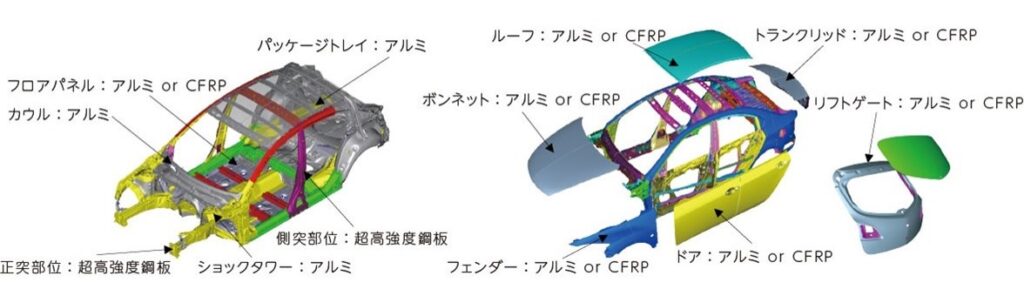
出典:新構造材料研究組合、http://isma.jp/ja/works/
2013~2017年には、高張力鋼の高延性化(引張強度:1500MPa、伸び:20%)、難燃性マグネシウム合金(引張強度:363MPa、伸び:15%)や高強度アルミニウム合金(引張強度:739MPa、伸び:15.3%)の開発などが行われた。
また、短繊維強化の熱可塑性炭素繊維強化樹脂(CFRTP:Carbon Fiber Reinforced Thermo Plastic)による車体/構造用部品の試作が行われた。
さらに、溶融接合や摩擦撹拌接合(FSW:Friction Stir Welding)による同種材料(炭素鋼板-炭素鋼板)の接合、異種材料の接合技術開発(炭素鋼板-CFRPの接着接合、アルミニウム合金-炭素鋼板のスポット溶接、アルミニウム合金―CFRPのFSWなど)が実施された。
また、2018~2020年には、マルチマテリアル化を目指した技術や部品化の課題を解決し、衝突安全性に考慮した構造設計を行うなど、自動車ホワイトボディのモデル化の検討を行うなど、実用化・事業化を目指した研究開発が推進された。
2022年6月、大王製紙はレース用EV部品への植物由来素材「セルロースナノファイバー(CNF)」の提供を発表した。2018年から部品提供を開始、2021年にドアやルーフパネルに採用され、今回は愛媛大学や川之江造機と開発した新成型方法でバンパーやボンネットなどの大型部品にCNFを適用した。
CNFは原料のパルプをナノ(ナノは10億分の1)メートル単位に細かく解きほぐして作り、同社のCNF成形体は引張強度がプラスチックの約5倍であり、車体の軽量化による燃費向上に寄与する。置き換えた部分は約5割の重さになり、米国コロラド州のレースでの公道検証が行われる。
マルチマテリアル化の本質的な目的は、適材適所よるものづくりにある。この適材適所はガソリン車、ハイブリッド車、電気自動車、燃料電池車などの車種とは無関係に、自動車に共通の課題である。
自動車において革新的な軽量化を実現するために、従来はオール炭素鋼製であったボディーを薄板の高張力鋼板に置き換えたり、部分的にアルミニウム合金、マグネシウム合金、炭素繊維強化樹脂(CFRP:Carbon Fiber Reinforced Plastic)などの軽量材料への置き換えが進められている。
一方で、これらの各種材料をボルトやリベットなどの機械的締結でつなぐことは、基本的に軽量化とは相反する。そのため、革新的な軽量化を実現するためには異種材料の継手設計と、異種材料間の接合技術の開発が不可欠となる。
コメント